ICR Group has announced a strategic partnership with Wellube, a Unique Group company, to expand the reach of its bespoke technology solutions in the Middle East and India.
This collaboration aims to introduce ICR’s advanced products – including the Technowrap composite repair system, Quickflange weldless connections, and INSONO non-intrusive inspection technology to new markets. Wellube becomes the latest partner as ICR seeks to strengthen its global presence.
Wellube has been providing cutting-edge bespoke services to the oil and gas, renewables, power, petrochemical and infrastructure industries for over 20 years. Renowned for its engineering solutions the team brings a wealth of market presence and industry knowledge to the partnership.
Jim Beveridge, Chief Executive at ICR Group, said, “Welcoming Wellube into the ICR partner network is a significant milestone in our mission to deliver cutting-edge integrity solutions worldwide. Wellube’s strong presence in the Middle Eastern and Indian markets is ideal for the introduction our advanced technologies into new sectors and to new customers.”
Garry Kidd, Managing Director at Wellube, said: “This collaboration unites our long-standing market presence and deep understanding of the industrial landscape with ICR’s innovative solutions. We are committed to delivering unparalleled services, and the use of Technowrap, Quickflange, and INSONO will enhance our provision of turnkey solutions for our clients from start to finish.”
The partnership highlights both companies’ commitment to enhancing asset maintenance solutions. By combining Wellube’s client base with ICR’s innovative and bespoke product range, the collaboration promises to deliver a comprehensive suite of services.
ICR’s dedication to innovation is demonstrated though one of the core products, Technowrap – an engineered composite repair system. It’s a versatile long-term alternative to steel replacement that offers practical, cost-effective rehabilitation and minimal disruption to operations. Technowrap has been utilised extensively by major operators in the Middle East for applications ranging from pipework and pipelines to structures as well as significant subsea composite repair projects. The defined life repair technology for damaged pipework can be engineered to last up to 20 years providing both immediate and long-term benefits.
Further to this, INSONO, a non-intrusive composite inspection technique complements the Technowrap range. It has been developed to validate the condition and integrity of composite repairs providing operators with assurance in the application and long-term performance. The technology can detect anomalies in the bond line and interlaminar dis-bonds within composite repair material and, thereby, support and underpin asset written schemes of examination.
Quickflange, a high-performance weldless flange-to-pipe connector, is another core offering that addresses scenarios where traditional welding solutions are impractical due hot work constraints or time limitations. The innovation enhances operational safety and efficiency. Over the past 20 years, Quickflange has built up a global track record of providing rapid and safe installations generating cost efficiencies and an 80% time saving over traditional welding methods. ICR had a global network of more than 25 partners.
Introduction
As the energy infrastructure landscape in the United States undergoes transformation, the demand for innovative solutions that enhance efficiency, safety, and regulatory compliance has never been more pronounced. Quickflange weldless connectors offer substantial advantages over traditional welding and replacement methods. This thought leadership piece aims to highlight the benefits of Quickflange weldless connectors in the US market, emphasising regulatory approval and the transformative impact on pressure systems integrity and maintenance.
Regulatory Approval
The USA’s stringent regulatory environment places a premium on safety in all industrial operations, and Quickflange has successfully navigated this. With case-by-case installation approvals from regulatory bodies including Bureau of Safety and Environmental Enforcement (BSEE), attesting to its use as a permanent repair method, these connectors have become a trusted choice for maintenance projects. This regulatory endorsement for connectors up to 14” NPS, provides confidence to operators, ensuring that they are adopting solutions aligned with the highest safety standards.
Mitigating Risks
The inherently safer nature of Quickflange aligns seamlessly with the risk mitigation priorities outlined by regulatory authorities. By eliminating the need for hot work and reducing the potential for accidents associated with traditional welding, these connectors contribute to a safer working environment. This not only safeguards personnel but also protects the integrity of the surrounding infrastructure.
Accelerating Project Timelines
In a sector where project timelines are critical, Quickflange stands out by streamlining installation and maintenance processes. The compact design of these connectors allows for rapid installation, significantly reducing downtime. With regulatory approval validating its reliability, operators can confidently implement the connectors to accelerate project timelines whilst dramatically improving the safety aspect, without compromising on the quality requirements.
