Client: Major European chemical manufacturer
Asset: Manufacturing plant
Location: UK
Client challenge
A major European chemical manufacturer undertaking plant upgrades in the UK faced the challenge of creating 10” diameter holes in 20” diameter x 1½” wall carbon steel pipes. The program of works was challenging, with a short timeframe required for completion. In addition there were tight access restrictions at some work locations, requiring innovative solutions for efficient execution.
What we did
In response to the client’s challenges, we developed a strategic solution to meet the demanding scope. Instead of the conventional approach of drilling a smaller hole and boring it out to the desired size, we opted for trepanning in a single operation. This decision aimed to streamline the process and adhere to the tight timeframe set by our client.
Leveraging our machining expertise and industry contacts, we commissioned 10” trepanning cutters. These cutters were then paired with our modular drilling equipment. The modular design of the equipment allowed it to fit into spaces with tight access restrictions, ensuring flexibility and adaptability to the challenging work environments.
Results
Our innovative approach and precise execution led to several achievements:
Efficient operation: The trepanning cutters, paired with the modular drilling equipment, proved to be an efficient solution. The decision to trepan in a single operation eliminated the need for additional finishing steps, saving time and resources.
Tolerance compliance: The cutters performed flawlessly, producing holes to the required tolerance without the need for further finishing operations. This precision ensured that the newly created holes met the exact specifications set by the client.
Timely completion: Despite the challenging program of works and tight access restrictions, all holes were successfully completed within the specified timeframe. Our ability to navigate the constraints and deliver on time showcased their commitment to meeting client expectations.
