ICR Group has announced a strategic partnership with Wellube, a Unique Group company, to expand the reach of its bespoke technology solutions in the Middle East and India.
This collaboration aims to introduce ICR’s advanced products – including the Technowrap composite repair system, Quickflange weldless connections, and INSONO non-intrusive inspection technology to new markets. Wellube becomes the latest partner as ICR seeks to strengthen its global presence.
Wellube has been providing cutting-edge bespoke services to the oil and gas, renewables, power, petrochemical and infrastructure industries for over 20 years. Renowned for its engineering solutions the team brings a wealth of market presence and industry knowledge to the partnership.
Jim Beveridge, Chief Executive at ICR Group, said, “Welcoming Wellube into the ICR partner network is a significant milestone in our mission to deliver cutting-edge integrity solutions worldwide. Wellube’s strong presence in the Middle Eastern and Indian markets is ideal for the introduction our advanced technologies into new sectors and to new customers.”
Garry Kidd, Managing Director at Wellube, said: “This collaboration unites our long-standing market presence and deep understanding of the industrial landscape with ICR’s innovative solutions. We are committed to delivering unparalleled services, and the use of Technowrap, Quickflange, and INSONO will enhance our provision of turnkey solutions for our clients from start to finish.”
The partnership highlights both companies’ commitment to enhancing asset maintenance solutions. By combining Wellube’s client base with ICR’s innovative and bespoke product range, the collaboration promises to deliver a comprehensive suite of services.
ICR’s dedication to innovation is demonstrated though one of the core products, Technowrap – an engineered composite repair system. It’s a versatile long-term alternative to steel replacement that offers practical, cost-effective rehabilitation and minimal disruption to operations. Technowrap has been utilised extensively by major operators in the Middle East for applications ranging from pipework and pipelines to structures as well as significant subsea composite repair projects. The defined life repair technology for damaged pipework can be engineered to last up to 20 years providing both immediate and long-term benefits.
Further to this, INSONO, a non-intrusive composite inspection technique complements the Technowrap range. It has been developed to validate the condition and integrity of composite repairs providing operators with assurance in the application and long-term performance. The technology can detect anomalies in the bond line and interlaminar dis-bonds within composite repair material and, thereby, support and underpin asset written schemes of examination.
Quickflange, a high-performance weldless flange-to-pipe connector, is another core offering that addresses scenarios where traditional welding solutions are impractical due hot work constraints or time limitations. The innovation enhances operational safety and efficiency. Over the past 20 years, Quickflange has built up a global track record of providing rapid and safe installations generating cost efficiencies and an 80% time saving over traditional welding methods. ICR had a global network of more than 25 partners.
The USA is a thriving market for ICR Group . In recent months we’ve doubled the size of our American business, and we have stregthened our team to help us capitalise on new opportunities in diverse market sectors.
As a provider of specialist maintenance, integrity, and inspection solutions, we have a range unique products that provide significant benefits customers in industries ranging from oil & gas oil & gas and renewables to defence, nuclear and telecoms.
Stemming from our focus on technological innovation – and founded on the principles of safety, reliability, and efficiency – our products serve to protect and maintain assets and critical infrastructure for customers around the world. One of the products that is gaining significant traction in the USA is Technowrap.
Technowrap™ is a versatile “Structural, Pipework and Pipeline repair and rehabilitation technology that offers a long-term alternative to steel replacement that requires minimal disruption to operations. Applied to live targeted areas, with no requirement for shutdown, Technowrap supports safe operations whilst delivering tangible cost savings and environmental benefits.
One of the key benefits of the technology is it’s versatility. Our bespoke engineered repair systems use either glass or carbon fibre stitched cloths, combined with two-part epoxy resins Technowrap is suitable for use on pipework and piping components, valves, and flanges as well as repairs in the Splashzone as well as structural components; including decks, roofs, beams, caissons and risers, blast walls, tanks and vessels.
Technowrap™ is internationally recognised and all engineering is bespoke and completed in-house, in accordance with the latest issues of ISO 24817 and ASME PCC-2, offering a repair life of up to 20 years dependant on design conditions.
Some of the key
- With Technowrap’s increasing popularity among US customers, there are numerous examples that attest to this, foir example;.We provided an engineered composite repair on a large methanol drip pan on an offshore platform in the Gulf of Mexico – with a 10-year design life –
- Technowrap was used repairto reinstate the integrity of two pressure vessels for a major operator in the Texas Eagle Ford Basin. This solution has a 20-year design life as well as long-term corrosion protection.