Cost-Effective Regulatory Compliance
Quickflange not only fulfils regulatory standards but also provides a cost-effective alternative to traditional welding. The reduced downtime, minimised risk of accidents, and streamlined compliance processes contribute to long-term cost savings. Further to this the reduced labour requirements and costs associated with these connectors contribute to an overall more economical solution, thus allowing operators to allocate resources more strategically, optimising their budget for sustained operations.
Environmental Benefits
Quickflange also offers several environmental benefits compared to traditional welding methods, contributing to a more sustainable approach to maintenance. These benefits include reduced emissions, minimised waste generation, enhanced environmental compliance, and long-term sustainability. These advantages align with the growing global emphasis on sustainable practices.
Conclusion
Quickflange has not only earned its place as an innovative technology but has successfully navigated the regulatory landscape in the USA. As the energy industry continues to evolve, these connectors offer a safer, more efficient, and economically viable alternative to traditional welding methods. By aligning with regulatory standards, operators can not only meet compliance requirements but also pave the way for a future where pressure systems integrity is synonymous with innovation and safety.
ICR Group has secured another partnership agreement in Africa.
The collaboration with South Africa-based SGB-Cape, a leading industrial services provider, broadens the scope of ICR’s innovative products, including the Technowrap™ composite repair system and Quickflange™ weldless connections.
Scott Byers, Head of Business Development, Africa, at ICR, said: “Welcoming SGB-Cape into the ICR partner network marks another significant step in our mission to deliver cutting-edge integrity solutions worldwide. Their strong presence across the African market is ideal for the rapid introduction of our advanced technologies into new sectors, locations and customers. We are delighted to extend our reach by adding to our African partner network.”
Ben Garrad, Managing Director of SGB-Cape, said: “The collaboration is a perfect synergy, uniting SGB-Cape’s longstanding market presence and profound understanding of the African industrial landscape with ICR’s innovative solutions and international insights. SGB-Cape will serve as a key partner of ICR, solidifying its commitment to delivering unparalleled industrial services solutions.”
The alliance is a testament to both companies’ commitment to enhancing asset integrity management, corrosion protection and inspection services in Africa. It combines SGB-Cape’s 75 years of industry experience with ICR’s innovative solutions, promising to deliver a comprehensive suite of services to meet the unique challenges of the African market.
SGB-Cape, a leading provider of industrial services across Africa, specialises in asset integrity, corrosion protection and inspection solutions.
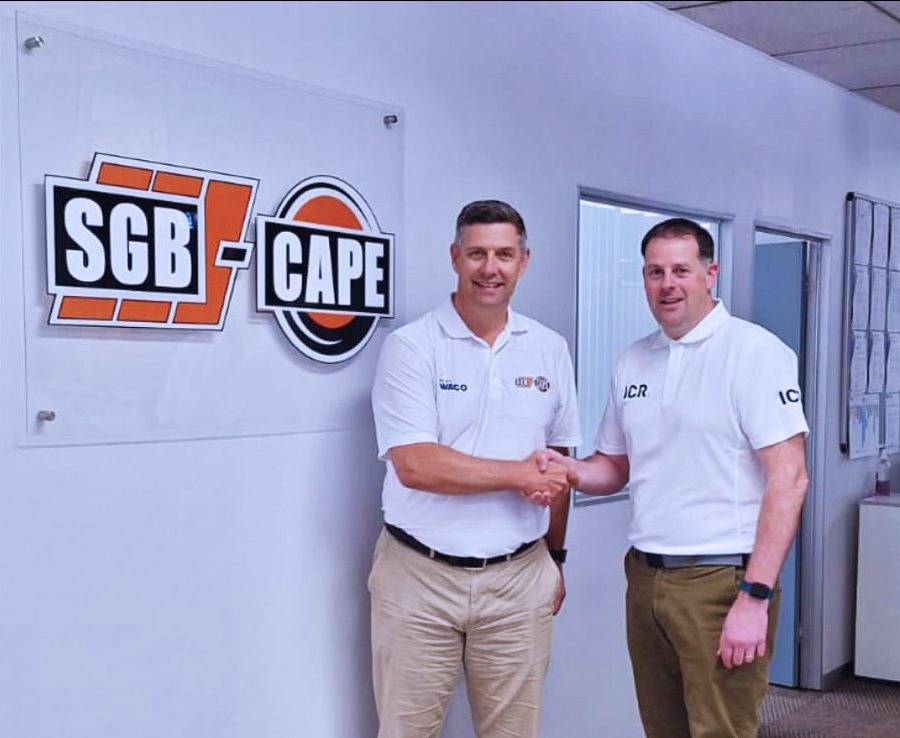
Today we put the spotlight on our North-west of England technical base
ICR’s Carnforth operation is on course to increase its contribution to the overall turnover figure of the company this year.
