Date | Client | Location |
---|---|---|
March 2022 | Energy Company | Nuclear Power Station, England |
Scope
ICR’s UK Onshore team was asked to complete a Technowrap™ composite repair scope at a nuclear power station site in England where replacement was not practicable due to severe access restrictions and isolation issues.
Solution
Although typical composite resin systems within a confined space area require breathing apparatus, ICR was able to use its bespoke resin system and installed a Technowrap™ engineered composite repair to eliminate the requirement. Following visual inspection and risk assessment, the area was grit blasted with the pipework remaining in service at all stages. The repair was implemented and signed off within a 3-day window.
Results & Benefits
- No hot work required, reducing safety risk
- Cost effective solution
- 20 year design life achieved
- Has led to several further scope enquiries from client
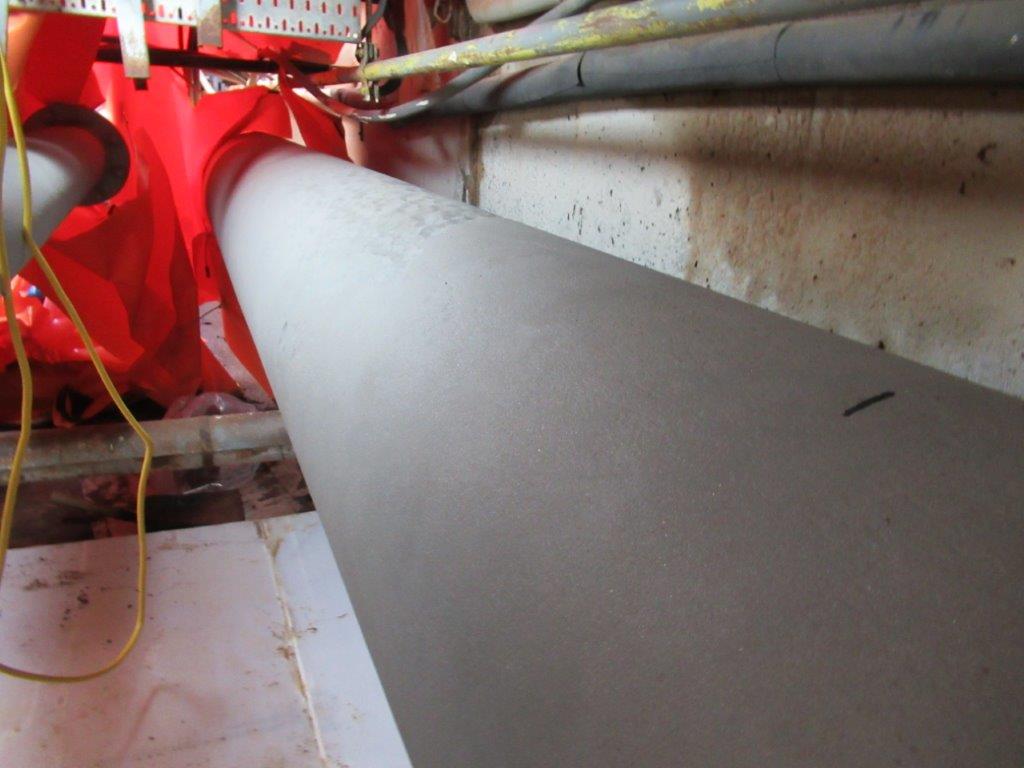
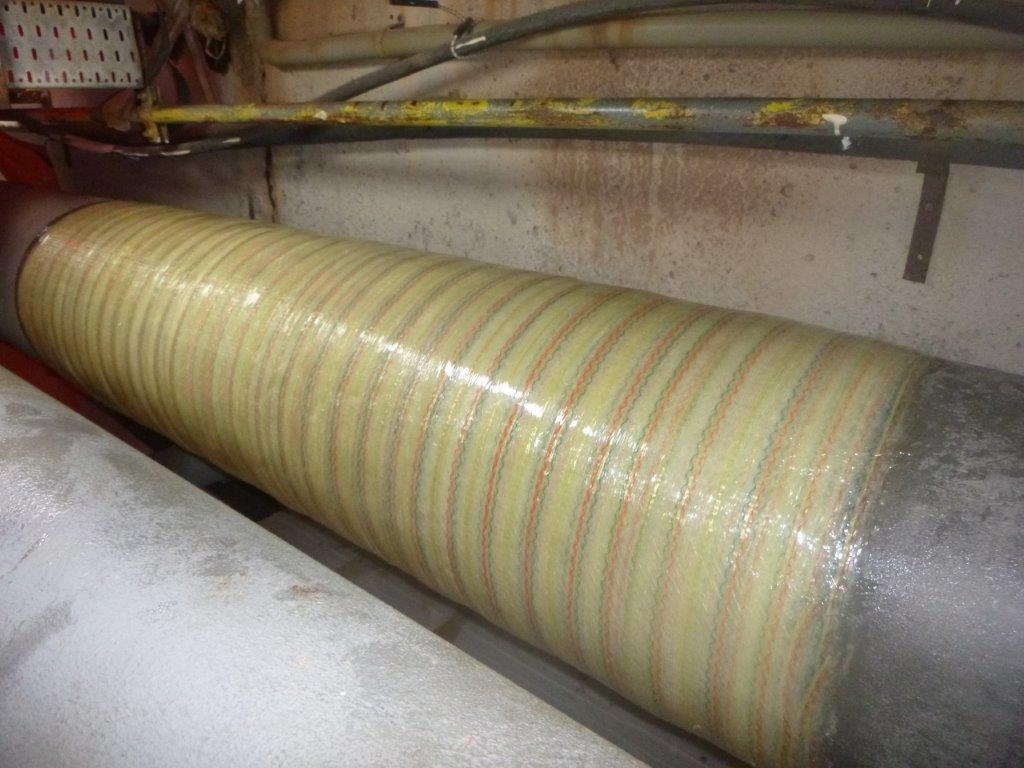
Client Feedback
“We would also like to pass on our thanks to your Team for the work carried out. It was a job well done with no issues and to an excellent standard.”
Date | Client | Location |
---|---|---|
July 2021 | UK Medical Products Supply Company | South East England |
Scope
On removal of insulation during plant shutdown, severe external corrosion under insulation was found on an approx. 3m length of 2” to 4” diameter water/ethanol pipework between valves and branches. ICR were approached to propose a solution to restore the integrity of the pipework and allow the plant to be rapidly returned to service. The repair design conditions being 2.5barg pressure, ambient/-35°C temperature with 2 year design life.
