Date: May 2022
Client: Major Operator
Location: North Scotland
Client challenge
Our client, a major energy operator, required two Biocide Chemical Injections Pump packages for their oil and gas terminal, as elevated levels of Sulphate Reducing Bacteria had been discovered. This bacteria caused increased corrosion rates on the main pipeline at the terminal, especially in areas with low points where water tends to accumulate. The integrity of the pipeline system was at risk due to this corrosion, necessitating biocide injection at both the pig receiver and the crude oil manifold.
Solution
Our team designed and built two bespoke chemical injection units complete with:
- Two CRP2250W600CR-BR Williams Milton Roy Air Driven W Series Plunger Chemical Metering Pumps
- One head operating to individual injection point with one complete standby pump.
All equipment supplied was bespoke and reflected the duty parameters and chemical application specified by our client.
The packages included the following bespoke elements:
- Two compartment containers divided by a partition wall and painted in accordance with our client’s coating specification.
- Package containerised with galvanised roller doors provided for operator access and designed to ensure safe and easy changeover of IBCs.
- The IBC was connected by a 300mm section of flexible hose and an adapter to fit the IBC outlet connection.
- Each side of the container was internally outfitted with ex-rated fluorescent lighting fittings, controlled by a manual switch which terminated at the package edge.
- Package bunded with two off 1.25m3 bunded sections separated by a bulkhead wall, with flange drain valves.