The hub is the group’s base for on-site machining, hydraulic bolt tensioning, leak sealing, Quickflange and Technowrap.
ICR has invested in new equipment and training at Carnforth, where additional technical and sales staff have been added. The team at the base has risen from 42 to 60 in the past year.
Carnforth’s status within ICR has been further underpinned after the group secured a four-year extension to a major contract for specialist onsite machining projects at a large engineering facility in the North-west. Work has also been secured in the energy, nuclear, government and defence sectors, across projects including flange management, controlled bolting, machining, leak sealing and composite repairs.
Darryl Dixon, General Manager of ICR at Carnforth, said: “We have a clear vision of our mission, which in turn cascades outwards so our customers know what it is ICR stands for and what we will deliver: right first time, innovation, safety and reliability.
“Our ongoing success reflects a genuine team effort at our Carnforth base, alongside collaboration with wider ICR operations and the support of senior management. We’ve invested significantly in facilities, equipment and people to ensure that knowledge and training from our existing technicians is shared across our wider pool of new talent.
“We already have exceptional subject matter experts, from design engineers to product-specific technical authorities, and our on-site technicians do great work every day in delivering our products and services on behalf of clients. Our goal now is to capitalise on all those resources, capabilities, and experience to realise further growth – not least in new markets such as renewables.”
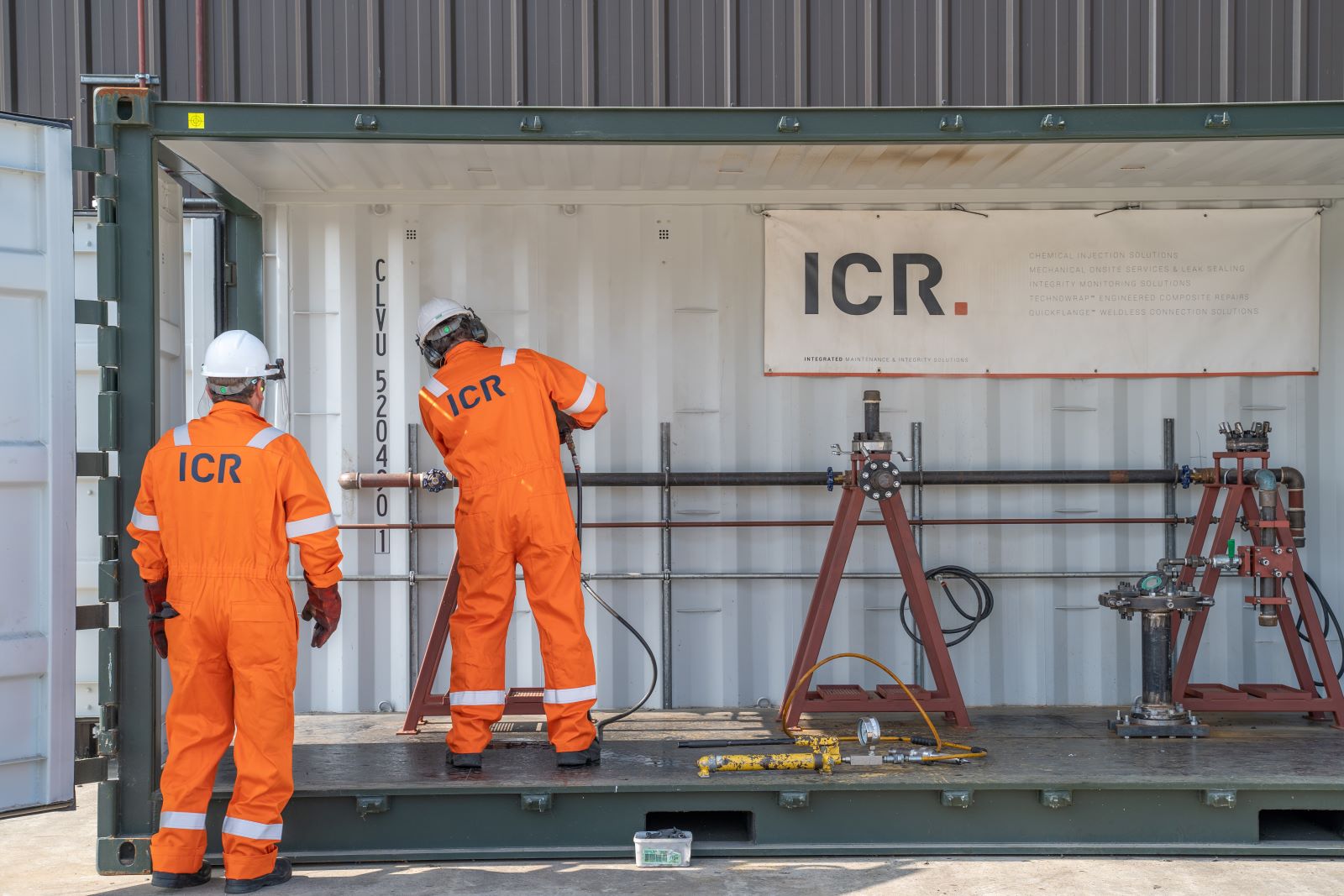
This article appeared in the Herald Newspaper on Monday 29 January 2024
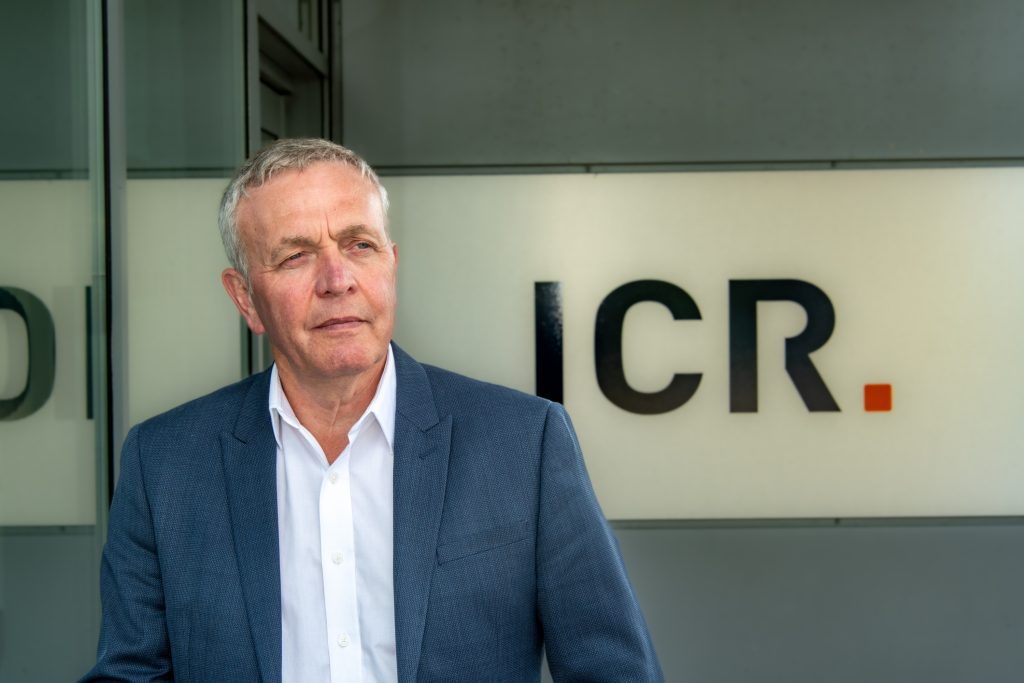
Glasgow-born Jim Beveridge is the chief executive officer at ICR Group.
With its headquarters in Aberdeen, ICR is a global technology-focused provider of specialist maintenance, inspection and integrity solutions across multiple industrial sectors. The firm recorded a 20% rise in turnover for its latest financial year and it expects to exceed that figure this year.
ICR supports clients with their asset integrity challenges, reducing time and costs. It also has a ‘drones’ division, Sky-Futures, a worldwide leader in unmanned aircraft and remote sensing operations. This part of the business plays a key role in addressing issues related to emissions.
Demonstrating a robust commitment to sustainability, ICR employs pioneering techniques that significantly contribute to the net zero goals of its clients.
What is your business called?
ICR Group.
Where is it based?
