Client: Operator
Asset: Offshore asset
Location: Southern North Sea
Result: Two anomalies were identified and can be monitored over the design life of the repair
Client challenge
A major oil and gas producer approached us looking for continued assurance in the integrity of a pre-existing composite repair used in their infrastructure. They required a comprehensive visual inspection and non-intrusive inspection (NII) to assess the current condition of the repair wrap. The primary objective was to identify, quantify, and record any anomalies that could compromise the pressure-retaining capacity of the repair and substrate for inclusion in the framework of their Risk-Based Inspection (RBI)/Written Scheme of Examination (WSE).
What we did
Our team conducted a close visual inspection to evaluate the external condition of the repair wrap. Subsequently, we performed a non-intrusive examination using INSONO™, a technology that uses the principles of acoustic inspection to assess the entire volume of the composite wrap and substrate. This technique was chosen for its capability to detect anomalies in critical areas such as the bond line, interlaminar dis-bonds, and the steel substrate. The goal was to identify any features that could – if left unmonitored – impact the integrity and life cycle of the repair wrap and assess its suitability for continued use.
Results
The examination successfully located two delaminations (voids) within the wrap. Following a thorough technical assessment by the composite design team’s technical authority and fitness-for-service evaluation against defined acceptance criteria, it was determined that these anomalies likely occurred during the application of the wrap. Engineering assessments confirmed that these features had no detrimental significance to the integrity of the wrap repair.
As a result, the client’s Written Scheme of Examination (WSE) was updated in accordance with their Risk Based Inspection (RBI) process. The composite repair wrap was deemed fit for continued service, and a valid justification for extension was provided.
Conclusion
Our composite repair examination, played a crucial role in providing data driven justification for the continued classification of the composite