- We partnered with a local specialist provider to refurbish a corrosion-hit main deck on a platform offshore Trinidad & Tobago. The work, for a global operator, constituted a cold-work solution as the platform was online.
- Technowrap was used to reinstated a production chemical injection skip pan on an asset in the Gulf of Mexico, for a global major operator. Again, this was engineered with a 10-year design life
- Several areas of a logging support deck plate on a global supermajor’s platform in the Gulf of Mexico were repaired using a Technowrap application.
Each of these projects posed unique challenges, yet they all shared a common priority: implementing a robust repair solution that would restore confidence in our customers regarding the integrity of their infrastructure.We’re continuing to grow our reputation in the States – and indeed internationally – as a specialist partner looking to identify and safely deliver the optimum solution.
I’m proud of what we’ve achieved in the US to date, but we’re only getting started. We plan to grow our profile, grow our business, and grow our track record of front-line success.
Houston-based Phil Paterson is ICR Group’s Business Development Director. ICR Group specializes in asset integrity, maintenance and inspection across various sectors, with a strong presence in the US and the Gulf of Mexico.
Phil Paterson
Business Development Director
Client Challenge
Structural components (including I-beams, CHS sections, roofs, panels, members, struts) can suffer both corrosion resulting in material loss. This material loss can be severe such that the component is no longer fit for service.
What We Did
The design challenge for a structural component repair is to ensure sufficient strength or stiffness within the composite repair to withstand the applied loads, either in-plane or bending and also whether those loads are tensile or compressive. A design methodology for the repair of structural components has been developed by ICR TechnowrapTM (based on ISO 24817) that ensures both repair strength and stiffness. It is possible to design the repair either with or without allowance for the remaining strength or stiffness of the structural component.
Application
The installation of a composite repair on a structural component is comparable to in procedure to that of pipework. The main difference is the mean of compression used during curing of the repair.
Results
The repairs have either been designed to withstand the applied loads or return the component back to its original strength with a warranted design lifetime from between 5 and 20 years.
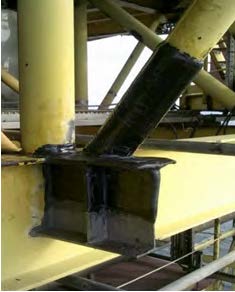
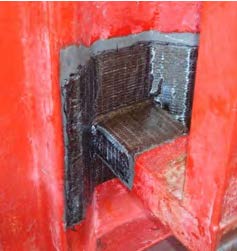
OGV Energy magazine put the spotlight on Technowrap™ – a remarkable ICR product used worldwide by clients.
ICR Group continues to redefine asset integrity with its revolutionary Technowrap™ product.
This repair solution is specifically designed to significantly enhance operational efficiency and sustainability, while minimising downtime and environmental impacts.
By harnessing the strength of glass or carbon fibre stitched cloths paired with two-part epoxy resins, Technowrap™ rehabilitates damaged pipework, pipelines and structural components across various scenarios.
ICR’s comprehensive in-house approach encompasses engineering, material provision, technician training and installation, ensuring quality and reliability.
The versatility of Technowrap™ is evident in its broad range of applications, from pressurised systems and pipelines to structural repairs of tanks, vessels, caissons, risers and even underwater environments. It offers a cost-effective alternative to steel replacement, enabling repairs to be conducted without the need for operational shutdowns.
Repairs can last for up to 20 years. Moreover, Technowrap™ can contribute to environmental sustainability by offering a 66% reduction in carbon emissions compared to traditional replacement methods.
Ewan Robertson, Global Composite Repair Director at ICR, said: “Technowrap™ is the ideal product for assets to keep in their toolbox to cover a myriad of maintenance and repair applications for pipework and infrastructure. This technique has now had a 30-year track record in the industry and can provide further advantages from a sustainability and efficiency perspective.”
The ICR portfolio also boasts INSONO™, an innovative non-destructive testing (NDT) technique for inspecting engineered composite repairs.
Furthermore, ICR’s online leak sealing solutions provide tailored, in-house engineered clamps and repairs designed to tackle specific leaks in operational systems.
Quickflange™ offers another remarkable solution within ICR’s arsenal, delivering weldless, high-performance flange-to-pipe connections that improve pipeline integrity and flow assurance. This is a permanent, efficient repair option, yielding up to 80% time savings and a 57% reduction in greenhouse gas emissions compared to traditional welding methods.
ICR’s machining and bolting capability brings extensive experience to a wide range of industrial sectors. Meanwhile, the firm’s drone division, Sky-Futures, delivers inspection reports and supported an operator by measuring methane emissions at four platforms in the North Sea.