In conclusion, our strategic use of trepanning cutters and modular drilling equipment not only addressed the client’s challenges in creating large-diameter holes but also demonstrated efficiency, precision, and timely completion of the complex work scope. This case study highlights the importance of innovative solutions in overcoming tight timeframes and access restrictions in industrial projects.
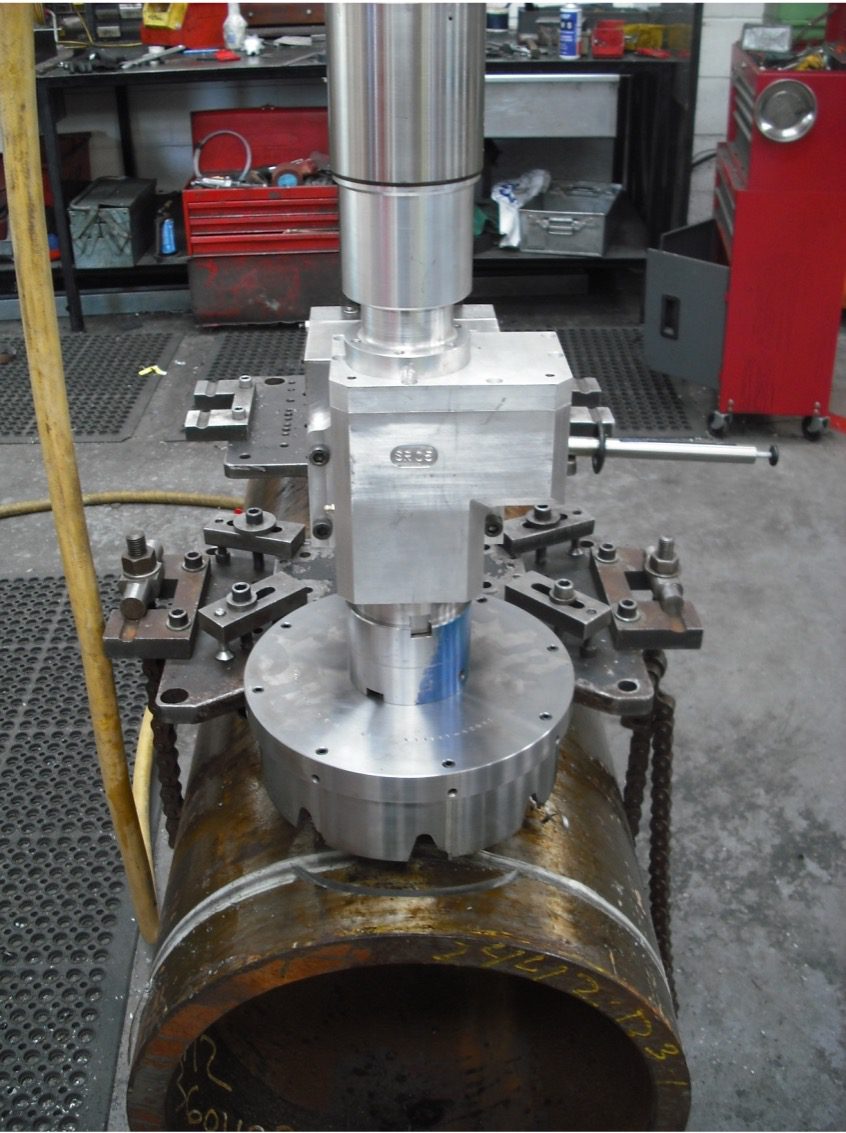
Featured articles
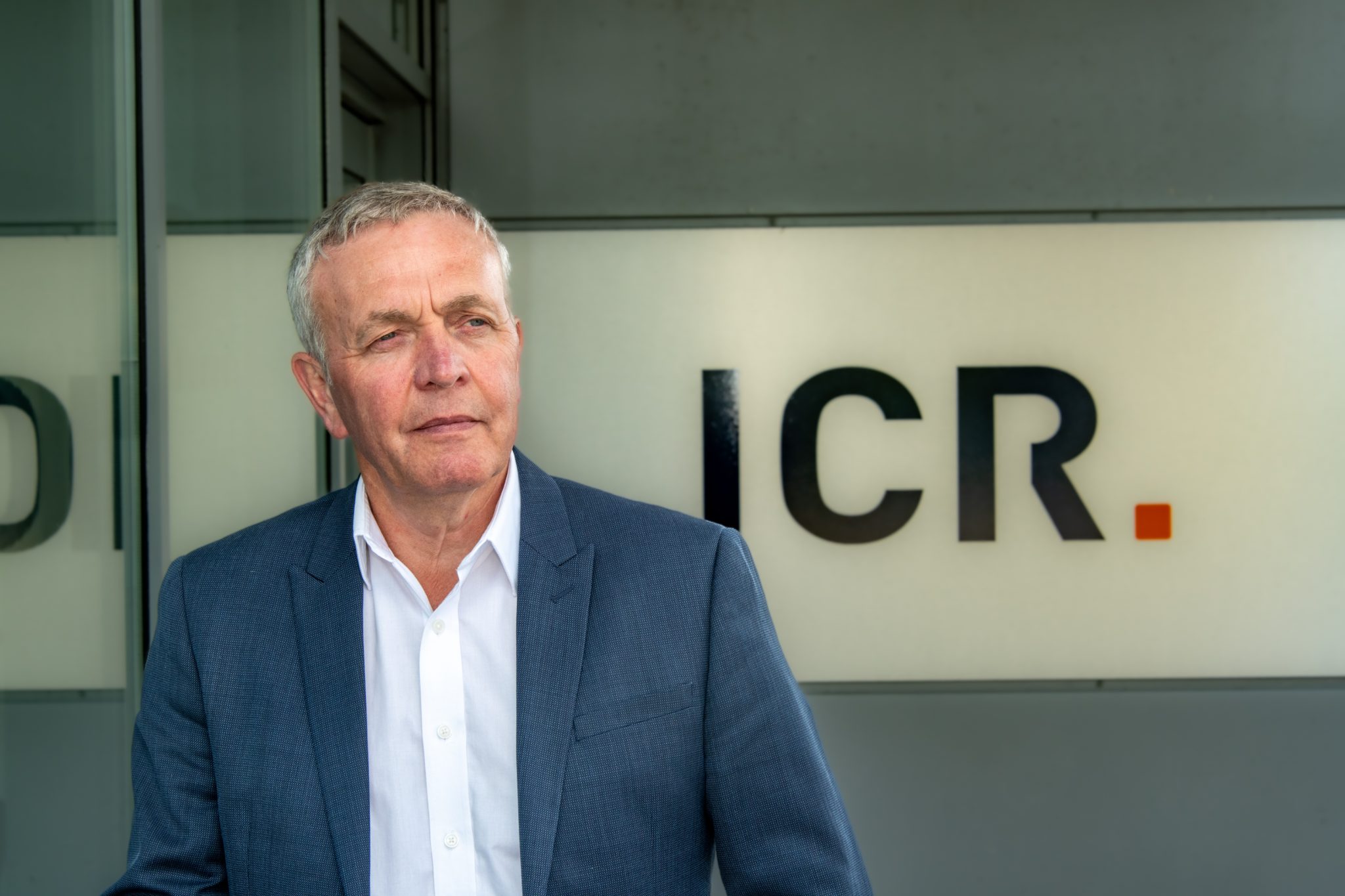
University of life stands Govan-raised engineer in good stead
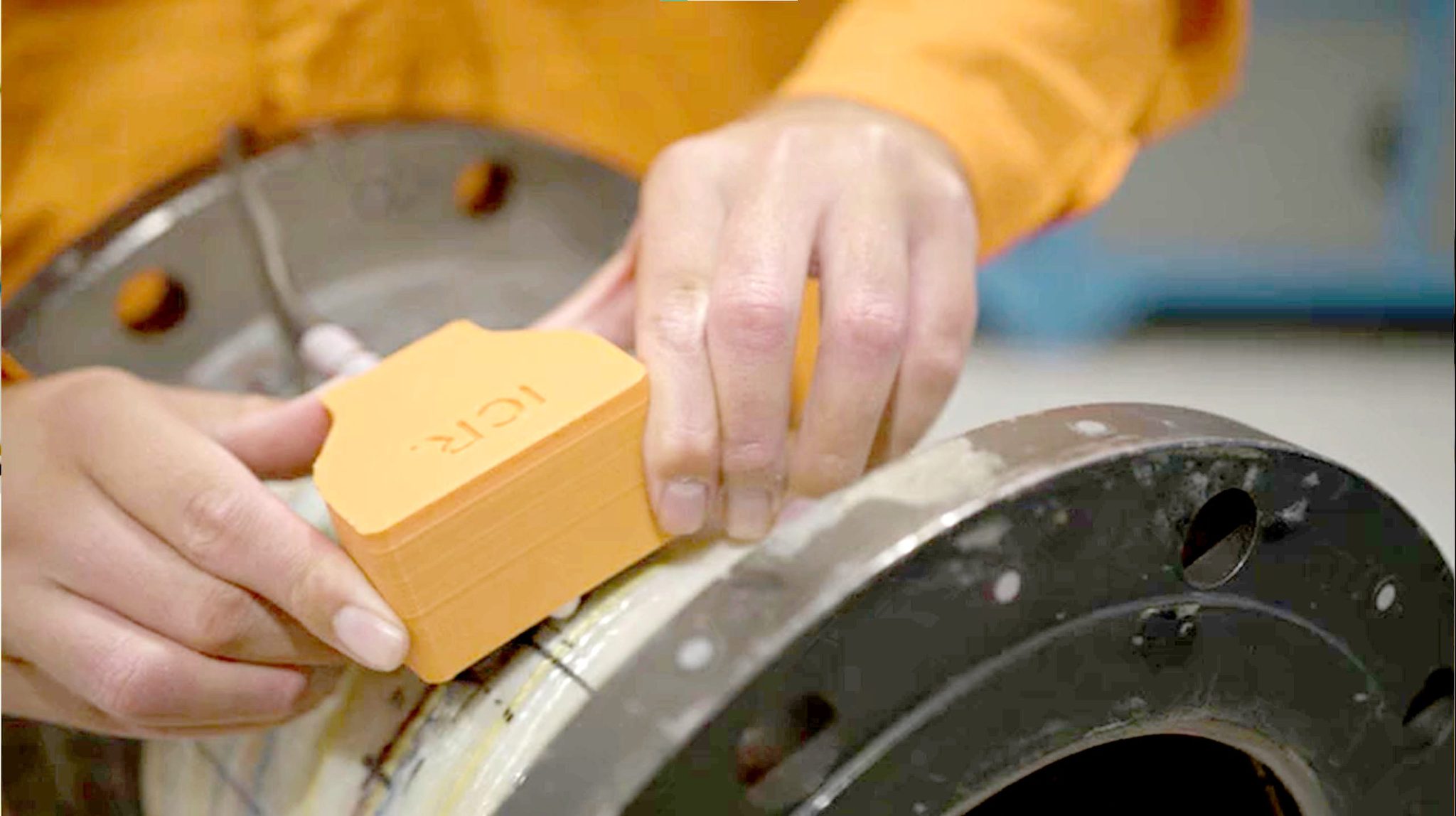
LR and UKAS boost for ICR Group’s INSONO innovation
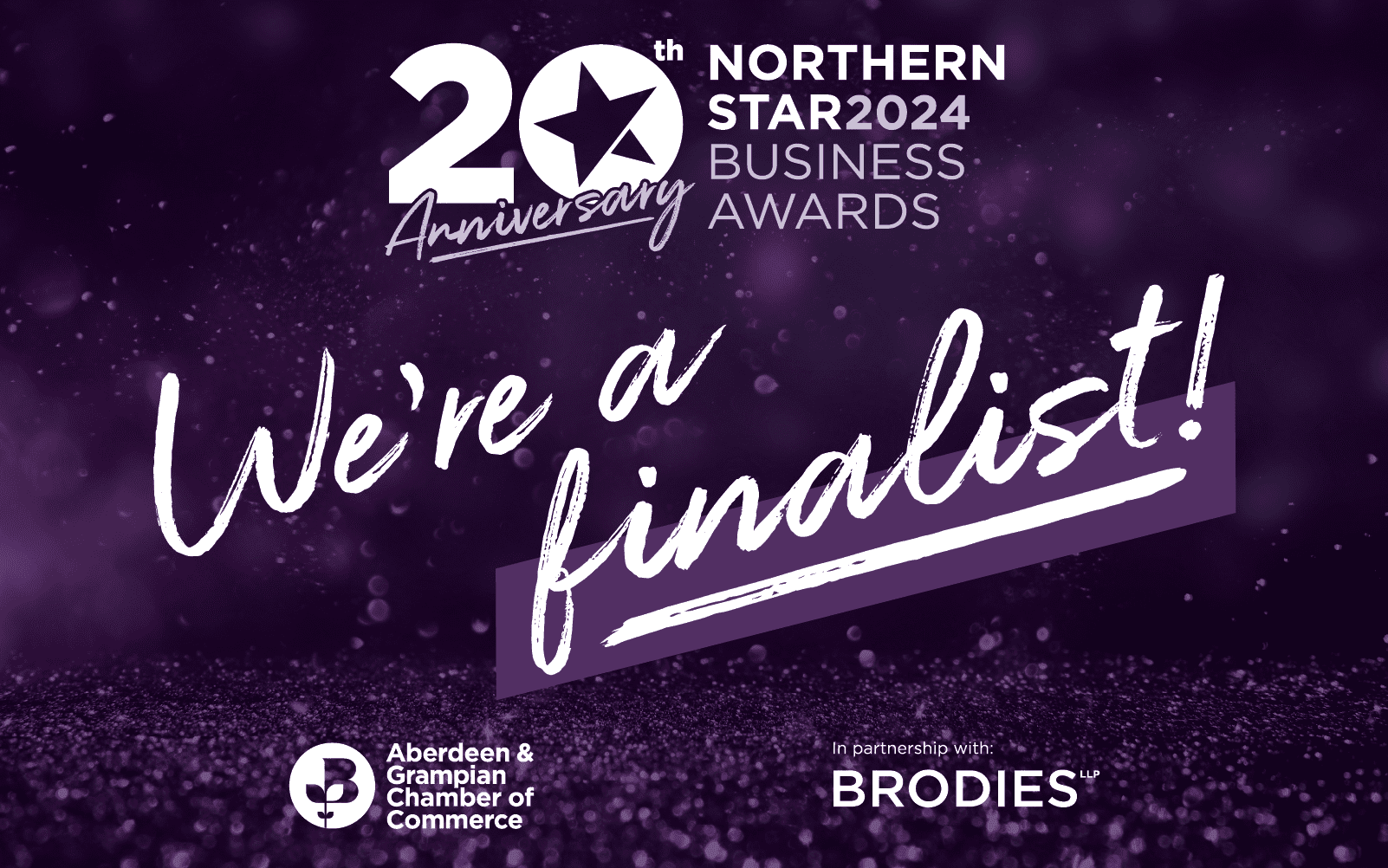