Aberdeen, Carnforth, Hemel Hempstead, Stavanger (Norway), Houston (USA), Abu Dhabi (Middle East), Perth (Australia). ICR has partnership agreements in 25 countries, where we train the local workforce to deliver engineering projects. This helps to reduce the carbon footprint.
What does it produce/do?
ICR specialises in cutting-edge maintenance, inspection and integrity solutions. We are playing our part in the transition to a lower carbon future across multiple industries and international markets.
For example, Technowrap provides life-long repairs that can be applied to internal, external and through-wall defects on complex geometries, while INSONO is an unique NDT (non-destructive testing) technique for the inspection of engineered composite repairs. The Technowrap repair system reduces emissions by 66% compared to the traditional replacement methods.
To whom does it sell?
Clients from a broad range of sectors count on ICR to support engineering projects. These include oil & gas, renewables, defence, nuclear, telecommunications, process industries, utilities and infrastructure and other markets.
What is its turnover?
Turnover for our 2022-23 year-end was £41.7m – a 20% increase on the previous financial year. The aim is to hit £50m in 2024 and I’m confident we will achieve this.
How many employees?
268. We’re looking to add to the team.
Why did you take the plunge?
The chance to create long-term sustainable jobs and to continue to grow a business across an international footprint was an extremely attractive proposition. The CEO role at ICR was an opportunity to put my own stamp on things, and lead from the front. I was previously with a global engineering and consulting business with more than 35,000 employees.
What were you doing before?
Senior vice-president, Asia Pacific Central at Wood plc. I enjoyed my 19 years with them. I joined ICR as CEO in April, 2022. It’s been an interesting career journey since growing up in Govan.
What do you least enjoy?
Jet lag. The novelty of long-distance travel wore off a long time ago!
What are your ambitions for the firm?
It’s vital we continue to be a sustainable business. We are diversifying into new sectors and continually looking at new opportunities. The aim is to create long-term jobs and significantly grow revenue and profitability year-on-year. As well as organic growth, we are also looking to expand through acquisitions.
What single thing would most help?
Continued product development is key. We must always be a forward-thinking company – one able to move with the times and not be reliant on one region, product or industrial sector. For example, we are working with Robert Gordon University on a number of innovative solutions.
What is the most valuable lesson you have learned?
You can’t stand still in business, you need to keep looking to improve. As Albert Einstein said: “Insanity is doing the same thing over and over again and expecting different results.’”
You’ve got to change it up. Also, I’m very appreciative of the people I worked beside when I started my apprenticeship on the Clyde with marine and mechanical engineering firm Hutsons.
Many of my colleagues were working class and extremely intelligent. They came from a generation where university wasn’t really an option. I’m always grateful for their time and advice. It was my university of life experience; one which led to me eventually going on to gain a degree in aeronautical engineering from the University of Glasgow.
Where do you find yourself most at ease?
On the golf course or watching football with lifelong friends.
If you weren’t in your current role, what job would you most fancy?
I used to think being a chef would be good, but it looks like it would take a huge amount of effort to really do it to a high standard.
What phrase or quotation has inspired you the most?
“Everyone I pass on the way up I’m going to meet again on the way back down.” Treat everyone the way you would want to be treated yourself.
What is the best book you have ever read? Why is it the best?
Who moved my Cheese? It’s a business book by Dr Spencer Johnson. It’s a simple, short story that illustrates how people must embrace change and should adapt to new situations with an open mind and a motivated spirit.
What has been your most challenging moment in life or business?
In my previous role we had more than 1,000 workers that couldn’t leave a number of offshore installations in South East Asia due to a major Covid outbreak. There was a great deal of responsibility on myself and my colleagues to ensure we looked after the well-being of the team. The way everyone pulled together was a sight to behold and all worked out well in the end, but it was a huge logistical challenge. The health and safety of your team should always be your priority.
What do you now know that you wish you had known when starting out in your career?
Embracing failure as a learning opportunity; it’s an essential part of growth and innovation.
This article can be found online here – https://www.heraldscotland.com/news/24078257.university-life-stands-govan-raised-engineer-good-stead/
ICR Group has recorded its highest turnover since the business was launched in 2011 – with the Middle East playing a key role in the firm’s success.
ICR, a technology-focused provider of specialist maintenance, inspection and integrity solutions across multiple sectors, has seen increased demand across its core energy sector operations, following the roll-out of an internationalisation strategy and diversification into other sectors.
