Defined life repair technology for damaged pipework, pipelines and structural components.
Technowrap™ is a versatile long-term alternative to steel replacement that offers practical and cost-effective rehabilitation and minimal disruption to operations. Applied to live targeted areas, with no requirement for shutdown, it supports safe operations while optimising production uptime whilst delivering tangible cost savings and environmental benefits.
Overview
With over 30 years of experience and more than 50,000 composite repair applications globally, we are a market leader in composite repair technology. Our bespoke engineered repair systems utilise glass or carbon fibre stitched cloths combined with two-part epoxy resins, tailored to meet a wide range of mechanical and environmental requirements.
For pipework and pipelines, our Technowrap engineered composite repairs are tested and qualified to ISO 24817 and ASME PCC-2 Article 401 standards, with all subsequent engineering conducted to meet these exacting standards.
Technowrap is designed to address various defect types, including thin wall defects, internal and external corrosion, and through-wall defects. It can be engineered for service temperatures up to 230°C (446°F). While pressure tolerance is dependent on design inputs, the limitation for through-wall defects is 70 bar (1015 psi), and for thin-wall defects, it can exceed 250 bar (3625 psi), depending on pipe diameter and remaining steel thickness.
In addition to piping components, Technowrap repairs can be engineered for structural components such as decks, beams, and columns. Utilising mechanical property testing from coupon tests through to full-scale validation testing. Where necessary, designs are supported by hand calculations or Finite Element Analysis (FEA) to ensure optimal performance and reliability.
What can we repair?
Pressure System Repairs
- Critical and non-critical pipework, all components, including bends, tees, and flange and clamp overwraps.
- Pipelines
- Vessel repairs
- Composite live leak sealing
- Splashzone and subsea repairs (including all wet environments i.e. high humidity)
- Caisson and risers, leak sealing and corrosion protection
Structural Repairs
- Structural strengthening of caissons and risers
- Strengthening of decks, roofs and floors and drip pans
- Strengthening of tanks and vessels (shells, supports & nozzle attachments)
- Blast Walls, panels, and accommodation modules.
- I-beams, CHS members
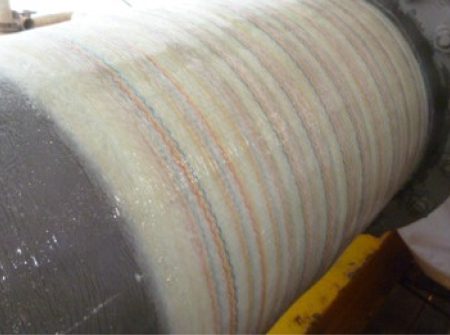
Pipework Repairs
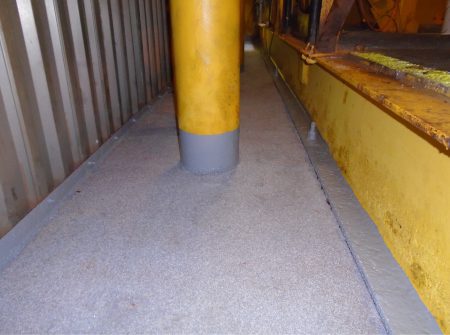
Deck Repairs
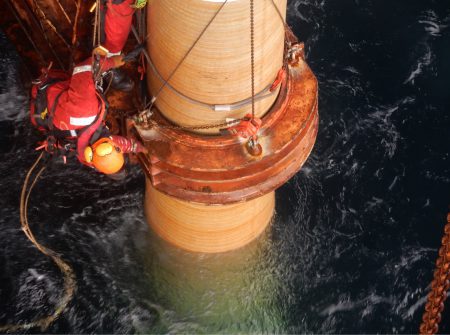
Caisson Repairs
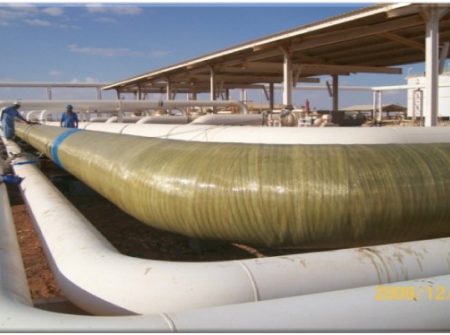
Pipeline Repairs
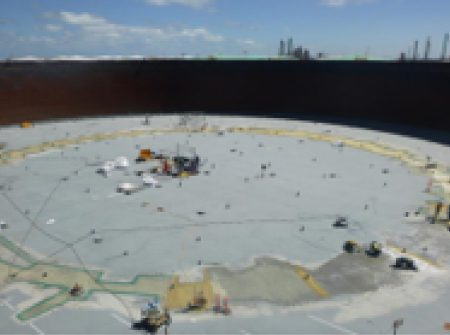
Tank & Vessel Repairs
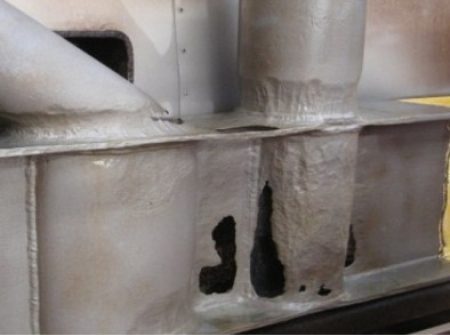
Stuctural Component Repairs
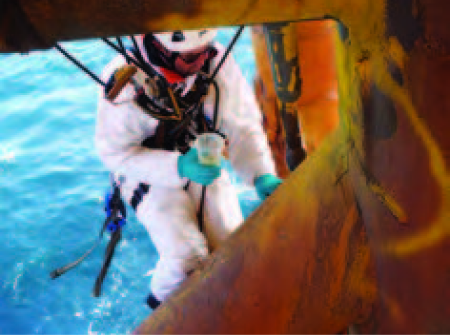
Splashzone & Subsea Repairs
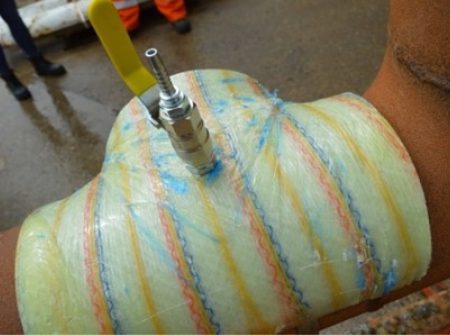
Live Leak Sealing
Track Record