This article first appeared in OGV Energy magazine’s asset integrity issue.
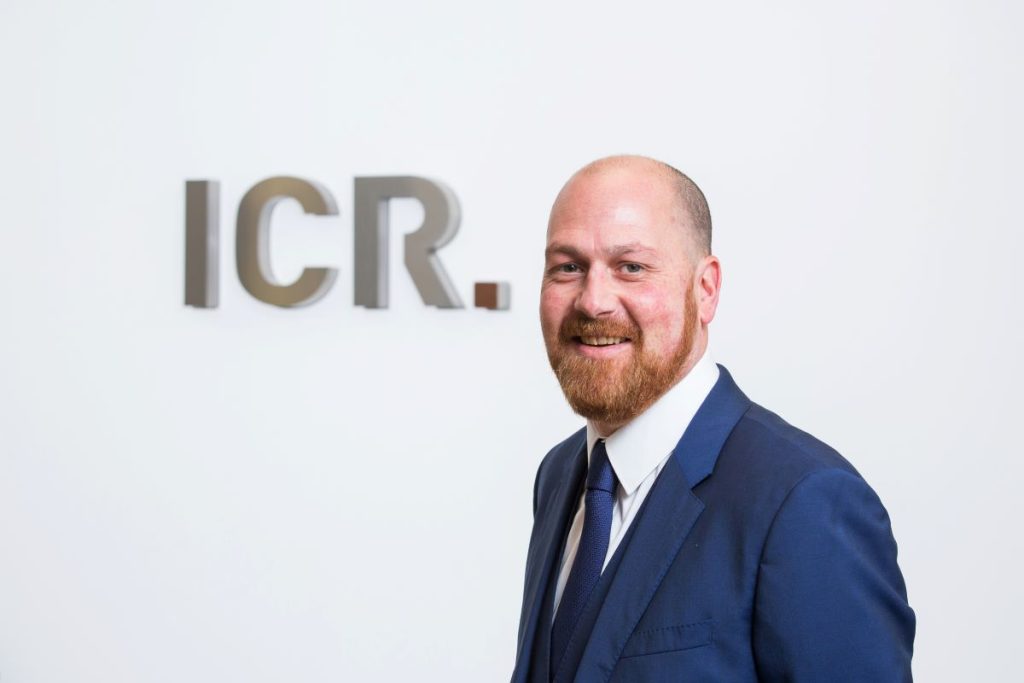
ICR Group has secured another partnership agreement in Africa.
The collaboration with South Africa-based SGB-Cape, a leading industrial services provider, broadens the scope of ICR’s innovative products, including the Technowrap™ composite repair system and Quickflange™ weldless connections.
Scott Byers, Head of Business Development, Africa, at ICR, said: “Welcoming SGB-Cape into the ICR partner network marks another significant step in our mission to deliver cutting-edge integrity solutions worldwide. Their strong presence across the African market is ideal for the rapid introduction of our advanced technologies into new sectors, locations and customers. We are delighted to extend our reach by adding to our African partner network.”
Ben Garrad, Managing Director of SGB-Cape, said: “The collaboration is a perfect synergy, uniting SGB-Cape’s longstanding market presence and profound understanding of the African industrial landscape with ICR’s innovative solutions and international insights. SGB-Cape will serve as a key partner of ICR, solidifying its commitment to delivering unparalleled industrial services solutions.”
The alliance is a testament to both companies’ commitment to enhancing asset integrity management, corrosion protection and inspection services in Africa. It combines SGB-Cape’s 75 years of industry experience with ICR’s innovative solutions, promising to deliver a comprehensive suite of services to meet the unique challenges of the African market.
SGB-Cape, a leading provider of industrial services across Africa, specialises in asset integrity, corrosion protection and inspection solutions.