The UK firm’s turnover for its 2022-23 year-end was £41.7m, a 20% increase on its previous financial year. Headcount has increased globally by 15%, from 204 to 235, since May 2022, and the company expects to create around 50 jobs across its operations during the next phase of its strategy.
Jim Beveridge, Chief Executive Officer at ICR, said: “Our presence in the Middle East has been particularly noteworthy, with recent high-value projects completed in the United Arab Emirates, Qatar and Saudi Arabia. We have also solidified our presence in the region by appointing a new partner in Abu Dhabi.
“Our ongoing international expansion not only bolsters our long-term sustainability but also plays a vital role in creating meaningful and enduring employment opportunities, rightly positioning us as a contributor to the energy transition.
“The Middle East is a dynamic market, brimming with potential for innovative companies such as ICR. At ADIPEC, we are eager to foster deeper relationships with our partners and engage with organisations striving to achieve their net-zero objectives. With COP28 on the horizon, our industry must remain steadfast in its commitment to facilitating a just transition toward a lower-carbon future.”
ICR’s established technological solutions continue to play a significant part in its growth. Technowrap provides life-long repairs that can be applied to internal, external and through-wall defects on complex geometries, while INSONO is an innovative NDT (non-destructive testing) technique for the inspection of engineered composite repairs. The Technowrap repair system reduces emissions by 66% compared to the traditional replacement methods.
Quickflange offers cold work solutions with weldless, high-performance flange-to-pipe connections. It provides a permanent repair option for improving pipeline integrity and flow assurance, eliminating the need for welding or hot work. ICR’s drone division, Sky-Futures, has also secured further international work.
NAMA Development Enterprises is ICR Group’s sponsor in Abu Dhabi, while its new execution partner in Abu Dhabi is APS.
ICR Group and NAMA Development Enterprises will be exhibiting at Stand 6210 at ADIPEC.
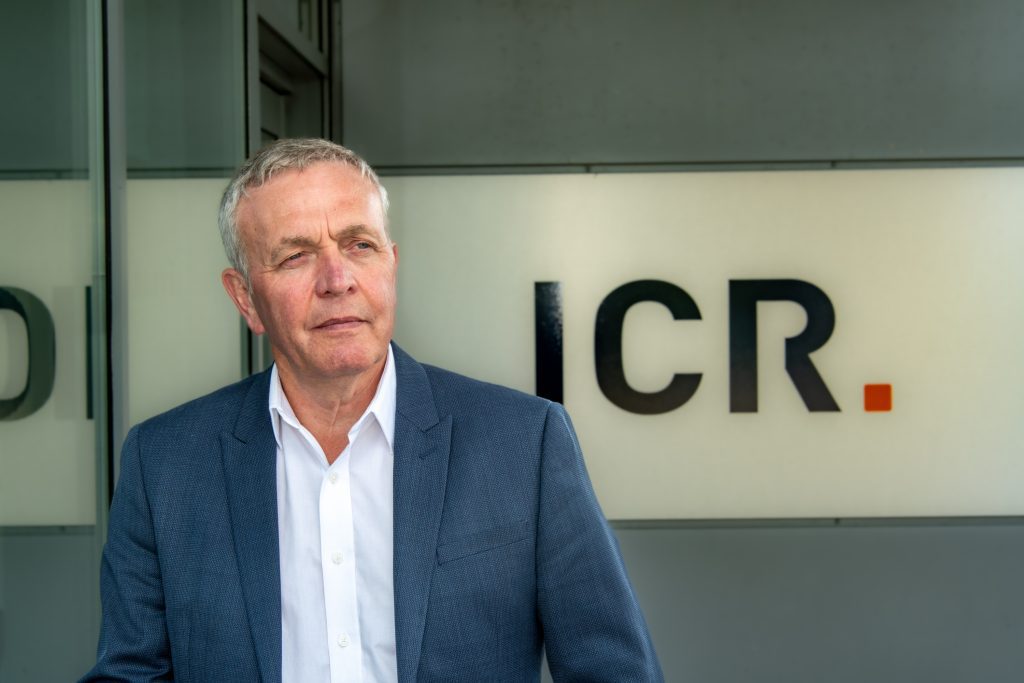
ICR Group is set to highlight its innovative technologies by contributing to a broader conversation on decarbonisation strategies at Offshore Europe.
