Client challenge
Ferrovial Construction, as part of the Southern Runway Targeted Interventions integrated project team, employed Sky-Futures™ to conduct a drone-based photogrammetry survey of the southern runway at Heathrow Airport in July 2020.
At the time of the survey, restrictions from the COVID 19 pandemic were still in force. During this window the northern and southern runways were alternating single runway operations every 2 weeks.
In this context, Heathrow set out to undertake targeted deep interventions on the southern runway that would not have been possible otherwise. In order to improve the existing information and to deliver an accurate survey of the area, in a limited time, the team planned to perform the works taking advantage of the southern runway closure (Northern Single runway operations). The construction works were delivered by Ferrovial Construction between the months of July and September, combining daytime possessions in July and night-time activities during August and September.
Surveys are part of the early preparation activities for a given project, when historical records are analysed, gaps identified, and a survey scope prepared to complete the existing information. In this case, the scope included topographical, utilities, and dilapidation surveys of the whole area with the objective of creating a detailed ‘digital twin’ of the runway.
Using Sky-Futures™ drone expertise, detailed data and analytics could be provided in an innovative, yet safe manner to support with future planning decisions.
What we did
Given the existing operational context and based on the success from the previous implementation of survey drones on the Kilo Apron Development (KAD) Project, Ferrovial Construction proposed the innovative use of a drone-based photogrammetry survey to provide an alternative way to commission and deliver the topographical and dilapidation surveys required.
Sky-Futures™ used its 9 years’ experience of providing drone-based inspections in complex environments to support this unique project. A robust project management plan was implemented, tailored to the considerations of operating drones in one of the world’s busiest airports. Critical to the success of this was ensuring that the correct governance was in place. All relevant stakeholders were engaged with and all requisite permissions were in place to undertake the work. Sky-Futures™ and Ferrovial Construction worked directly with Heathrow Air Traffic Control, NATS and Heathrow Airside Operations to ensure that everyone was aligned with how the project could be delivered in a safe and effective manner.
To undertake the survey, Sky-Futures™ deployed a 2-man team equipped with a Real Time Kinetic (RTK) drone and worked at all times under Ferrovial Construction site supervision. Whilst the South runway was not active, aircraft were still taxiing across the runway. The team therefore broke the flight path into sections along the length of the runway in order to coordinate with other works in the area. This allowed the team to deconflict with any taxiing activity with ease and ensured that maximum safety was maintained throughout any flights, whilst causing no impact to the ongoing operations of the airport itself. The North runway remained fully operational throughout the whole project window.
Results
- The project was scheduled to be conducted over 4 days; however, the survey team were able to complete the project in 3 days without compromising the data quality. This reinforced the value of Sky-Futures’ drone service in being able to offer both a time and cost-efficient solution when compared to traditional methodologies.
- The aim of the dilapidation survey was to capture existing features like paint marking, manholes, airfield ground lights (AGL), certain cracks and previous repair works to complete the existing record information.
- Traditional dilapidation surveys are usually done by a survey team on site taking photos and references, translating these into a report. It is a time-consuming and laborious task as information must be organised and classified to indicate the elements being captured and their location.
- Processing the data in-house not only allows us to have total control of the deliverables that we produce without depending on a third party, but it also gives us the opportunity to research and test the various possibilities new technologies can bring to the project.
- Before the intervention works started on site, the dilapidation survey of the runway was available on the cloud-based platform for everyone to work with. A dilapidation survey in the form of an orthomosaic (aerial photo) which is a “screenshot” of the runway at a specific moment in time, which, unlike traditional survey reports, prevents any misinterpretation.The cloud-based platform was set up with all relevant information the team needed to interrogate the data. Existing record information and design drawings in the form of CAD drawings were uploaded and overlaid to the orthomosaic.
- During the works on site, the tool was widely used by the team. Having the right information available in their laptops, reduced the time on site and the need for revisits, minimising the exposure of the team to interact with potential risks.
- The designers and construction team were able to validate areas of works by overlaying the design drawings to the orthomosaic, and based on the high accuracy of the images, they could make better informed decisions and plan the works accordingly.
The information also became a useful tool for our client, as it helped them visually brief the different stakeholders at the airport:
- Heathrow Development to understand the scope and progress of the works
- Airside Operations to daily brief on AGL status, plans and progress
- Airside Operations for Communications and progress meetings
- Heathrow Investment Committee (HIC)
- Airlines
- Handover team to understand the final condition and to compare it with the original. This was done by overlying the orthomosaic with the existing records and the as-built information on a CAD drawing to reflect the whole story
- The dilapidation survey also provided Heathrow with valuable information to update and complete their existing records if required and inform future projects.
- The project showcased how drones can continue to provide clients with a technological platform to offer dynamic alternatives to traditional practices. The team proved that with the correct planning and procedures in place, drones can be deployed safely and effectively even in highly complex environments, such as Heathrow Airport.
- The survey became a key asset of daily use to consult information, avoiding the need to re-visit site, saving time, and allowing the team to focus on the important tasks of planning and executing the works safely.
- The feedback from the whole team and especially the client was excellent.
