Challenges
- Hot work restrictions
- Multiple installations
- Hydrocarbon line media
- Space constraints
Benefits
- No hot work
- Increased safety
- Cost-effective solution
- Quick installations
- Cold work technology
Scope
A multinational energy company was approached by our Thailand-based partner, Pipeline and Piling Services Co (PAPS), to resolve the integrity of an open drain utility line at its offshore central processing plant. Located in the Gulf of Thailand, PAPS identified that ICR’s weldless technology, Quickflange™, would be an optimal solution for repairing the 3” galvanised pipeline which was made from seamless carbon steel.
After assessing the pipeline, ICR’s experts determined that multiple Quickflange™ installations were required. To ensure the project was cost-effective and timely, PAPS technicians, who are trained and qualified to complete Quickflange™ installations in the region, were mobilised at short notice to complete the scope.
Solution
Once the technical review was complete and the solution was designed, the necessary tools, flanges, and personnel were quickly mobilised to the site. After isolating the lines, straight cuts to the pipe were prepared in each of the repair zones to allow the project technicians to progress through the various installations. All repairs utilised a 3” Sch160 Carbon Steel 150# Quickflange™ connector, each of which were hydrostatically tested after each installation to verify the integrity of the repair.
Results
Despite the considerable number of installations required and the limited space in some repair zones, the project was completed safely with maximum efficiency. From initial reviews to offshore work and final demobilisation, each stage of the project was completed on time and within budget.
Our partner completed 17 Quickflange™ installations in just 4 days. By utilising Quickflange™ technology over traditional welding techniques, our client cut the project timeline by an estimated 30 days. The outstanding results have led to the identification of additional scopes with the operator, securing further collaboration with ICR in 2025.
To discover more about our Quickflange™ technology, or to submit an enquiry to our team, please click here.
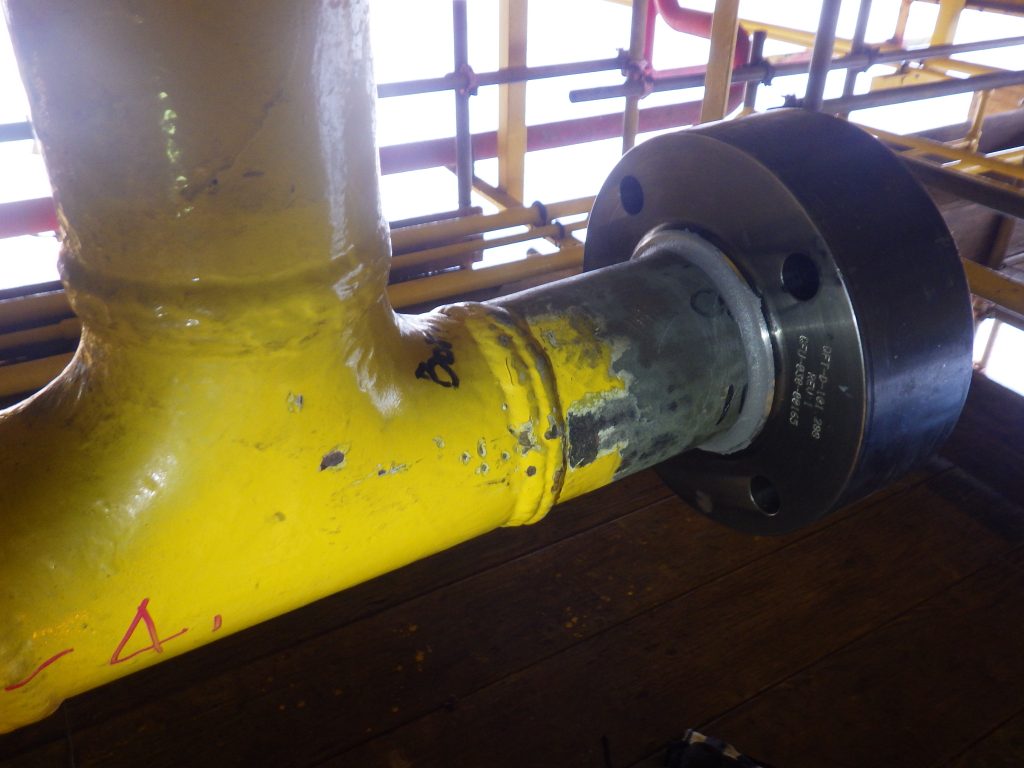
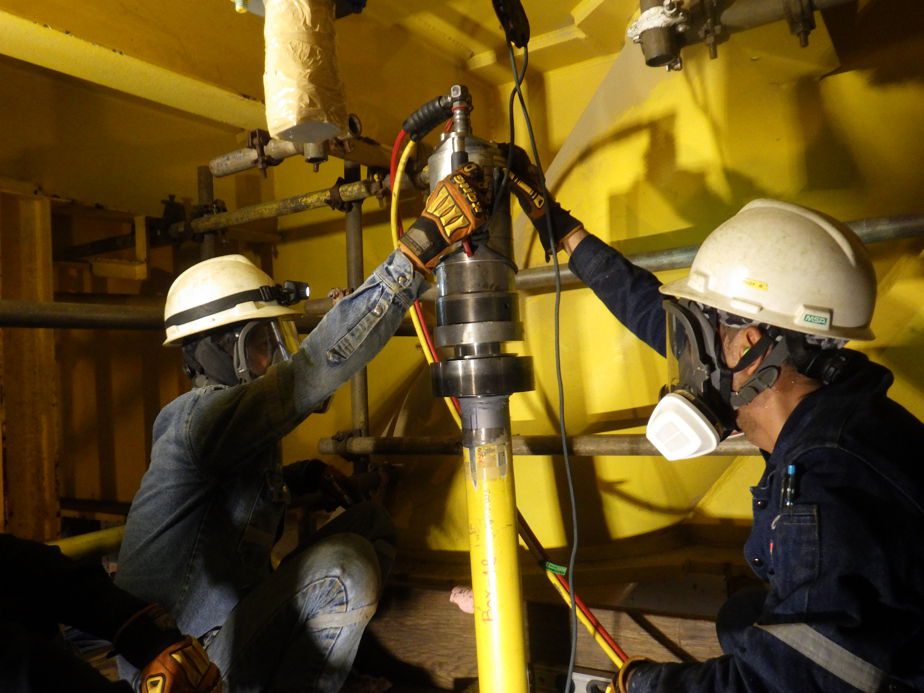
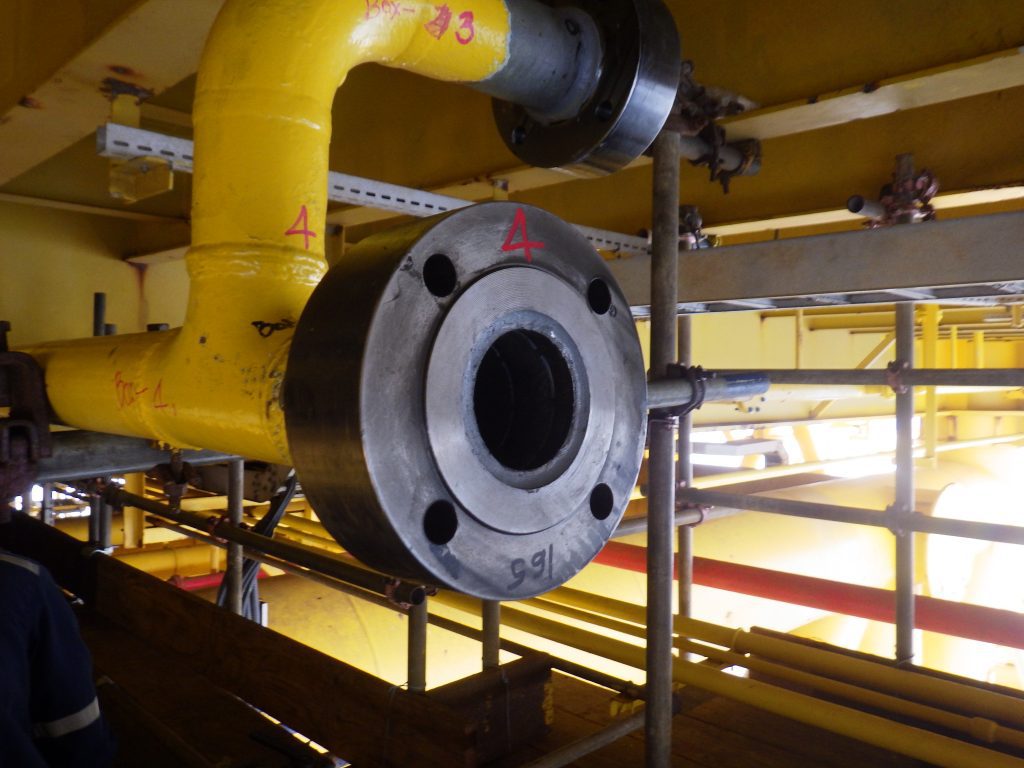
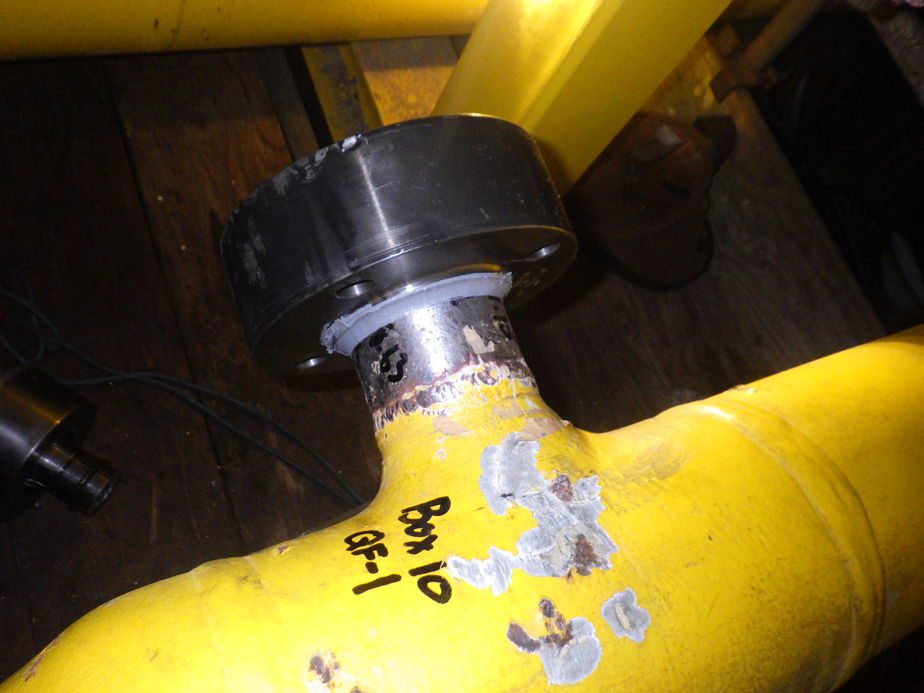
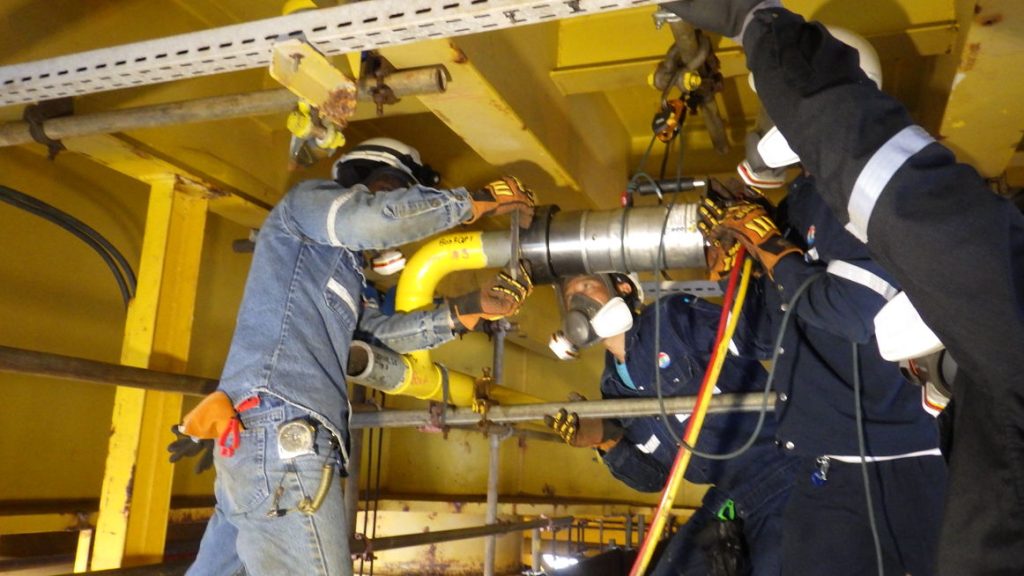
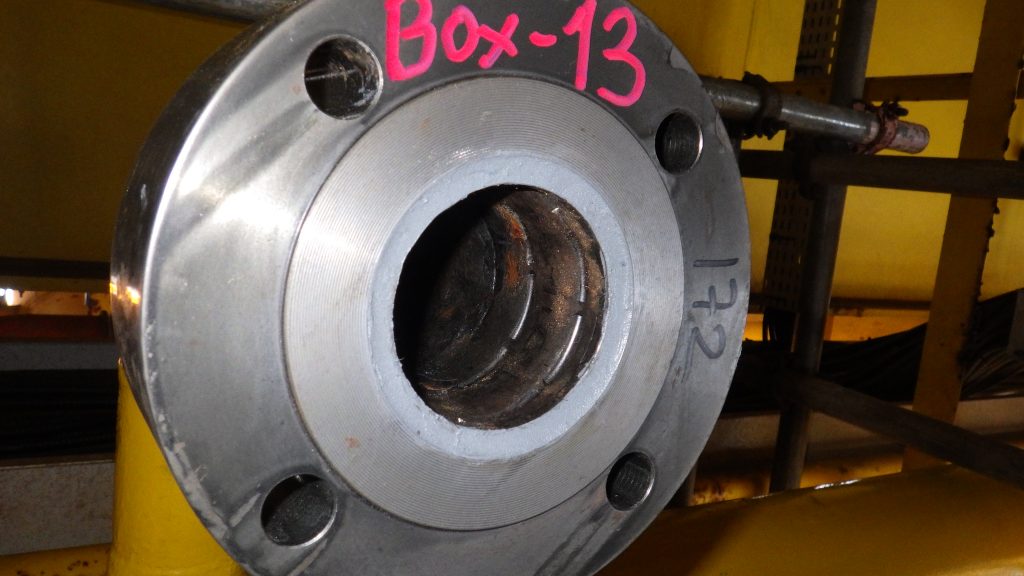
Challenges
- Remote location
- Extreme environment
- High-grade carbon steel
Benefits
- No hot work
- Minimal downtime
- Increased safety
Scope
The primary objective of this project involved the removal and replacement of a deteriorated section of API-5L Grade X42 line pipe, which had suffered significant corrosion over time. This required the installation of a prefabricated spool measuring 50 metres in length. The worksite’s remote desert location added unique logistical challenges, including limited accessibility, extreme environmental conditions, and the need for precise coordination to ensure seamless delivery and installation of the replacement spool. Despite these constraints, the project was designed to ensure minimal disruption to operations while adhering to strict industry standards and safety protocols.
Solution
Quickflange™ was selected as the preferred cold work repair solution. Trained personnel from our local partner were mobilised to the site to carry out the activations. After isolating the pipeline, a cold cut was performed on the corroded pipe section, and the pipe ends were prepared to accommodate the 6″ Sch40 Class 600 API-5L Grade X42 Quickflange™ connectors. Upon completion of the installations, each connector underwent hydrostatic testing in accordance with the client’s specifications.