Solution
A Technowrap™ 2K LT engineered composite repair solution was proposed with surface preparation by hand to minimise chance of pipework going through wall. ICR mobilised technicians and material to site. During the repair, additional pipe sections were found to be corroded and repair scope doubled. ICR provided additional materials and technicians with night shift established to enable repairs to be completed to the required schedule. From initial approach to the repairs (including additional scope) being completed and signed off, was just over a week.
Results & Benefits
- Pipework integrity restored
- No through wall penetration during repair
- ICR technicians worked day and night to complete the repair with increased scope allowing the plant to return to service in line with schedule
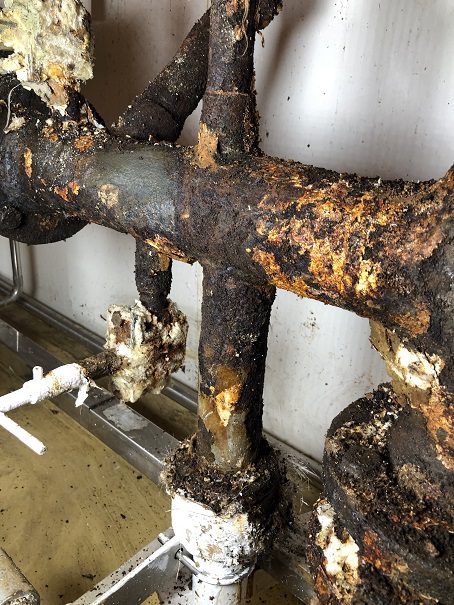
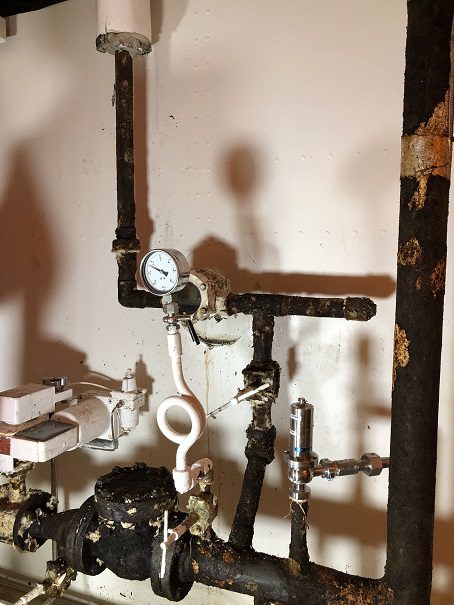
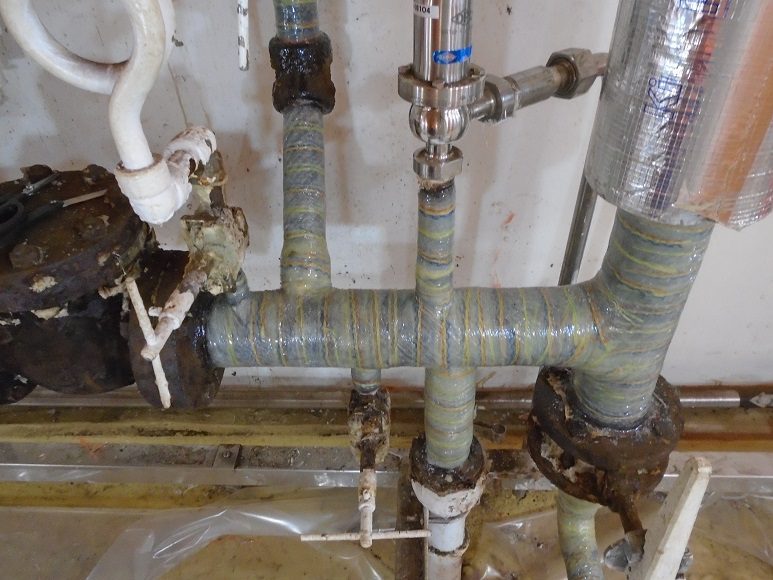
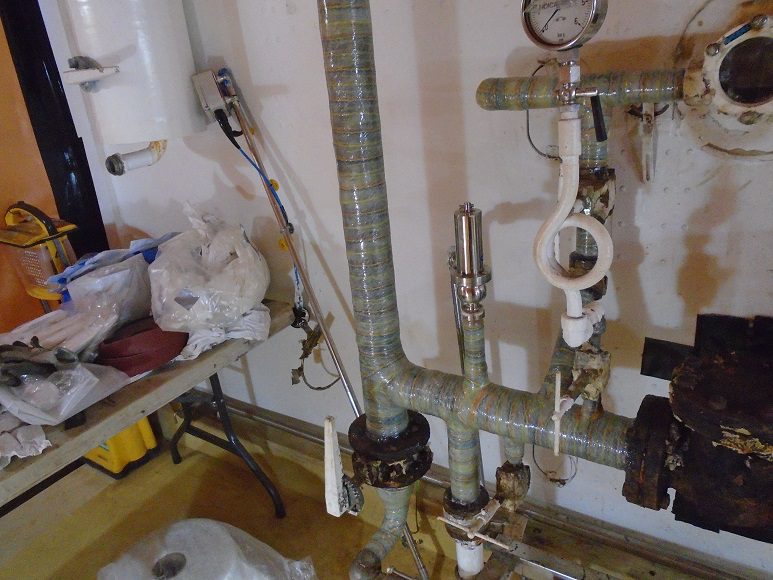
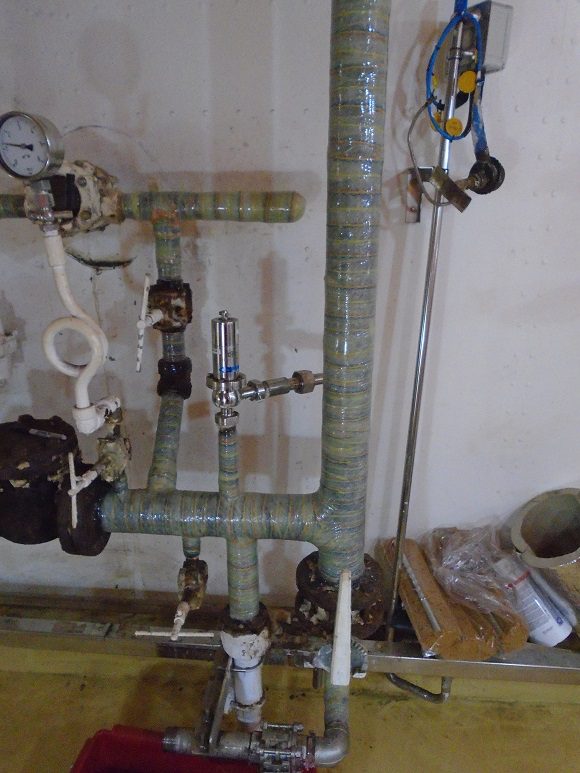
Client | Location |
---|---|
EDF | Heysham 1 Power Station |
Scope
EDF Carbon Steel 20” Condensate Pipework Repair Water Line (TG2- 20” Condensate Return). The line was suffering from a through wall defect caused by external corrosion.