- Ventilation grills were located on all three walls of the container to avoid ingress of rainwater.
- Equipped with lifting points rated for twice the weight of a fully outfitted container and holding down foot plates with slings and suitably sized and rated shackles supplied to facilitate the single point lift. The containers conform to DNV 2.7-1 lifting and structural requirements.
- Two off M12 earthing was provided and were located on diagonally opposite, external corners of the package.
- The package included safety signage.
All process tubing including, suction, discharge, and air manifolds as well as the fittings and valves were constructed from 316 stainless steel. Instruments had a permanent tag label fitted. The injection pump package was mounted in a 316 stainless steel box frame complete with all valves, instrumentation and piping for safe and proper operation.
Results & benefits
We successfully delivered the chemical injection packages within the planned schedule and under budget. Each package was specifically designed to reflect our client’s specifications, duty parameters and environmental factors.
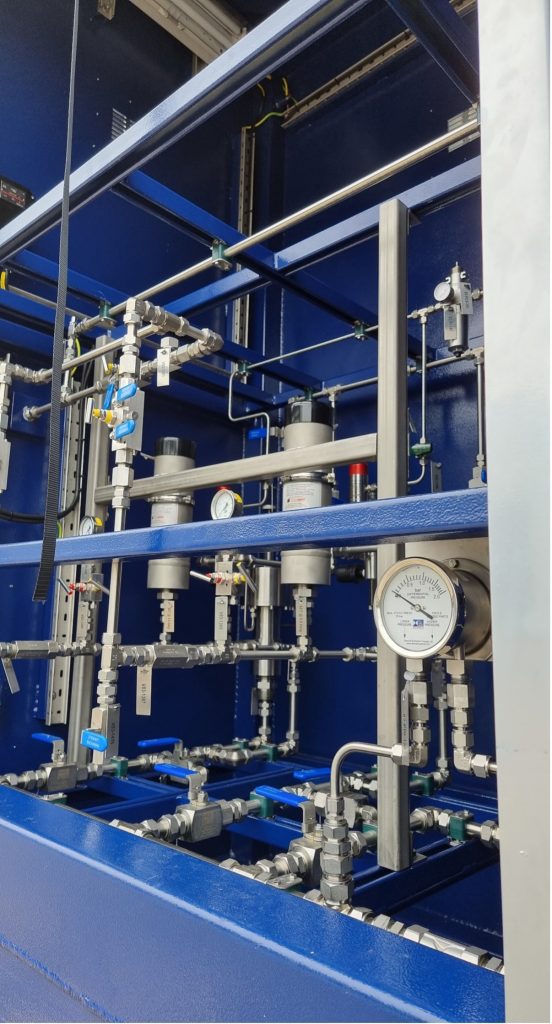
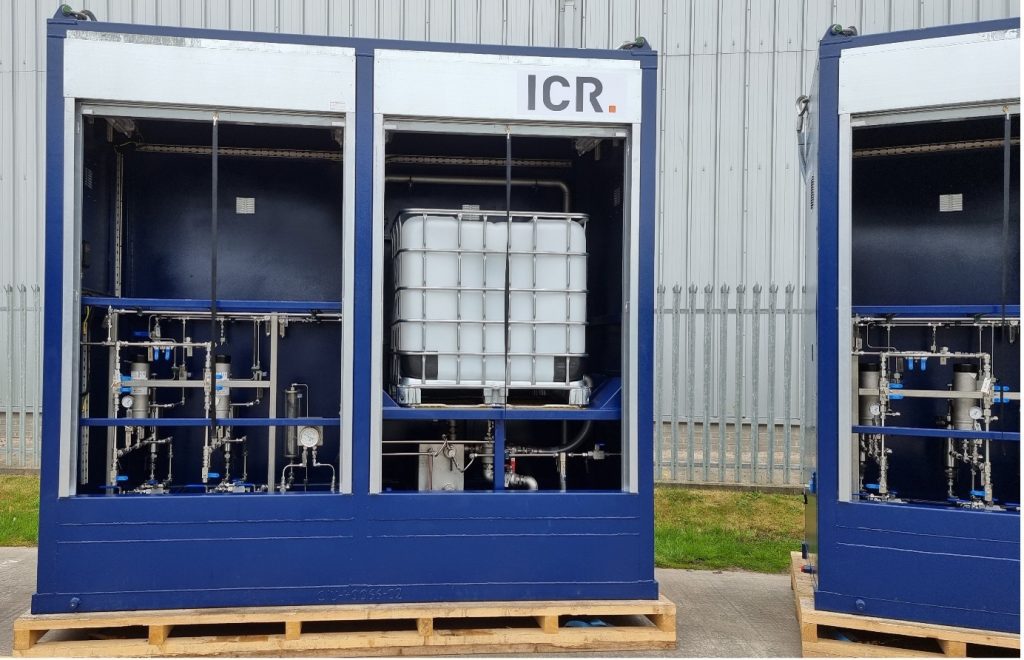
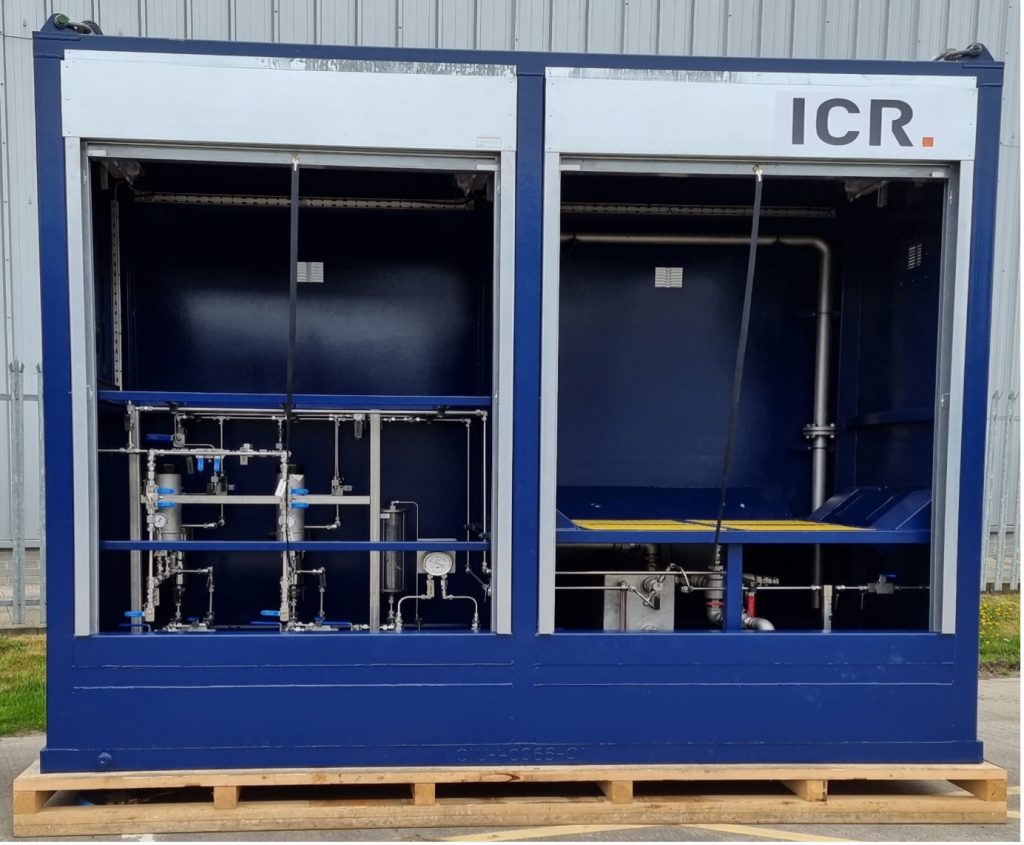
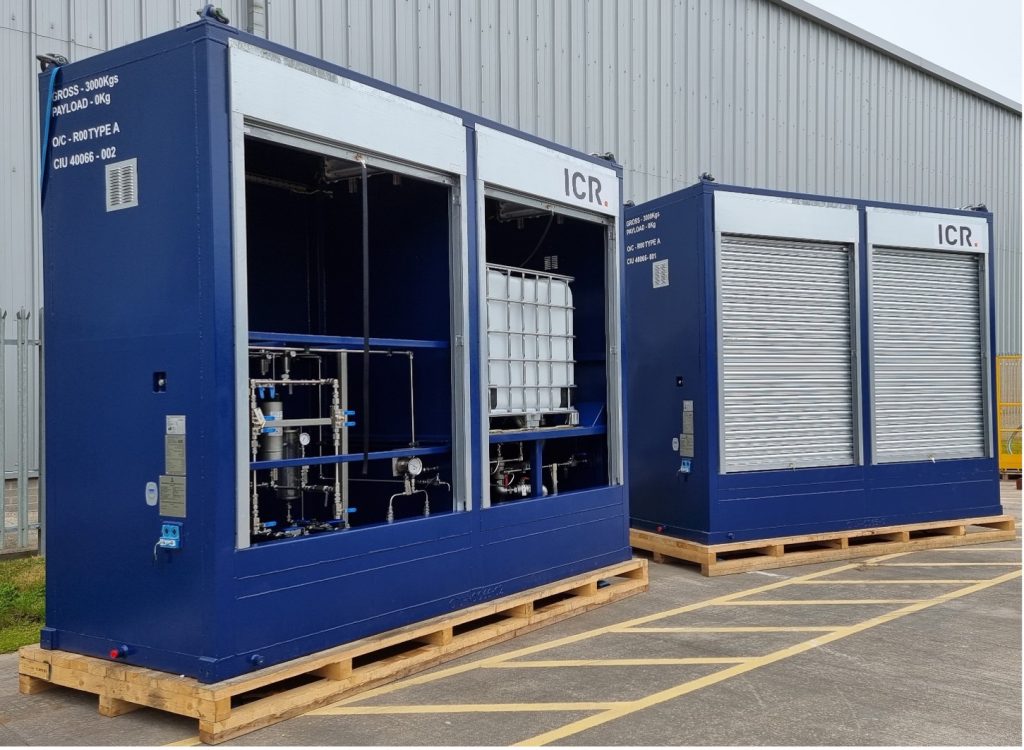