Result
The successful installations were completed within a single shift. From pipe cutting to final activation, both installations were finished in a combined total of two hours. By employing a cold work method, the need for hot work was entirely eliminated, significantly reducing risks and ensuring strict compliance with safety protocols. This approach not only minimised downtime but also demonstrated the effectiveness of Quickflange™ in delivering fast, reliable pipeline repairs.
For more on our Quickflange™ technology, click here.
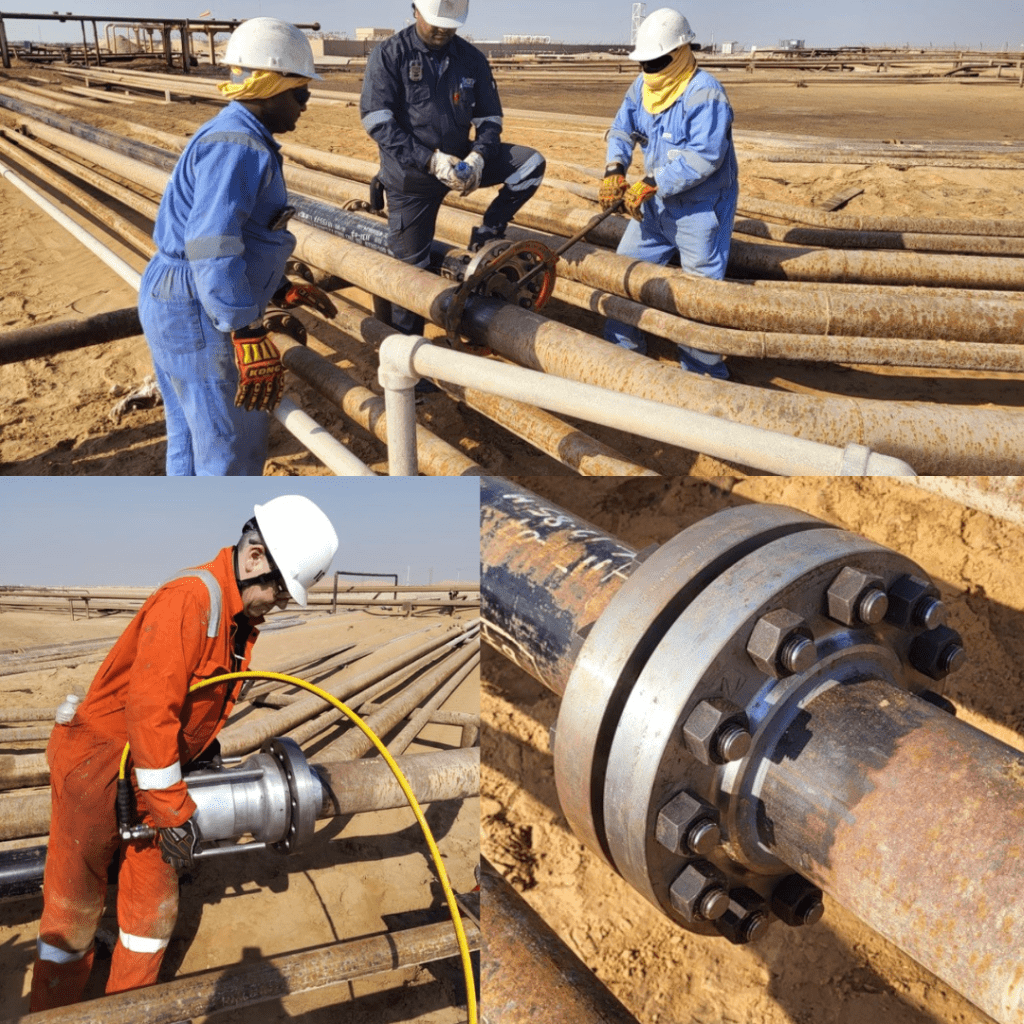
Client: North Sea operator
Location: United Kingdom – North Sea
Challenges
- Hydrocarbon flare line
- Hot work restrictions
- Installation at height
Benefits
- No hot work
- Increased safety
- Cost-effective solution
- Large bore connectors
Scope
A North Sea operator identified a critical issue with its high-pressure flare collection header. The 10″ blowdown pipework was at risk of low-temperature embrittlement and required urgent modification. The repair posed several challenges, including the hydrocarbon nature of the line, its five-metre height, and the constrained shutdown window. To ensure a safe and efficient resolution, the operator collaborated with Katoni Engineering, who designed and engineered the pipework replacement using Quickflange™ technology.
Solution
The scope included the installation of a 10” Sch20 150# Carbon Steel Quickflange™. Before installation, temperature and impact testing requirements were carefully reviewed, with Quickflange™ meeting all compliance standards. The existing pipework was removed using clamshell cutting equipment, ensuring a precise, straight cut for the Quickflange™ installation. Following installation, a hydrostatic strength test was successfully performed using a flange joint tester, verifying proper installation with no leak paths.
Result
The Quickflange™ installation was completed in just one shift, allowing the team to efficiently progress through the remaining shutdown tasks. The elimination of hot work was particularly significant given the hazardous environment, enhancing both safety and operational efficiency. Compared to conventional welding methods, Quickflange™ offered a more economical solution while minimising downtime. Additionally, the client benefited from the availability of large-bore Quickflange™ connectors, perfectly suited for the specific work scope requirements.
For more on our Quickflange™ technology, click here.
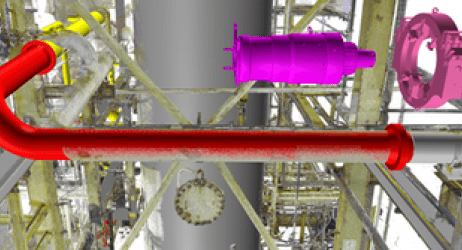
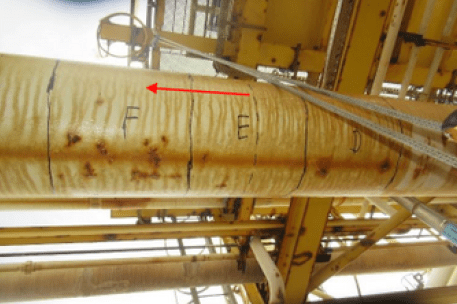
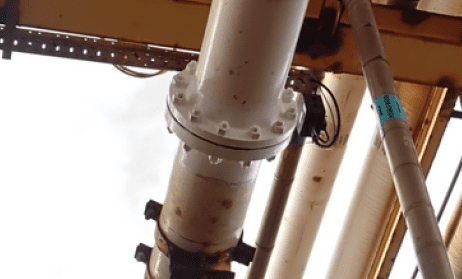
Client Challenge
Our client, an energy operator in Azerbaijan, faced the challenge of tying in new 6” & 8” carbon steel spools on the asset’s drill floor low-pressure mud lines. Traditional welding methods posed risks due to the presence of hydrocarbons, necessitating a cold-work solution to avoid hot work and mitigate associated hazards. Our client urgently required a reliable method to conduct the tie-ins without compromising safety, operational downtime, or incurring additional costs.
What We Did
In response to our client’s challenge, our weldless connector technology, Quickflange, was the preferred cold-work solution to facilitate the pipeline tie-ins. Quickflange’s innovative design eliminates the need for hot work, habitats, and associated safety risks, ensuring a safe and efficient repair process.