Ross McHardy, Group Director at ICR, will be hosting a session entitled ‘Small Steps for a Bigger Change: Decarbonisation Through Technology’. The event on Tuesday, September 5 (10am-11.15am) at Aberdeen’s P&J Live will also feature other industry leaders.
This seminar is part of the Collaboration Zone, an initiative organised by the Energy Industries Council (EIC). Running throughout the week, the programme offers an avenue for speakers and attendees to exchange knowledge, explore smarter operational methods and present valuable insights gained from past experiences.
In addition’s, ICR’s innovations will be showcased at the same venue on Wednesday, September 6 (10am-10.30am) during a dedicated Technology Spotlight Session. This EIC event, hosted by Josh Cannell, Interim Head of Sales – Quickflange™, and Calum Macnaughton, Inspection and Integrity Engineer at ICR, will put the focus on Quickflange™ and INSONO™. Day 2 of the EIC Collaboration Zone – Navigating Net Zero – is sponsored by ICR.
Ross said: “Offshore Europe serves as an excellent platform to engage with the industry and share best practice and innovative ideas. Decarbonisation stands as a pivotal element in ICR’s strategy for fostering sustainable growth and both these EIC events provide a first-rate opportunity to highlight our ethos and smart technology.”
ICR’s Quickflange™, a weldless connector solution, offers an alternative for cold work applications, particularly for high-performance flange-to-pipe connections. This technology facilitates permanent repairs, enhancing pipeline integrity and ensuring fluid flow, all without the need for welding or hot work. With its wide range of applications, Quickflange™ has proven to be both cost-effective and efficient, reducing repair times by up to 80% compared to traditional methods. Remarkably, it also contributes to a 57% reduction in greenhouse gas emissions when contrasted with conventional welding practices.
INSONO™ is an innovative NDT (non-destructive testing) technique for the inspection of engineered composite repairs. It is a solution that allows for the extension of defined life repairs, reducing waste while avoiding high-carbon emissions from traditional steel replacement alternatives. INSONO™ complements ICR’s Technowrap™ range and provides operators with the assurance their composite repairs are fit for purpose and satisfy regulatory body guidelines on inspection criteria.
Technowrap™, a lifelong repair system, boasts the capability to address internal, external, and through-wall defects, even when dealing with complex geometries. This innovative solution has demonstrated a remarkable 66% reduction in emissions when compared to conventional replacement methods.