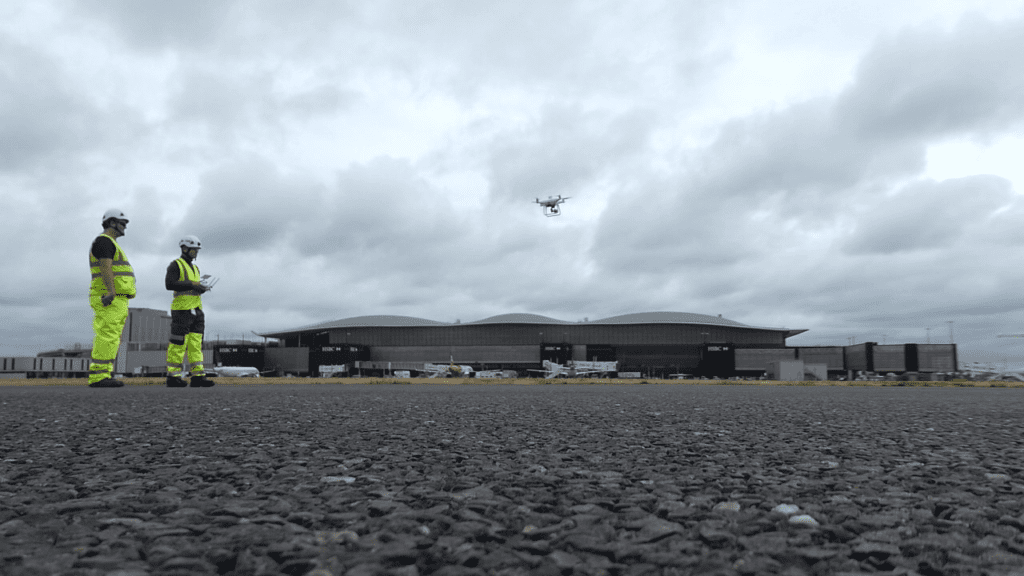
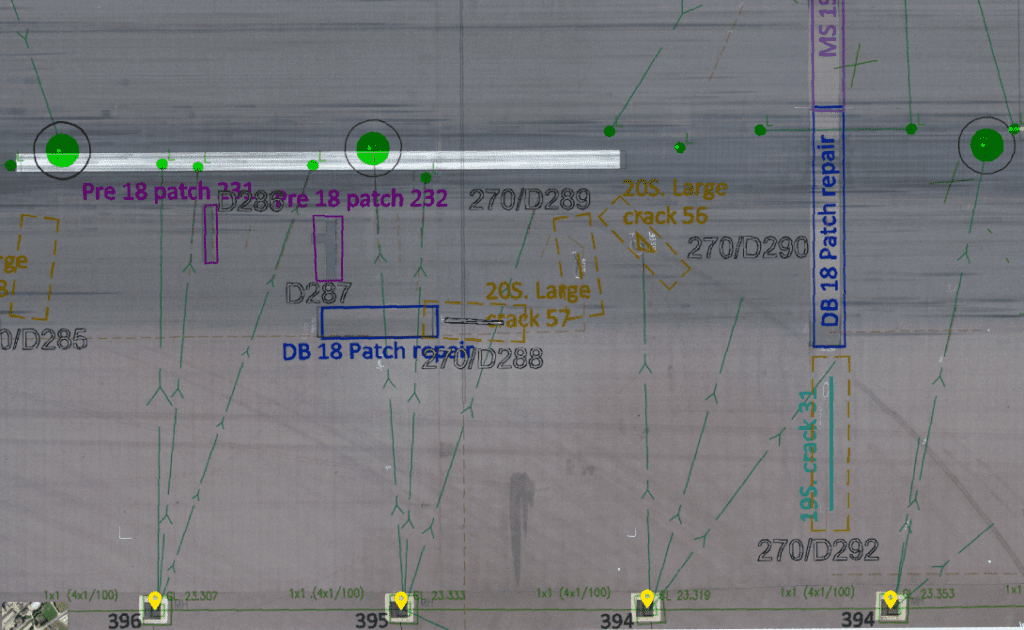
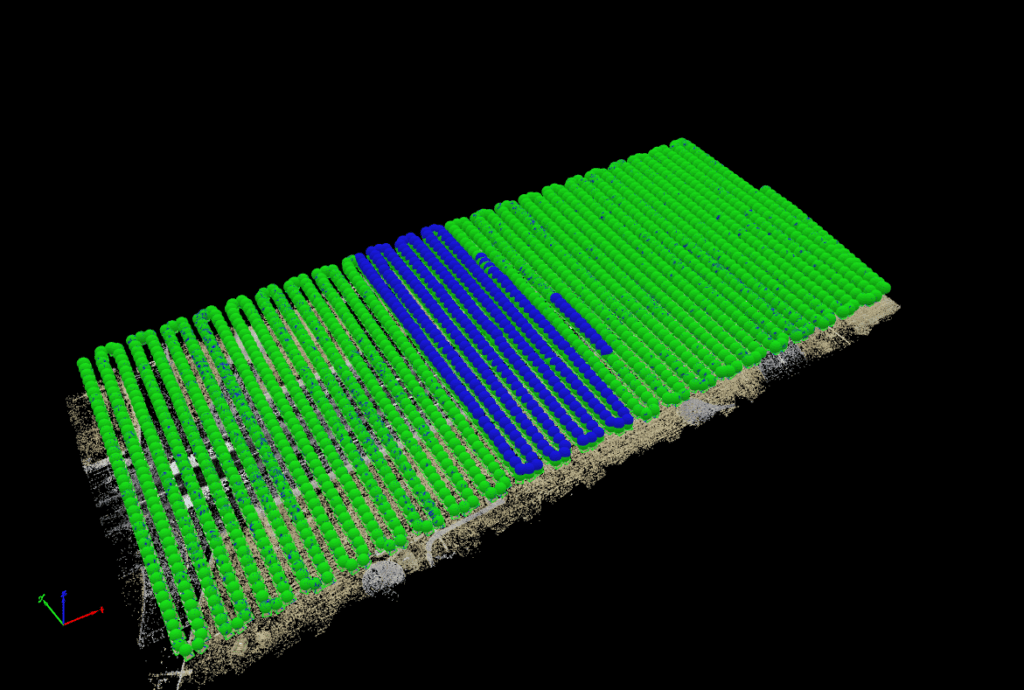
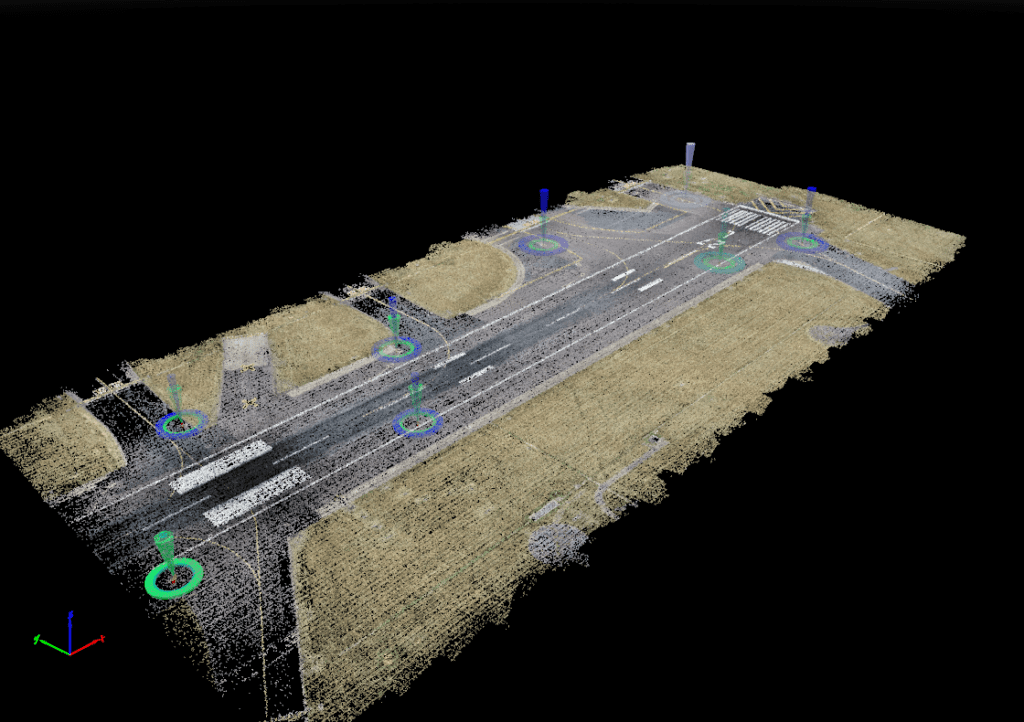
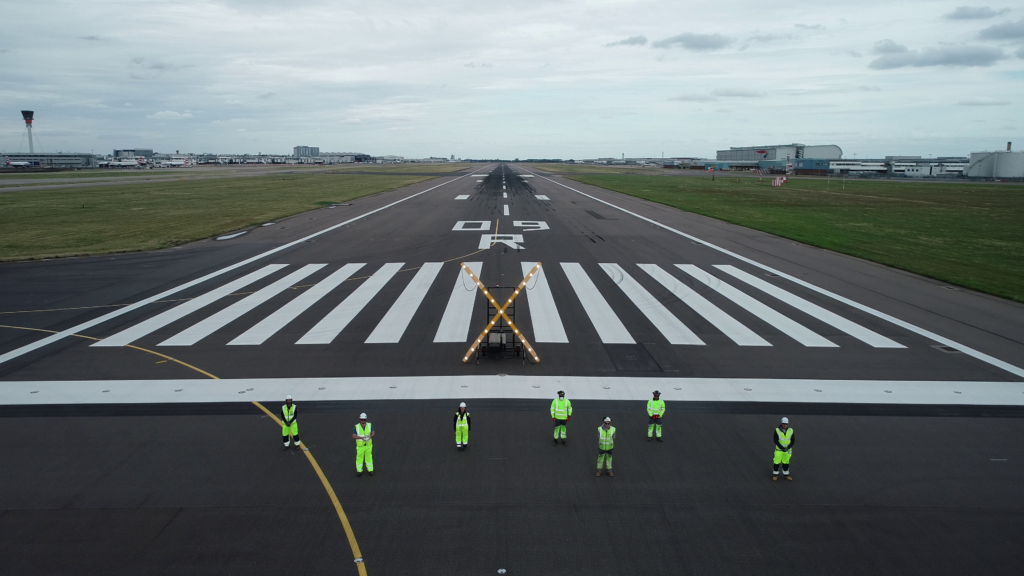
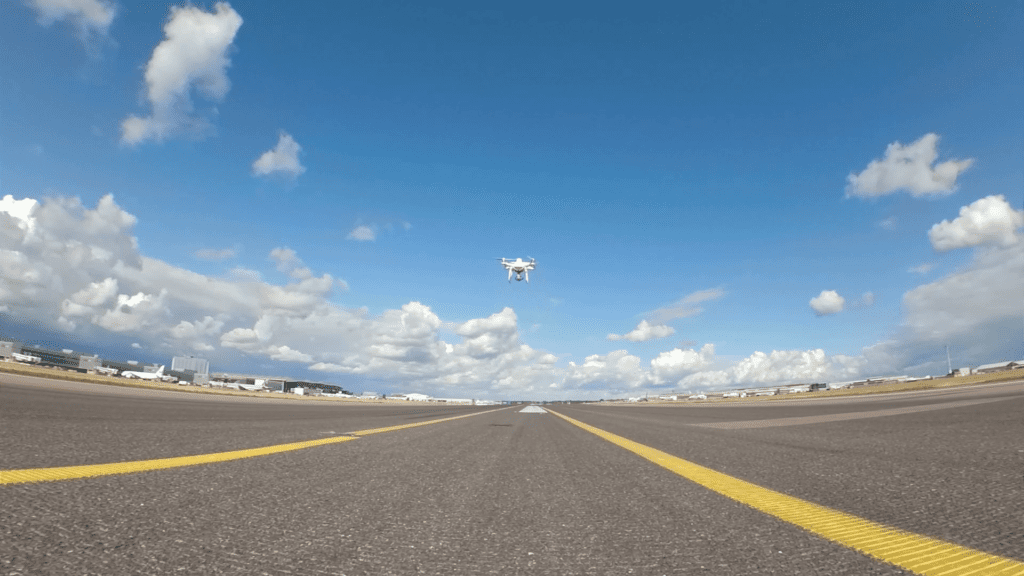
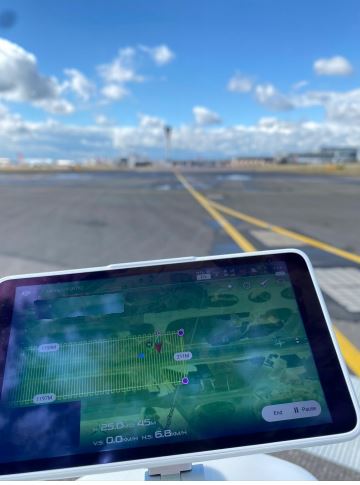
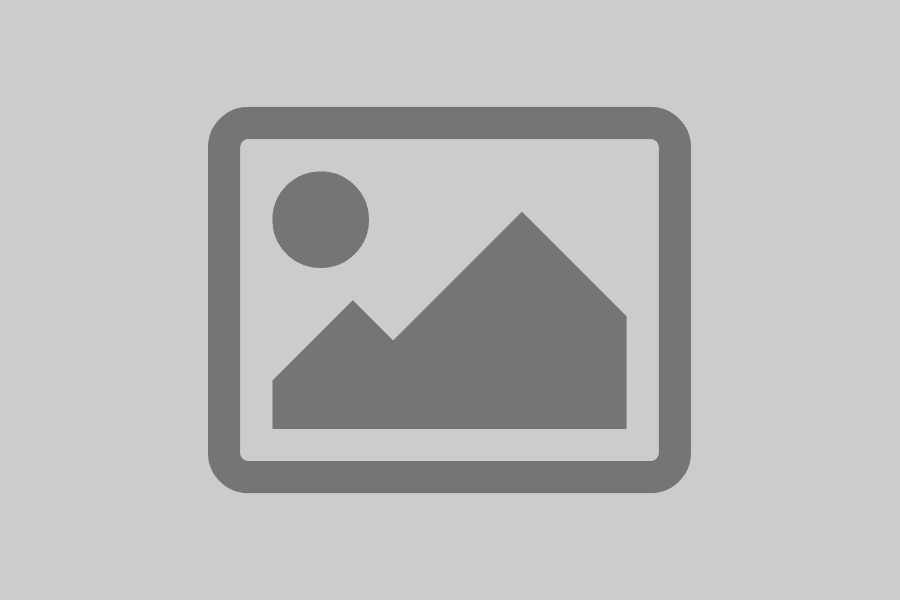
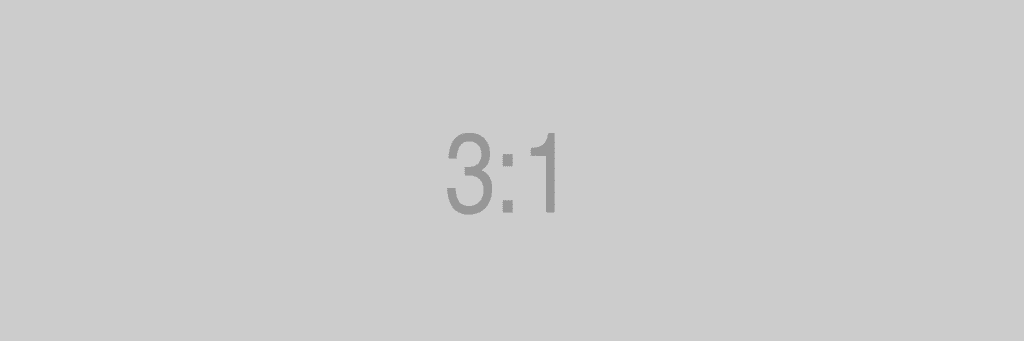
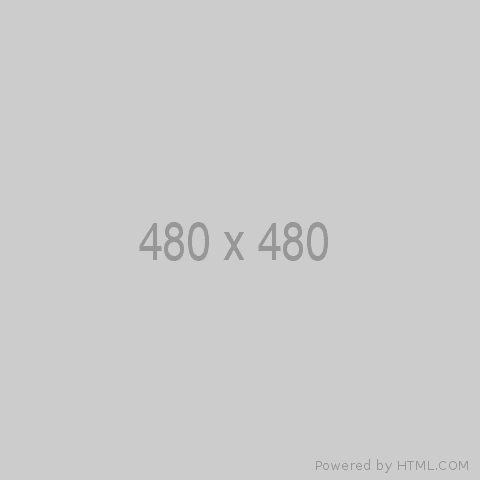
Client challenge
Dataverse-AIM, is a software development and consultancy business that provides asset integrity management software and data validation support services. They faced the challenge of efficiently inspecting an offshore substation at the Thanet Wind Farm, located offshore in Kent. The objective was to conduct a comprehensive visual inspection of the platform while avoiding the logistical complexities and costs associated with helicopter mobilisations. Additionally, there was a need for regular condition monitoring data to aid in planning future maintenance and repair scopes. Simultaneously, the terrestrial cable spanning 12km from the shoreline to the onshore substation required inspection, demanding a method that provided detailed insights without causing disruptions.