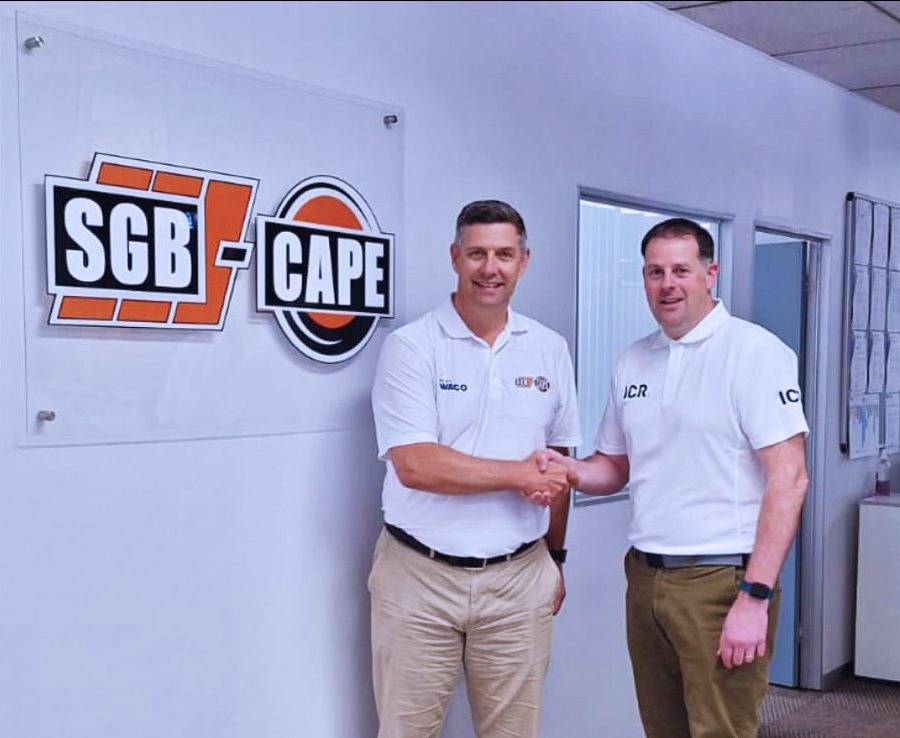
Today we put the spotlight on our North-west of England technical base
ICR’s Carnforth operation is on course to increase its contribution to the overall turnover figure of the company this year.
The hub is the group’s base for on-site machining, hydraulic bolt tensioning, leak sealing, Quickflange and Technowrap.
ICR has invested in new equipment and training at Carnforth, where additional technical and sales staff have been added. The team at the base has risen from 42 to 60 in the past year.
Carnforth’s status within ICR has been further underpinned after the group secured a four-year extension to a major contract for specialist onsite machining projects at a large engineering facility in the North-west. Work has also been secured in the energy, nuclear, government and defence sectors, across projects including flange management, controlled bolting, machining, leak sealing and composite repairs.
Darryl Dixon, General Manager of ICR at Carnforth, said: “We have a clear vision of our mission, which in turn cascades outwards so our customers know what it is ICR stands for and what we will deliver: right first time, innovation, safety and reliability.