repair as fit for service. The repeatability of this inspection method positions the client well for future life extensions, as potential concerns can be consistently addressed and mitigated. This case underscores the importance of advanced inspection techniques in ensuring the ongoing integrity and safety of critical infrastructure components in the oil and gas industry.
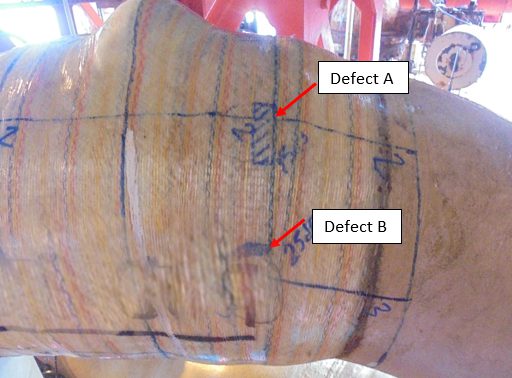
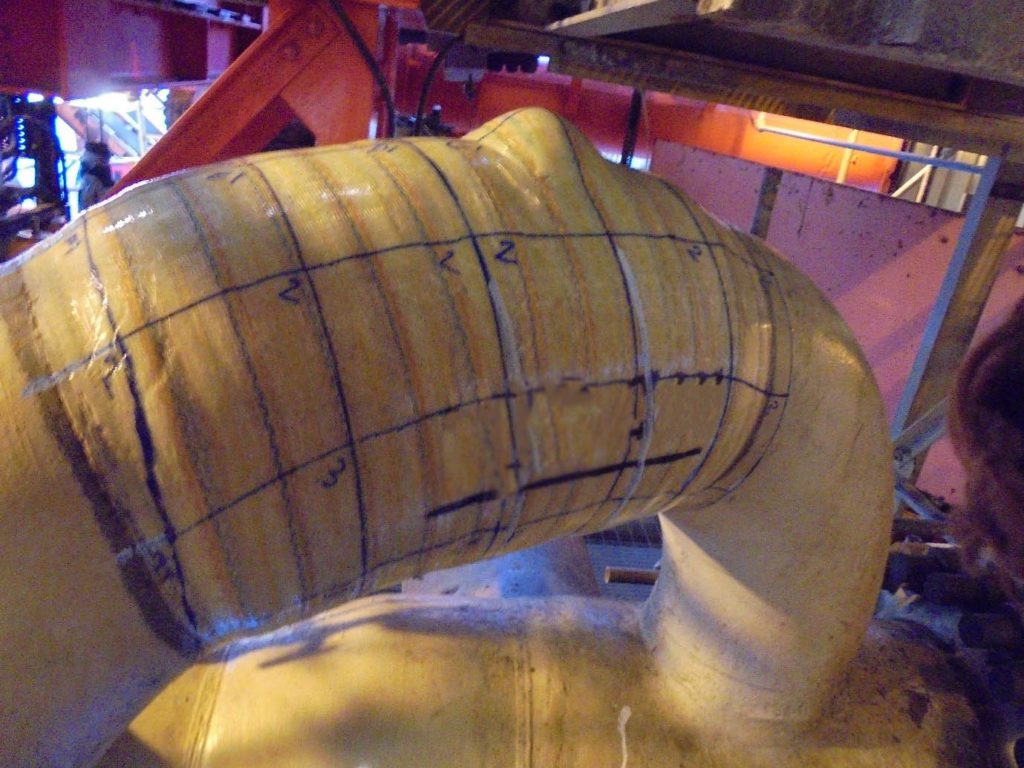
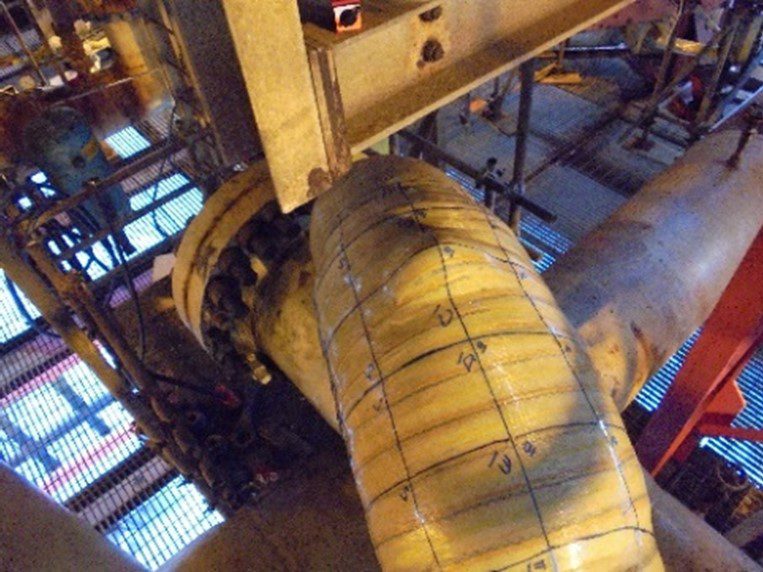
Featured articles
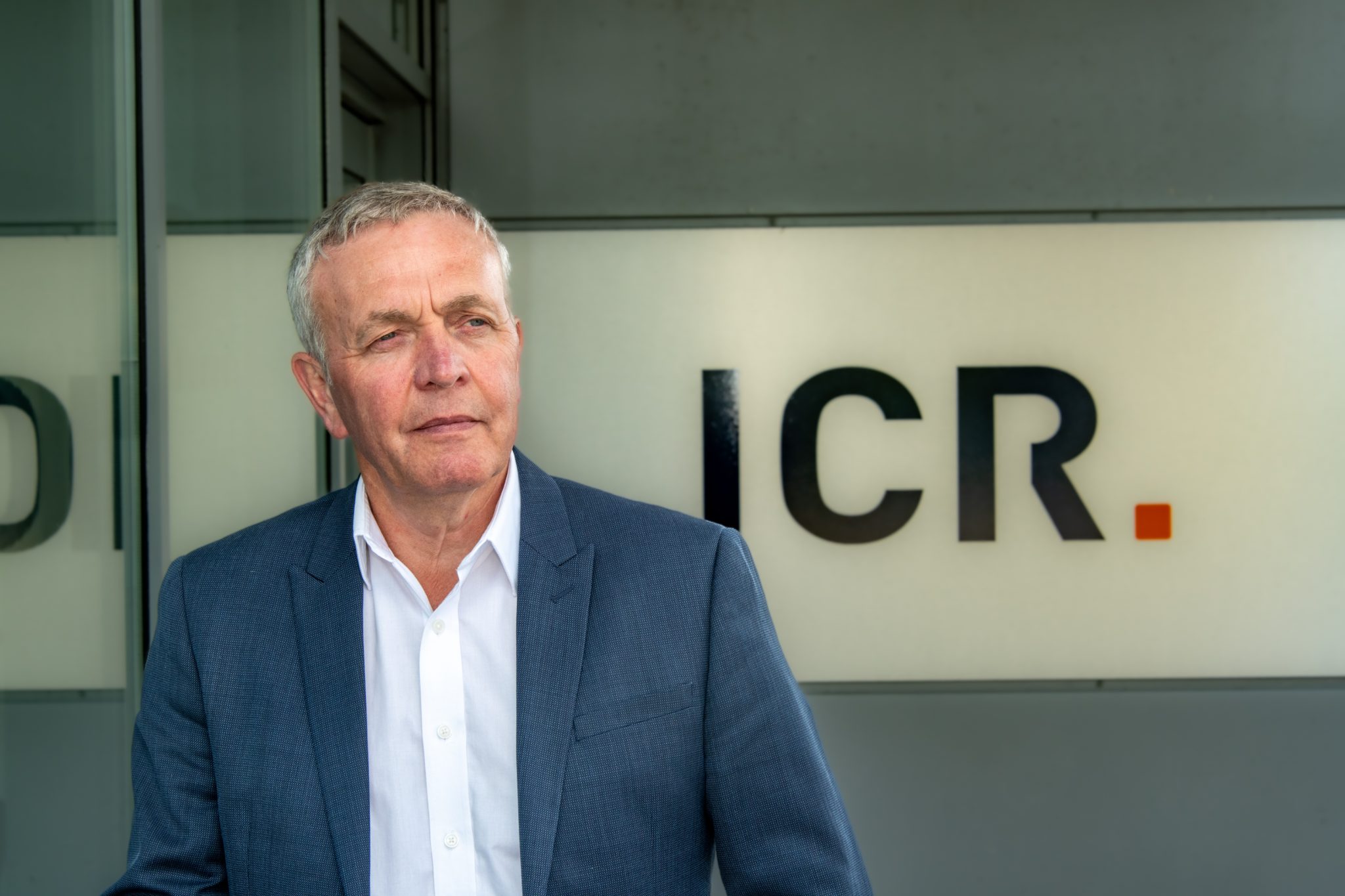
University of life stands Govan-raised engineer in good stead
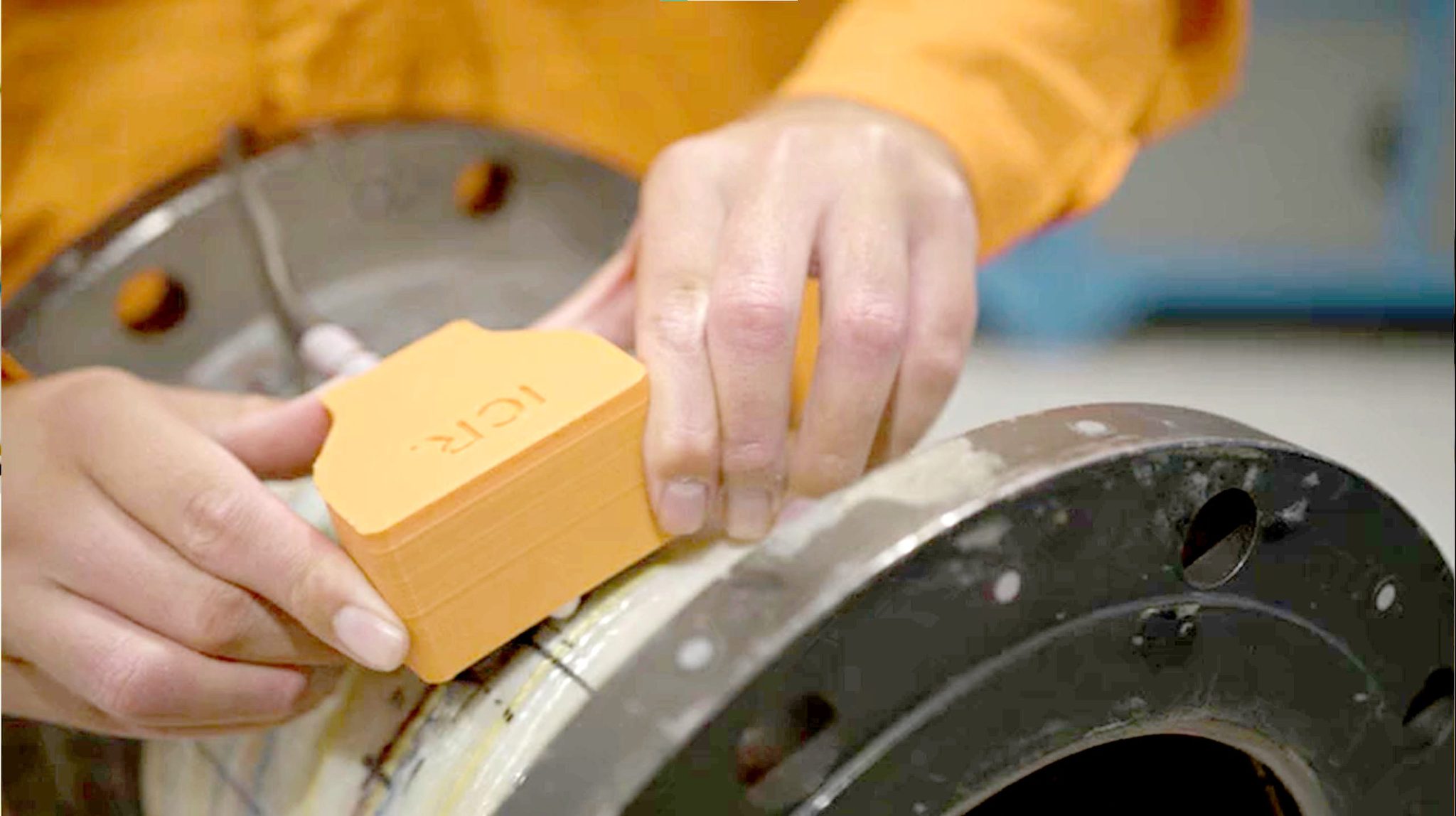
LR and UKAS boost for ICR Group’s INSONO innovation
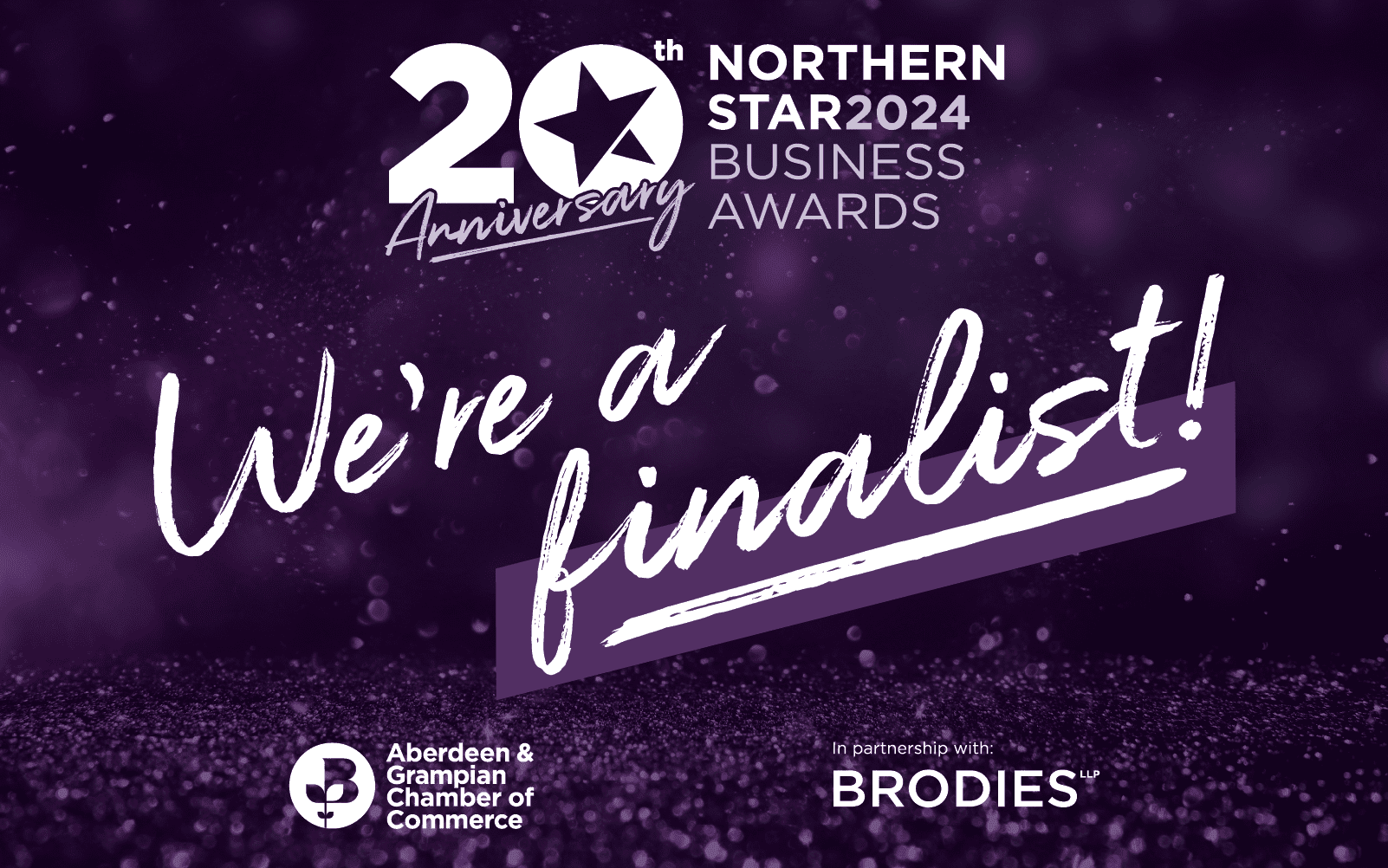