Collaborating with our partner, Khazar Engineering in Azerbaijan, our team mobilised equipment and trained technicians to execute the repair swiftly and effectively. Khazar’s trained technicians undertook line preparation, cold cutting of the pipe, and the installation of Quickflange connectors. Additionally, they provided essential support for the installation of the new spool tie-in sections, ensuring seamless integration with the existing pipeline infrastructure.
Results:
The implementation of Quickflange enabled a rapid turnaround for the client, addressing the repair needs on short notice without compromising operational efficiency. The elimination of hot work not only minimized downtime but also resulted in substantial cost savings compared to traditional welding methods.
With Quickflange, our client achieved a permanent repair solution that meets safety standards while optimizing operational resources and costs. The successful collaboration between ICR, Khazar Engineering, and the client highlights the effectiveness that Quickflange generates when addressing complex repair challenges in offshore environments.
Client challenge
A major North Sea operator encountered a significant challenge when dealing with a leaking 4” Sch80 carbon steel nozzle crucial for a diesel tank’s operation. Complicating matters, the application of hot work methods was obstructed by time constraints and extreme space restrictions in the confined void where the nozzle was located, rendering conventional welding impractical.
What we did
This project presented several challenges, including the proximity of an i-beam, tight clearances, limited rigging options, and confined spaces. Within a 48-hour timeframe from the initial request, we successfully mobilised all necessary equipment, minimising downtime for our client. Post-installation, a thorough testing of the Quickflange™ joint ensured its integrity, conforming to both industry and client standards.
Results