What we did
To address Dataverse’s challenges, we conducted an offshore substation inspection from a vessel, eliminating the need for helicopter mobilisations and providing a cost-effective visual assessment. The survey aimed to ensure ongoing condition monitoring and assist in planning future maintenance. As part of the same mobilsation, we performed an onshore survey of the 12km terrestrial cable, utilising both fixed-wing and rotary aircraft to gather comprehensive data. Our approach included leveraging advanced technology, such as photogrammetry, to deliver detailed inspection reports and models of the cables and structures.
Results
The collaborative initiatives delivered impactful outcomes for Dataverse-AIM. The vessel-based inspection emerged as a cost-effective substitute for helicopter mobilisations, facilitating a thorough visual assessment of the offshore substation. Conducted at regular intervals, the surveys offered Dataverse essential condition monitoring data, empowering proactive planning for upcoming maintenance and repair activities.
Moreover, the comprehensive inspection of the 12km terrestrial cable, executed using fixed-wing and rotary aircraft, resulted in detailed inspection reports and photogrammetry models, providing Dataverse with a comprehensive understanding of their cables and structures.
This case study highlights our commitment to innovative and efficient solutions in enhancing offshore infrastructure resilience for Dataverse-AIM. The integration of vessel-based and aerial surveys showcases our ability to provide comprehensive insights while minimising logistical challenges and costs for our clients.
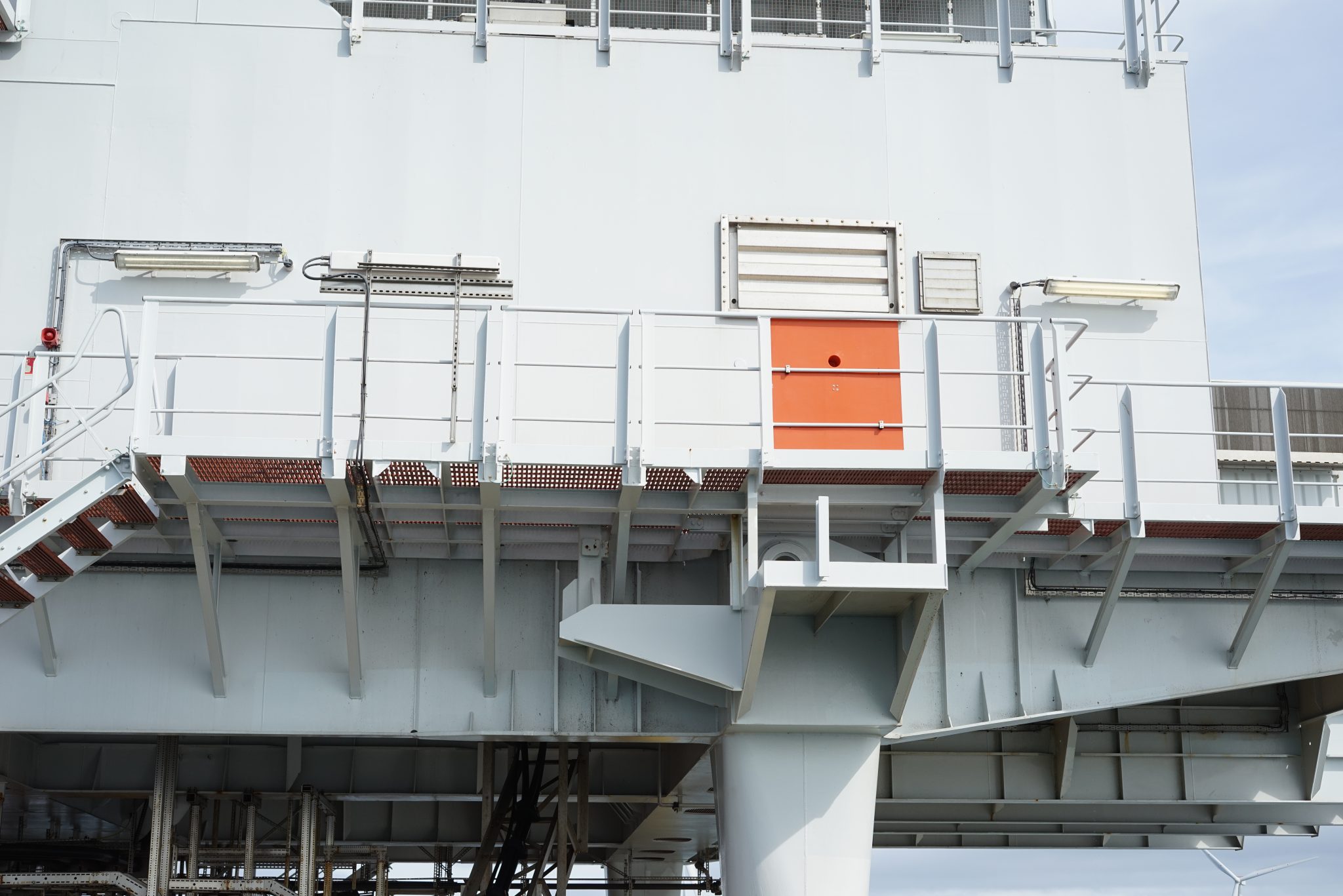
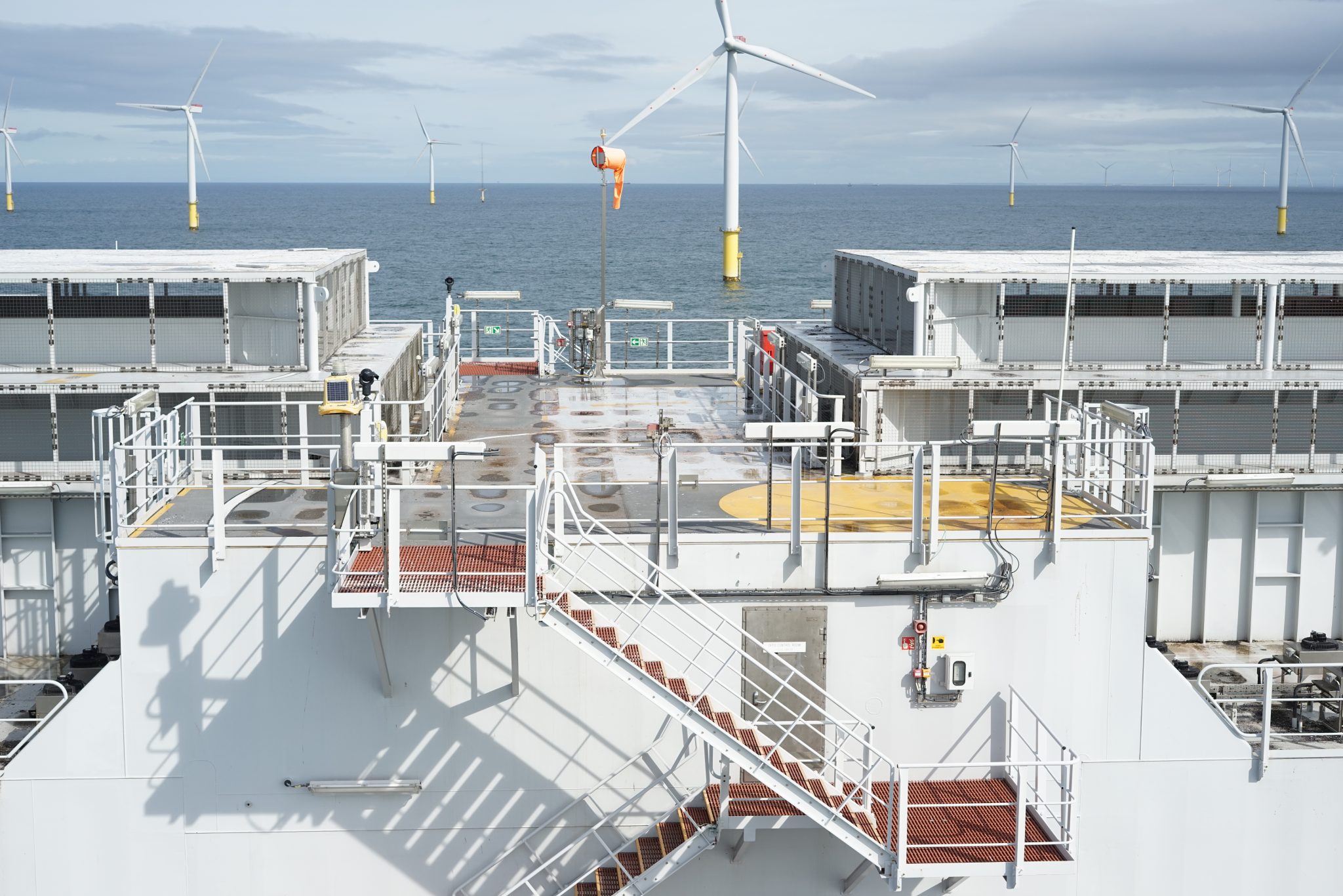
Date: 2022
Client: Repsol Sinopec
Location: Moray Firth, Scotland
Client Challenge
Repsol Sinopec, a prominent energy conglomerate, enlisted ICR’s Sky-Futures™ drone inspection team to perform a thorough assessment of two wind turbines situated in the Beatrice oil field, located in Scotland’s Moray Firth. The turbine’s support structures and blades exhibited various forms of damage and irregularities, including cracks and compromised safety components, previously identified by rope access personnel. Furthermore, as the turbines were due to reach the end of their service life in the next five years, it was crucial to visually confirm the structures’ overall condition and ensure their continued functionality.
What We Did
Utilising decades of experience of both piloting unmanned aircraft, conducting challenging offshore inspections and remote sensing operations, our team deployed to the site using the crew access vessel as a launch point. Here they conducted a number of drone flights and gathered a large dataset of imagery to carry out the visual inspection of the condition of the turbines. This method reduced the exposure of personnel to working at height and enabled a swift and thorough inspection.
Employing ultra-high-resolution imagery, a meticulous examination was conducted to evaluate the identified anomalies, indicating no evidence of further deterioration. However, the inspection did reveal additional areas of concern, previously unaccounted for, which were meticulously documented and incorporated into a comprehensive inspection report. This report was then delivered to the client via our secure online portal to ensure optimal safety and confidentiality.
