Scope
We were requested by an Oil and Gas Operator to service a number of chemical injection locations throughout the production system on one of its assets during a routine platform shutdown. The majority of these locations had limited service history and ICR had not previously been requested to service these.
At each location the scope of work was to inspect and clean the injection assembly, replace the injection nozzle and renew all pressure retaining seals.
Solution
On retrieval of one of the devices the injection assembly was found to be detached from the carrier plug. It is believed this may have happened upon initial installation with the injection nut becoming caught on a weld impingement. As a result it is suspected that the chemical was not being injected at the desired rate / dispersed efficiently.
ICR removed the weld impingement, changed out the chemical injection nut and installed a new injection assembly.
Results & Benefits
- With the injection assembly now installed correctly and functioning as intended, the client noticed a significant decrease in the chemical injection rate required to achieve optimum performance. It is believed that due to the previous injection assembly becoming detached, the rate of injection had been increased in order to achieve the desired result.
- As a result the client has realised savings of thousands of pounds per week.
- Best practice is to inspect chemical injection locations on a regular basis to ensure the internal assemblies are functioning correctly and are free from blockages and damage.
- Ensuring devices are installed in the approved manner and are of the correct specification for their intended duty, not only provides confidence in chemical deployment but can also result in savings from reduced chemical treatment.
- Improved integrity management with the assurance that chemicals are being deployed effectively and efficiently.
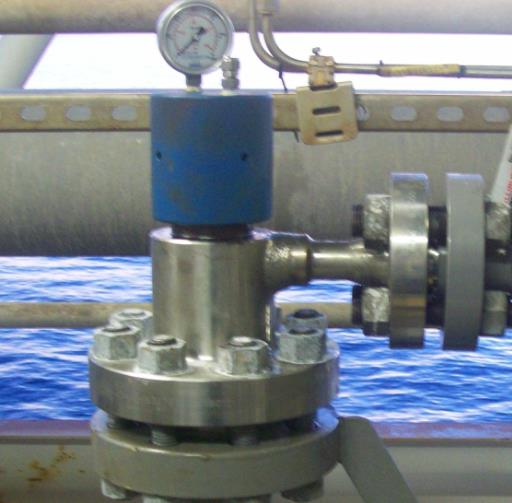
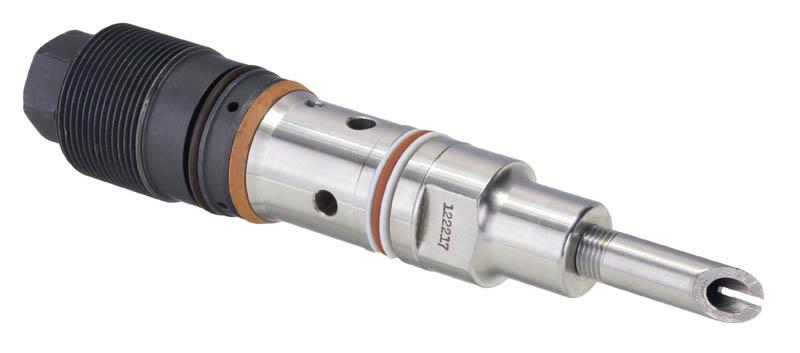
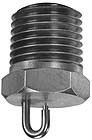
Featured articles
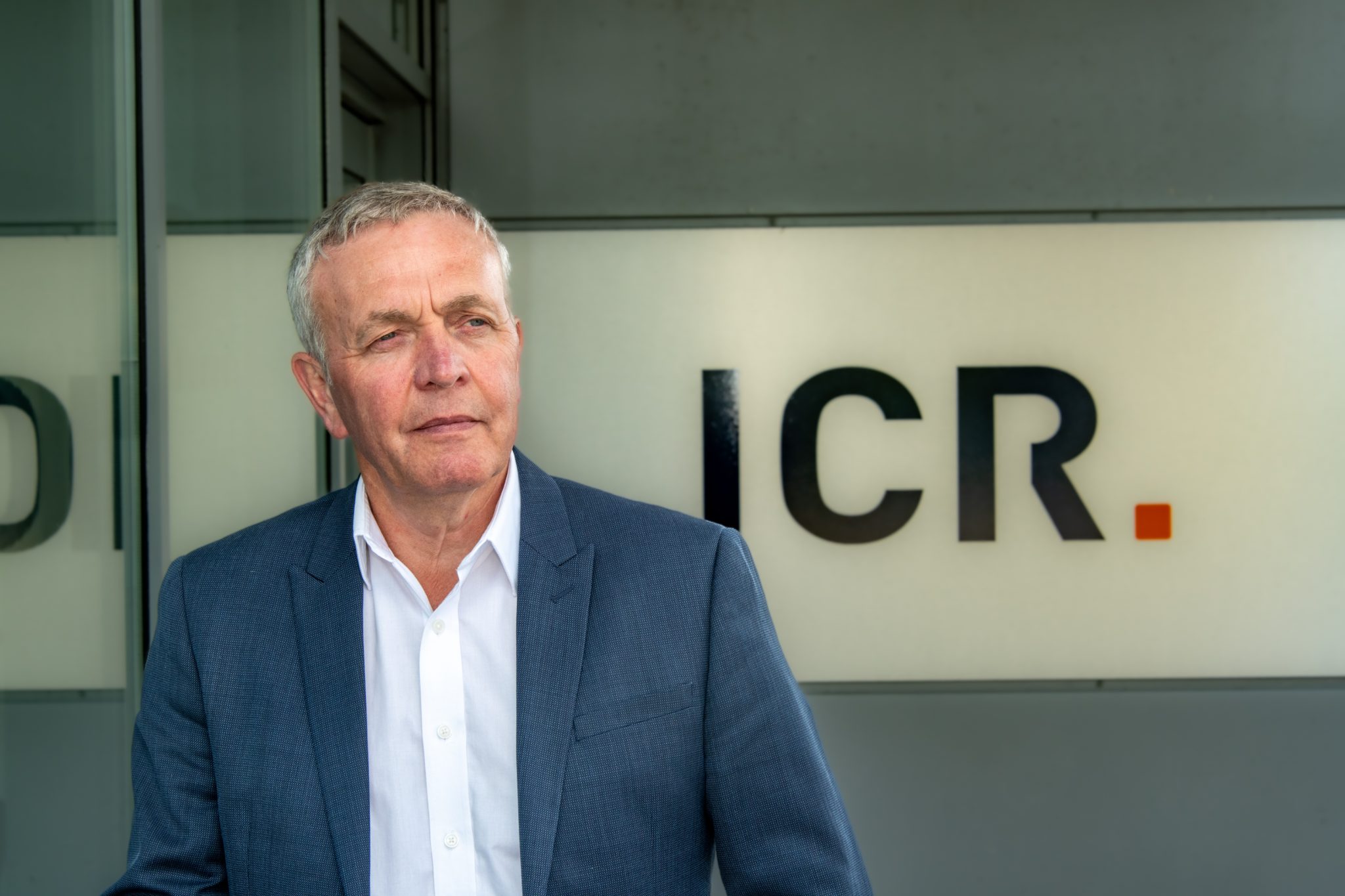
University of life stands Govan-raised engineer in good stead
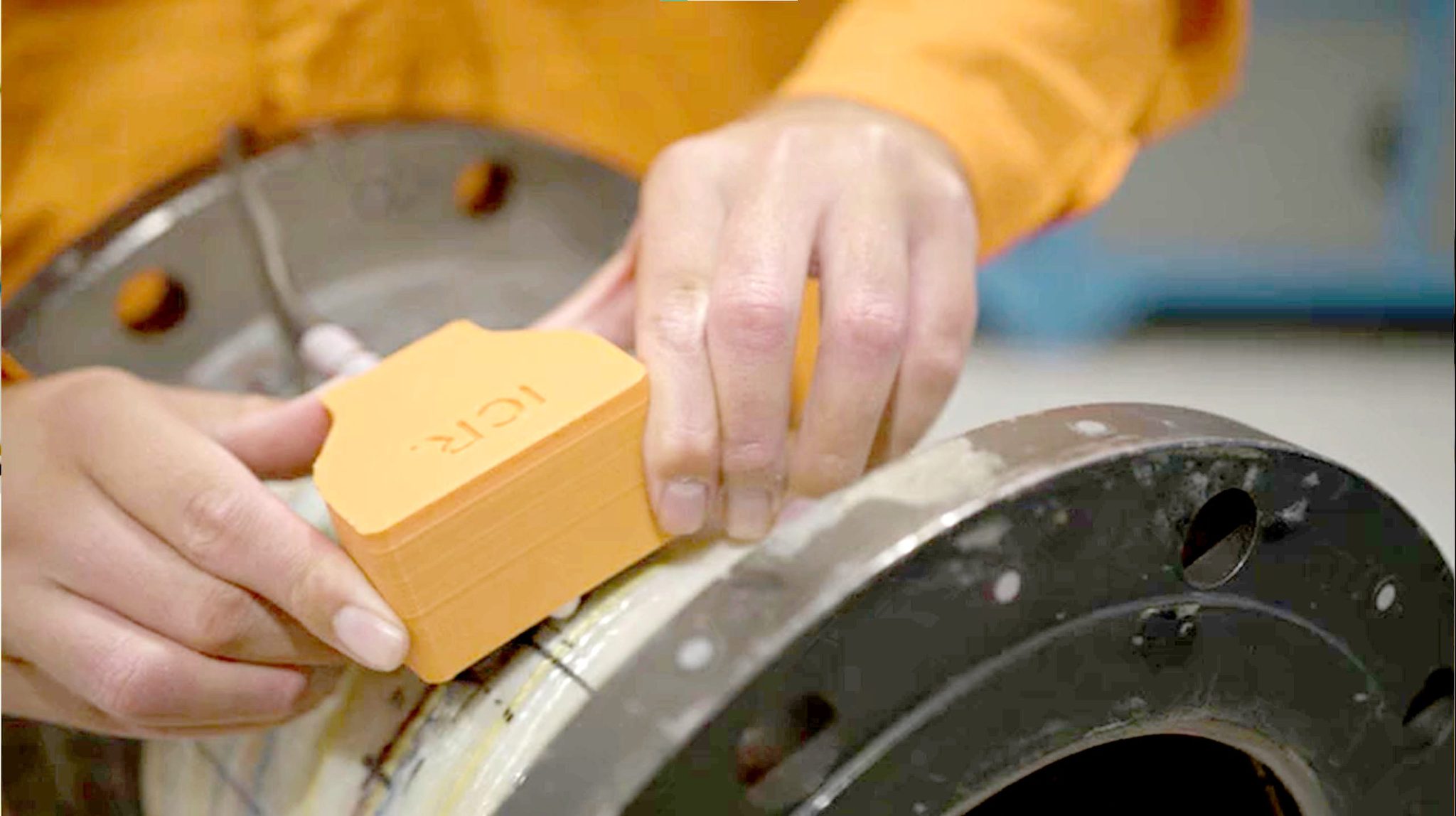
LR and UKAS boost for ICR Group’s INSONO innovation
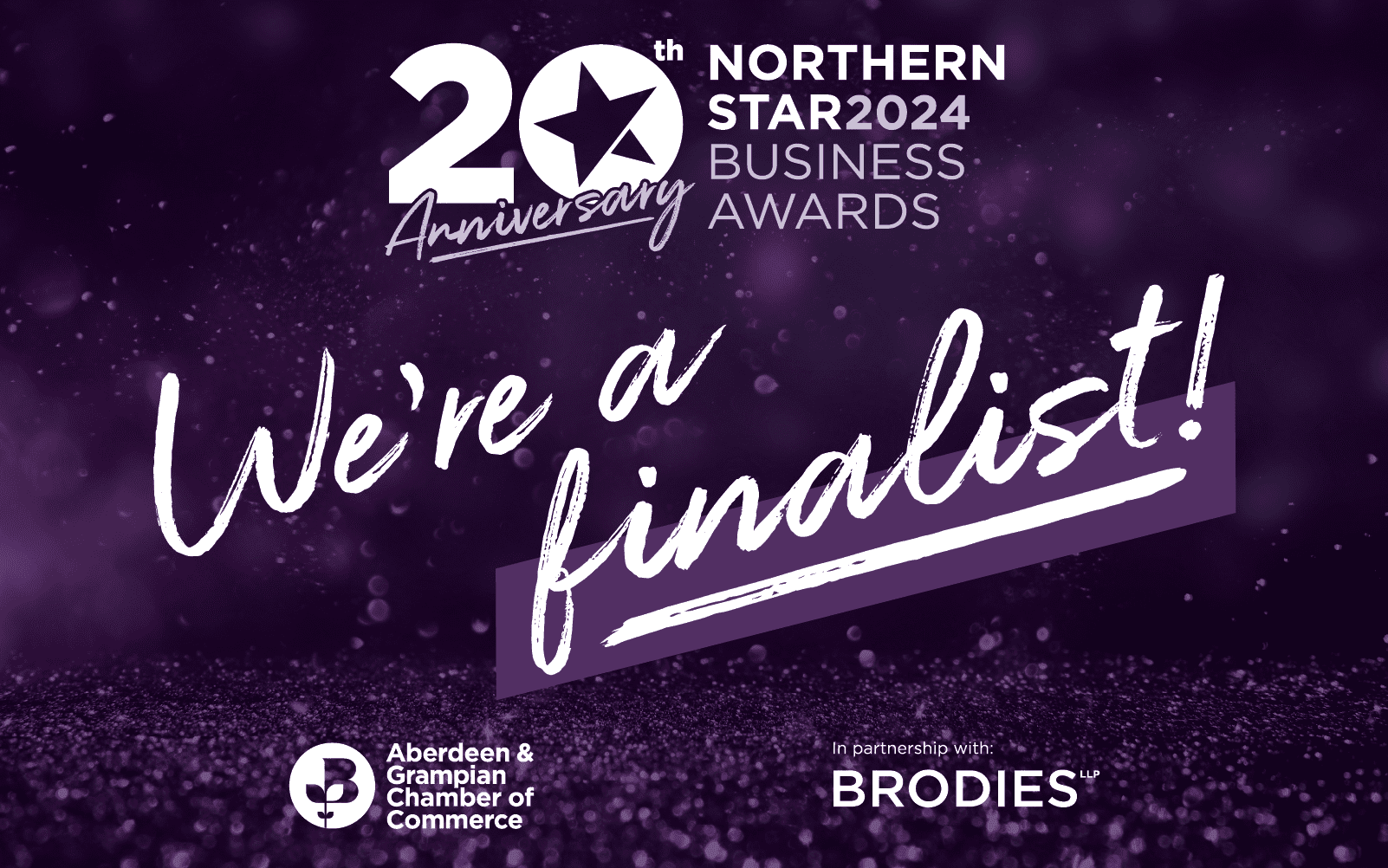