“Our ongoing success reflects a genuine team effort at our Carnforth base, alongside collaboration with wider ICR operations and the support of senior management. We’ve invested significantly in facilities, equipment and people to ensure that knowledge and training from our existing technicians is shared across our wider pool of new talent.
“We already have exceptional subject matter experts, from design engineers to product-specific technical authorities, and our on-site technicians do great work every day in delivering our products and services on behalf of clients. Our goal now is to capitalise on all those resources, capabilities, and experience to realise further growth – not least in new markets such as renewables.”
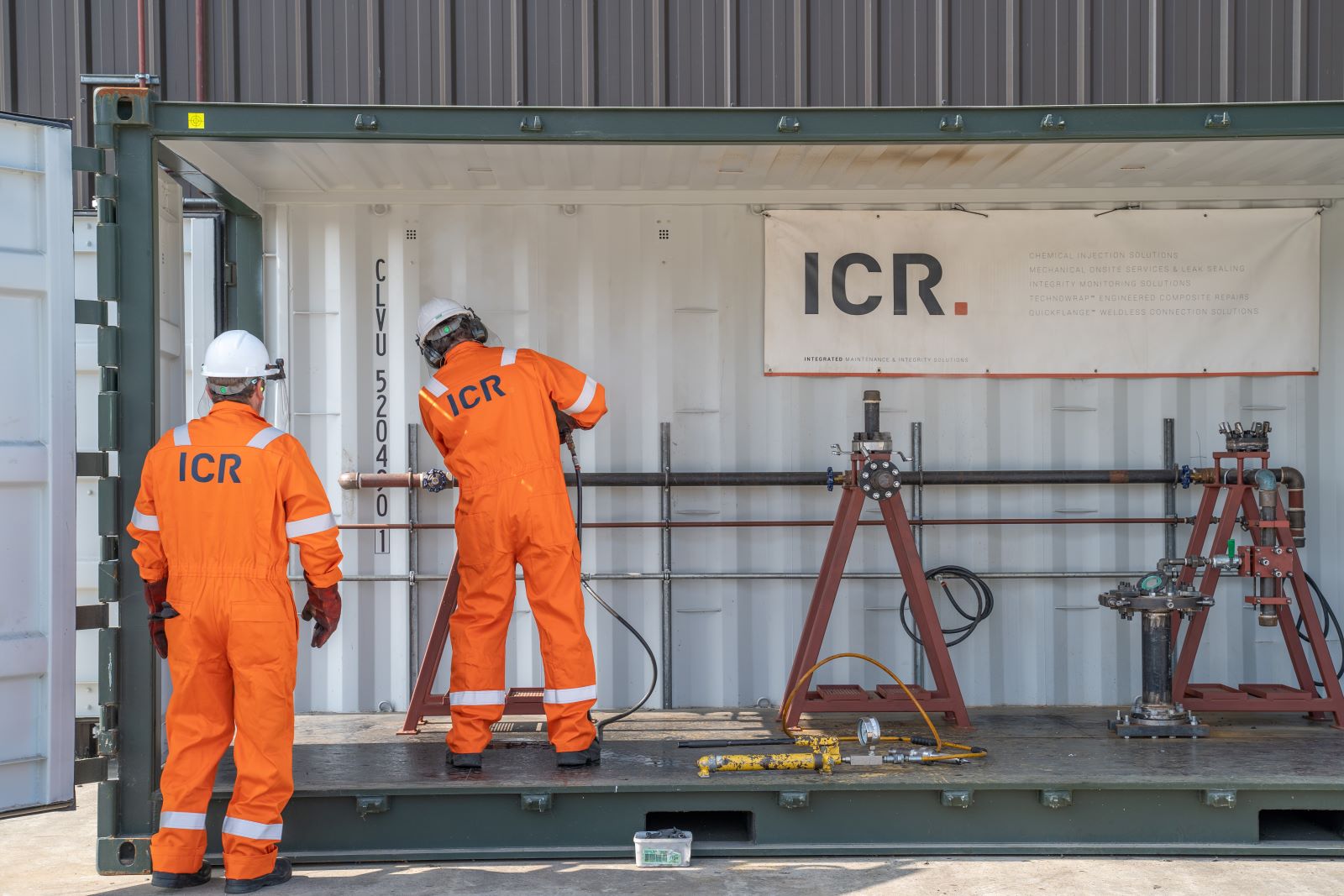
This article appeared in the Herald Newspaper on Monday 29 January 2024
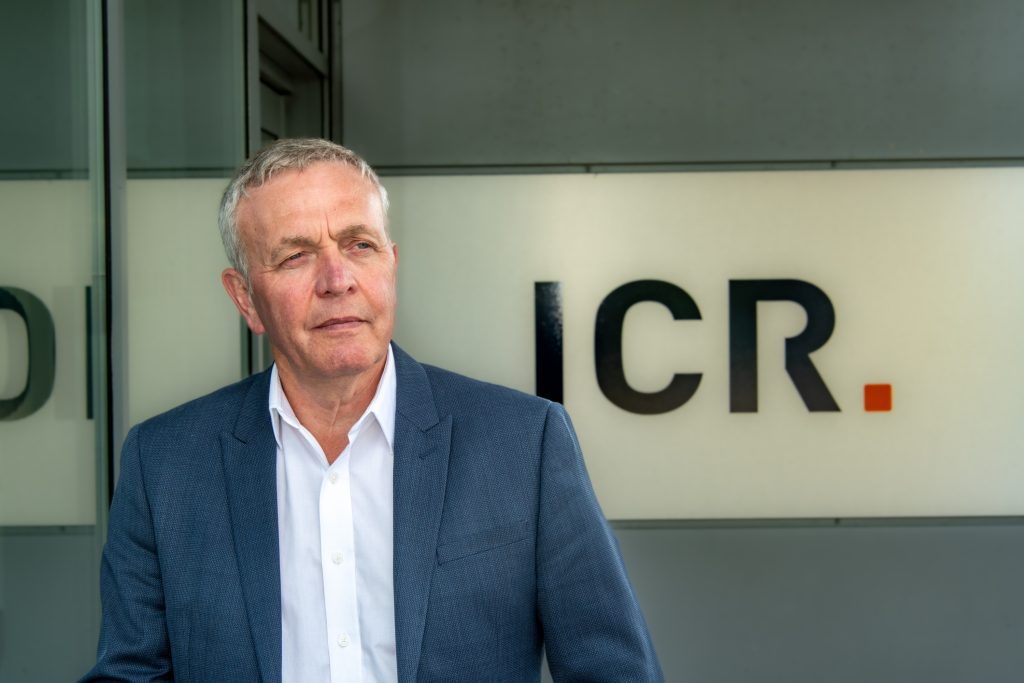
Glasgow-born Jim Beveridge is the chief executive officer at ICR Group.
