Challenges
- Limited space
Benefits
- Fully bespoke packages
- Delivered on time and within budget
Scope
ICR was contracted to supply a one off Scale & Corrosion Inhibitor Injection package for a major oil and gas production facility in the North Sea. The project scope consisted of an integrated Chemical Injection Package, including two off duplex (dual headed) Electric Drive API-675 injection pumps, and all necessary process equipment and instrumentation required to meet client specification.
The client requirements included:
- Injection package fully compliant with all applicable client, site, national, international and hazardous area specifications.
- One off electric drive, skid-mounted, integrated Scale & Corrosion Inhibitor Chemical Injection Package complete with all necessary process equipment and instrumentation, suitable for installation offshore.
Solution
The facility’s space constraints meant that the allocated area for equipment was extremely small. ICR conducted an optimisation study to identify pumps that were suitable for the given process parameters, while minimising required footprint. Through detailed design, ICR configured the package to fit within the allocated area, all while maintaining optimal package operability and ergonomics.
ICR designed and manufactured the package in accordance with all relevant client and end user specifications.
The Scale & Corrosion Injection Package included the following equipment:
- One off painted and load tested Carbon Steel skid c/w integral drip tray, and certified lifting gear.
- Two off Milton Roy Primeroyal PH Duplex API-675 injection pumps (in duty / standby configuration) c/w 1.1kW electric motors, capable of injection rate up to 8.34 l/hr at an operating pressure of 320 barg. Pump diaphragm rupture detection via Endress & Hauser pressure transmitters.
- Two off local start / e-stop stations.
- Four off Kenco Engineering pump setting gauges (1 off per pump head).
- Four off Coorstek pulsation dampers (1 off per pump head).
- Four off API-520 Pressure Relief Valves (supplied loose).
- Four off Endress & Hauser pressure transmitters c/w double block and bleed manifolds.
- Discharge non-return valves (NRV’s).
- Double block and bleed isolation on package suction and discharge.
- All required package process piping, fittings and equipment in 316 SS.
- All package instrumentation terminated into skid edge junction boxes (1 off DCS & 1 off ESD) for client hook-up on site.
Result
- Fully assembled and tested package completed and delivered within planned cost and schedule.
- Bespoke packages designed to meet client specifications and process parameters, and fit into small laydown area.
- Duplex pumps allow for two chemical duties via a single pump / motor.
To learn more about our chemical injection solutions, or to enquire with our team, please click here.
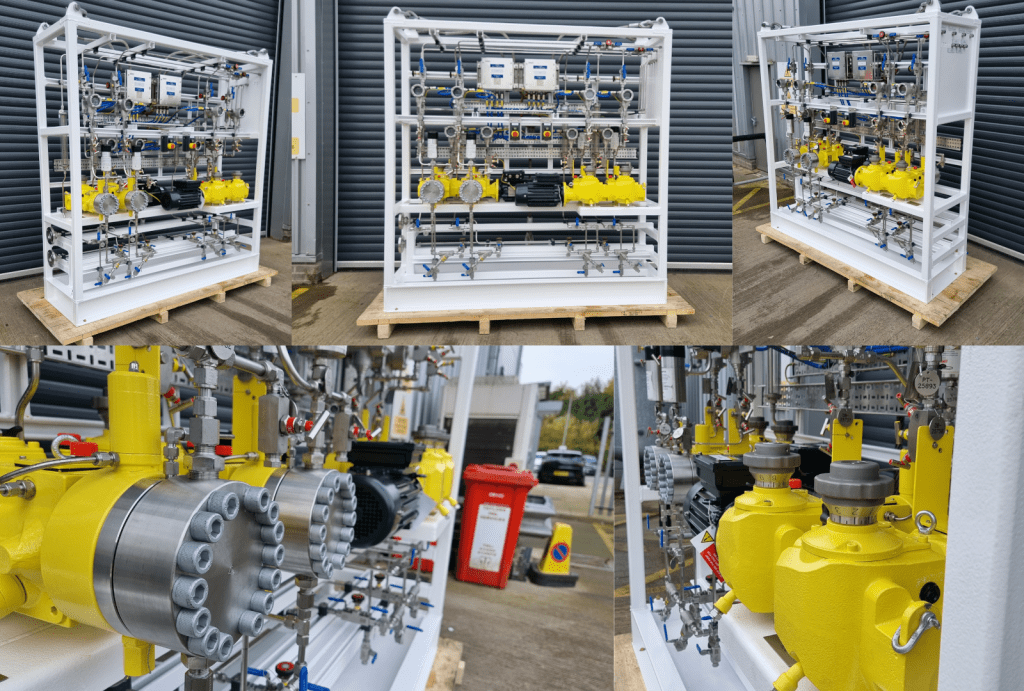