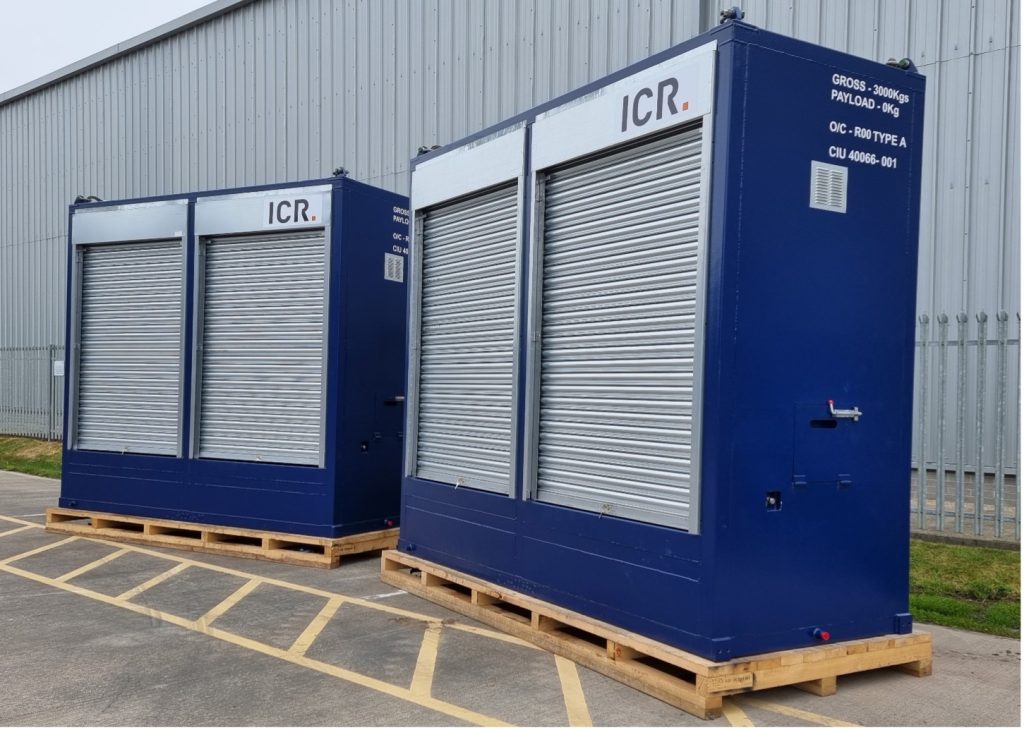
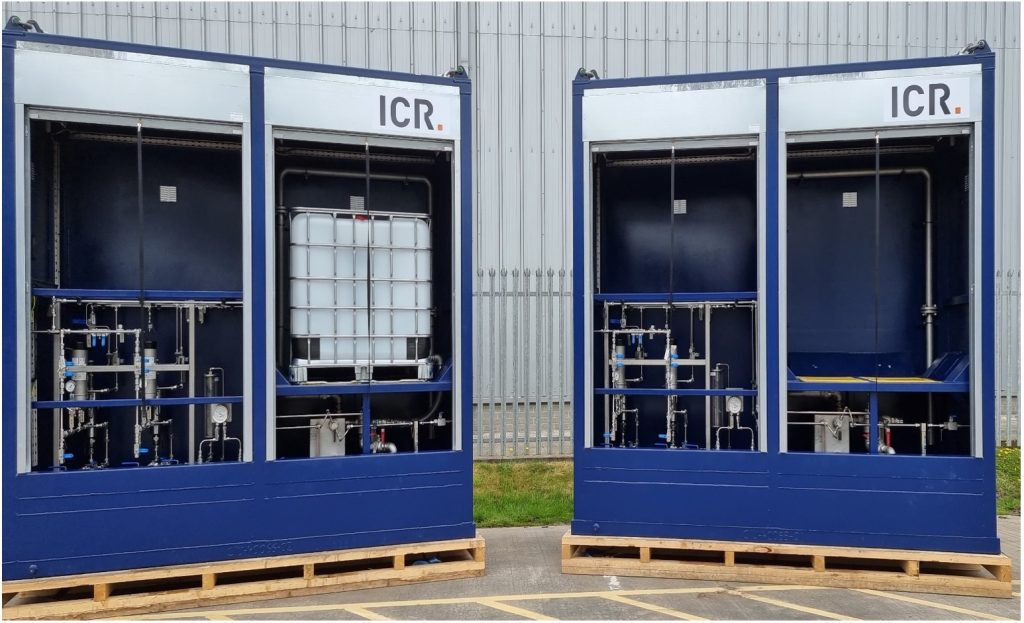
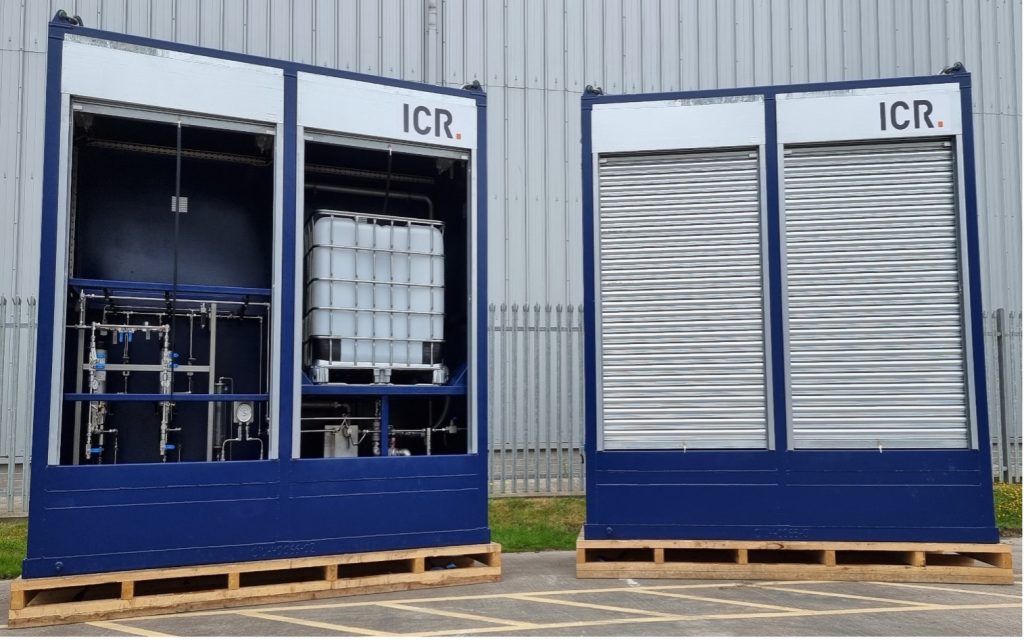
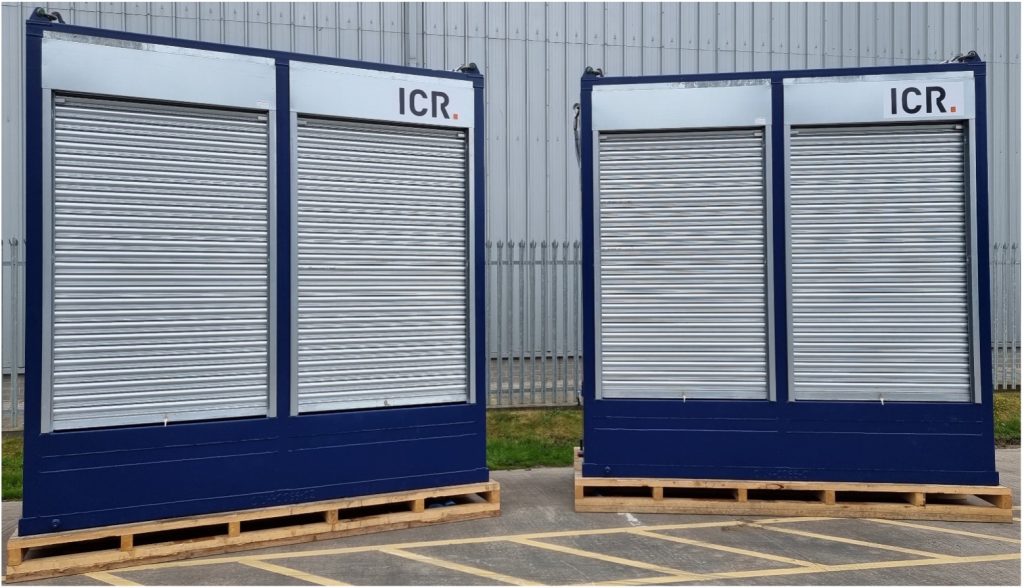
Featured articles
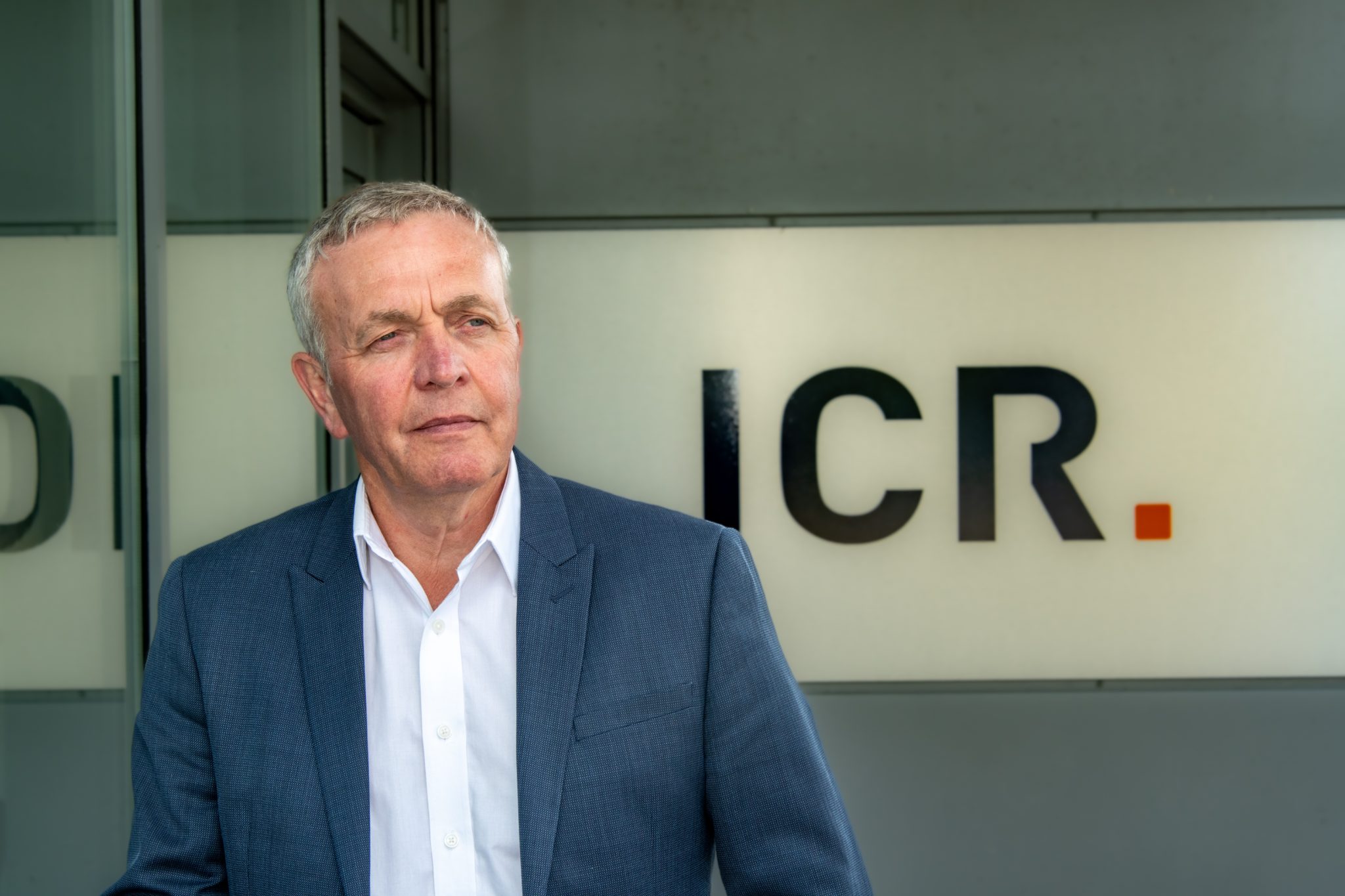
University of life stands Govan-raised engineer in good stead
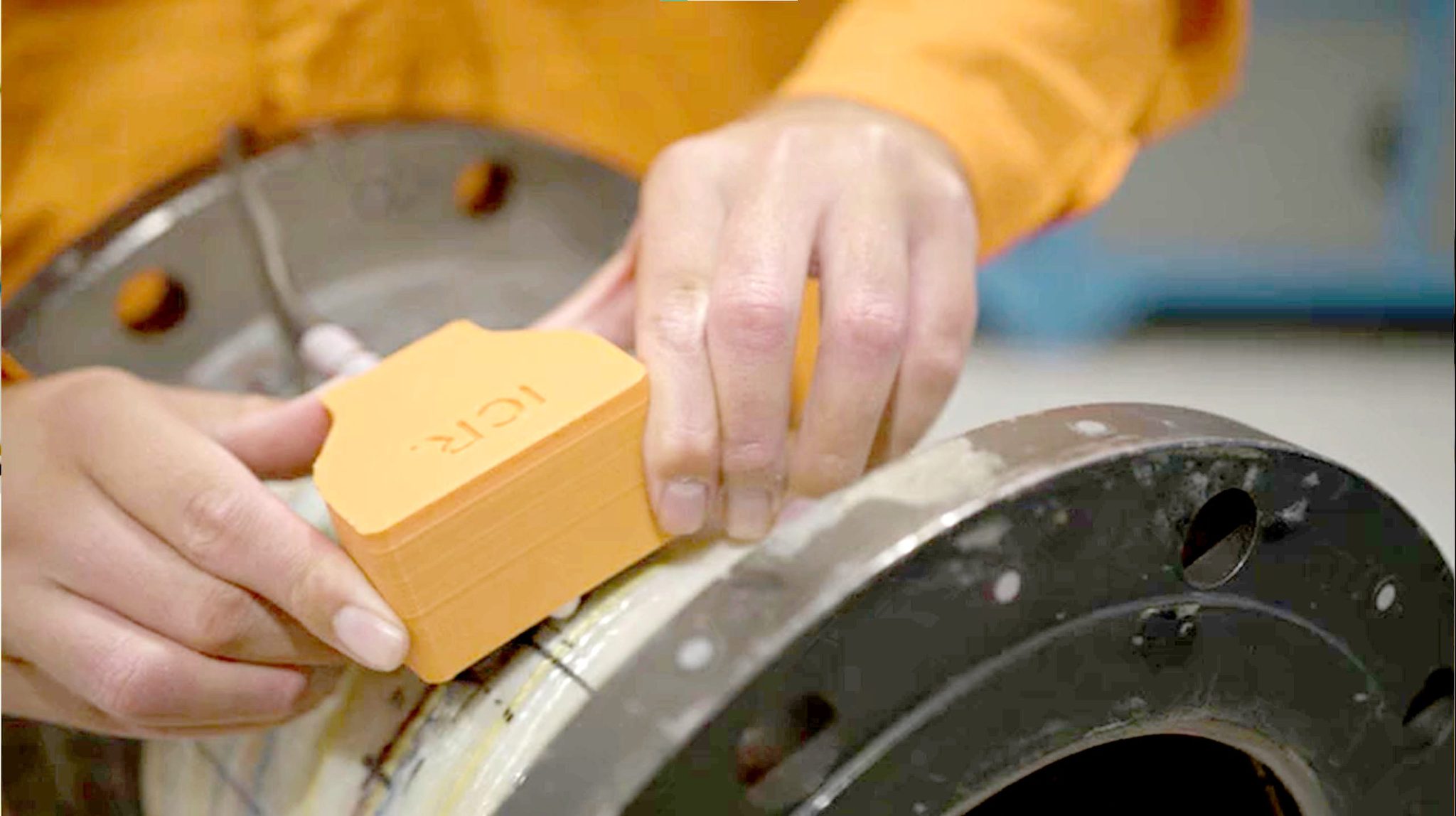
LR and UKAS boost for ICR Group’s INSONO innovation
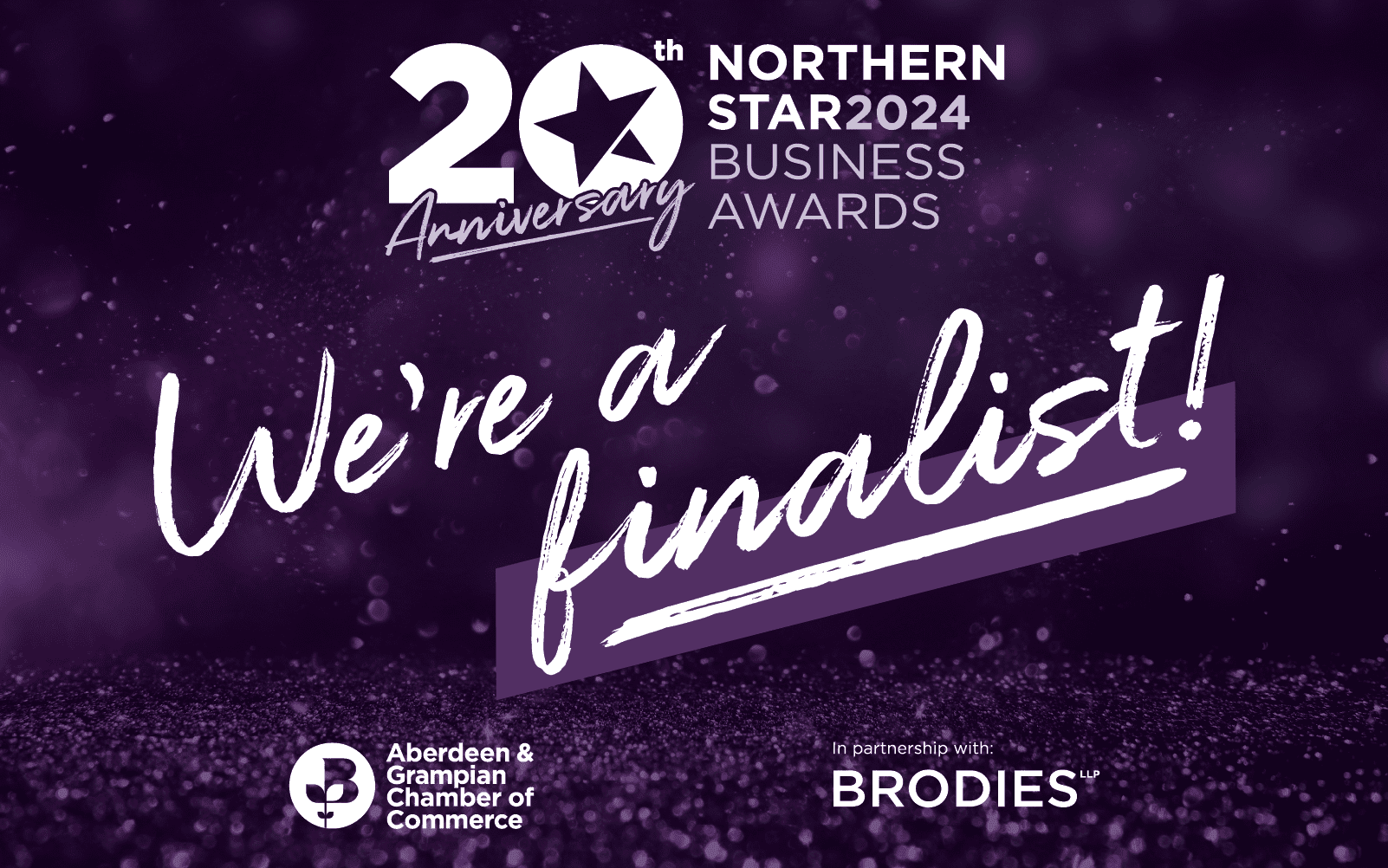