Client | Location |
---|---|
Major Middle East Operator | Oman |
Scope
An isolation joint (as part of the cathodic protection system) of a 36” pipeline was leaking through the internal sealing mechanism of the joint. It was not possible to isolate this joint so the repair had to be applied live. Therefore, one of the critical aspects of this repair application was the associated safety aspects of diverting the leaking gas from the joint while the repair was being applied.
Solution
The installation procedure for the clamp and composite repair consisted of the following steps;
1. Clean surface of joint and seal leak
2. Apply temporary clamp and gas diversion system
3. Prepare surface of pipeline
4. Apply composite repair
5. Perform QA/QC checks
The proposed solution involved first applying a temporary clamp over the leaking part of the joint and then applying a composite repair over the clamp to ensure longevity of the repair solution. ICR project managed the complete activity of this repair including surface preparation, clamp design and installation and composite repair design and installation.
The repair design was performed according to ISO/TS 24817. Due to live nature of the repair, the repair design was split into two parts. The first part involved the design of a temporary clamp and gas diversion system. The second part was the design of the composite repair to ensure the leak sealing capability of the repair. The solution was 15 layers of Technowrap™ 2K in the form of a fully circumferential wrap over the temporary clamp and extending along the axial length of the pipeline beyond the clamp by 300 mm.