The implementation of our weldless connector technology, Quickflange™, resulted favorable outcomes for our client. The repair process eliminated the need for hot work, addressing safety concerns and aligning with the client’s operational restrictions. Our tailored approach navigated extreme space restrictions, surpassing challenges unmatched by competitors.
The swift mobilisation of equipment within an impressive 48-hour timeframe significantly reduced downtime and operational disruptions. This rapid resolution showcased the effectiveness of Quickflange™ technology and demonstrated our capacity to deliver innovative solutions under challenging circumstances.
The impact included enhanced safety measures, increased operational efficiency, and substantial cost reductions associated with the repair process. This case study underscores our commitment to providing comprehensive solutions that prioritise safety, efficiency, and cost-effectiveness for our clients.

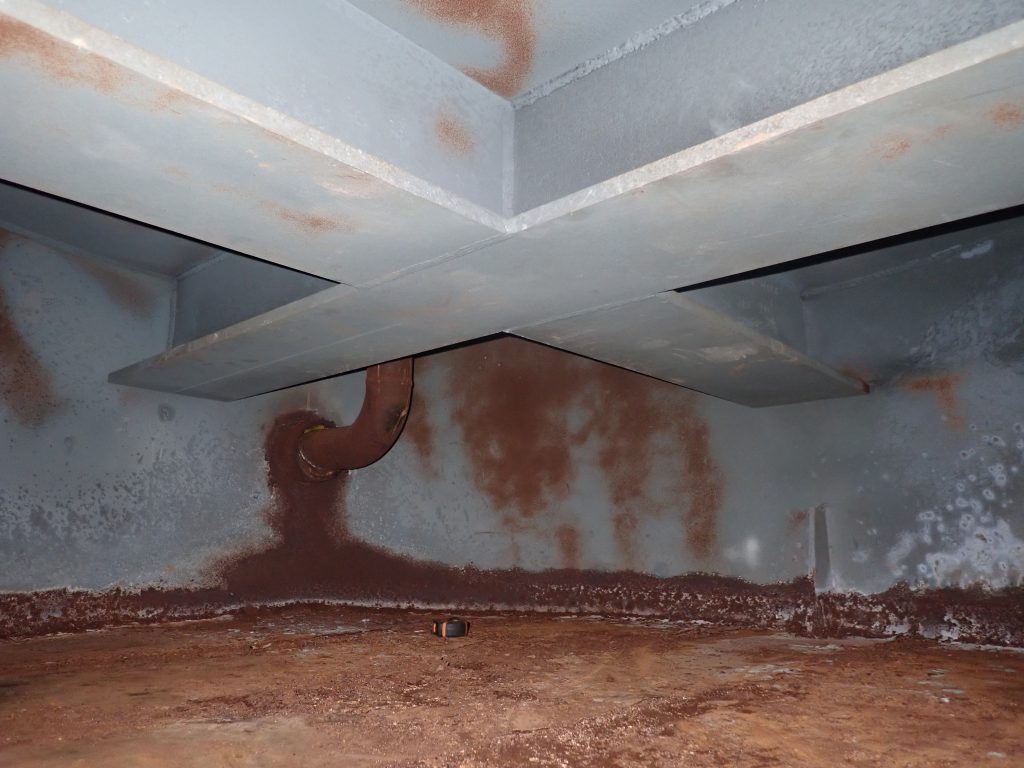
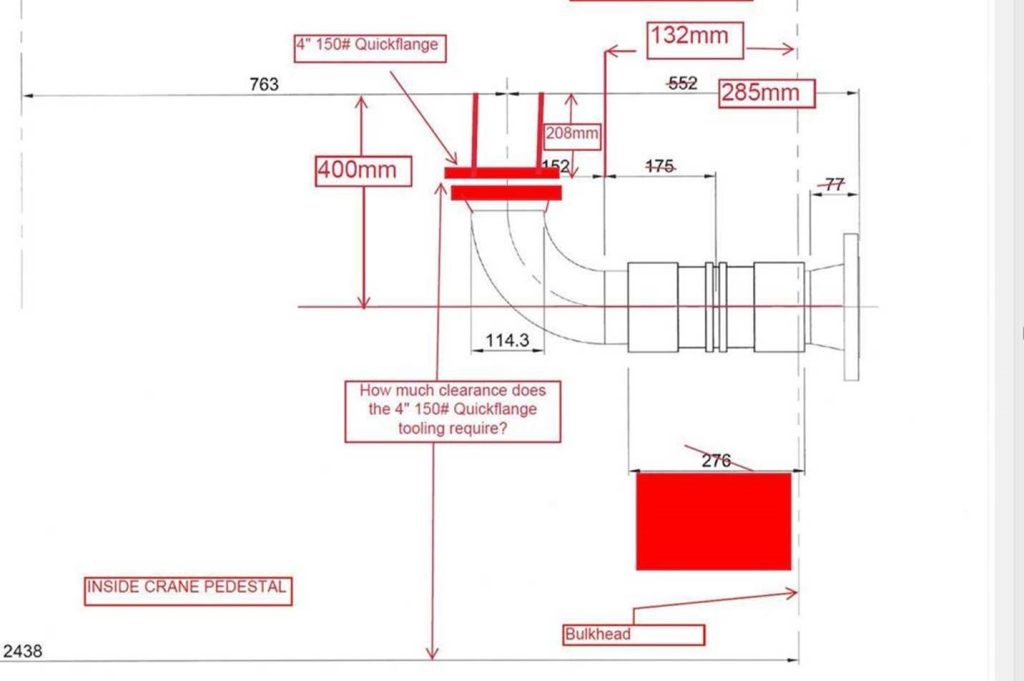
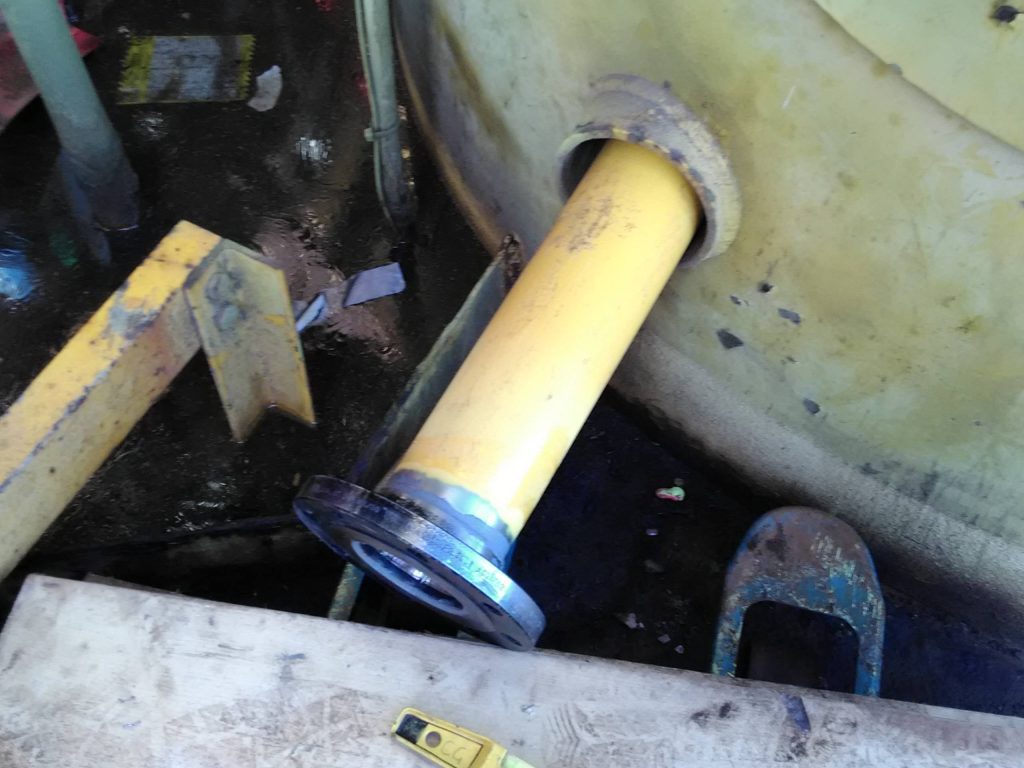
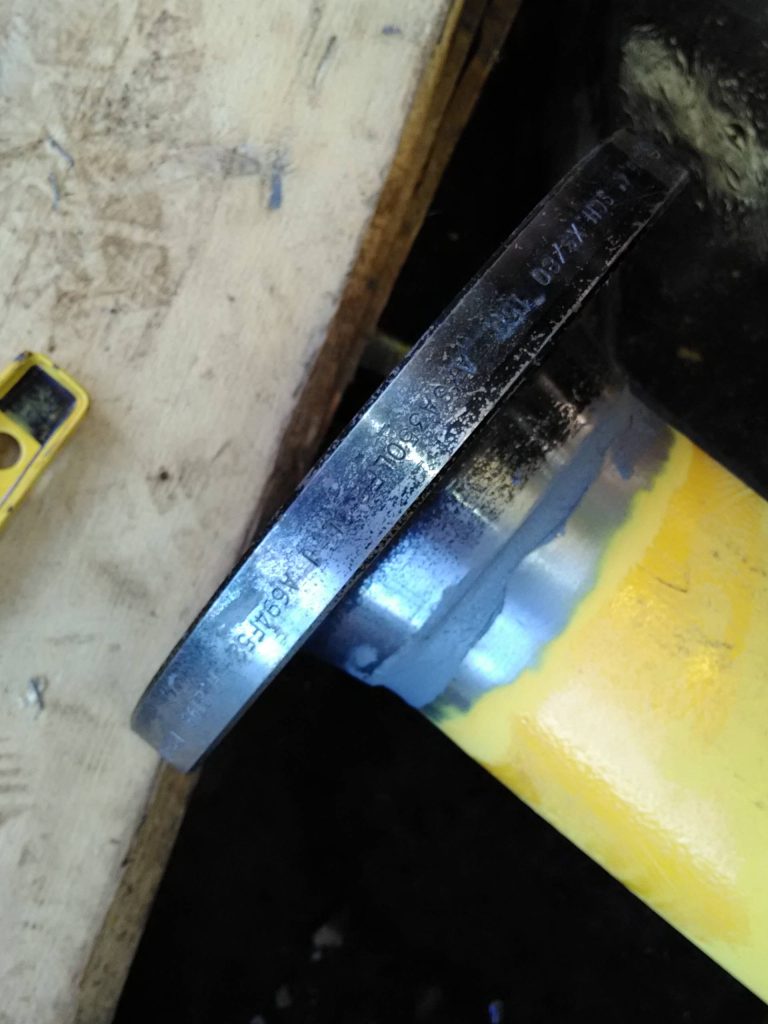
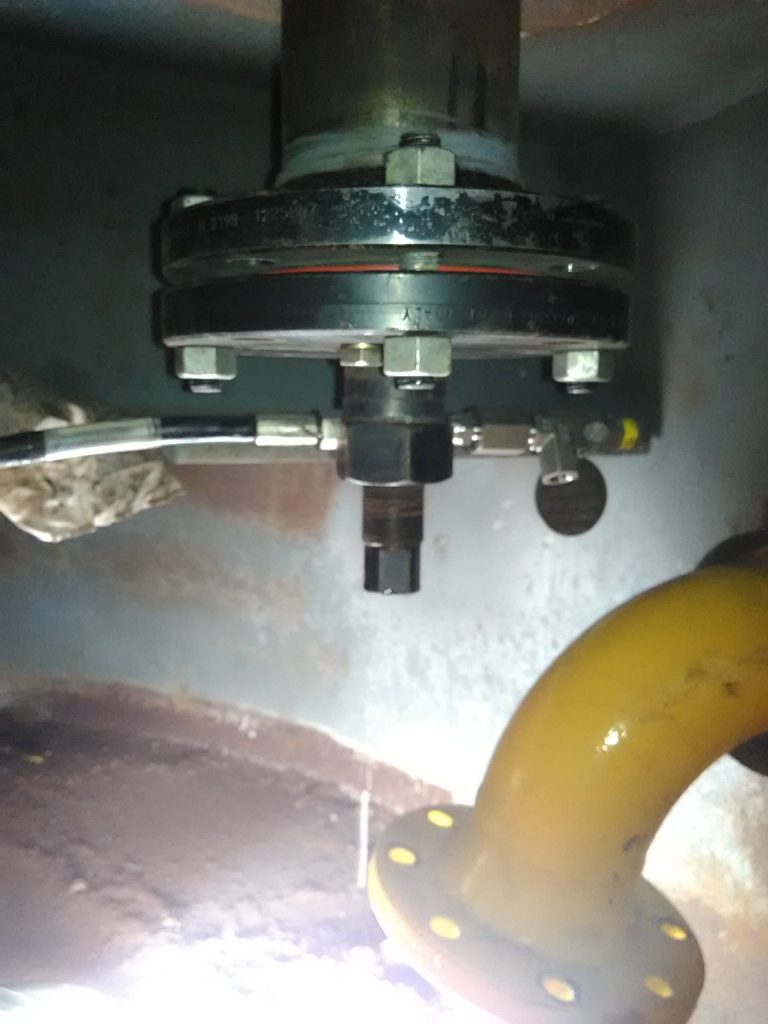
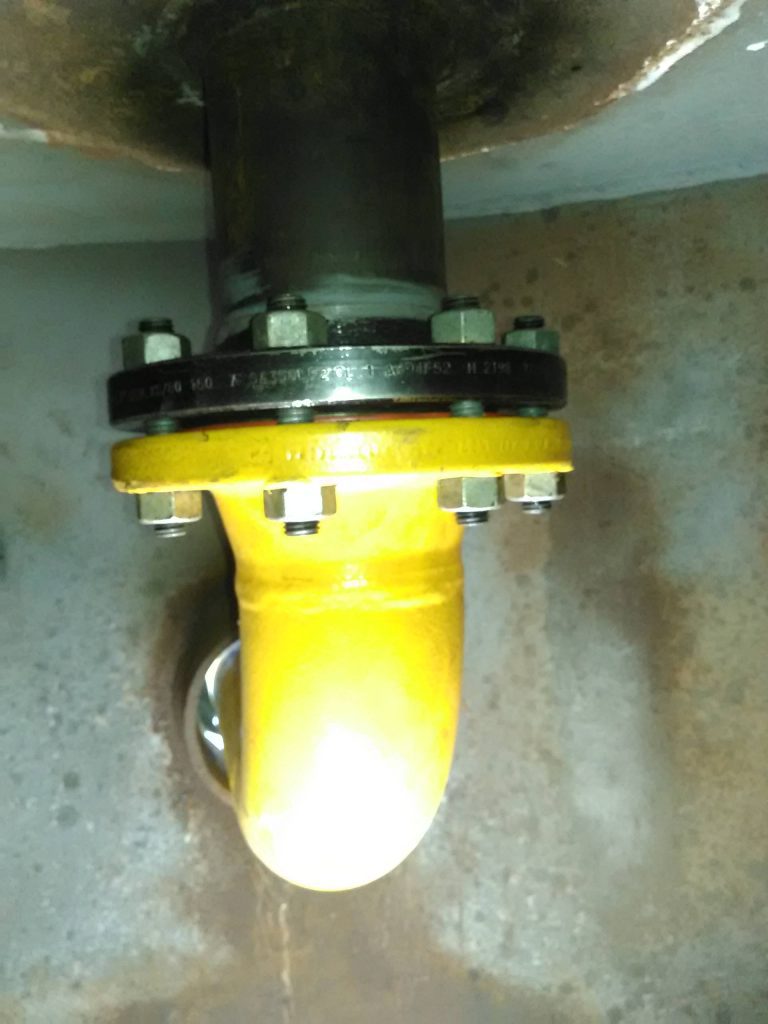
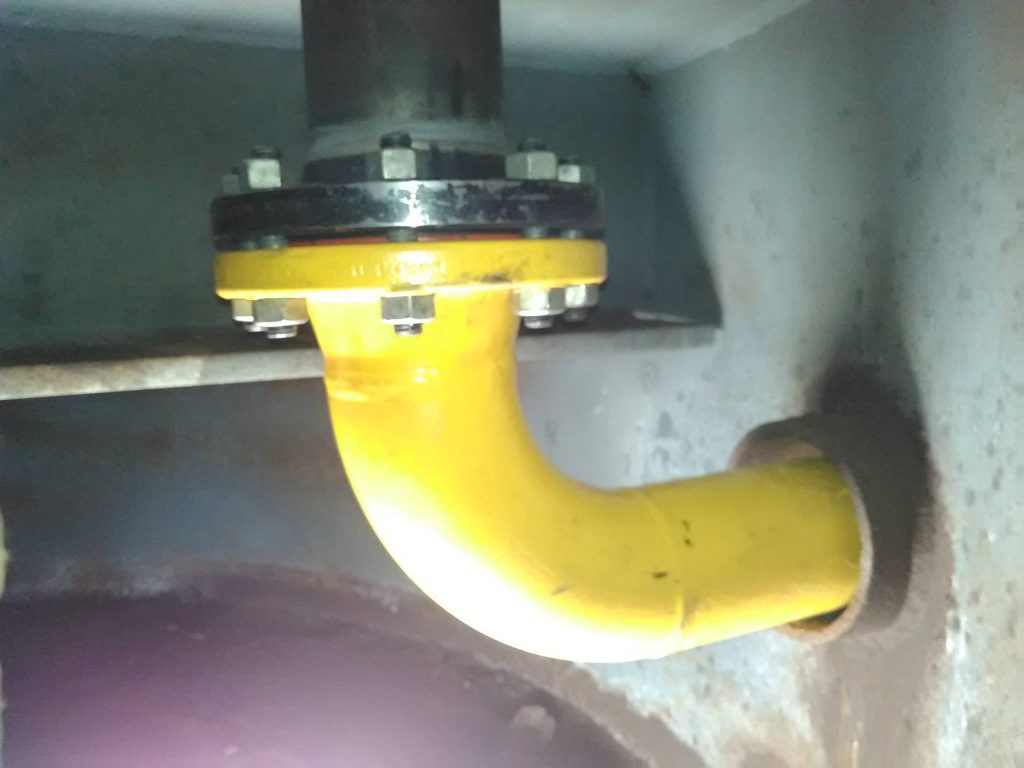
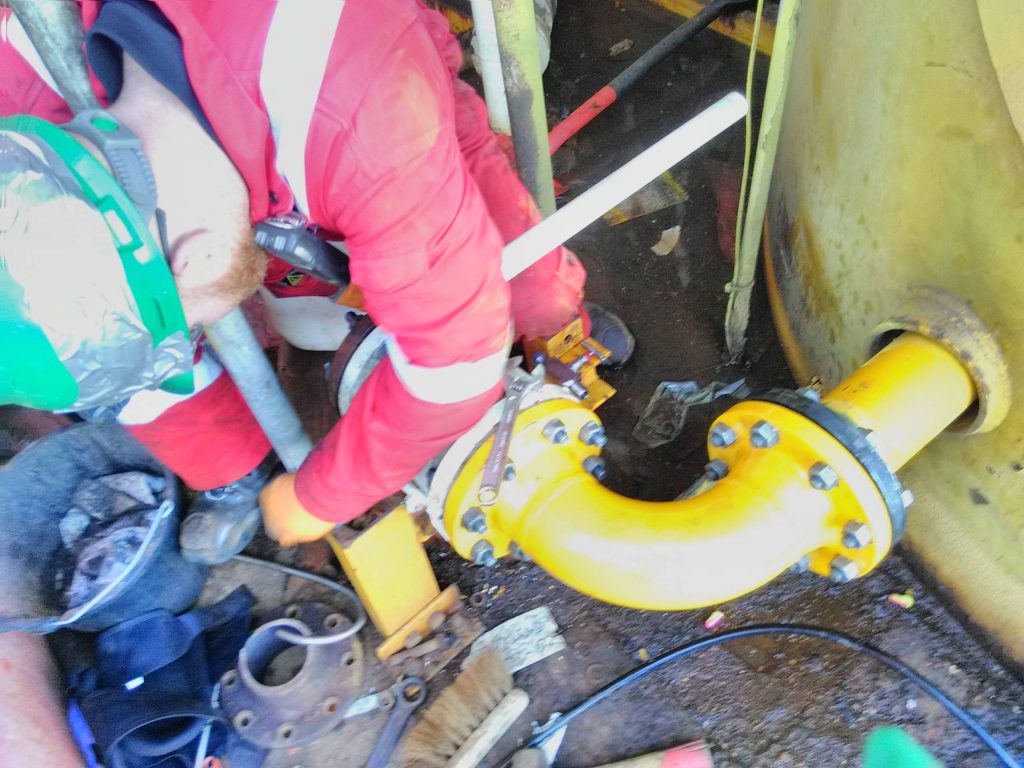
Client: Local EPC
Asset: Offshore platform
Result: Replacement of critical hydrocarbon, utility gas and air lines
Client Challenge
Our client faced a critical challenge in designing in the replacement of failing hydrocarbon, utility gas and air lines of various sizes. They also required the supply of a 3” Quickflange to enable the blinding of a line that would no longer be in use. The replacement of these essential lines was time-sensitive, as it required shutdowns to ensure safety and continued operations.
What we did
Our approach involved several key steps to address the client’s challenge of replacing the failing lines across 1×2”, 1×3” utility lines, 3x 1.5” lines, 1x 8” and 1×10” hydrocarbon sizes effectively:
3D modelling: We provided 3D modelling to help with the planning and that the cutting, Quickflange™ tooling and test equipment could be effectively utilised within the available space.