With its headquarters in Aberdeen, ICR is a global technology-focused provider of specialist maintenance, inspection and integrity solutions across multiple industrial sectors. The firm recorded a 20% rise in turnover for its latest financial year and it expects to exceed that figure this year.
ICR supports clients with their asset integrity challenges, reducing time and costs. It also has a ‘drones’ division, Sky-Futures, a worldwide leader in unmanned aircraft and remote sensing operations. This part of the business plays a key role in addressing issues related to emissions.
Demonstrating a robust commitment to sustainability, ICR employs pioneering techniques that significantly contribute to the net zero goals of its clients.
What is your business called?
ICR Group.
Where is it based?
Aberdeen, Carnforth, Hemel Hempstead, Stavanger (Norway), Houston (USA), Abu Dhabi (Middle East), Perth (Australia). ICR has partnership agreements in 25 countries, where we train the local workforce to deliver engineering projects. This helps to reduce the carbon footprint.
What does it produce/do?
ICR specialises in cutting-edge maintenance, inspection and integrity solutions. We are playing our part in the transition to a lower carbon future across multiple industries and international markets.
For example, Technowrap provides life-long repairs that can be applied to internal, external and through-wall defects on complex geometries, while INSONO is an unique NDT (non-destructive testing) technique for the inspection of engineered composite repairs. The Technowrap repair system reduces emissions by 66% compared to the traditional replacement methods.
To whom does it sell?
Clients from a broad range of sectors count on ICR to support engineering projects. These include oil & gas, renewables, defence, nuclear, telecommunications, process industries, utilities and infrastructure and other markets.
What is its turnover?
Turnover for our 2022-23 year-end was £41.7m – a 20% increase on the previous financial year. The aim is to hit £50m in 2024 and I’m confident we will achieve this.
How many employees?
268. We’re looking to add to the team.
Why did you take the plunge?
The chance to create long-term sustainable jobs and to continue to grow a business across an international footprint was an extremely attractive proposition. The CEO role at ICR was an opportunity to put my own stamp on things, and lead from the front. I was previously with a global engineering and consulting business with more than 35,000 employees.
What were you doing before?
Senior vice-president, Asia Pacific Central at Wood plc. I enjoyed my 19 years with them. I joined ICR as CEO in April, 2022. It’s been an interesting career journey since growing up in Govan.
What do you least enjoy?
Jet lag. The novelty of long-distance travel wore off a long time ago!
What are your ambitions for the firm?
It’s vital we continue to be a sustainable business. We are diversifying into new sectors and continually looking at new opportunities. The aim is to create long-term jobs and significantly grow revenue and profitability year-on-year. As well as organic growth, we are also looking to expand through acquisitions.
What single thing would most help?
Continued product development is key. We must always be a forward-thinking company – one able to move with the times and not be reliant on one region, product or industrial sector. For example, we are working with Robert Gordon University on a number of innovative solutions.
What is the most valuable lesson you have learned?
You can’t stand still in business, you need to keep looking to improve. As Albert Einstein said: “Insanity is doing the same thing over and over again and expecting different results.’”
You’ve got to change it up. Also, I’m very appreciative of the people I worked beside when I started my apprenticeship on the Clyde with marine and mechanical engineering firm Hutsons.
Many of my colleagues were working class and extremely intelligent. They came from a generation where university wasn’t really an option. I’m always grateful for their time and advice. It was my university of life experience; one which led to me eventually going on to gain a degree in aeronautical engineering from the University of Glasgow.
Where do you find yourself most at ease?
On the golf course or watching football with lifelong friends.
If you weren’t in your current role, what job would you most fancy?
I used to think being a chef would be good, but it looks like it would take a huge amount of effort to really do it to a high standard.
What phrase or quotation has inspired you the most?
“Everyone I pass on the way up I’m going to meet again on the way back down.” Treat everyone the way you would want to be treated yourself.
What is the best book you have ever read? Why is it the best?
Who moved my Cheese? It’s a business book by Dr Spencer Johnson. It’s a simple, short story that illustrates how people must embrace change and should adapt to new situations with an open mind and a motivated spirit.
What has been your most challenging moment in life or business?
In my previous role we had more than 1,000 workers that couldn’t leave a number of offshore installations in South East Asia due to a major Covid outbreak. There was a great deal of responsibility on myself and my colleagues to ensure we looked after the well-being of the team. The way everyone pulled together was a sight to behold and all worked out well in the end, but it was a huge logistical challenge. The health and safety of your team should always be your priority.
What do you now know that you wish you had known when starting out in your career?