Solution
ICR were requested to provide an engineered repair solution to restore the integrity of the line for a design life of 5 years. This repair is subsequently designed for a through-wall defect.
Results & Benefits
- Engineering design calculation complete with design sketch, materials and manpower to complete the 15-layer repair using the Technowrap™ 2K cloth with the Technowrap™ LT resin.
- No hot work required
- Defined life repair of 5 years
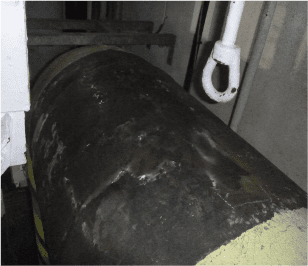
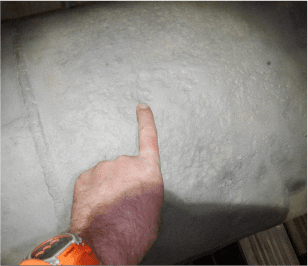
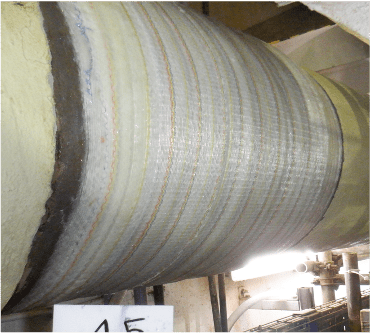
Date | Client |
---|---|
April 2022 | EDF Energy |
Scope
EDF Emergent requested out of hours on Bank Holiday Monday 18” Carbon Steel Gen TX 2 Spare Oil Conservator which was suffering from a through-wall defect due to external corrosion of the weld. This repair was subsequently designed for a through-wall defect.
Solution
ICR were onsite the following day, with an engineered repair solution of 8 layers of Technowrap™ 2K LT was delivered to restore the integrity for a design life of 15-years.
Results & Benefits
- Technicians onsite within 24 hours, installation was delivered, QA/QC checked and handed back to site in a 3 day window
- 15 year Design life
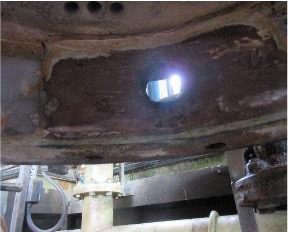
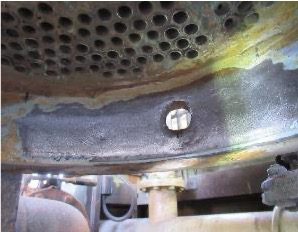
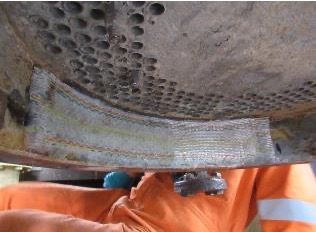