At the same time, we assessed the following component areas of the two turbines to identify any potential dropped objects, or other conditions which could impact the safe decommissioning of the turbines:
- Turbine blades
- Nacelles
- Support towers
- Jackets
- Access platforms
An additional report was issued to the client for use in their planning.
Results
Our team carried out the inspection safely and well within the planned time for deployment. They were able to launch the drone system from the crew transfer vessel and didn’t need to access the turbine base at any point. This approach saved time and further reduced the exposure to risk from being able to use a drone equipped with a large format still image camera system, rather than having rope access personnel descend the blades.
The detailed reports and accompanying imagery provided the client with a comprehensive understanding of the condition of the turbines and their support structures, serving as a crucial component of their decommissioning strategy.
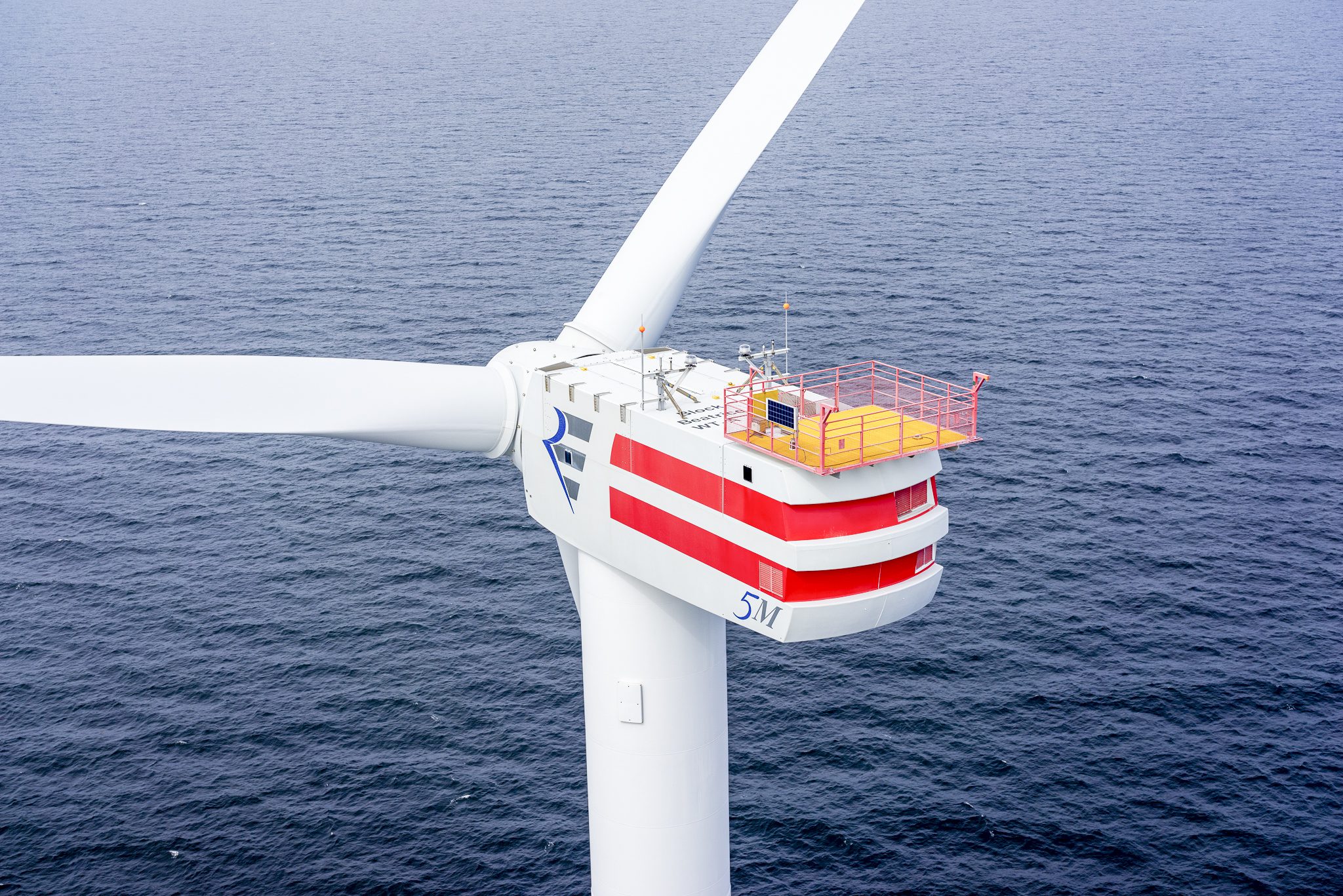
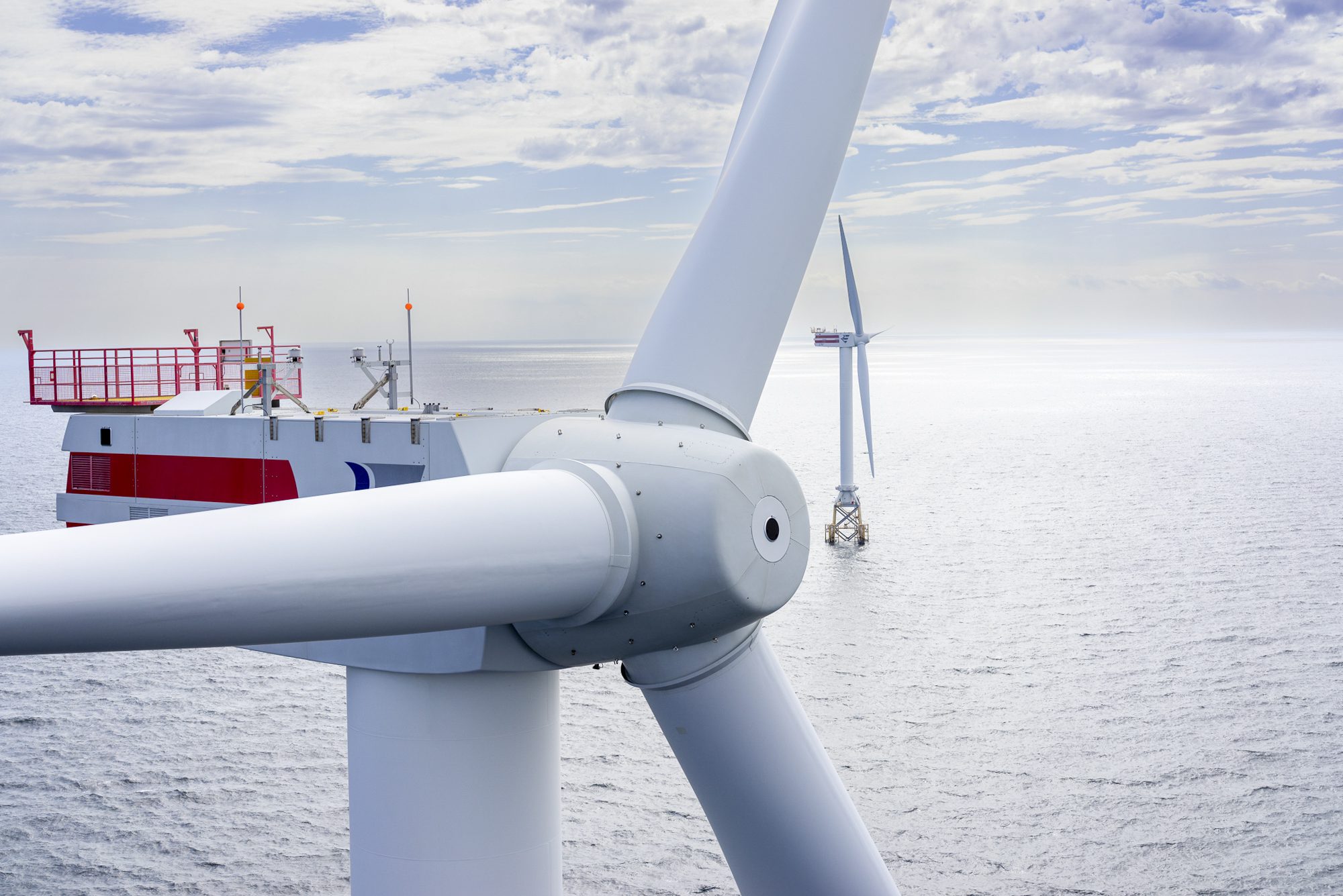
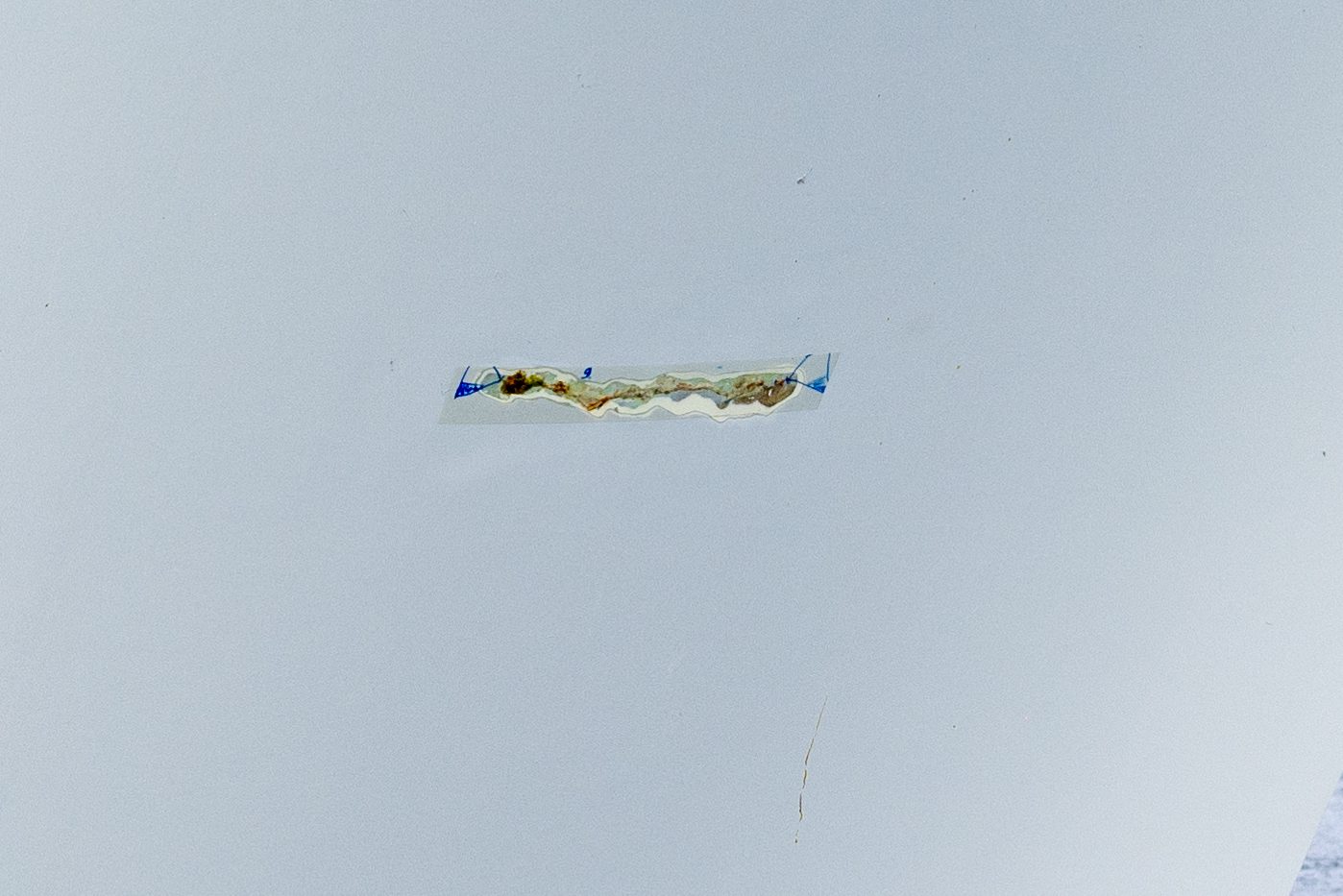
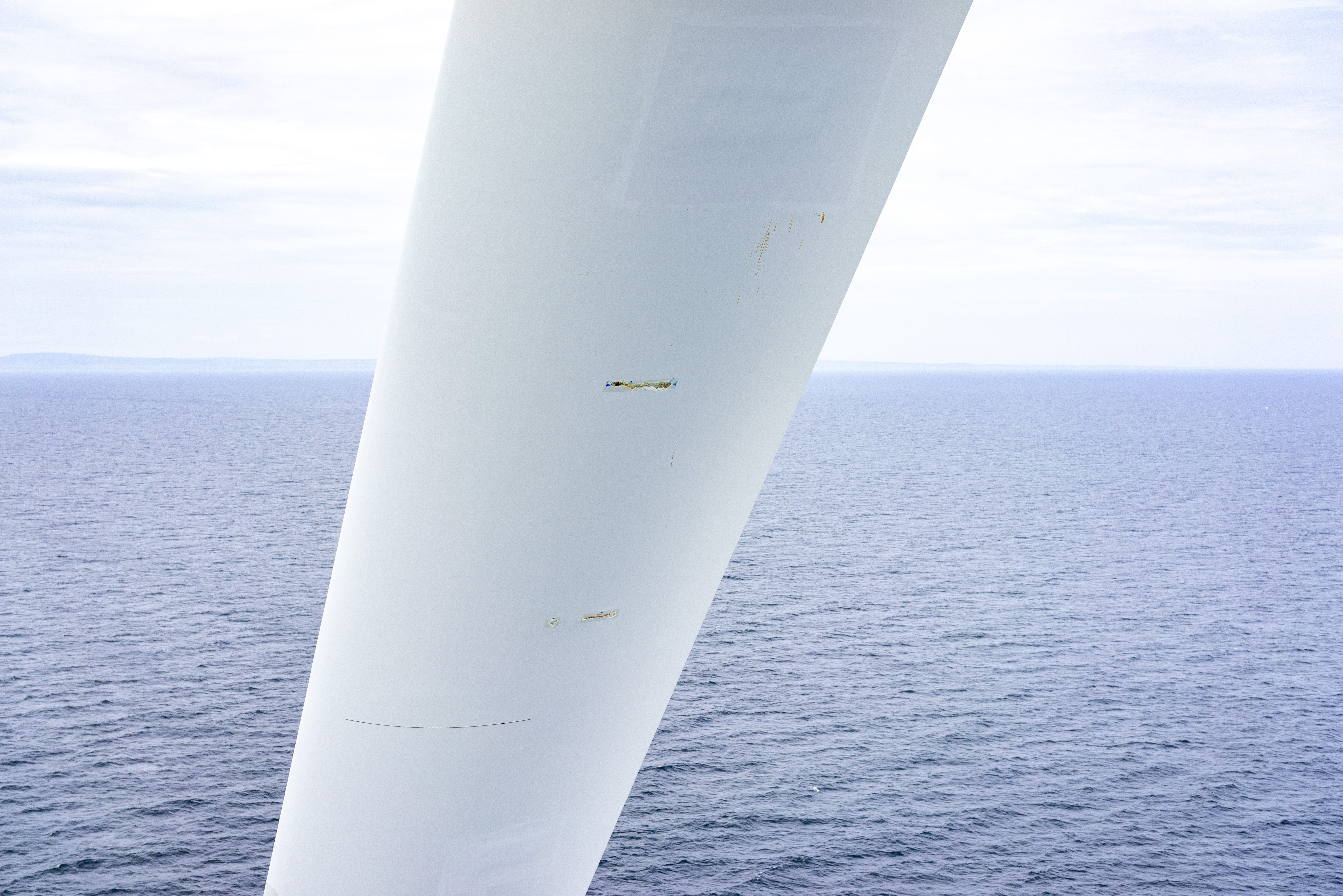
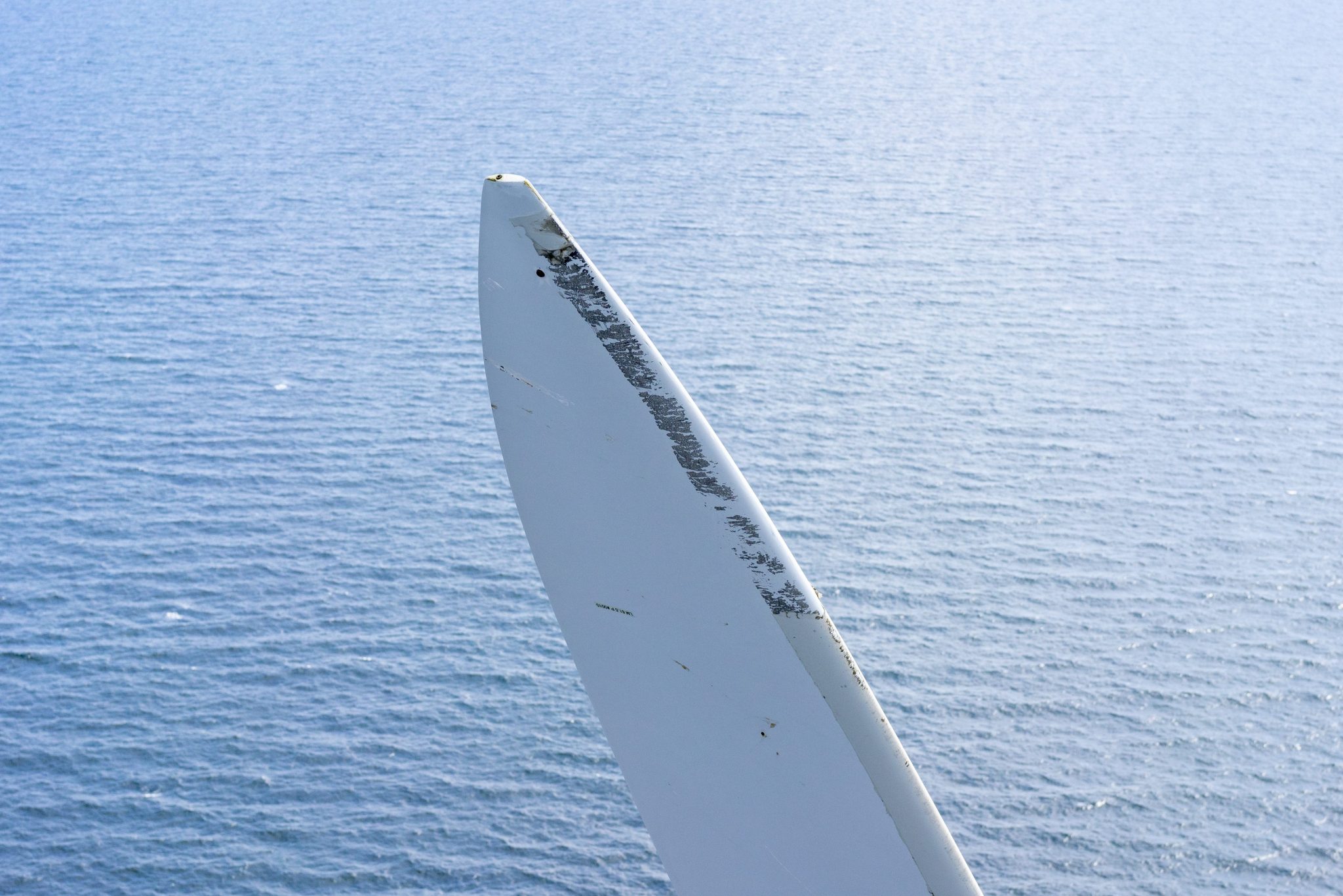