Manufacturing of Quickflanges: We manufactured galvanised 2” and 3” Quickflanges for the initial part of the project. For the hydrocarbon lines, we custom-forged Quickflanges and painted them according to operator specifications.
Match boring: All lines required match boring before installation, which we factored in and completed as part of the planning and installation process.
Collaboration: We worked closely with our client to transform plans into quotes, establish timelines, and determine the necessary workforce for the project.
Contingency planning: Recognising the critical nature of the project, we provided contingency tooling and kept additional tools ready in our warehouse for immediate dispatch if required.
Technician support: We supplied two highly trained technicians with expertise in Quickflange™ installation and match boring from our machining division. This allowed for flexible day and night shifts as necessary to meet the time-critical installation requirements.
Minimising downtime: Throughout the project, we took every aspect into consideration to minimise the shutdown period and expedite the resumption of production. Quickflange™ technology was instrumental in achieving a significant reduction in time compared to traditional welding. All cutting, match boring, and installations across the platform were successfully completed in just three days.
Results
Our collaborative approach, advanced Quickflange™ technology, and comprehensive planning resulted in a successful outcome.
The replacement of critical hydrocarbon, utility gas and air lines was completed efficiently, reducing downtime. The project was accomplished in just three days; a 50% reduction in time compared to traditional welding methods. The client achieved their goal of ensuring the safety and reliability of their hydrocarbon, gas and air lines, supporting uninterrupted operations.
Date: August 2023
Client: Leading Canadian Steel Manufacturer
Location: Canada
Client challenge
A leading Canadian steel manufacturer was faced with a critical challenge where they needed to demonstrate their ability to efficiently serve a variety of industries while also addressing two main concerns—timeframe and hot working. Specifically, the client had a pressing issue with faulty pipework that required immediate attention. They required a reliable solution that could not only meet their stringent timeframe requirements but also eliminate the need for hot working, and minimise safety risks and costs.
What we did
In response to our client’s challenge, we provided a comprehensive and efficient solution to showcase our capabilities and expertise with the following:
- Quickflange tool deployment: To minimize lead times and shipping costs, we utilized our hub in Houston to deploy our specialized 3” STD Quickflange tool. This tool was essential for creating gas-tight connections without the need for hot working.
- Custom spool fabrication: Working closely with our client, we designed and fabricated a bespoke spool to replace the faulty pipework. This spool was engineered to seamlessly integrate with the existing pipeline infrastructure.
- Onsite expertise: We ensured that trained personnel were available onsite to oversee the installation process, guaranteeing that the replacement spool and Quickflanges were securely and efficiently connected.
- Gas tight connection: Following the installation, we utilized our 3” STD Quickflanges to create a gas-tight connection, ensuring the integrity of the entire pipeline system. Our Quickflanges not only eliminated the need for hot working but also offered a reliable and efficient solution.
Results