Date | Client | Location |
---|---|---|
August 2019 | Major North Sea Operator | Onshore Aberdeen |
Scope
ICR were engaged to provide a engineered composite repair solution on a produced water caisson prior to installation offshore. The previous caisson was corroded due to wave action causing thermal cycling.
Solution
Two new sections of a 12” caisson were fabricated and sprayed with an internal coating prior to ICR applying the composite solution. It was a design requirement that surface preparation to Sa2.5 and was achieved prior to the application of 4 layers of Technowrap™ 2K using HT (High Teemperature) resin.
These were then welded together and an angular profile of 45μ was achieved using bristle blasters. A composite wrap was then applied to cover the welded section. Heat blankets were used througout the process to assist curing.
Design Temperature | 100°C |
Design Pressure | 2.5bar |
Material Grade | Super Duplex |
Surface Preparation | Sa2.5 |
The change in temperature was taken into consideration by derating the allowable strains in line with ISO 24817.
Results & Benefits
- ICR technicians worked day and night for a total of 7 days to complete the repair
- A repair lifetime of 20 years was given
- The solution will prevent future corrosion due to thermal cycling, maintaining the integrity of the structure

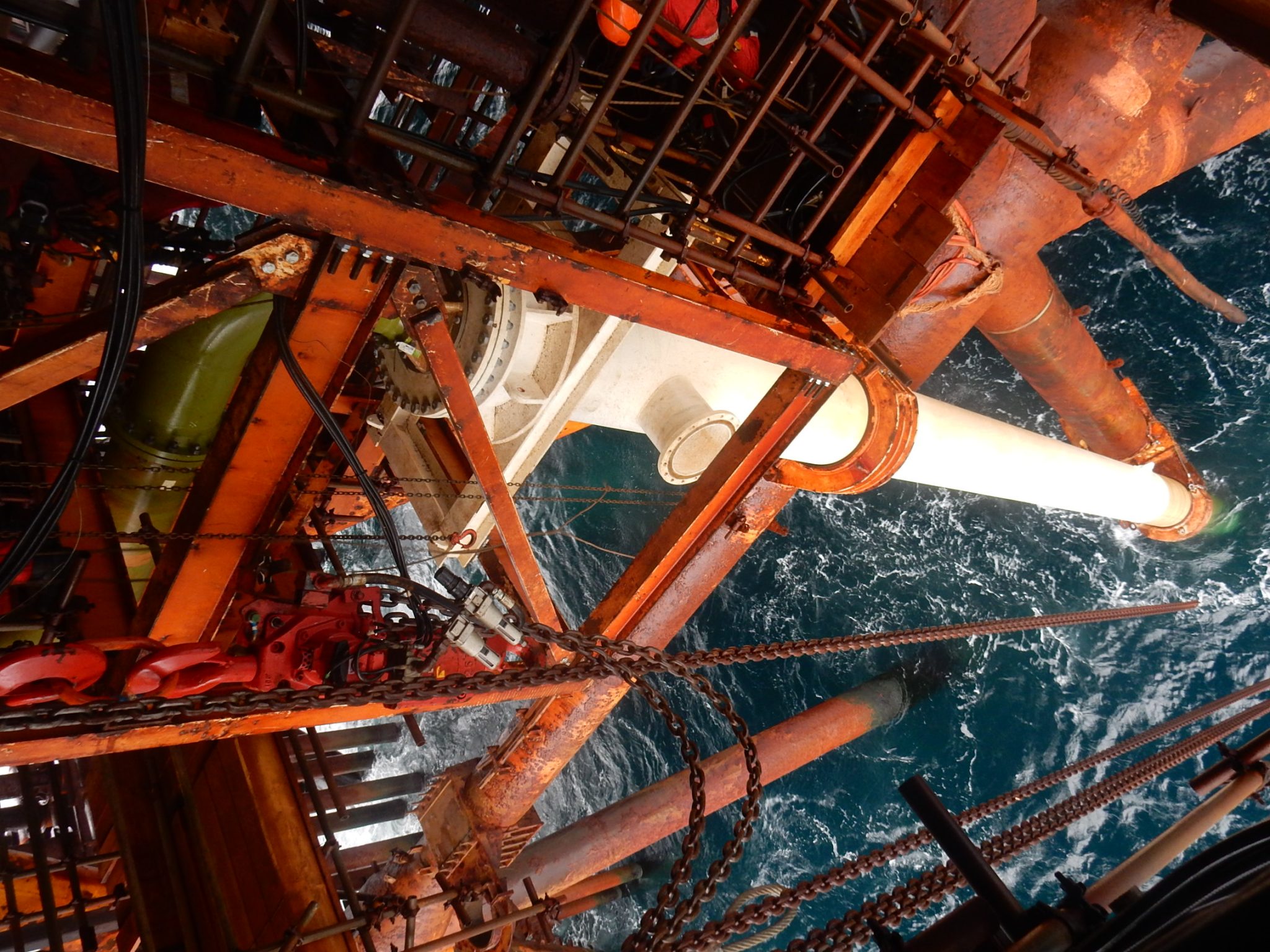
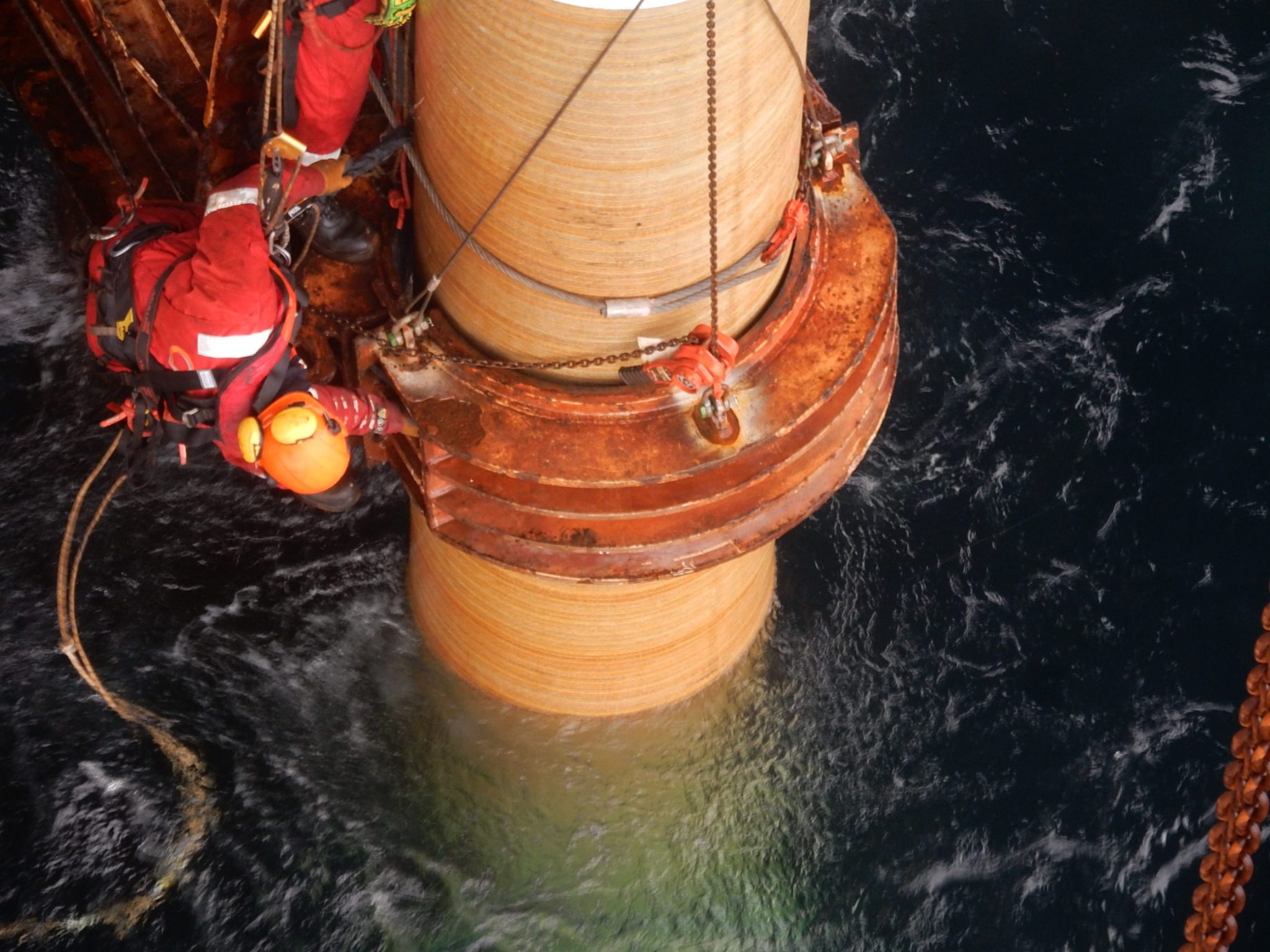
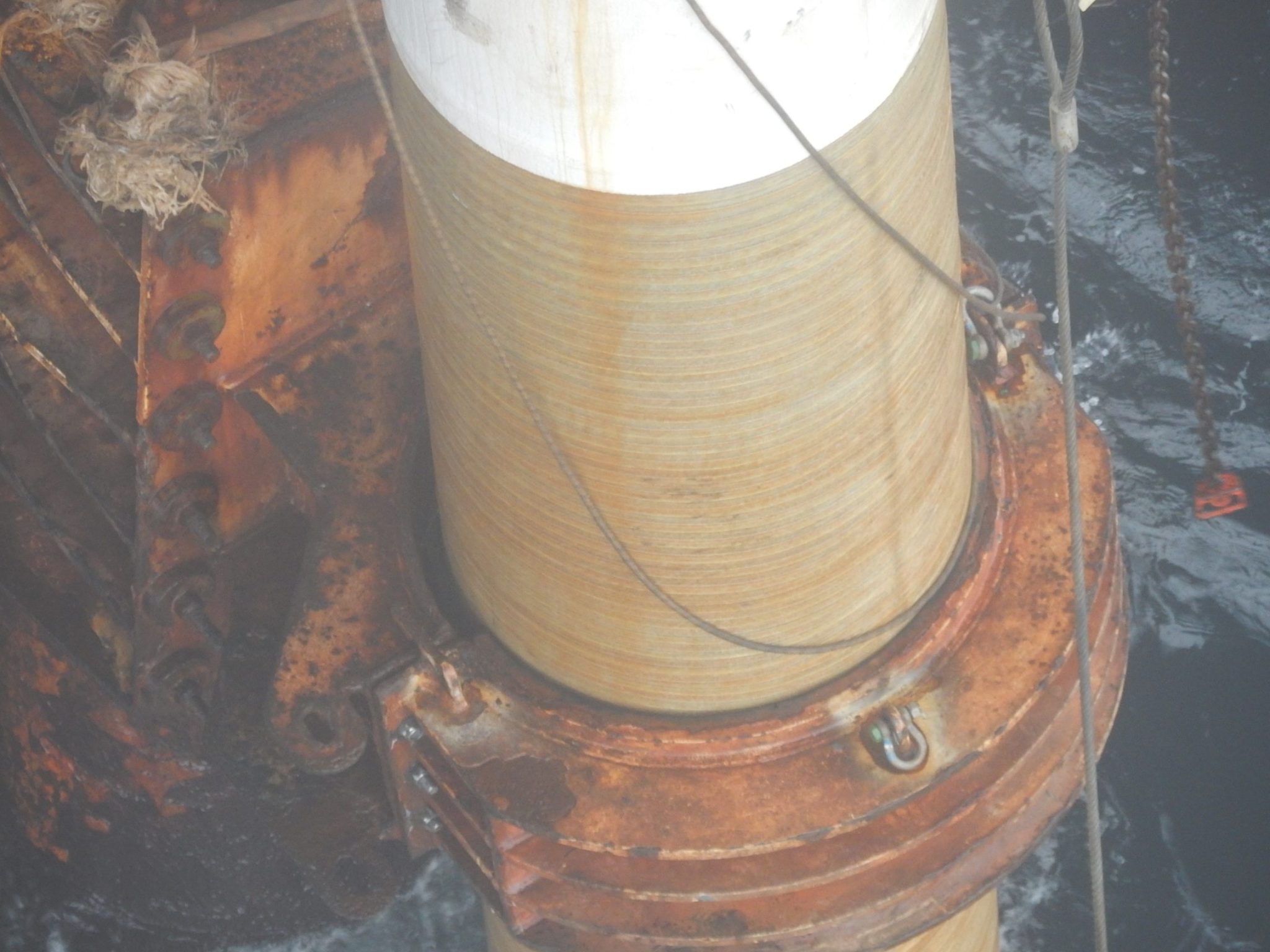
Date | Client | Location |
---|---|---|
April 2022 | EDF | North West England |
Scope
Various repairs carried out on a Carbon Steel Demin Water Reserve Feed Tank. The tank was suffering from through-wall defects due to external corrosion.
Solution
ICR were requested to provide an engineered repair solution to restore the integrity of the tank for a design life of 20 years.
Results & Benefits
- ICR provided engineering design calculation complete with design sketch, materials and manpower to complete the 8-layer repair using Technowrap™ 2K HA
- 5 x Dayshifts, 5 x repairs
- Fast & cost effective versus replacement
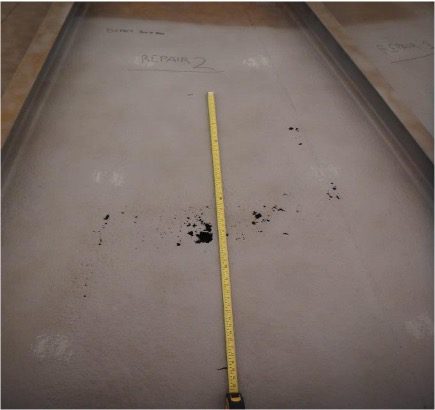
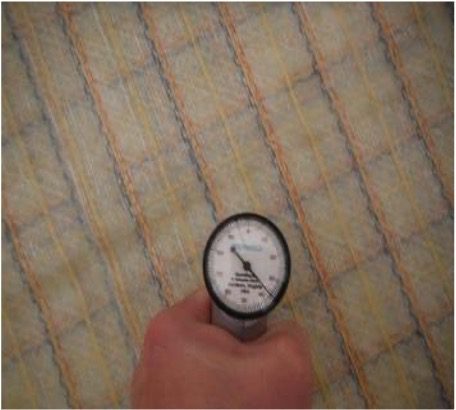
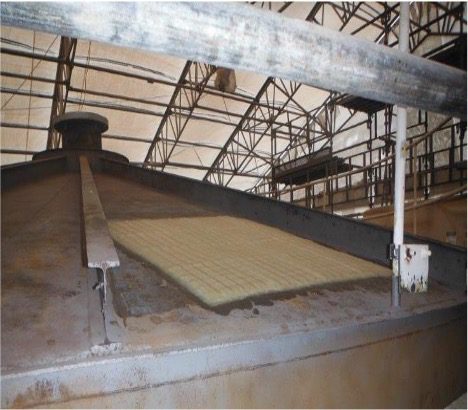
Client | Location |
---|---|
Major Middle East Operator | Oman |
Scope
An isolation joint (as part of the cathodic protection system) of a 36” pipeline was leaking through the internal sealing mechanism of the joint. It was not possible to isolate this joint so the repair had to be applied live. Therefore, one of the critical aspects of this repair application was the associated safety aspects of diverting the leaking gas from the joint while the repair was being applied.
