Client Challenge
Our client, an energy operator in Azerbaijan, faced the challenge of tying in new 6” & 8” carbon steel spools on the asset’s drill floor low-pressure mud lines. Traditional welding methods posed risks due to the presence of hydrocarbons, necessitating a cold-work solution to avoid hot work and mitigate associated hazards. Our client urgently required a reliable method to conduct the tie-ins without compromising safety, operational downtime, or incurring additional costs.
What We Did
In response to our client’s challenge, our weldless connector technology, Quickflange, was the preferred cold-work solution to facilitate the pipeline tie-ins. Quickflange’s innovative design eliminates the need for hot work, habitats, and associated safety risks, ensuring a safe and efficient repair process.
Collaborating with our partner, Khazar Engineering in Azerbaijan, our team mobilised equipment and trained technicians to execute the repair swiftly and effectively. Khazar’s trained technicians undertook line preparation, cold cutting of the pipe, and the installation of Quickflange connectors. Additionally, they provided essential support for the installation of the new spool tie-in sections, ensuring seamless integration with the existing pipeline infrastructure.
Results:
The implementation of Quickflange enabled a rapid turnaround for the client, addressing the repair needs on short notice without compromising operational efficiency. The elimination of hot work not only minimized downtime but also resulted in substantial cost savings compared to traditional welding methods.
With Quickflange, our client achieved a permanent repair solution that meets safety standards while optimizing operational resources and costs. The successful collaboration between ICR, Khazar Engineering, and the client highlights the effectiveness that Quickflange generates when addressing complex repair challenges in offshore environments.
Featured articles
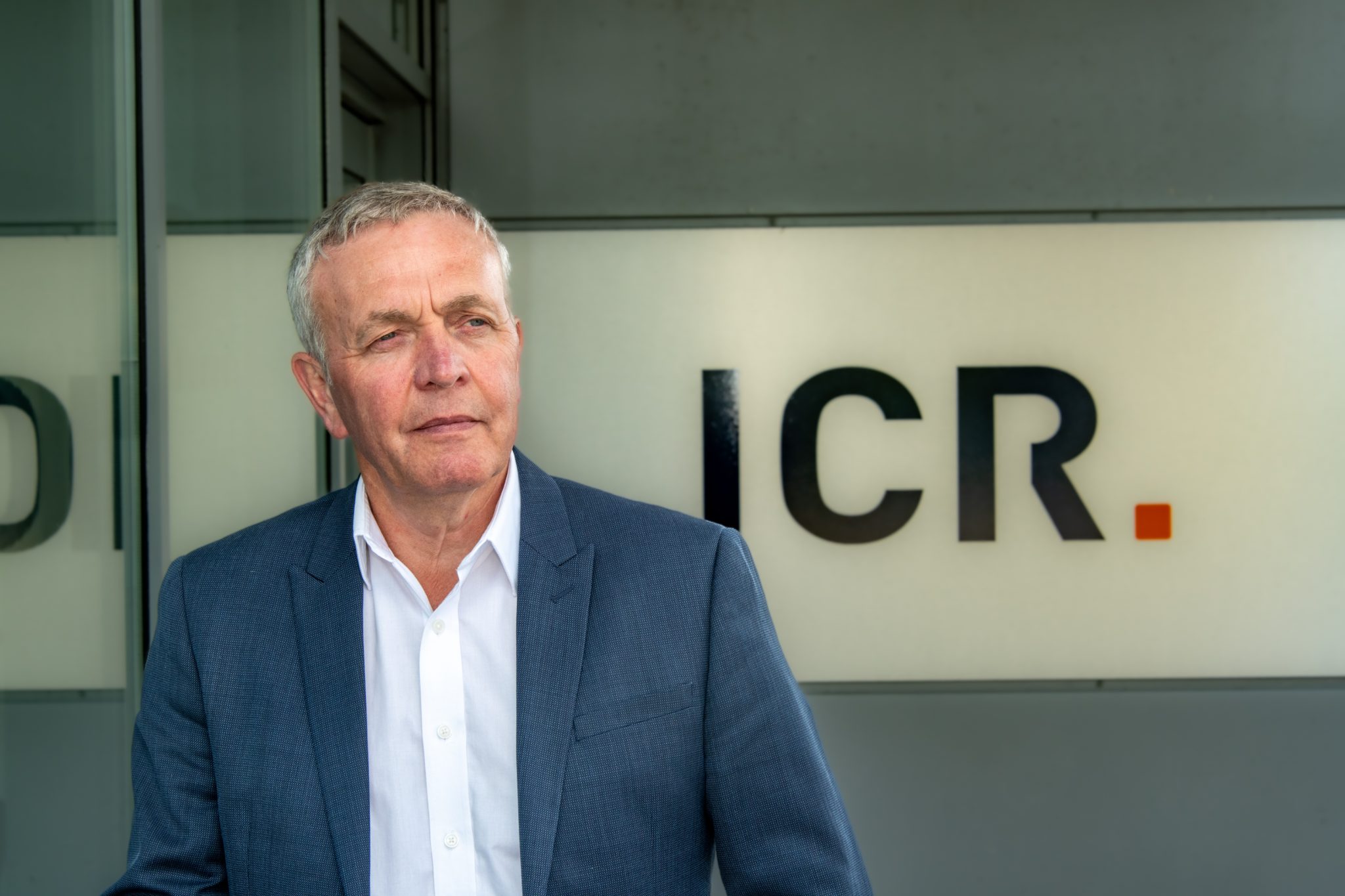
University of life stands Govan-raised engineer in good stead
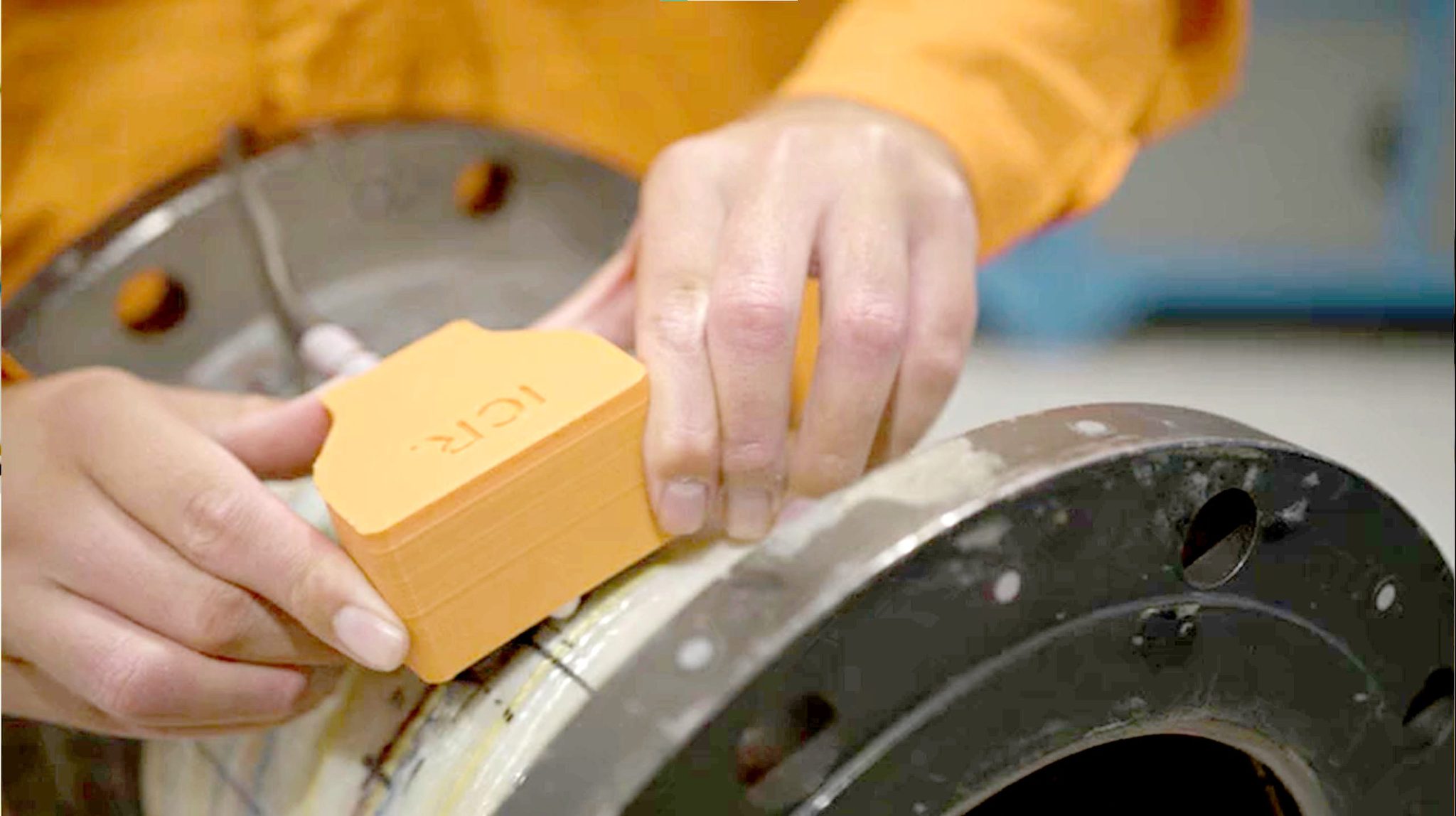
LR and UKAS boost for ICR Group’s INSONO innovation
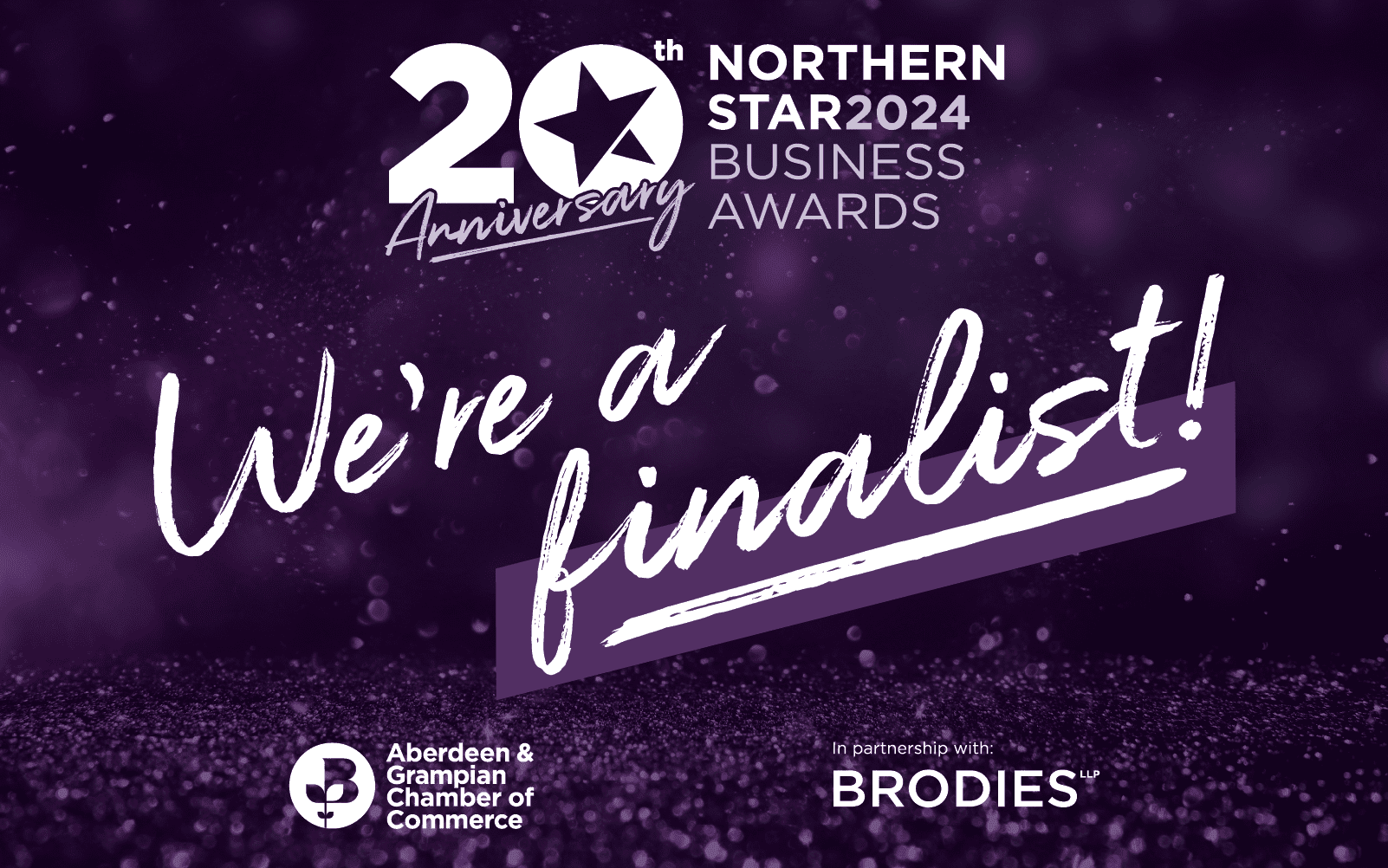