In his capacity as Group Director, Ross oversees the ICR repair division, which encompasses Technowrap™, Quickflange™, mechanical services and leak sealing business lines. He holds a BEng in Civil Engineering and an MSc in Offshore Engineering and is a chartered structural engineer. With 30 years of industry experience, he has held senior positions in various companies, including TAQA, EnQuest, and EnerMech.
Offshore Europe is celebrating its 50th anniversary. For more information about the conference & exhibition, please visit https://www.offshore-europe.co.uk/en-gb.html
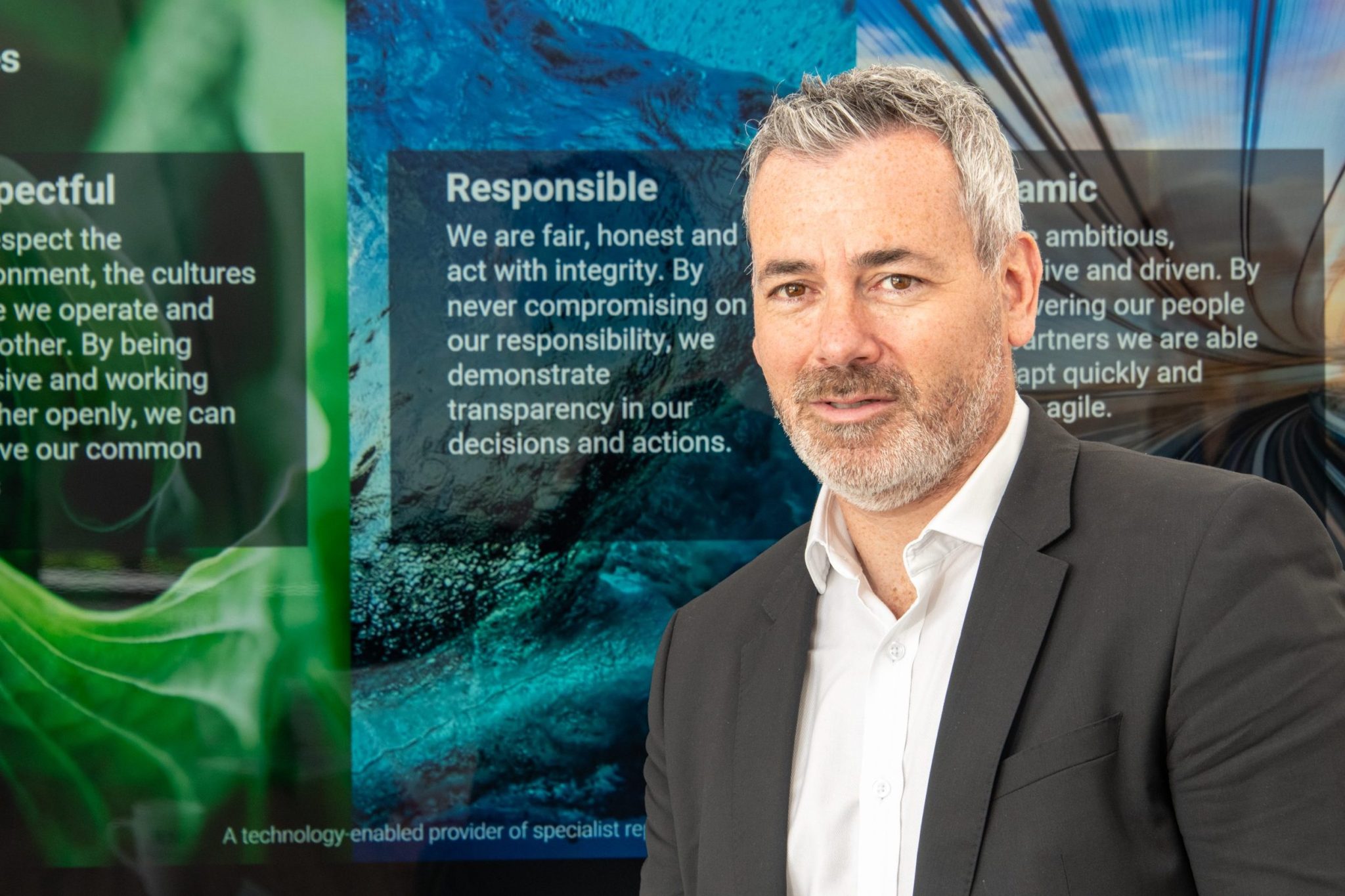
We had a brilliant day joining cold work specialists DIFLICOM at the launch of their new facility in The Netherlands! We thoroughly enjoyed presenting Quickflange™ technology along with carrying out multiple live 8” demo installations.
It was great to meet so many of our existing and new customers with over 30 representatives attending from different companies. Feedback was very positive and, since the event, we have received further enquiries and have hosted further demo days.
For more information on our Quickflange™ capabilities, contact Josh CannellMaurice van der Woude or Lindsay Anderson
Steve Jennings | Britney Houvet | Lindsay Anderson | Josh Cannell | Jamie Ironside | Phil Paterson
#ICR #Diflicom #Quickflange #WeldlessConnectors #AssetIntegrity #NoHotWork
ICR has been awarded a long-term hire contract with TAQA Bratani Limited (TAQA), for the provision of its Quickflange™ weldless connections for TAQA’s UK-based operations. The contract is for two years with a two-year extension option.
Lindsay Anderson, Head of Sales – Quickflange™ at ICR, said:
“We are delighted to secure this contract with TAQA, who we have been working with for almost 10 years. Quickflange™ offers clients permanent repair options minimising downtime or the need for hot work permits, making it a cost effective and efficient way of performing repairs. The technology has a long-standing track record, particularly in the North Sea & Norway sectors, but we are now seeing a growing demand for solutions onshore, out with the traditional oil and gas sector as well as our international locations throughout the globe.”
For almost 20 years, ICR’s patented Quickflange™ technology has built up a proven track record as a leading provider in cold work solutions, offering clients permanent repair options for improving pipeline integrity and flow assurance whilst eliminating the need for welding or hot work with zero emissions generated. With an extensive range, Quickflange™ is a safe, cost-effective and efficient solution generating an 80% time saving over traditional welding – enabling the technology to be used as an emergency solution or for any planned maintenance and repair work.