Solution
The installation procedure for the clamp and composite repair consisted of the following steps;
1. Clean surface of joint and seal leak
2. Apply temporary clamp and gas diversion system
3. Prepare surface of pipeline
4. Apply composite repair
5. Perform QA/QC checks
The proposed solution involved first applying a temporary clamp over the leaking part of the joint and then applying a composite repair over the clamp to ensure longevity of the repair solution. ICR project managed the complete activity of this repair including surface preparation, clamp design and installation and composite repair design and installation.
The repair design was performed according to ISO/TS 24817. Due to live nature of the repair, the repair design was split into two parts. The first part involved the design of a temporary clamp and gas diversion system. The second part was the design of the composite repair to ensure the leak sealing capability of the repair. The solution was 15 layers of Technowrap™ 2K in the form of a fully circumferential wrap over the temporary clamp and extending along the axial length of the pipeline beyond the clamp by 300 mm.
Results & Benefits
- The application of the Technowrap™ 2K HA went as planned and without delays
- The repair was designed with a lifetime of 5 years.
- Repair was applied whilst line was live, meaning no shut down for client
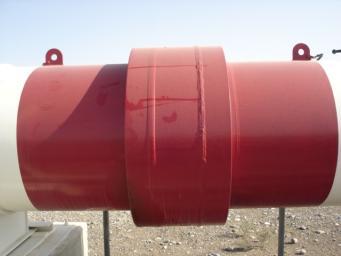