We delivered a timely resolution by leveraging our global footprint and deploying resources from the Americas hub, meeting the client’s stringent timeframe requirements and minimizing downtime, ultimately saving them valuable time and money. Furthermore, our Quickflange solution eliminated the need for hot working, enhancing safety and reducing associated costs. The successful activation of the Quickflange tooling and the seamless integration of a bespoke spool was effective and underscored our ability to provide trusted solutions across diverse industries.
This project also served as a showcase of our extensive global footprint, demonstrating our commitment to offering reliable solutions worldwide while serving Canada efficiently from the Americas hub.
Our Quickflange solution not only addressed our client’s immediate challenges, but also demonstrated our capability to serve diverse industries efficiently. This case serves as a strong example of our commitment to providing innovative solutions while minimizing lead times and costs, ultimately ensuring client satisfaction and industry trust.
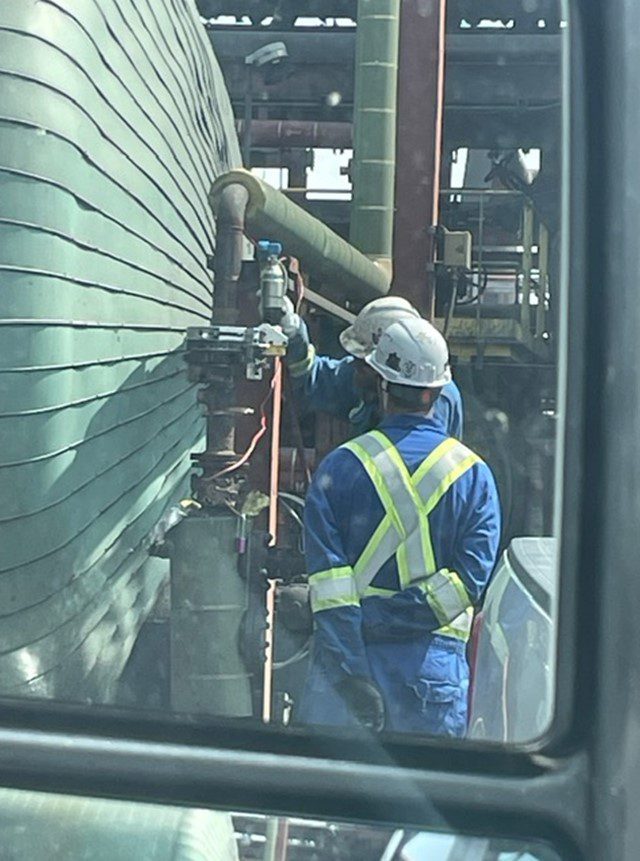
Date: July 2023
Client: Drilling Contractor
Location: UK North Sea
Client challenge
A North Sea drilling contractor faced a challenge with rerouting a pipeline system for their drilling package on an offshore rig. They needed a solution that was not only safer but also more cost-effective and time-saving than traditional hot work methods.
What we did
To meet our client’s needs, we obtained approval for a 10” carbon steel 150# Quickflange™ connector, which was ideal for horizontal installation on the asset’s lower deck. Despite facing initial discrepancies with the wall thickness from the listed piping specifications, we included extra match boring equipment in the quotation along with installation tools, testing, and cutting equipment.
We used orbital cutting equipment to cut the pipe and manually prepared the installation area. Wall thickness checks revealed the need for match boring to align the pipe’s wall thickness schedule with the supplied Quickflange™ connector. After completing the match boring, the installation proceeded successfully, passing a hydrostatic leak test.
Results
Our solution resulted in highly positive outcomes for our client. The installation process was significantly faster compared to traditional hot work methods, and the Quickflange™ option provided a simpler, more straightforward installation which was also more cost effective, without the need for permits and habitats. Our technician, proficient in Quickflange™ installation, pipe cutting, and match boring, proved invaluable as only one technician was required, saving space on the client’s onboard asset. Overall, the successful project demonstrated the advantages of our approach in terms of efficiency, safety, and cost-effectiveness.
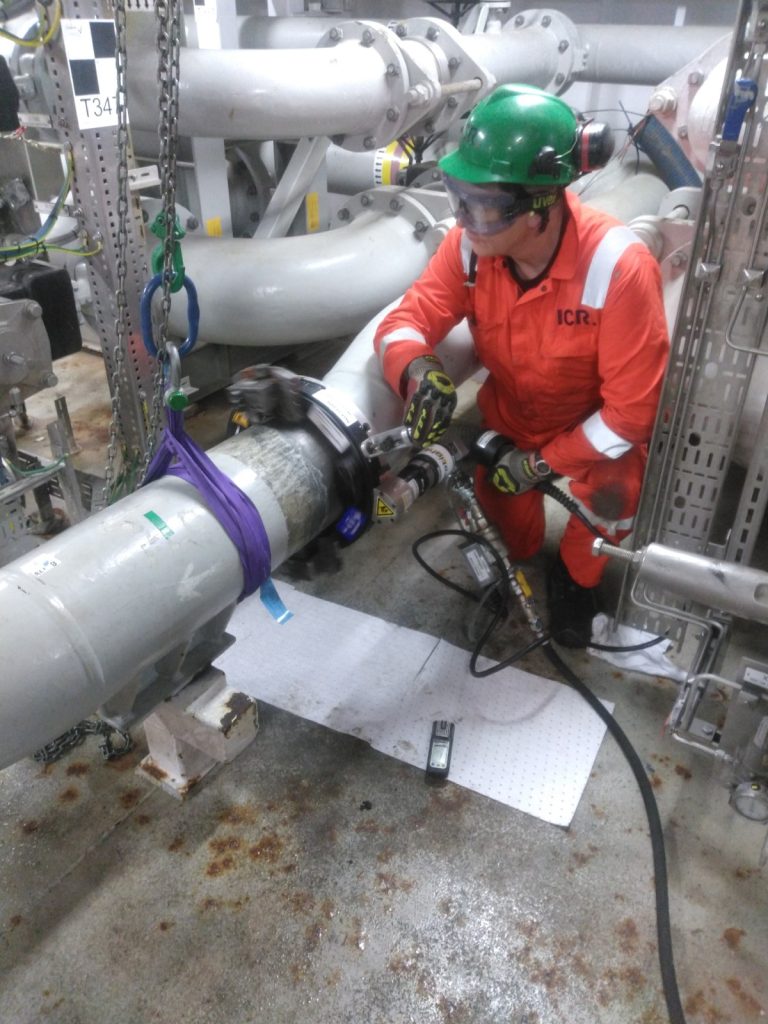
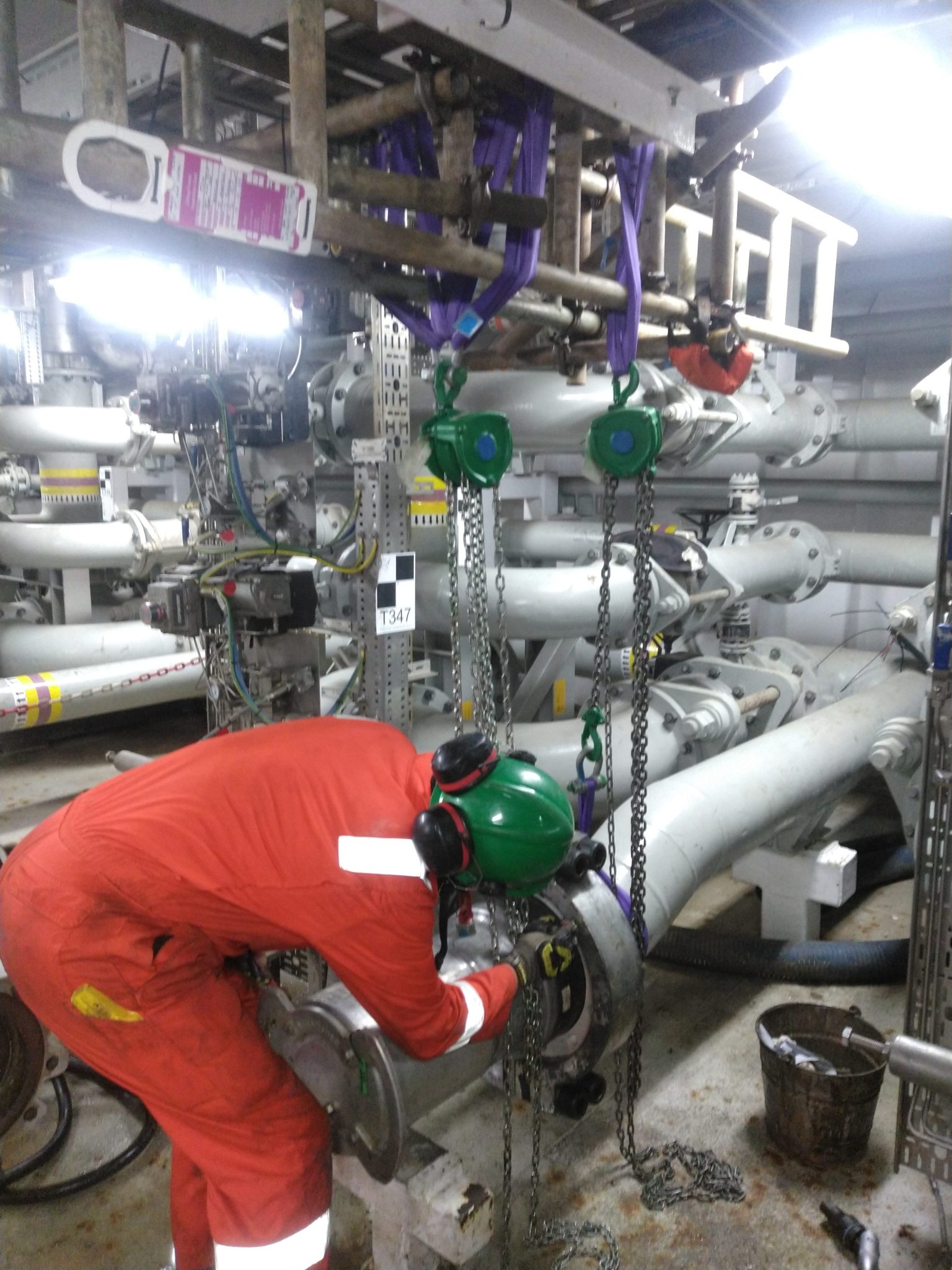
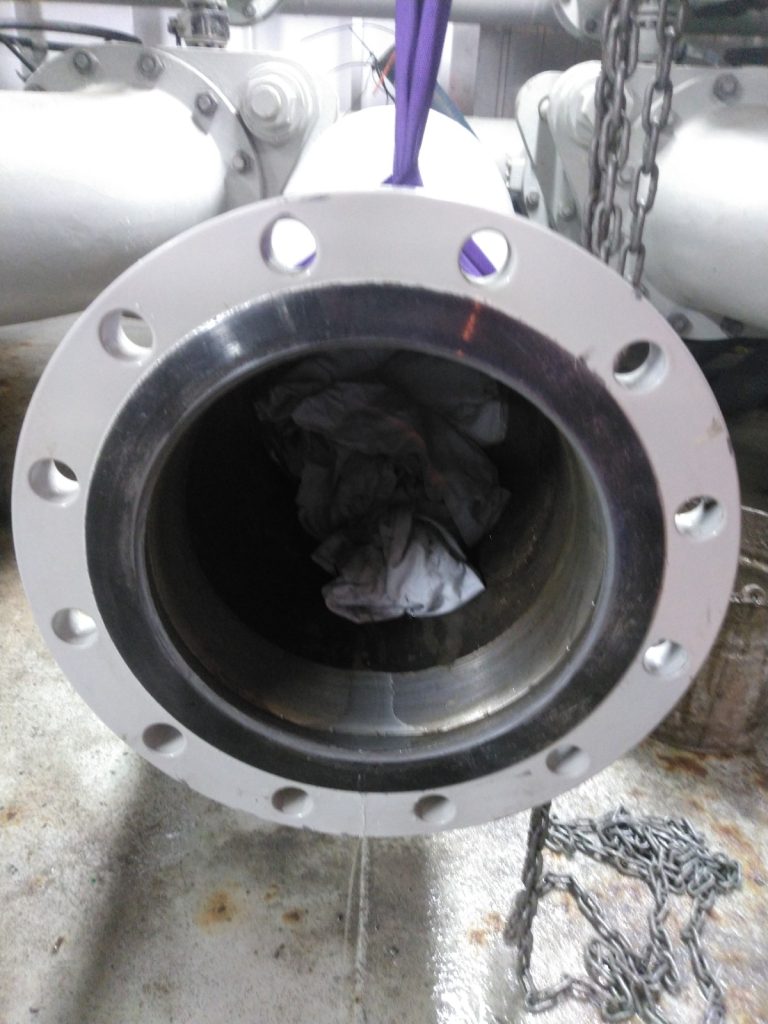
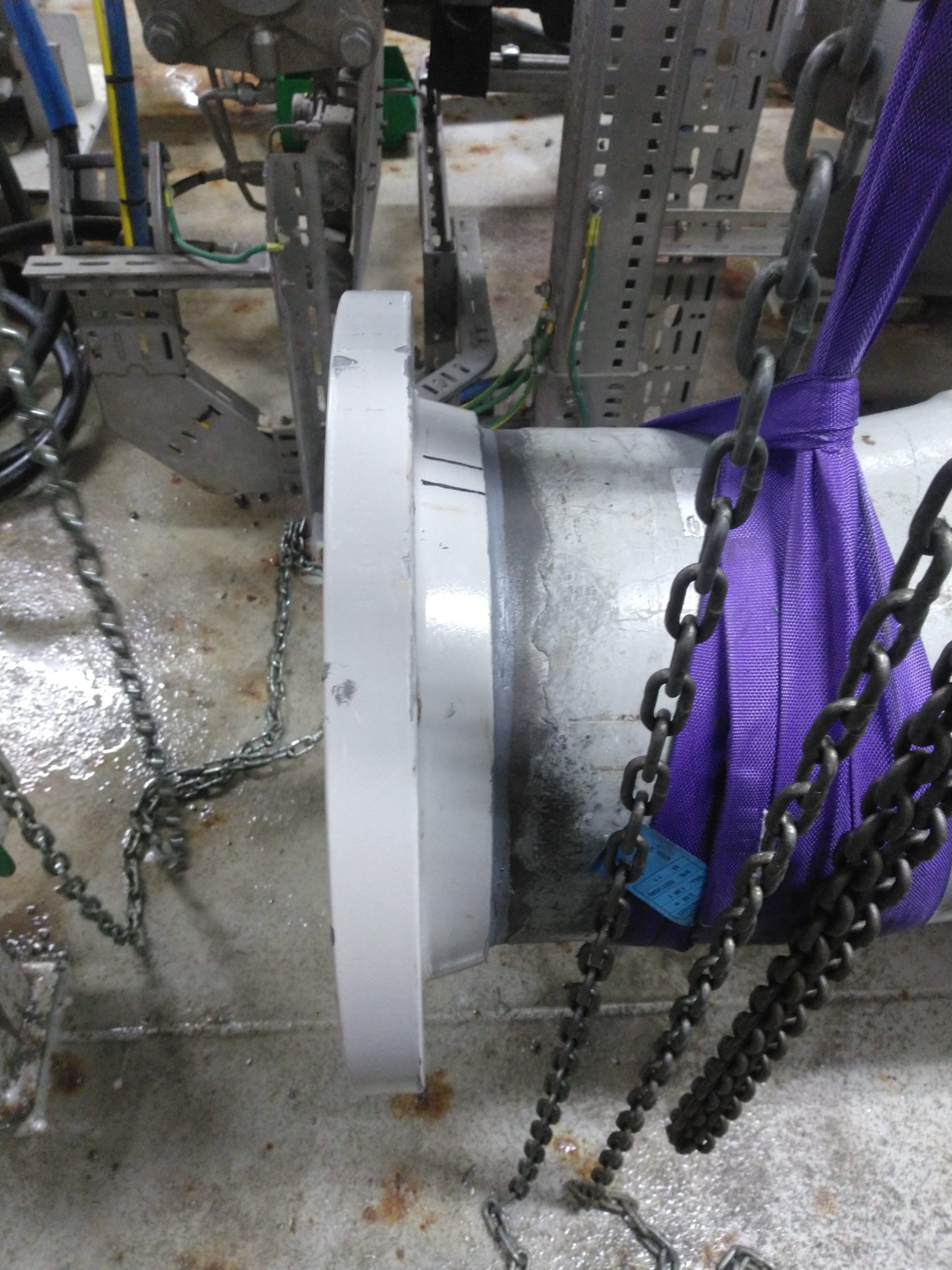
Client: Major North Sea operator
Location: Central North Sea
Scope
Quickflange™ technology was identified to repair a leaking 4” Sch80 carbon steel nozzle feeding from a diesel tank. Hot work was not an option due to both time constraints and the extreme space restrictions with the nozzle being located in a void which was too small for a welding habitat.
Solution
ICR’s standard installation equipment was mobilised, which was able to contend with the tight clearance, limited rigging options and space restrictions – having only limited clearance to the nearest I-beam obstruction. The technician mobilised was ‘confined space entry’ trained in order to complete the install in a safe manner. All items were mobilised within 48hours, minimising the client’s downtime. The Quickflange™ joint was also tested post installation, to ensure the integrity of the connection and that it conformed to industry and client standard.