Embracing failure as a learning opportunity; it’s an essential part of growth and innovation.
This article can be found online here – https://www.heraldscotland.com/news/24078257.university-life-stands-govan-raised-engineer-good-stead/
IC Integrity Pty Limited, a key ICR Group partner, has landed a significant contract with an operator in Australia.
The agreement sees IC Integrity deploy its Technowrap™ technology for planned maintenance campaigns on several facilities.
Perth-based IC Integrity is a technology-focused provider of specialist maintenance inspection and integrity solutions across multiple sectors.
This latest contract builds on a long history of collaboration with the client.
Russell Collins, Regional Director (APAC) at IC Integrity, said: “This is a substantial project that truly reflects both the successful relationship we’ve developed with the client and our team’s commitment to engineering and technical excellence. We were selected and trusted to work on this project following a competitive tender process.
“This is an important project for us, and this contract with a key industry player again involves the use of our Technowrap™ composite solution, which has become an increasingly common feature of planned maintenance campaigns – not least because of its low carbon footprint.”
Chris Otterbeck, Service Delivery Manager at IC Integrity, said: “We have completed more than 100 applications of the Technowrap™ composite solution for this client and the latest award reflects well on our dependable technology, technical capability and extensive track record.”
As the world moves towards a lower carbon emission future, the firm’s Technowrap™ and Quickflange™ products continue to offer significant benefits in the context of the climate change agenda.
Technowrap™ provides life-long repairs that can be applied to internal, external and through-wall defects on complex geometries. It reduces emissions by 66% compared to the traditional replacement methods.
Quickflange™ offers cold work solutions with weldless, high-performance flange-to-pipe connections. It is a cost-effective and efficient solution generating up to 80% time saving and a 57% reduction in greenhouse gas emissions over traditional welding.
In addition, INSONO™ is an innovative NDT (non-destructive testing) technique for the inspection of engineered composite repairs. It can validate the condition and integrity of composite repairs, giving operators long-term performance assurance.
ICR Group has partners in 25 countries and offices in the UK, Norway, USA and the Middle East. IC Integrity is a joint venture between ICR Group and IAS (UGL).
For further information, go to https://icrias-jv.com.au/
ICR Group is set to highlight its innovative technologies by contributing to a broader conversation on decarbonisation strategies at Offshore Europe.
Ross McHardy, Group Director at ICR, will be hosting a session entitled ‘Small Steps for a Bigger Change: Decarbonisation Through Technology’. The event on Tuesday, September 5 (10am-11.15am) at Aberdeen’s P&J Live will also feature other industry leaders.
This seminar is part of the Collaboration Zone, an initiative organised by the Energy Industries Council (EIC). Running throughout the week, the programme offers an avenue for speakers and attendees to exchange knowledge, explore smarter operational methods and present valuable insights gained from past experiences.
In addition’s, ICR’s innovations will be showcased at the same venue on Wednesday, September 6 (10am-10.30am) during a dedicated Technology Spotlight Session. This EIC event, hosted by Josh Cannell, Interim Head of Sales – Quickflange™, and Calum Macnaughton, Inspection and Integrity Engineer at ICR, will put the focus on Quickflange™ and INSONO™. Day 2 of the EIC Collaboration Zone – Navigating Net Zero – is sponsored by ICR.
Ross said: “Offshore Europe serves as an excellent platform to engage with the industry and share best practice and innovative ideas. Decarbonisation stands as a pivotal element in ICR’s strategy for fostering sustainable growth and both these EIC events provide a first-rate opportunity to highlight our ethos and smart technology.”
ICR’s Quickflange™, a weldless connector solution, offers an alternative for cold work applications, particularly for high-performance flange-to-pipe connections. This technology facilitates permanent repairs, enhancing pipeline integrity and ensuring fluid flow, all without the need for welding or hot work. With its wide range of applications, Quickflange™ has proven to be both cost-effective and efficient, reducing repair times by up to 80% compared to traditional methods. Remarkably, it also contributes to a 57% reduction in greenhouse gas emissions when contrasted with conventional welding practices.
INSONO™ is an innovative NDT (non-destructive testing) technique for the inspection of engineered composite repairs. It is a solution that allows for the extension of defined life repairs, reducing waste while avoiding high-carbon emissions from traditional steel replacement alternatives. INSONO™ complements ICR’s Technowrap™ range and provides operators with the assurance their composite repairs are fit for purpose and satisfy regulatory body guidelines on inspection criteria.