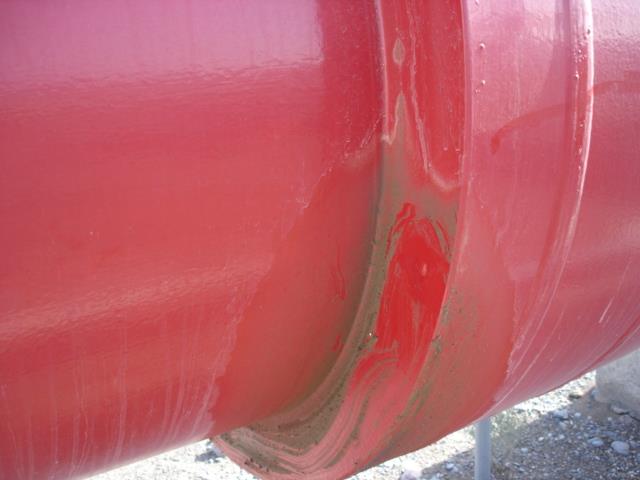
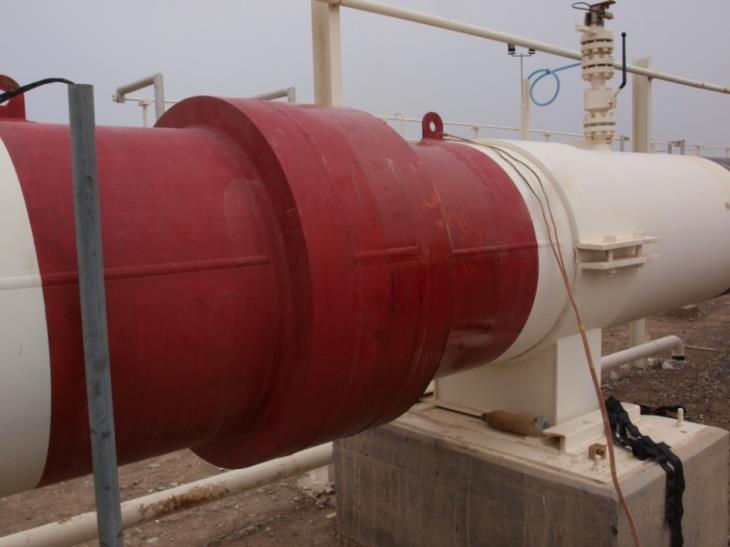
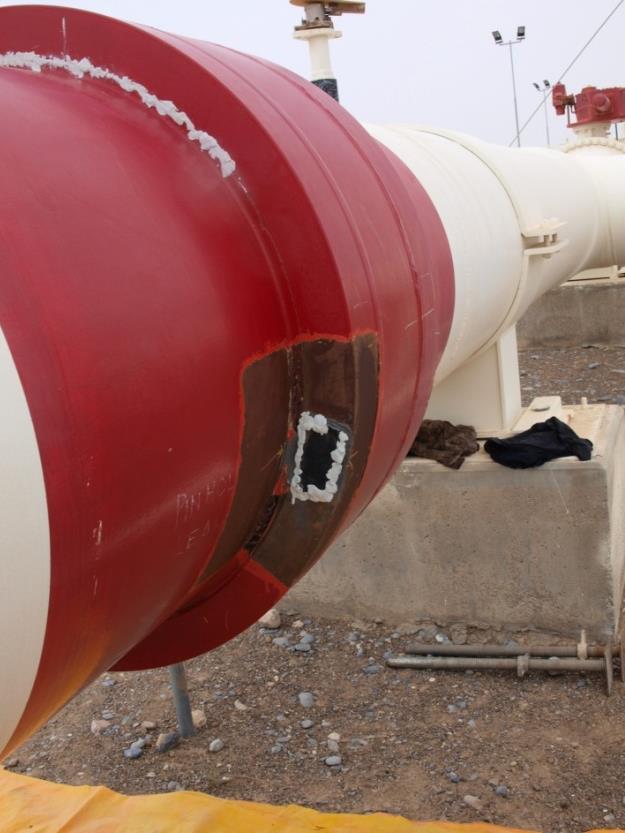
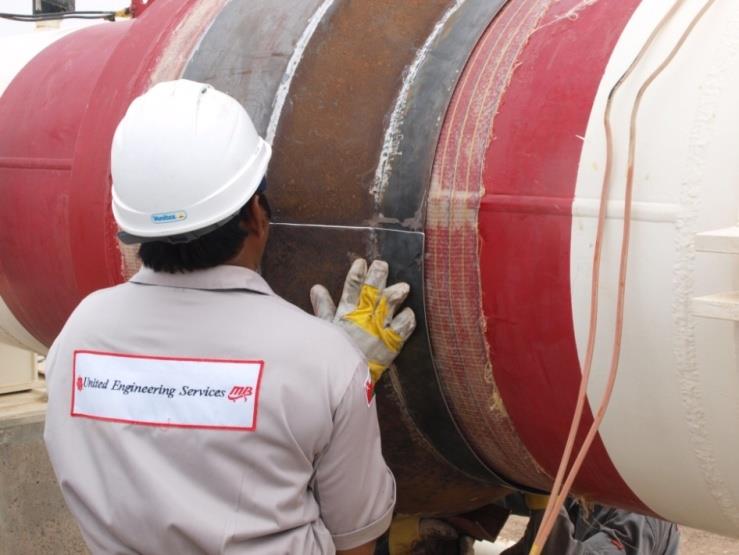
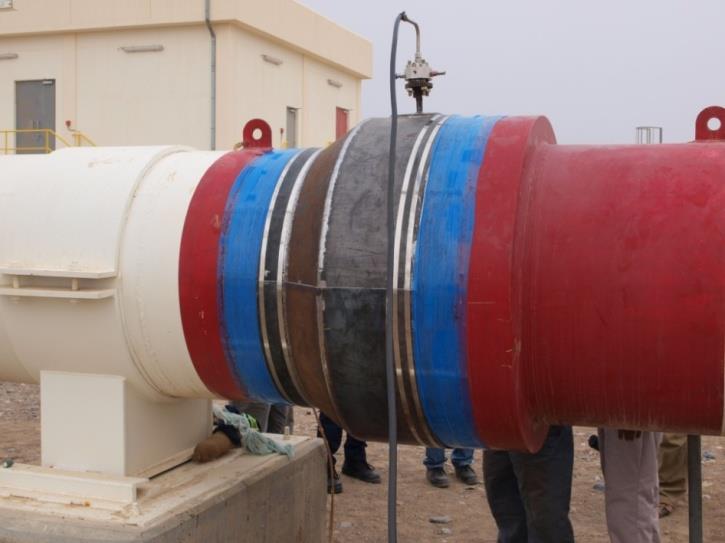
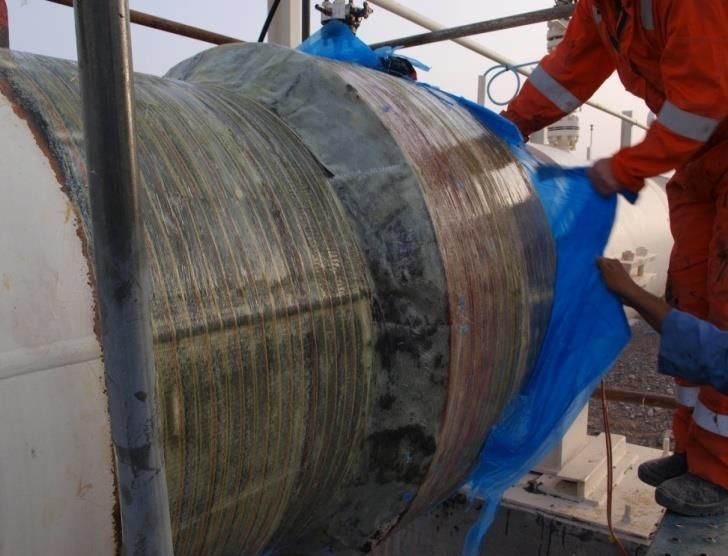
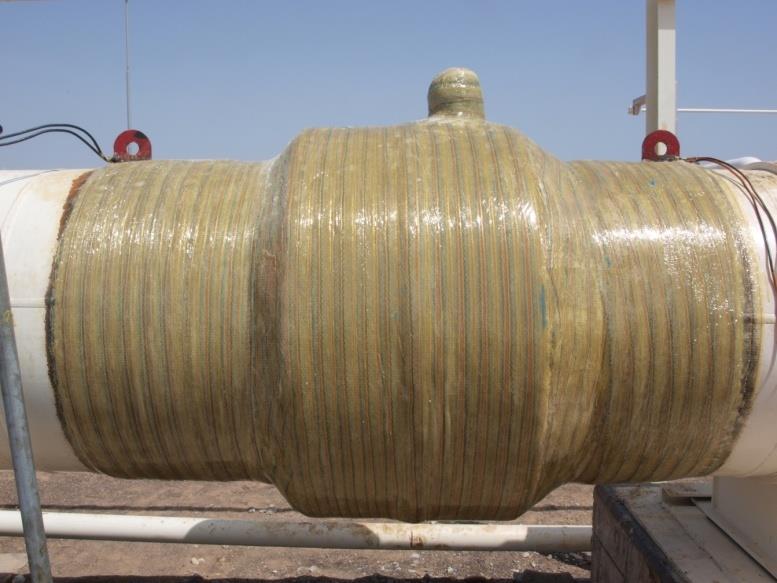
Client | Location |
---|---|
Major African Operator | Nigeria |
Scope
A 48” Main Oil Export line in Africa had sustained patches of external corrosion over a number of areas on the line. The client required an engineered composite repair to reinstate the integrity of the line.
The scope of work was to provide an engineered design, with 20 year repair lifetime, personnel & Technowrap ™ 2K HA materials to affect repair. Design pressure of the line was 19.6 bar g, with design temperature of 49ºC
Solution
The engineered design for the Technowrap™ 2K HA repair was performed according to ISO 24817.
Surface preparation to Sa2.5 was carried out by the client to ensure best bond of repair to substrate. The Technowrap™ repair was then installed according to ICR Installation Guidelines.
Existing concrete pipe supports were destructed and new concrete pipe supports cast and constructed to accommodate repair sites.
The client was also required to excavate trenches to allow the Technowrap™ personnel full access to the pipeline & allow the repair to be applied around the full circumference of the pipeline.