Results & Benefits
- No hot work
- Extreme space restrictions were met with no issues, something no other competitor could match
- Equipment mobilised 48hours from initial request
- Reduced cost due to minimal downtime
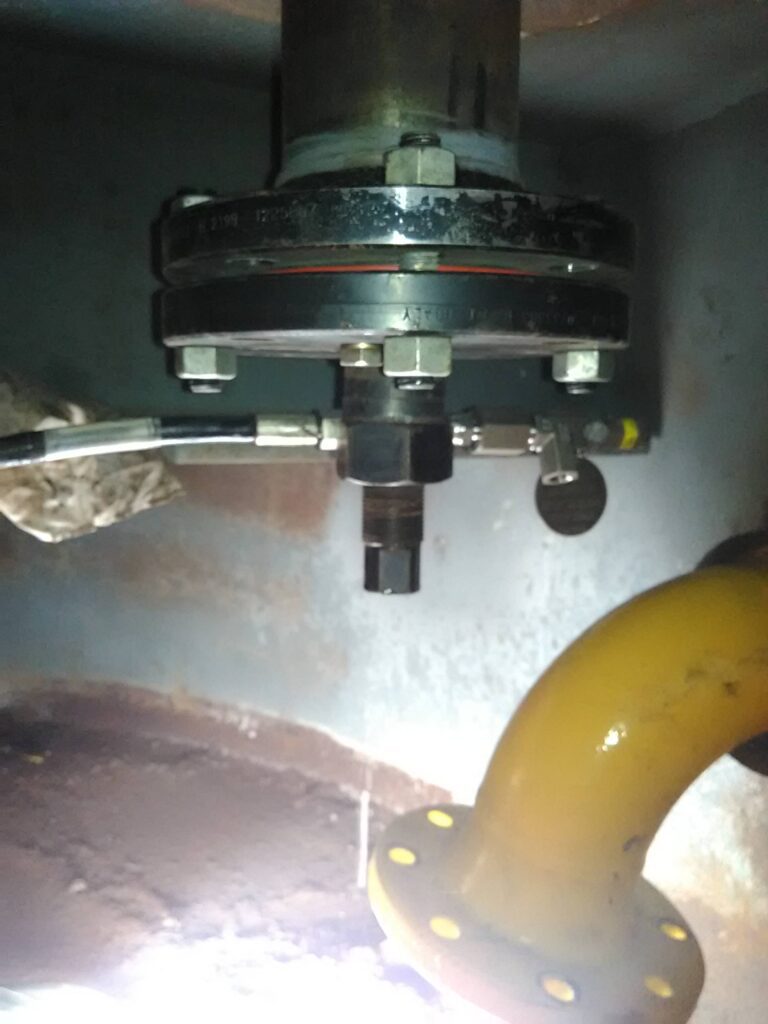
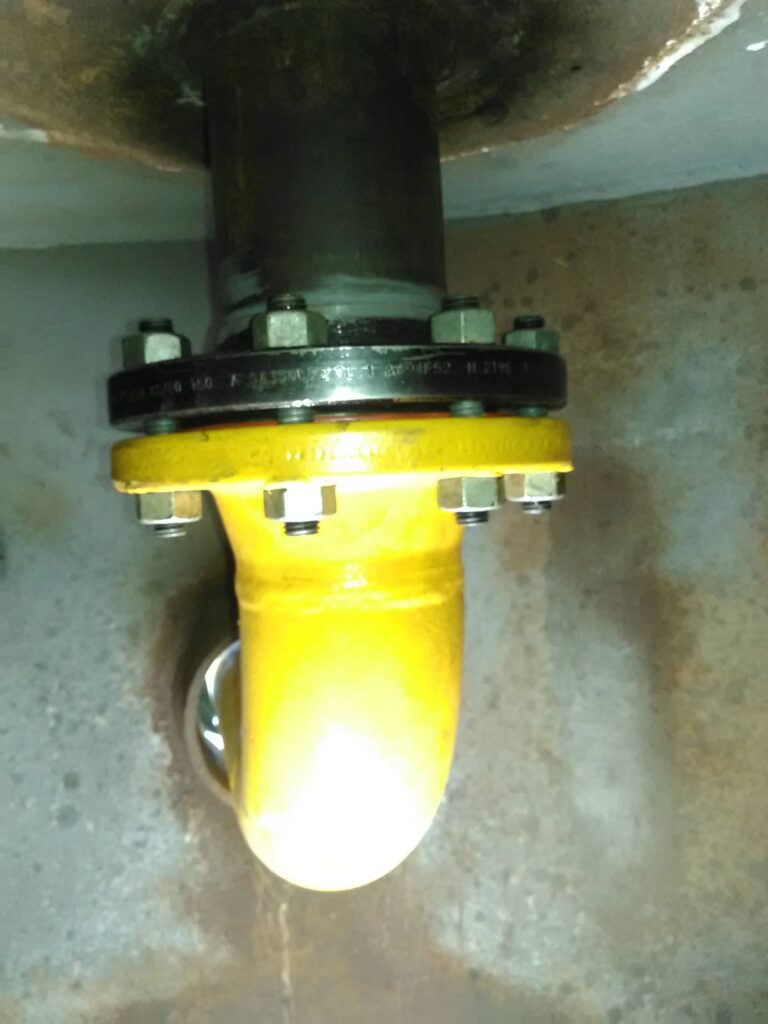
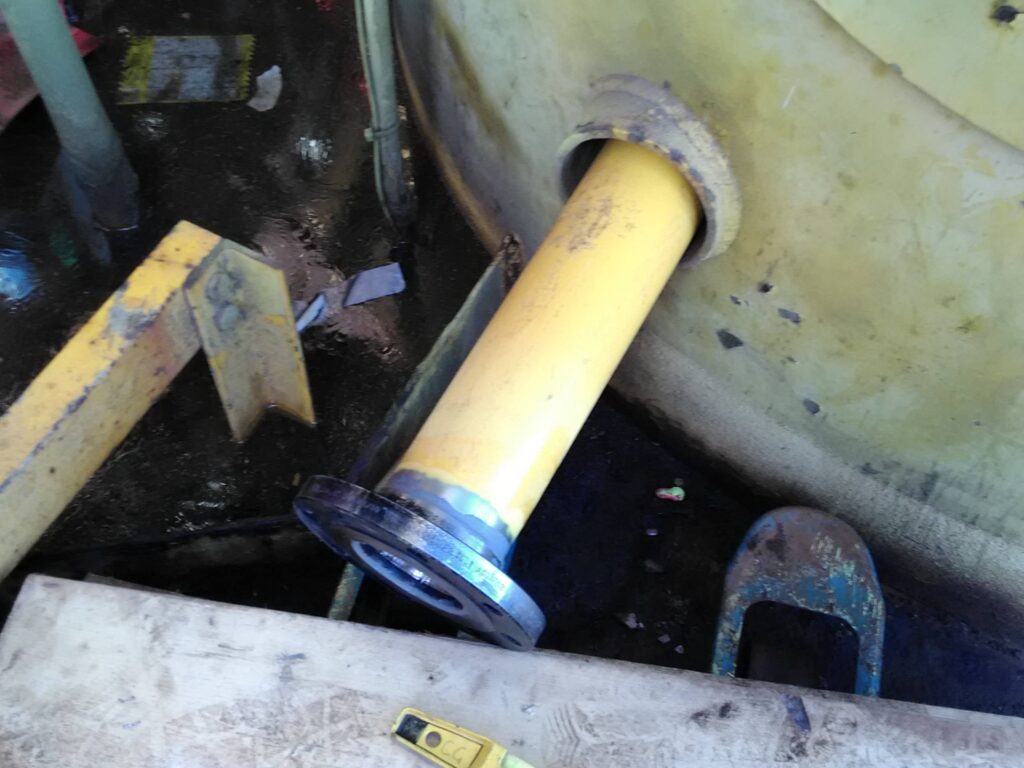
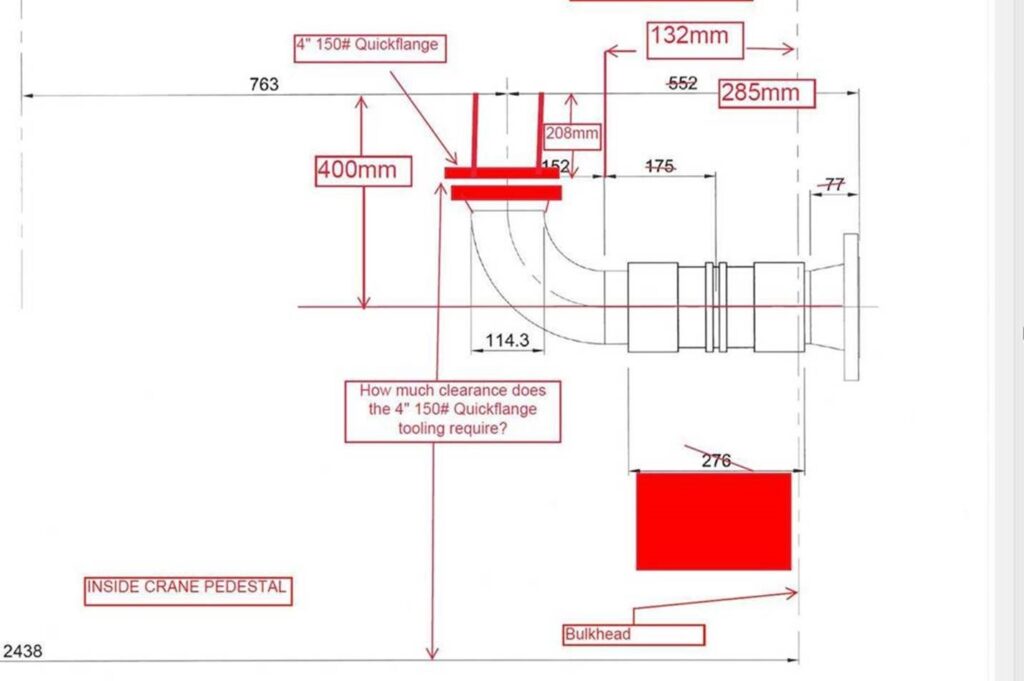
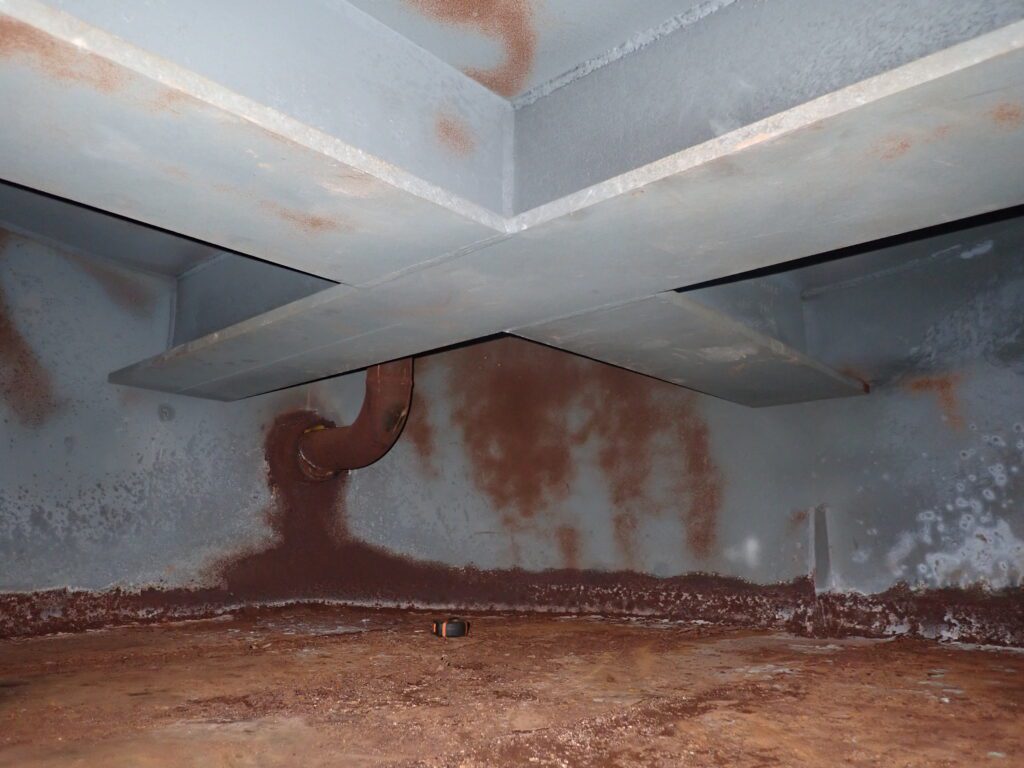
Client | Location |
---|---|
Major North Sea Operator | UKCS |
Scope
A major North Sea Operator was required to complete a dump cooler modification scope with a 10” Cunifer seawater line during a quick turnaround shutdown scope for a Floating Storage and Offloading vessel. Pipe removal and replacement with the use of 10” 5.5mm FF Cunifer flange connections was necessary for replacement of this cooling water repair scope. Quickflange™ was the preferred choice as a cold-work application.
Solution
A Quickflange™ solution was delivered which had undergone leak testing, mechanical testing and burst testing to meet the required criteria for DNV Type Approval Certification. Due to time criticality and personnel limitations on board, two multi-skilled ICR technicians were mobilised to complete this scope on back-to-back day and night shifts. The highly competent technicians held the following certification: Clamshell Cutting, Advanced Quickflange™ Installations, Flange Joint Testing and MJI10 Bolting & Torquing. The technicians completed:
- Prepping the pipe and performing two straight cuts with clamshell cutting equipment
- Installation of 2 x 10” 5.5mm CuNi 90/10 16/20 Quickflange™ Connectors
- Flange strength testing of both connections utilising flange joint testers and ancillaries
- Bolting and torqueing of spools to tie-in the new pipework
During the first of the Quickflange™ installations, the pipe was found to be oval once the cut had been performed with the clamshell cutter. This scenario can occur where the pipe ‘springs’ once the cut has been made due to tension in the pipework. The technicians used tried and tested techniques to bring the pipe to within the required outer diameter tolerances allowing the Quickflange™ to be installed. The technicians also remained to assist the shutdown team with other modification work on the asset ensuring the full scope of work planned for the shutdown was completed on time and to the highest of standards.