Technowrap™, a lifelong repair system, boasts the capability to address internal, external, and through-wall defects, even when dealing with complex geometries. This innovative solution has demonstrated a remarkable 66% reduction in emissions when compared to conventional replacement methods.
In his capacity as Group Director, Ross oversees the ICR repair division, which encompasses Technowrap™, Quickflange™, mechanical services and leak sealing business lines. He holds a BEng in Civil Engineering and an MSc in Offshore Engineering and is a chartered structural engineer. With 30 years of industry experience, he has held senior positions in various companies, including TAQA, EnQuest, and EnerMech.
Offshore Europe is celebrating its 50th anniversary. For more information about the conference & exhibition, please visit https://www.offshore-europe.co.uk/en-gb.html
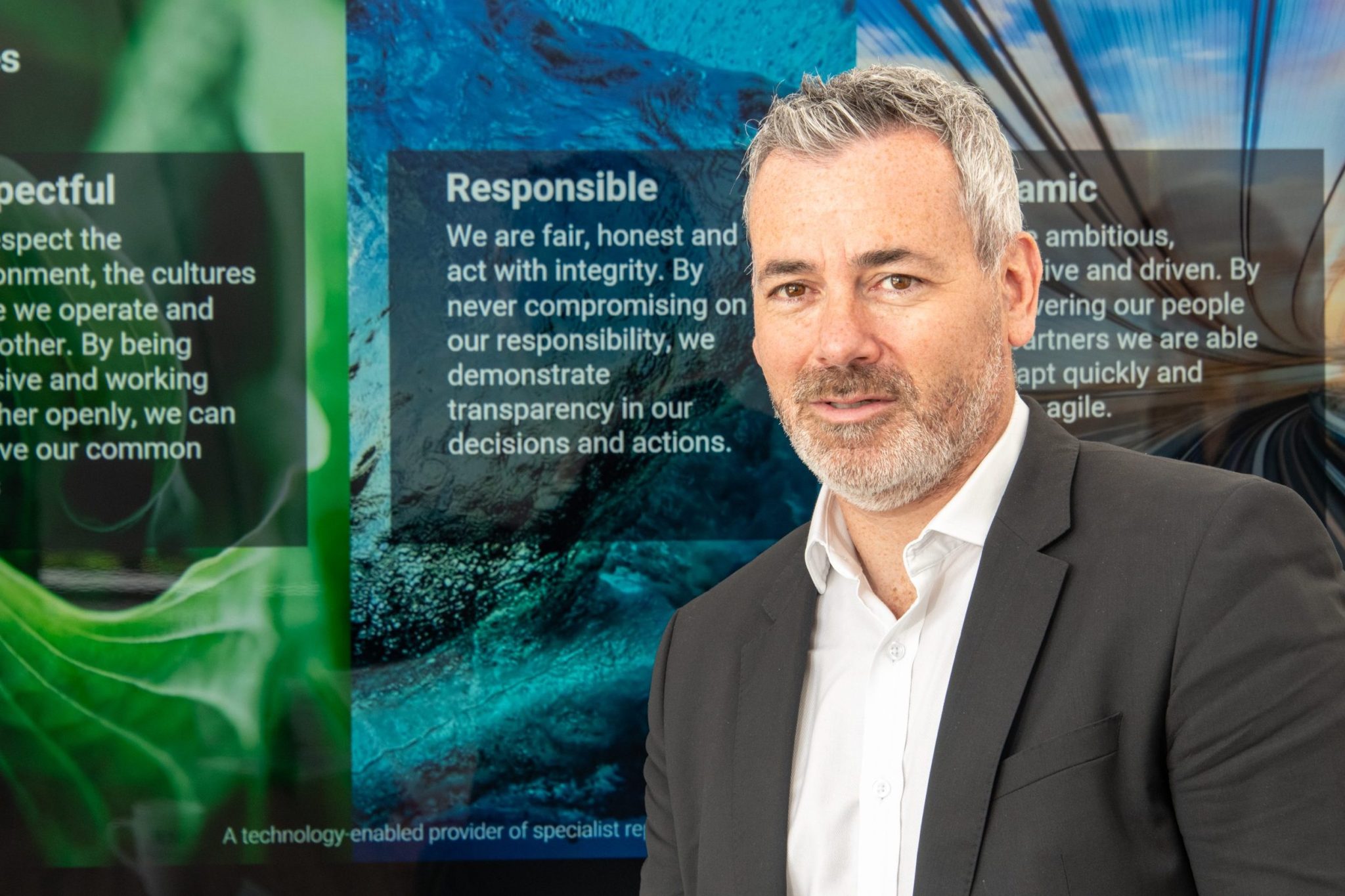