Client: Operator
Asset: Onshore terminal
Location: UK mainland
Result: INSONO™ inspection completed on production critical pipework. Results were fed back into WSE allowing continuous monitoring.
Client challenge
For many clients, ensuring the integrity of your repairs is an essential factor in establishing a baseline for future inspections and is integral to the Written Scheme of Examination (WSE)/ Risk Based Inspection (RBI) process. When an energy operator approached our team to conduct a comprehensive visual inspection and non-intrusive inspection (NII) on a repair, we utilised our extensive experience to accurately identify any potential anomalies that could jeopardise the suitability of the repair for service.
What we did
To address our client’s challenge, we conducted a meticulous close visual inspection covering 100% of the composite repair area, focusing on the external condition of the wrap. Following this, we used INSONO™, a proven non-intrusive technique that utilises soundwaves for a baseline NII examination. This comprehensive assessment evaluated the internal body of the composite wrap and substrate, recording any anomalies that might impact its integrity and life cycle. The established baseline serves as a reference point for future inspections/ examinations, aligning with the RBI and WSE.
Results
By using INSONO™ we effectively located, measured, recorded, and monitored anomalies associated with the wrap repair and substrate. By employing this technique, we provided the client with a robust solution for assessing composite repairs in areas with challenging accessibility or complex geometries, including bends, valves, multiple pipework connections, headers, pipe racks, vessels, and various structural locations. Our examination not only addressed the current concerns but also set the stage for ongoing monitoring and maintenance.
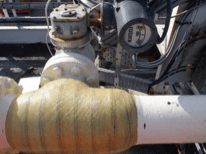
Client: Operator
Asset: Offshore asset
Location: Southern North Sea
Result: Two anomalies were identified and can be monitored over the design life of the repair
Client challenge
A major oil and gas producer approached us looking for continued assurance in the integrity of a pre-existing composite repair used in their infrastructure. They required a comprehensive visual inspection and non-intrusive inspection (NII) to assess the current condition of the repair wrap. The primary objective was to identify, quantify, and record any anomalies that could compromise the pressure-retaining capacity of the repair and substrate for inclusion in the framework of their Risk-Based Inspection (RBI)/Written Scheme of Examination (WSE).
What we did
Our team conducted a close visual inspection to evaluate the external condition of the repair wrap. Subsequently, we performed a non-intrusive examination using INSONO™, a technology that uses the principles of acoustic inspection to assess the entire volume of the composite wrap and substrate. This technique was chosen for its capability to detect anomalies in critical areas such as the bond line, interlaminar dis-bonds, and the steel substrate. The goal was to identify any features that could – if left unmonitored – impact the integrity and life cycle of the repair wrap and assess its suitability for continued use.
Results
The examination successfully located two delaminations (voids) within the wrap. Following a thorough technical assessment by the composite design team’s technical authority and fitness-for-service evaluation against defined acceptance criteria, it was determined that these anomalies likely occurred during the application of the wrap. Engineering assessments confirmed that these features had no detrimental significance to the integrity of the wrap repair.
As a result, the client’s Written Scheme of Examination (WSE) was updated in accordance with their Risk Based Inspection (RBI) process. The composite repair wrap was deemed fit for continued service, and a valid justification for extension was provided.
Conclusion
Our composite repair examination, played a crucial role in providing data driven justification for the continued classification of the composite repair as fit for service. The repeatability of this inspection method positions the client well for future life extensions, as potential concerns can be consistently addressed and mitigated. This case underscores the importance of advanced inspection techniques in ensuring the ongoing integrity and safety of critical infrastructure components in the oil and gas industry.
