The Middle East offers significant opportunities for innovation-driven companies like ICR Group, making it central to our growth strategy due to rising demand for our products and services.
We have completed numerous high-value projects in the region, including the UAE, Oman, Qatar, and Kuwait, strengthening our presence through formal partnerships and upcoming collaboration agreements.
The ADIPEC Exhibition has been instrumental in accelerating our market development, providing a platform to highlight our solutions and engage with potential clients.
Our technology- driven products, such as the composite repair technology Technowrap, the INSONO non-destructive testing (NDT) technique, and the Quickflange weldless connectors, have proven effective in the region, supporting clients’ infrastructure integrity and net-zero goals.
- In Kuwait, Technowrap 2K repaired a live 30” crude oil pipeline without downtime, surpassing a previous ineffective clamp-based method.
- In Oman, Technowrap 2K restored a 36” pipeline header system suffering from internal erosion and corrosion, ensuring leak-sealing and strength restoration. A significant defect in a 48” crude oil pipeline was repaired using Technowrap 2K, executed by trained air divers within 10 days, resulting in substantial cost savings and minimal production disruption.
- In Qatar, Technowrap 2K was trialled as a corrosion protection system on subsea pipelines, demonstrating time and cost savings and an extended service life.
- In Oman, Quickflange technology provided weldless connections for several tie-in points, with over 20 connectors installed ahead of schedule, yielding cost savings, and eliminating hot work.
These successful solutions have led to long-term agreements with operators in the Middle East. Continued collaboration with our partner network will further build our reputation and support ongoing growth in the region.
OGV Energy magazine put the spotlight on Technowrap™ – a remarkable ICR product used worldwide by clients.
ICR Group continues to redefine asset integrity with its revolutionary Technowrap™ product.
This repair solution is specifically designed to significantly enhance operational efficiency and sustainability, while minimising downtime and environmental impacts.
By harnessing the strength of glass or carbon fibre stitched cloths paired with two-part epoxy resins, Technowrap™ rehabilitates damaged pipework, pipelines and structural components across various scenarios.
ICR’s comprehensive in-house approach encompasses engineering, material provision, technician training and installation, ensuring quality and reliability.
The versatility of Technowrap™ is evident in its broad range of applications, from pressurised systems and pipelines to structural repairs of tanks, vessels, caissons, risers and even underwater environments. It offers a cost-effective alternative to steel replacement, enabling repairs to be conducted without the need for operational shutdowns.
Repairs can last for up to 20 years. Moreover, Technowrap™ can contribute to environmental sustainability by offering a 66% reduction in carbon emissions compared to traditional replacement methods.
Ewan Robertson, Global Composite Repair Director at ICR, said: “Technowrap™ is the ideal product for assets to keep in their toolbox to cover a myriad of maintenance and repair applications for pipework and infrastructure. This technique has now had a 30-year track record in the industry and can provide further advantages from a sustainability and efficiency perspective.”
The ICR portfolio also boasts INSONO™, an innovative non-destructive testing (NDT) technique for inspecting engineered composite repairs.
Furthermore, ICR’s online leak sealing solutions provide tailored, in-house engineered clamps and repairs designed to tackle specific leaks in operational systems.
Quickflange™ offers another remarkable solution within ICR’s arsenal, delivering weldless, high-performance flange-to-pipe connections that improve pipeline integrity and flow assurance. This is a permanent, efficient repair option, yielding up to 80% time savings and a 57% reduction in greenhouse gas emissions compared to traditional welding methods.
ICR’s machining and bolting capability brings extensive experience to a wide range of industrial sectors. Meanwhile, the firm’s drone division, Sky-Futures, delivers inspection reports and supported an operator by measuring methane emissions at four platforms in the North Sea.
This article first appeared in OGV Energy magazine’s asset integrity issue.
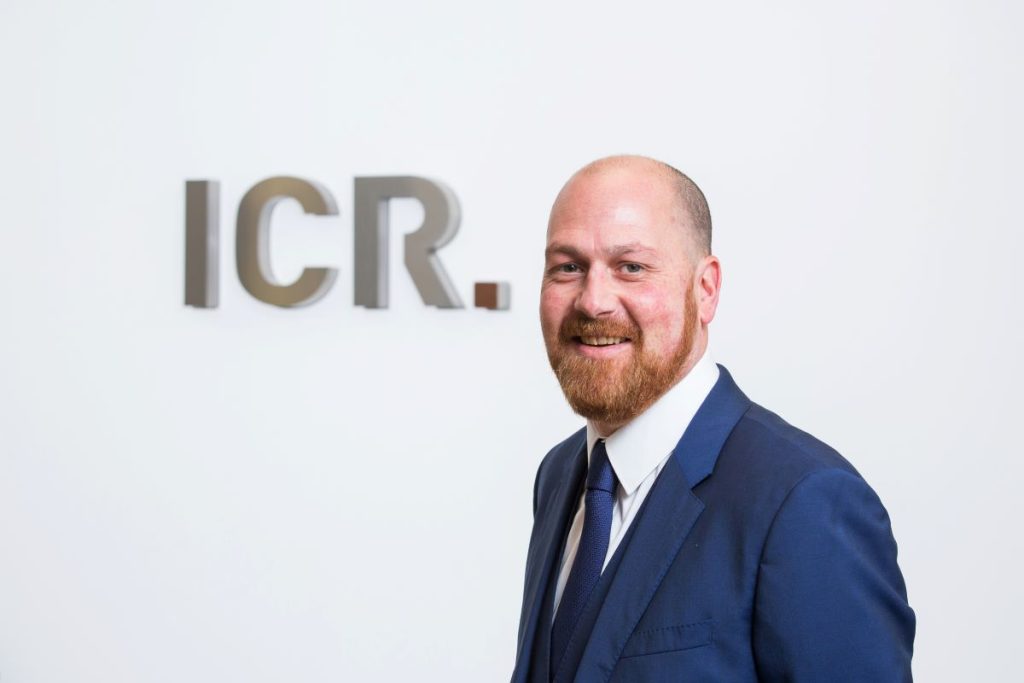