Results & Benefits
- Integrity of line was reinstated by repair
- 20 year design life
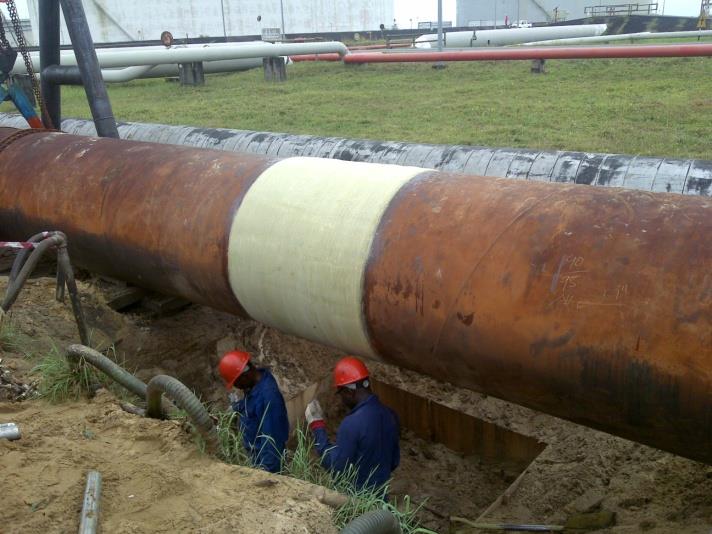
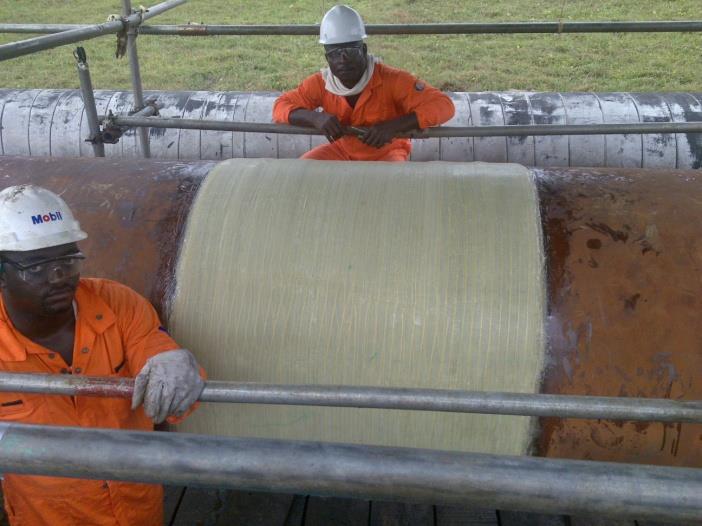
Date: January 2023
Client: Enerpro
Location: UKCS
Client challenge
In collaboration with Enerpro Group, a construction service company specialising in the repair and maintenance of Upstream Mobile Offshore Drilling Units, we were tasked with addressing a critical issue. Our expertise was sought to rectify a connection failure on an 8″ GRP Seawater Line for an offshore drilling contractor.
What we did
Technowrap™ is internationally recognised and all engineering is bespoke and completed in-house, in accordance with the latest issues of ISO 24817 and ASME PCC-2. In addition, our engineering designs are carried out to current code requirements and are validated by a range of testing.
Our team implemented a design using Technowrap™ with the following criteria:
- A 10-year lifetime
- Pressure of 4.5 bar
- Temperature of 90°C
It was specifically engineered to withstand the full applied load, considering the defect as a fully circumferential slot with an axial extent of 50mm. To complete the scope of work, we deployed one composite repair supervisor. Before installing the composite repair, we performed a live leak seal on the joint to ensure proper sealing. Once the defect had been sealed, eight layers of Technowrap™ 2K were meticulously applied to the defective area, improving its strength and durability.
Results
- The seamless installation of a Technowrap™ composite repair not only ensured an extended lifetime of 10 years but also marked the successful completion of the project within the allocated timeframe and budget, prioritising safety at every step. These expert repairs facilitated comprehensive rehabilitation without causing significant operational disruptions, resulting in substantial cost savings compared to a complete replacement. Furthermore, the absence of any hot work requirement significantly mitigated safety risks, further enhancing the overall project safety.
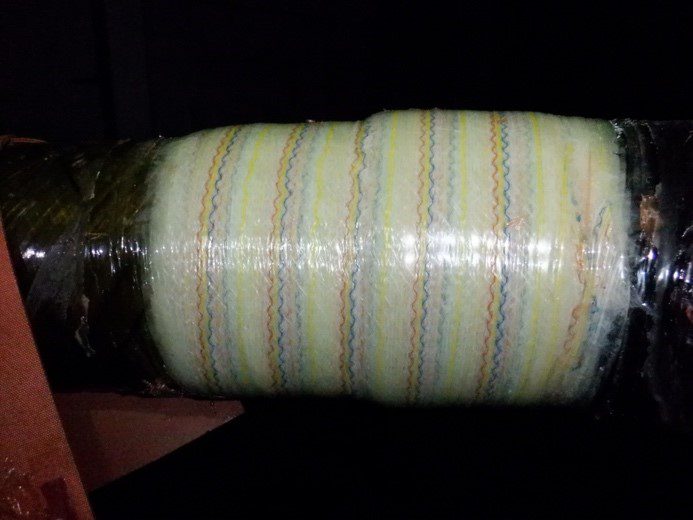
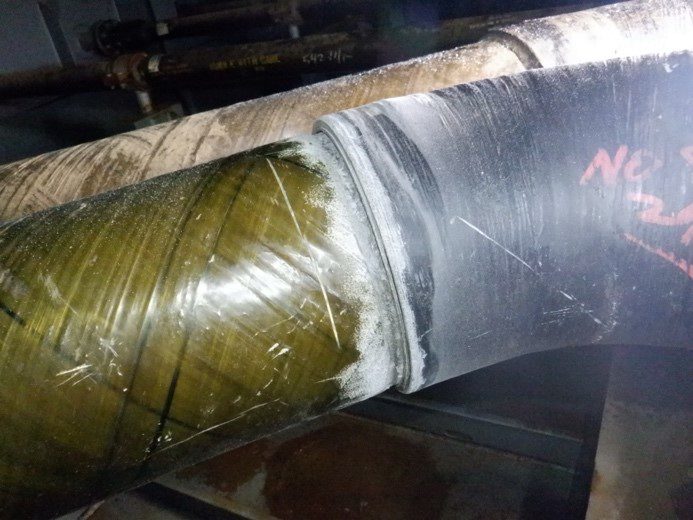
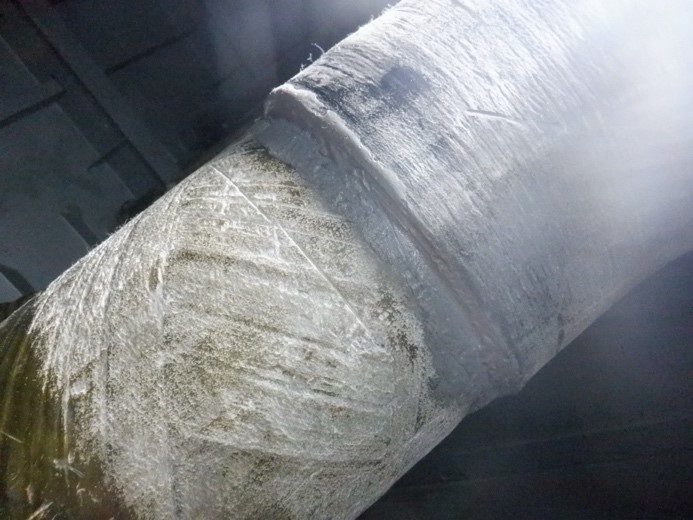