Results & Benefits
- Work successfully completed over a 3-day period; technicians on 6 back-to-back shifts cut, installed and tested the Quickflanges™
- Long-term safety of system improved by permanent repair
- Safety, time, production and cost savings compared to conventional welding
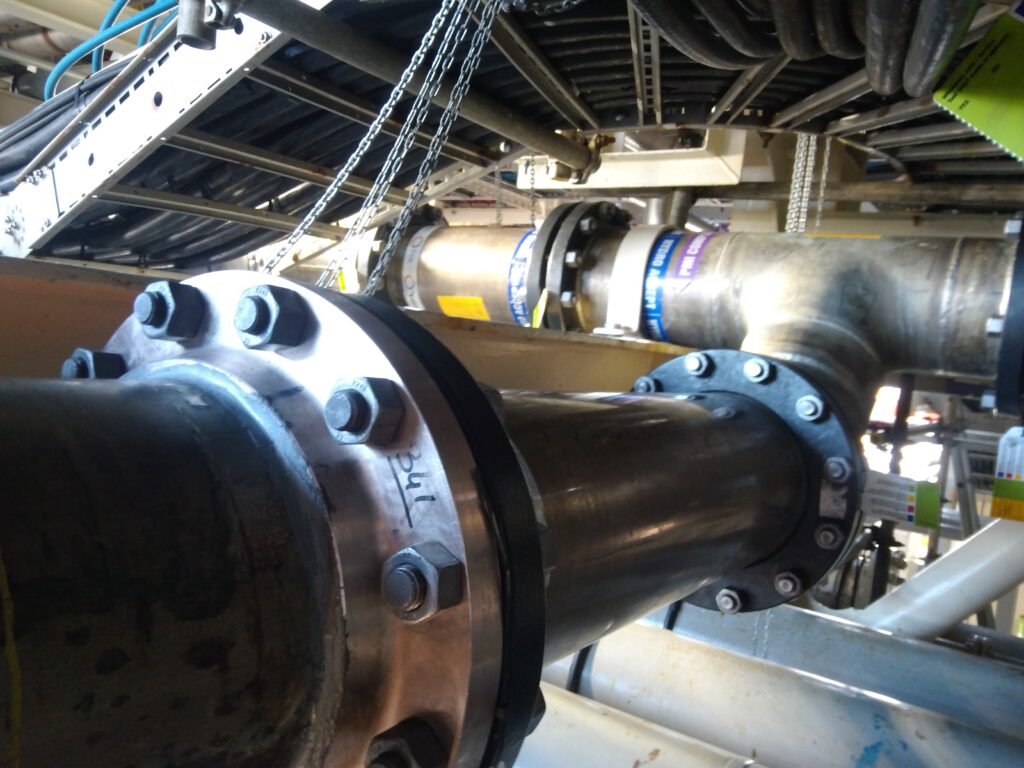
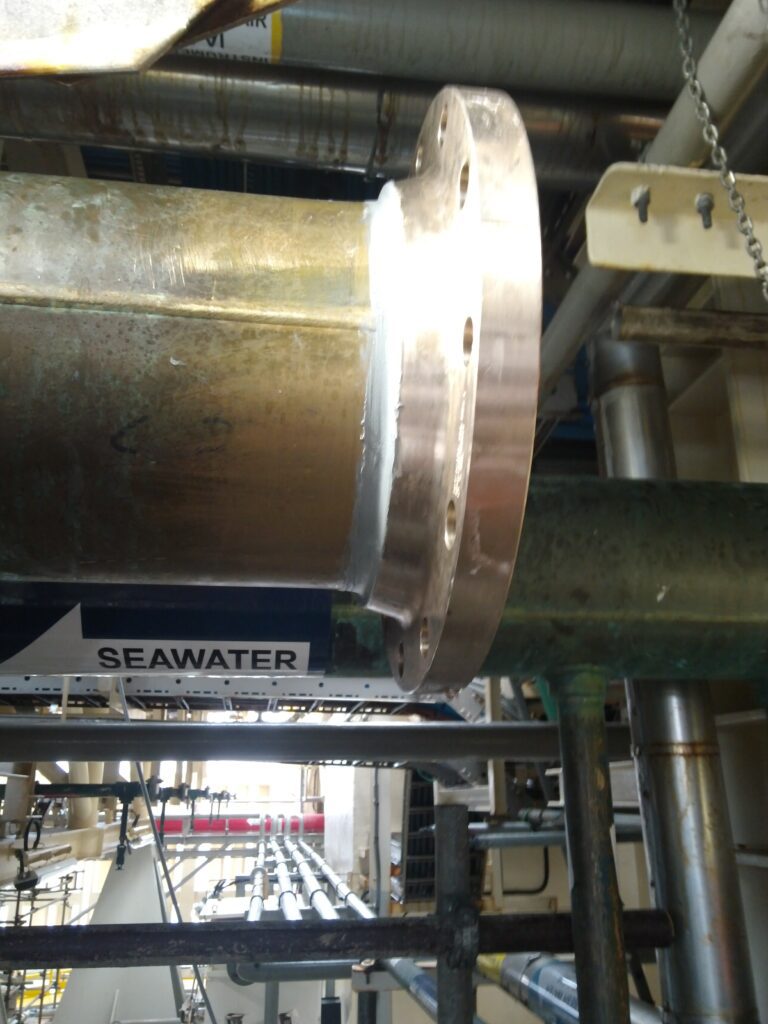
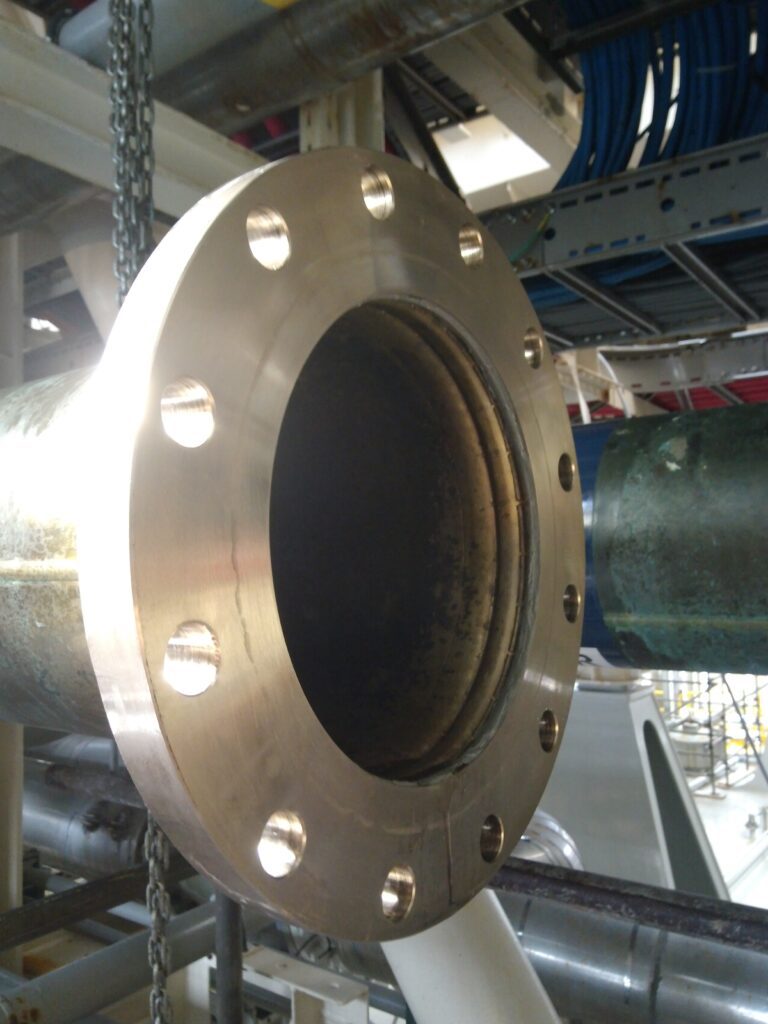
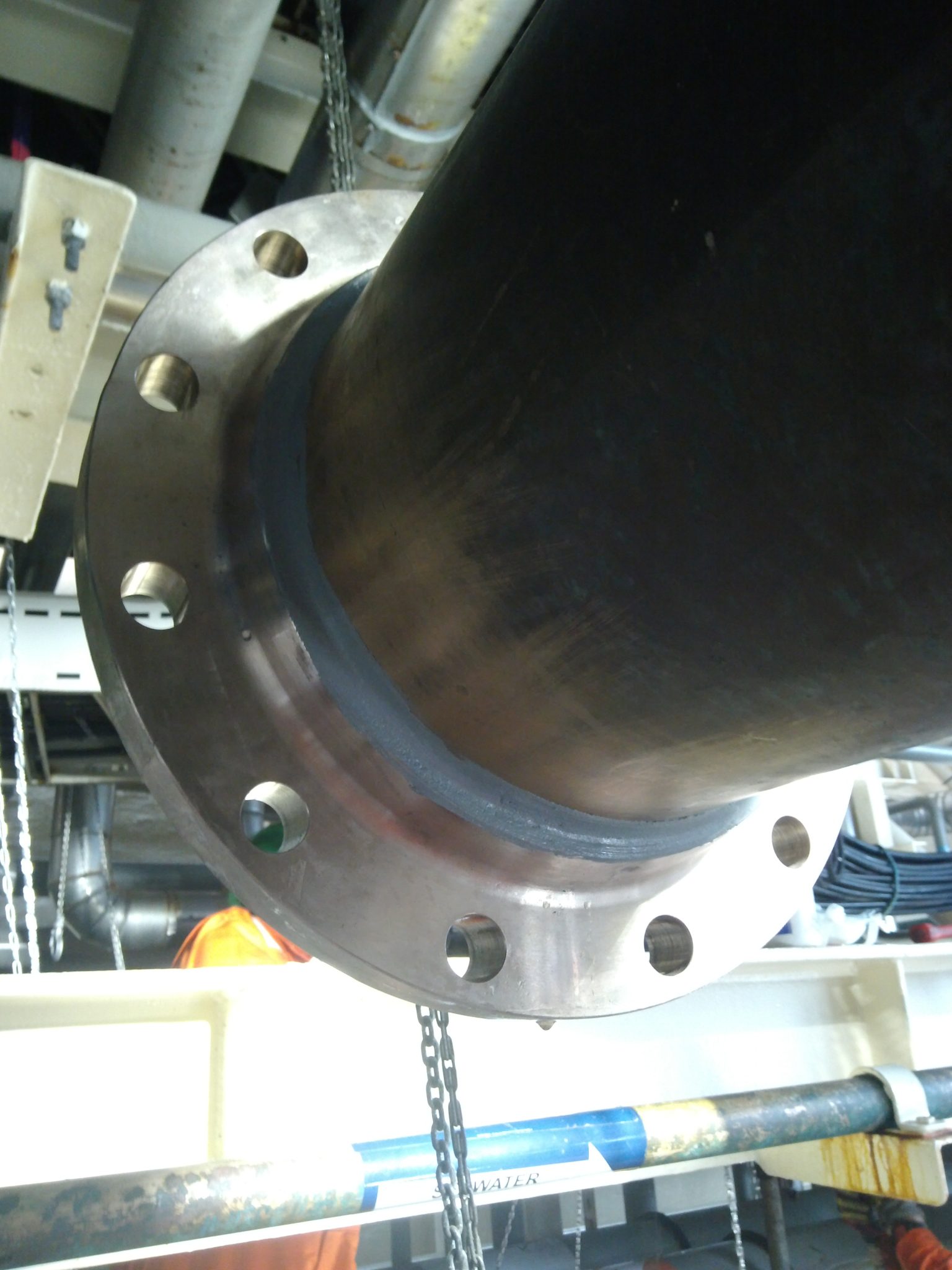