Results & Benefits
- The application of the Technowrap™ 2K HA went as planned and without delays
- The repair was designed with a lifetime of 5 years.
- Repair was applied whilst line was live, meaning no shut down for client
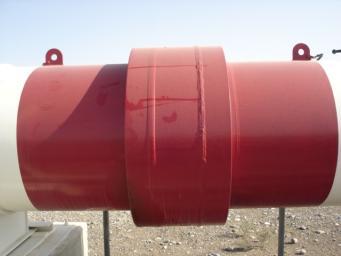
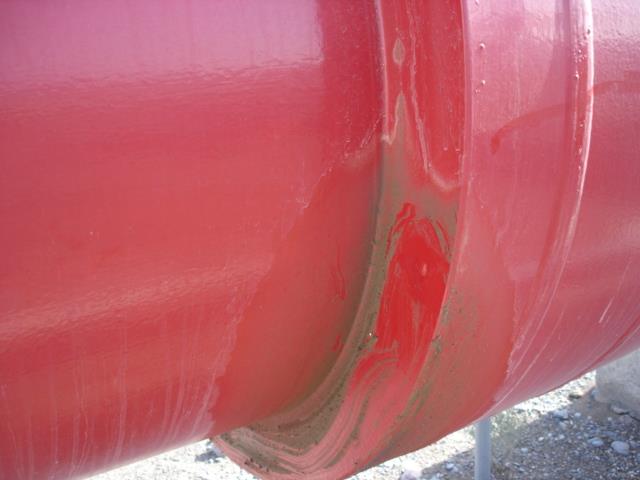
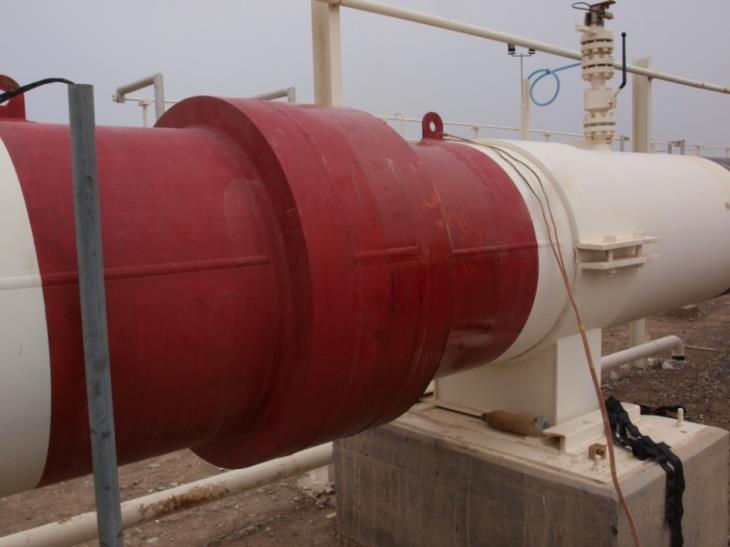
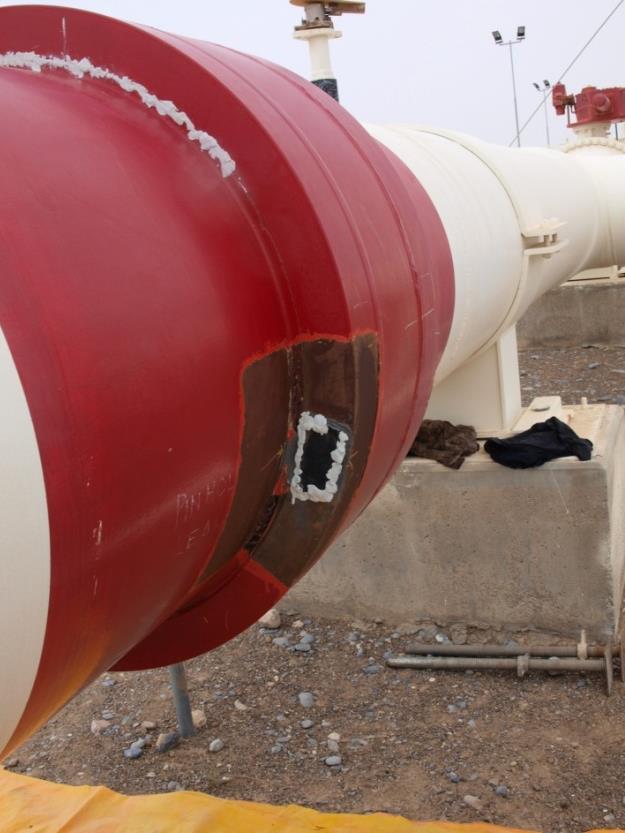