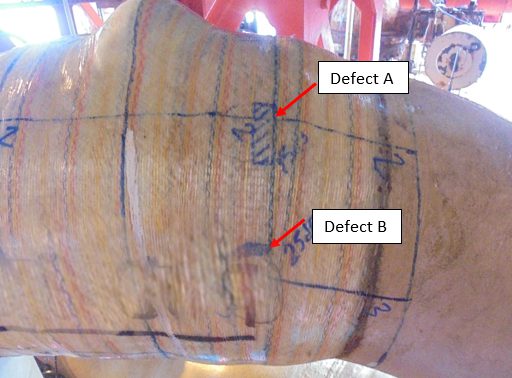
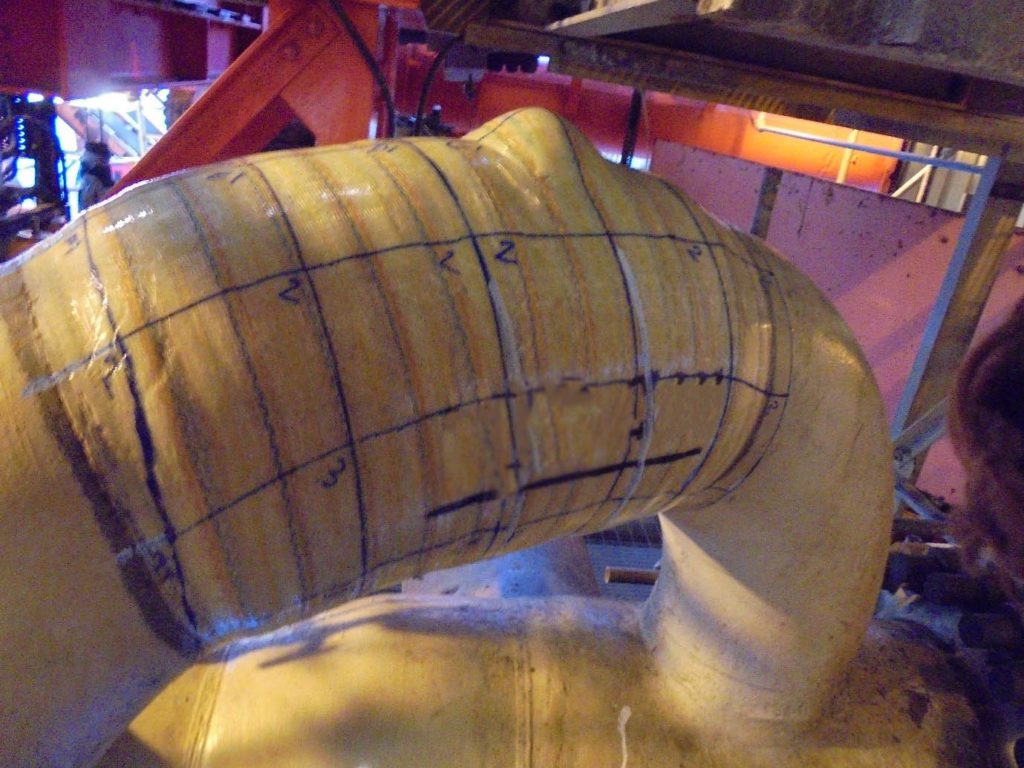
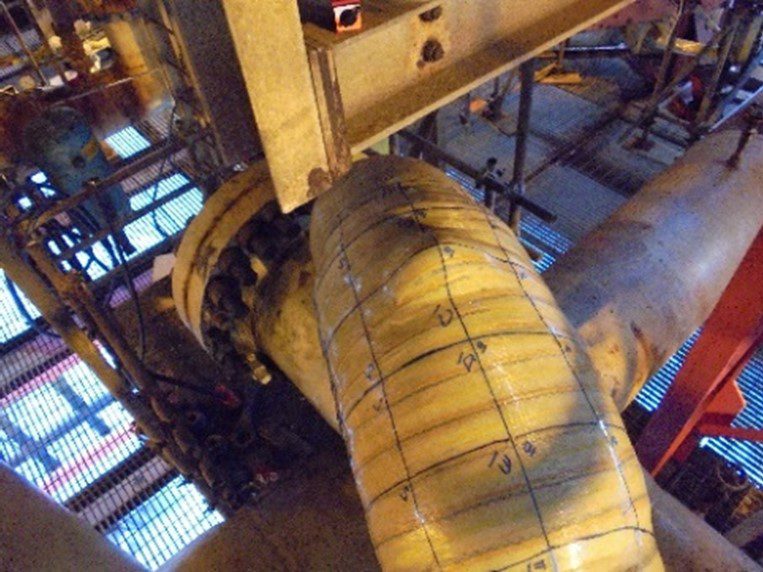
Client: Operator
Asset: Offshore asset
Location: Southern North Sea
Result: The INSONO™ inspection was completed to assess the integrity of wraps applied to a series of off-takes.