Technowrap has been utilised on tens of thousands of installations worldwide, giving operators added reassurance through our experience and in-service application history. Our in-house integrated service provides engineering, materials, training, and installation, which has enabled us to become the industry specialist, having dealt with some of the most challenging projects in the industry both on and offshore. We have proudly led the industry in the development and adoption of composite repair technology and are key member of both ASME and ISO committees. Technowrap™ is internationally recognised and all engineering is bespoke and completed in-house, in accordance with the latest issues of ISO 24817 and ASME PCC-2. Our engineering designs are carried out to current code requirements and are validated by a range of material property and design scenario testing which has been independent by third parties (Lloyds Register, ABS Design & Manufacturing, DNV Type Examination) and certified as fully compliant.
Benefits
- Design Flexibility: Can be designed to match the specific mechanical properties required for a repair, allowing for customisation. They are full engineered and come with traceability and documentation to support design basis.
- Defined life: In accordance with ISO 24817, the design lifetime is between two and 20 years, allowing operators to extend the life of their assets or get through to the next available shutdown.
- Reduced Downtime: The repair is targeted and can be applied live with no shutdown and no hot work and an often be carried out without the need for extensive dismantling.
- Strength and Weight: Can be tailored to provide high strength while remaining lightweight, making them suitable for applications where minimizing weight is crucial.
- Corrosion & UV Resistance: No significant maintenance during the defined life (RBI is recommended). They are corrosion resistant and UV tolerant meaning the composite material will not degrade due to environmental factors.
- Reduced cost, time and POB: Can be applied live, limited impact on production and are more cost effective compared with replacement.
- Environmental benefits: 66% reduction in carbon emissions comparative to traditional replacement.
- INSONO™ Inspection: Composite material and the bond line can be inspected using INSONO™
Cloth | Fibre Type | Application |
---|---|---|
2K | Tri Axial Fibre Glass Cloth + Epoxy Resins | General Piping systems |
Structural (SRS) | Quadraxial Carbon Fibre Cloth + Epoxy Resins | All structural components |
HP PRS | Uni directional Carbon Fibre, 99 GPa (anisotropic) | High axial loading scenarios |
Resin | Application |
---|---|
Low Temp (LT) | Quick curing at low ambient temperatures from -75°C to 100°C (-103°F to 212°F) |
High Temp (HT) | Suitable for service temperatures up to 230°C (446°F) |
High Ambient (HA) | Longer working life at high ambient temperatures |
DRS | Rubber toughened to withstand impact for decks |
Glycol | Compatible with 100% glycol at 90°C (194°F) |
Splashzone | Pipework in wet areas, splashzone, subsea or high humidity (and CuNi) |
Potable | Potable water systems |
Case studies
Send us your enquiry
Please complete the form below, and a member of our team will be in touch as soon as possible. Alternatively, please send your enquiry directly to sales@icr-world.com