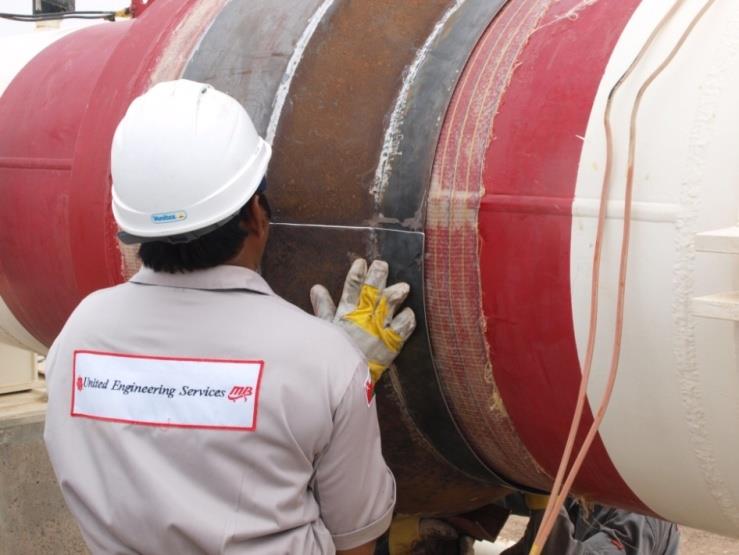
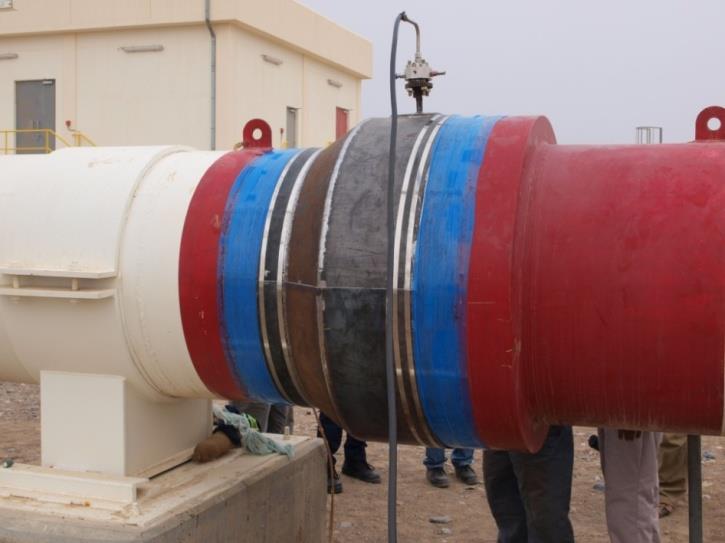
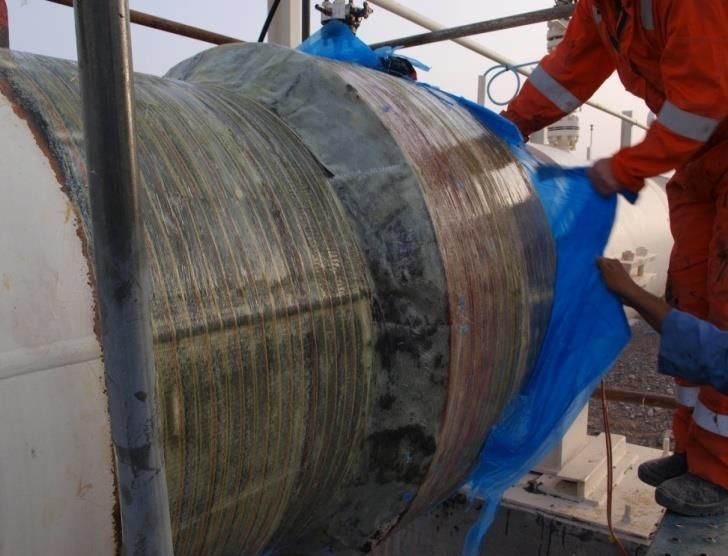
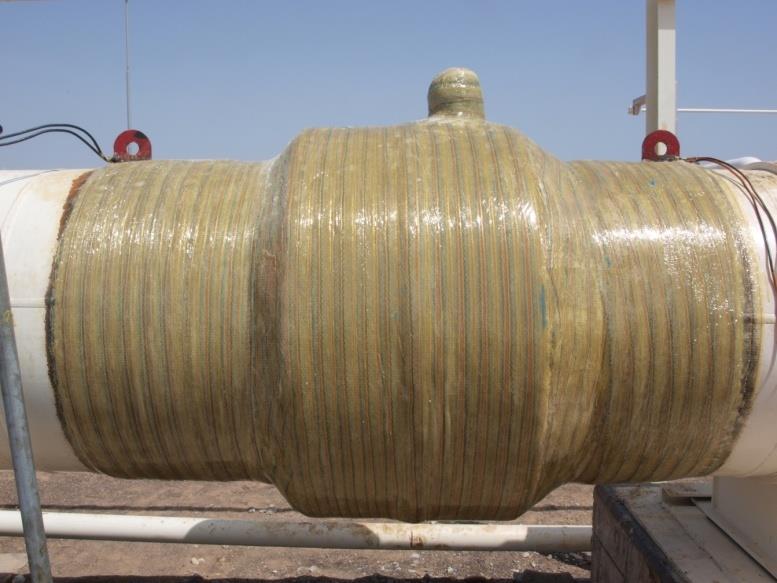
Featured articles
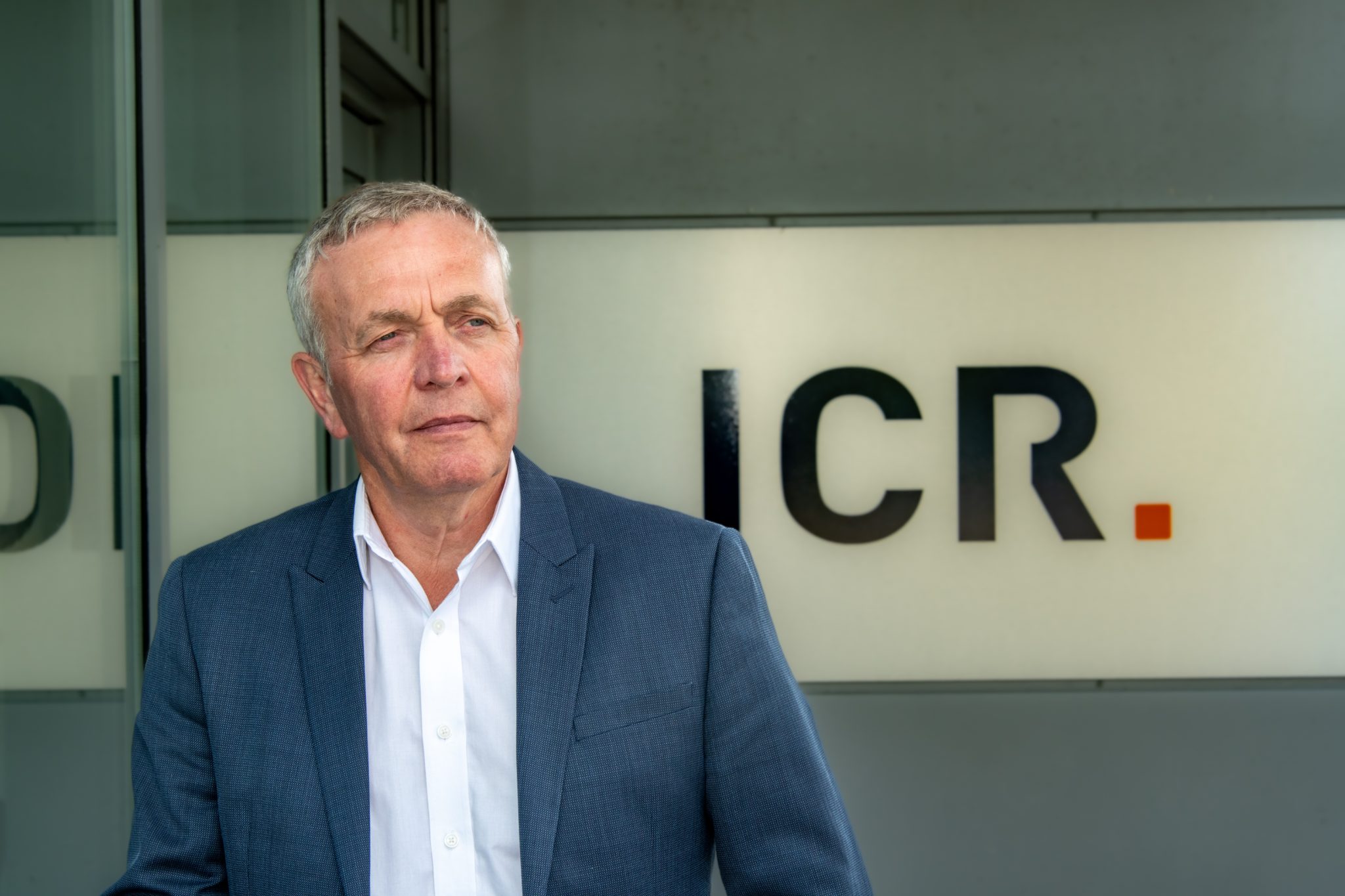
University of life stands Govan-raised engineer in good stead
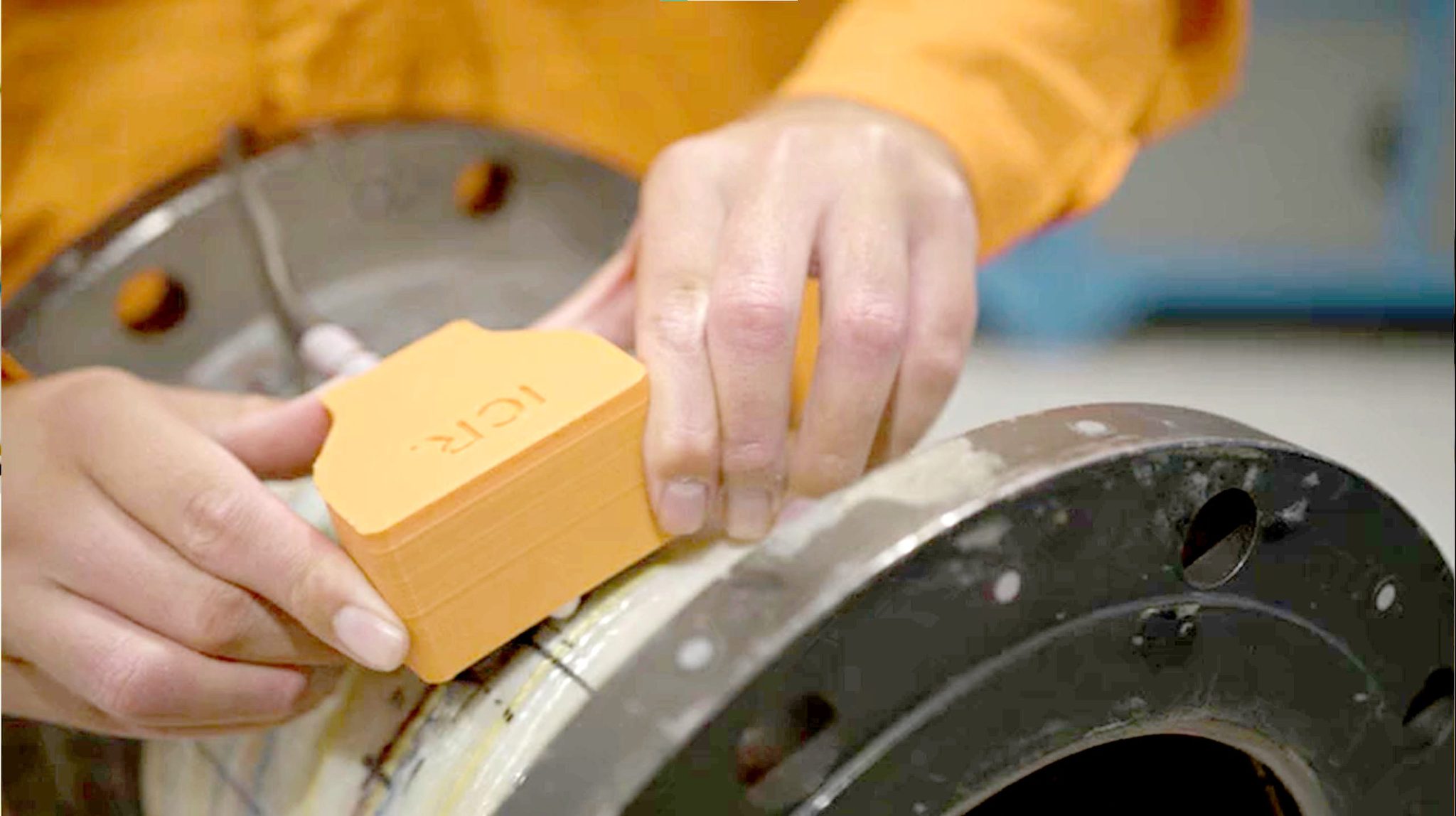
LR and UKAS boost for ICR Group’s INSONO innovation
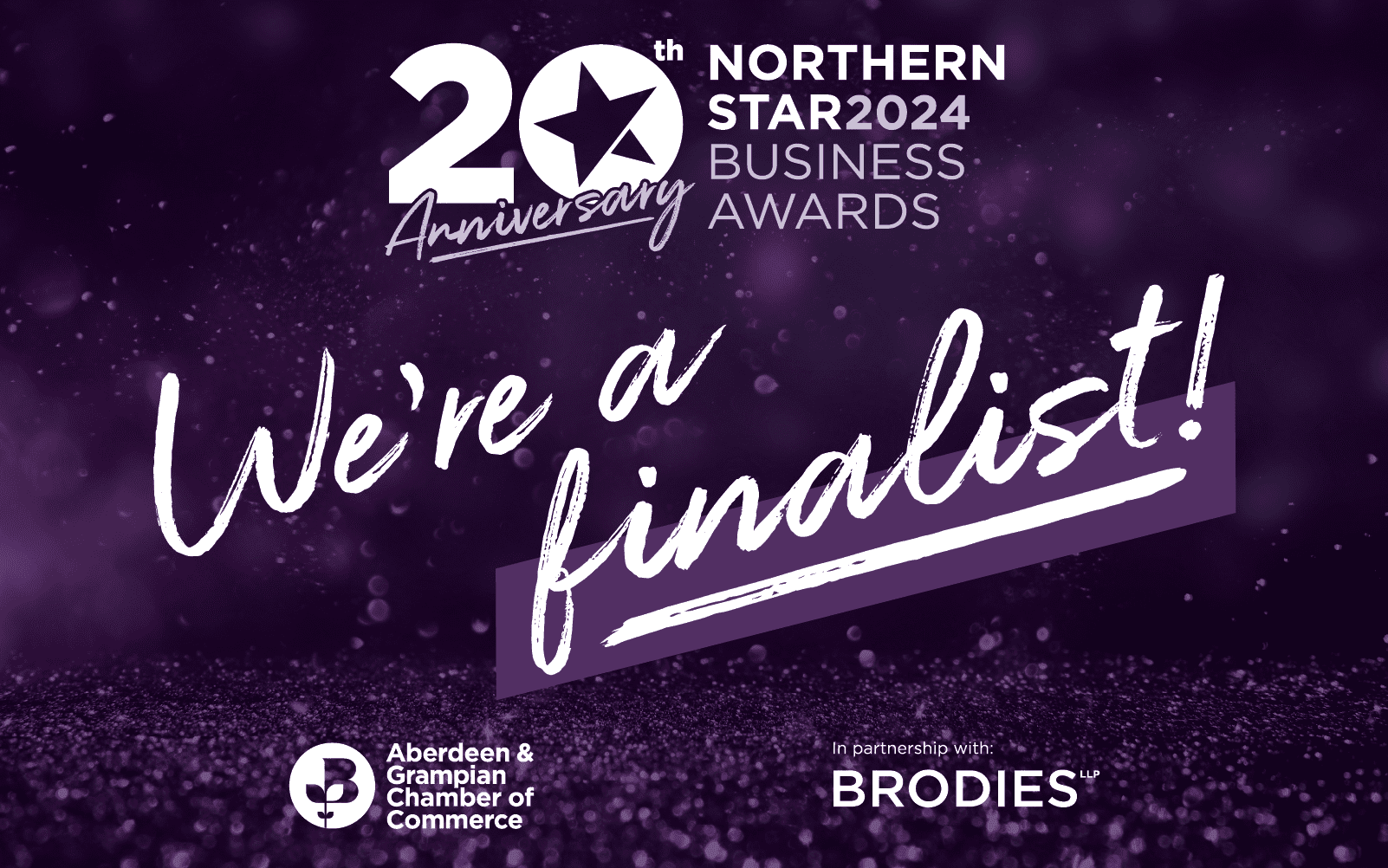