Client challenge
Our client, a energy operator, faced the challenge of ensuring the integrity and reliability of their composite wrap processes. They needed a solution that would deliver confidence and assurance in Fitness for Service (FFS)/Risk-Based Inspection (RBI) schemes. The specific challenge was to locate, measure, record, and monitor anomalies associated with both baseline/new wrap surveys and in situ wraps. It is important to identify any anomalies associated with any composite repair and monitor them over time to ensure continued safe operation and minimise risk to the overall infrastructure.
What we did
To address the client’s challenge, we implemented our non-intrusive technique INSONO™ into the FFS/RBI schemes. INSONO™ utilises a non-intrusive (NII) examination technique incorporating low-frequency sound waves to assess the internal body of the composite wrap and substrate. This method locates, quantifies, and records anomalies that could compromise the suitability for service.
The versatility of INSONO™ as a proven non-intrusive technique made it particularly suitable for inspecting wraps in challenging and unconventional areas. This included leaks or damaged areas that tend to arise during production, as well as bends, valves, multiple pipework connections, headers, pipe racks, vessels, and various structural locations. The adaptability enabled it to address the client’s specific concerns and requirements, showcasing its effectiveness in diverse configurations.
Our inspection established a baseline reference for future wrap inspections as part of the Written Scheme of Examination/ Risk-Based Inspection (WSE/RBI) process, ensuring continued service in line with RBI/WSE standards.
Results
The incorporation of INSONO™ as an inspection tool proved to be highly successful. It provided a robust solution for locating, measuring, recording, and monitoring anomalies associated with wrap repairs and substrates. This method demonstrated its efficacy in both baseline, new wrap surveys and current in situ wraps, offering repeatability for ongoing assessments. Our client gained confidence and assurance in the composite wrap process, knowing that potential issues affecting integrity and life cycle were systematically identified and addressed.
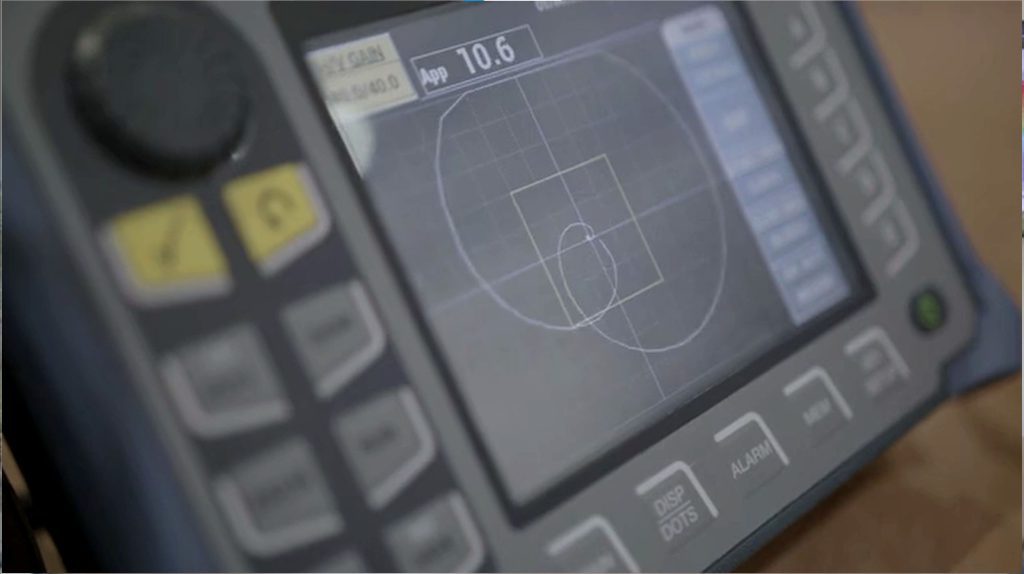
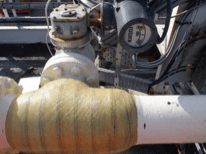