Client challenge
A client approached our team with a critical challenge involving the production chemical injection skip pan, which was experiencing localized pitting, wall loss, and through-wall defects of varying sizes. While structural capacity was a minor consideration due to small loads, the primary goal was to reinstate the skip pan’s integrity to ensure effective containment of fluids. We were was tasked with providing a solution that addressed the defects and maintained the production process’s reliability.
What we did
In response to the client’s challenge, we devised a comprehensive solution to rehabilitate the production chemical injection skip pan. The proposed repair involved the application of two layers of Technowrap 2K™ substrate with Technowrap HA™ (High Ambient) resin, supplemented by localized plates strategically placed over the through-wall defects. The repair covered the entire skip pan, ensuring the proper pan gradient for fluid drainage. With a design life of 10 years, a fluid loading of 20 psf, and a maximum temperature of 120ºF, the composite repair was engineered to share the load with the existing steel structure, assuming an average remaining wall thickness of 0.125” (3.175mm).
One notable challenge encountered during the application was limited space access which we overcame by fabricating a custom roller with an extension. This innovative solution enabled the application of Technowrap 2K™ in the cramped working area between the equipment and the skip pan catch basin.
Results
The implemented composite repair solution yielded positive results and notable benefits:
10-Year Defined Life: The repair was engineered to provide a 10-year defined life, ensuring the longevity and reliability of the skip pan.
Safety and Compliance: No hot work was required during the repair process, significantly reducing safety risks and ensuring compliance with stringent safety standards.
Cost-Effective Alternative: The composite repair solution proved to be a cost-effective alternative when compared to the traditional approach of welded replacement, providing significant cost savings for the client.
Minimal Personnel Onboard (POB) Requirements: The repair was executed with minimal POB requirements, contributing to operational efficiency and cost-effectiveness.
In conclusion, our innovative composite repair not only addressed the client’s challenges related to the production chemical injection skip pan but also provided long-term reliability, safety, and cost-effectiveness. This case study highlights the adaptability of composite repair solutions in overcoming complex challenges in industrial settings.
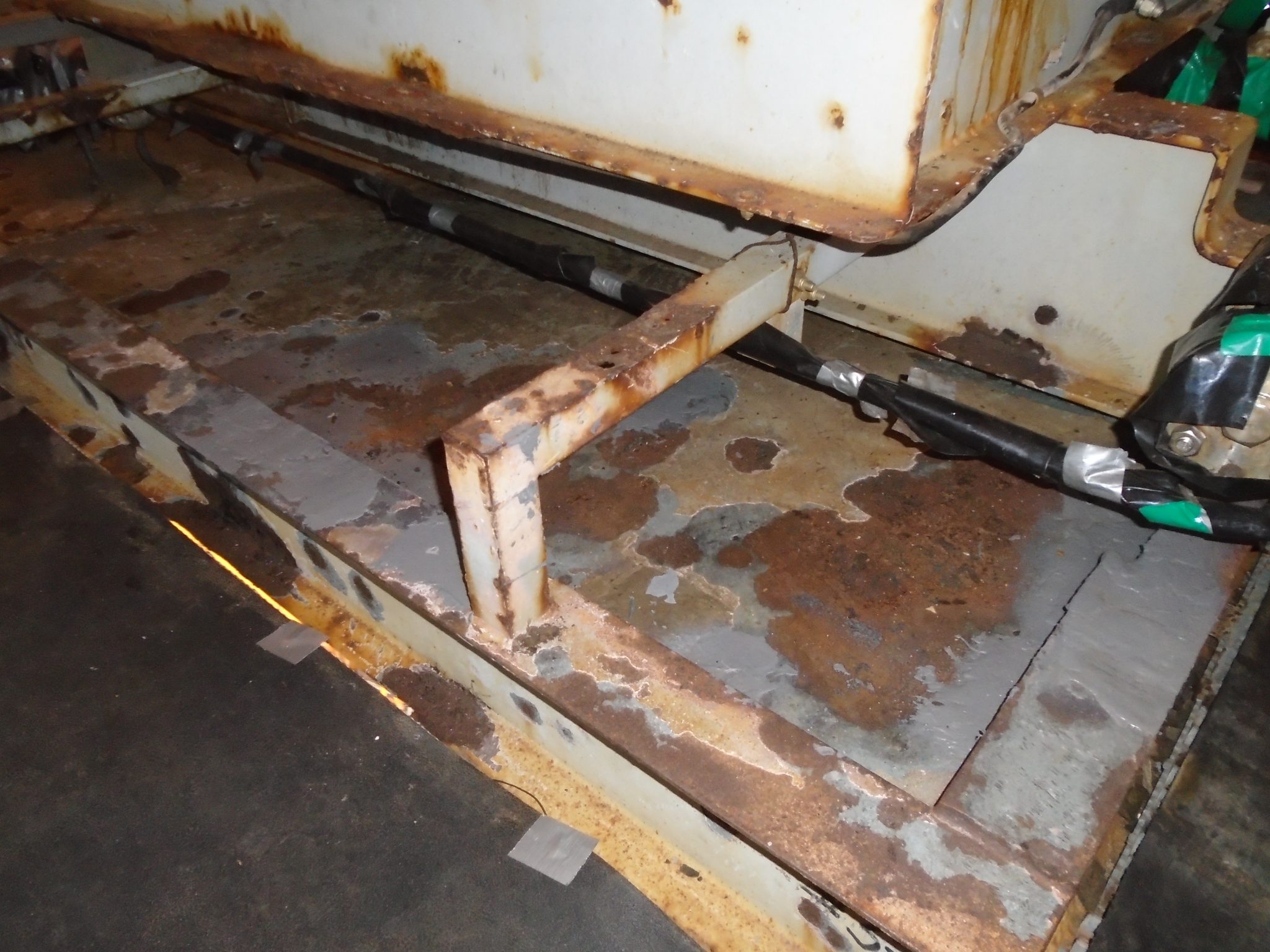