Client challenge
A major North Sea operator encountered a significant challenge when dealing with a leaking 4” Sch80 carbon steel nozzle crucial for a diesel tank’s operation. Complicating matters, the application of hot work methods was obstructed by time constraints and extreme space restrictions in the confined void where the nozzle was located, rendering conventional welding impractical.
What we did
This project presented several challenges, including the proximity of an i-beam, tight clearances, limited rigging options, and confined spaces. Within a 48-hour timeframe from the initial request, we successfully mobilised all necessary equipment, minimising downtime for our client. Post-installation, a thorough testing of the Quickflange™ joint ensured its integrity, conforming to both industry and client standards.
Results
The implementation of our weldless connector technology, Quickflange™, resulted favorable outcomes for our client. The repair process eliminated the need for hot work, addressing safety concerns and aligning with the client’s operational restrictions. Our tailored approach navigated extreme space restrictions, surpassing challenges unmatched by competitors.
The swift mobilisation of equipment within an impressive 48-hour timeframe significantly reduced downtime and operational disruptions. This rapid resolution showcased the effectiveness of Quickflange™ technology and demonstrated our capacity to deliver innovative solutions under challenging circumstances.
The impact included enhanced safety measures, increased operational efficiency, and substantial cost reductions associated with the repair process. This case study underscores our commitment to providing comprehensive solutions that prioritise safety, efficiency, and cost-effectiveness for our clients.

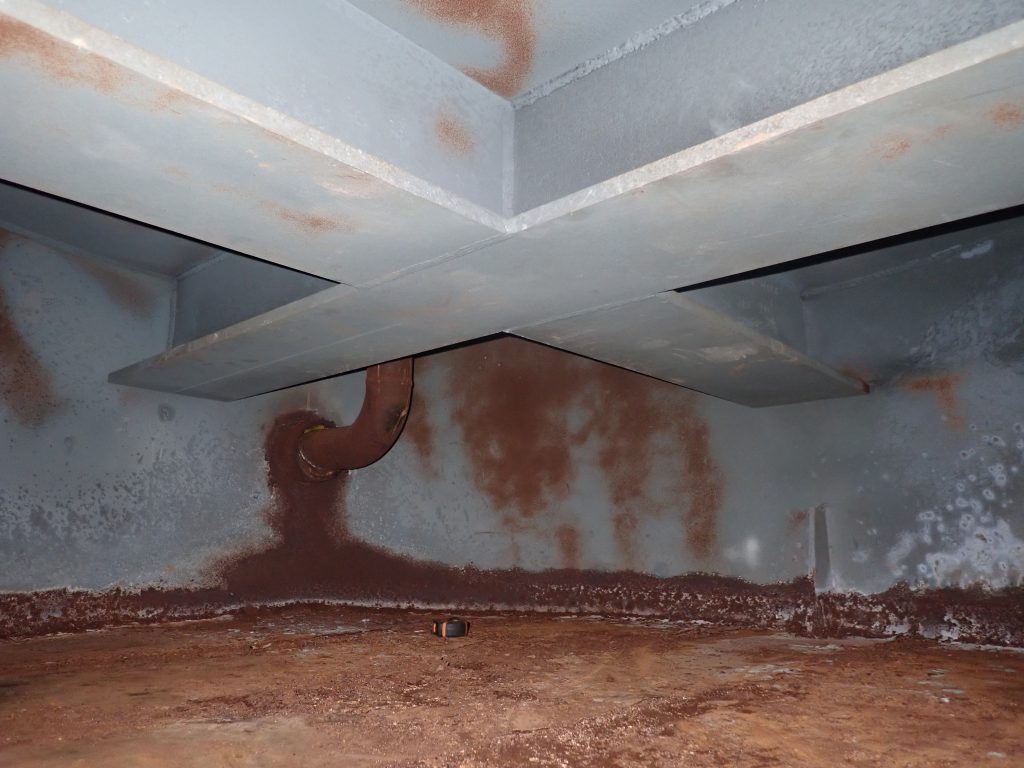
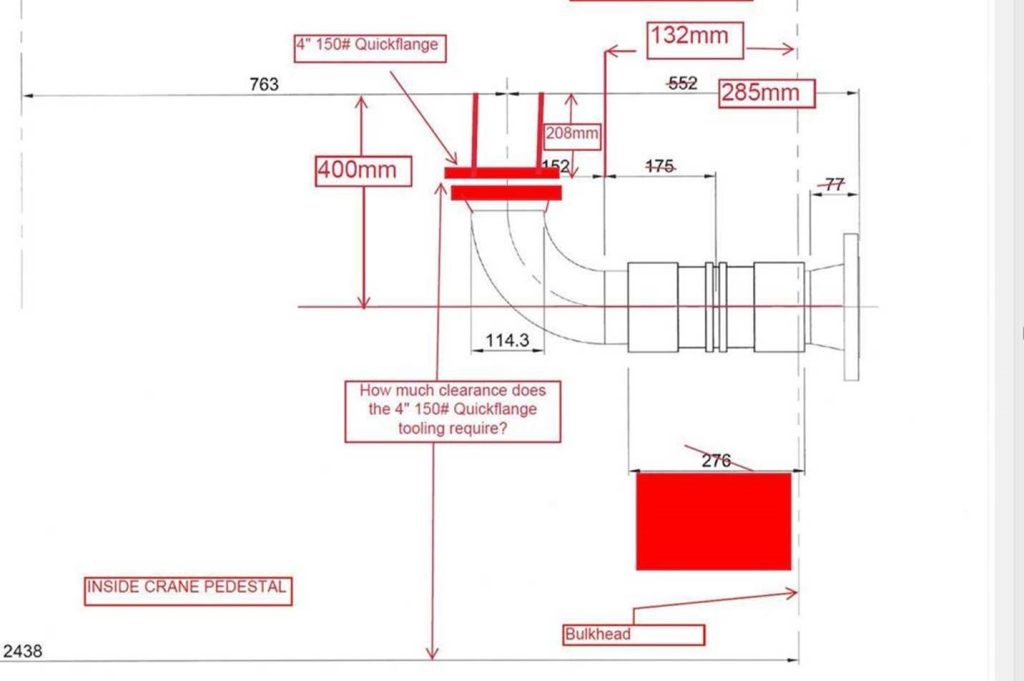
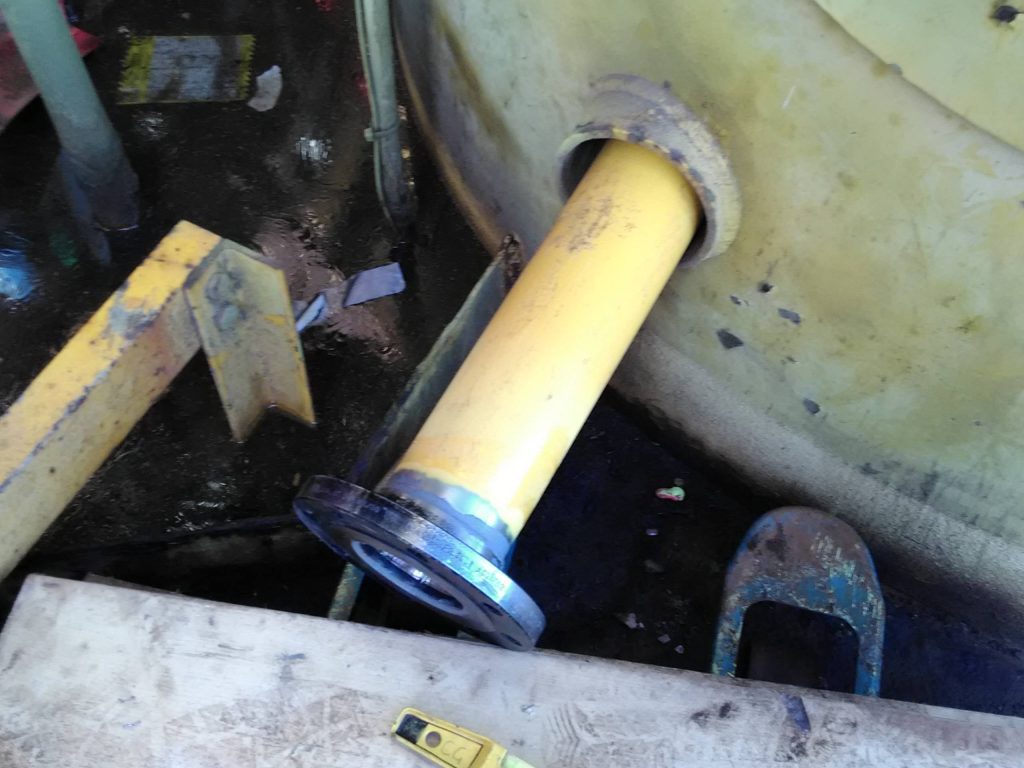
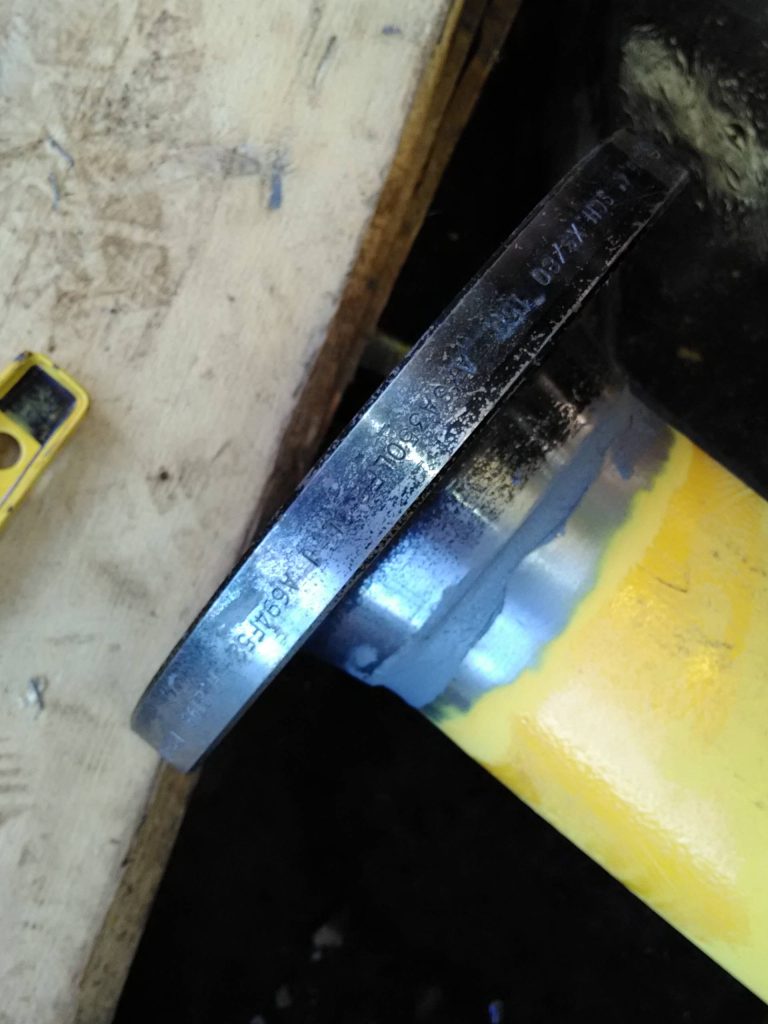
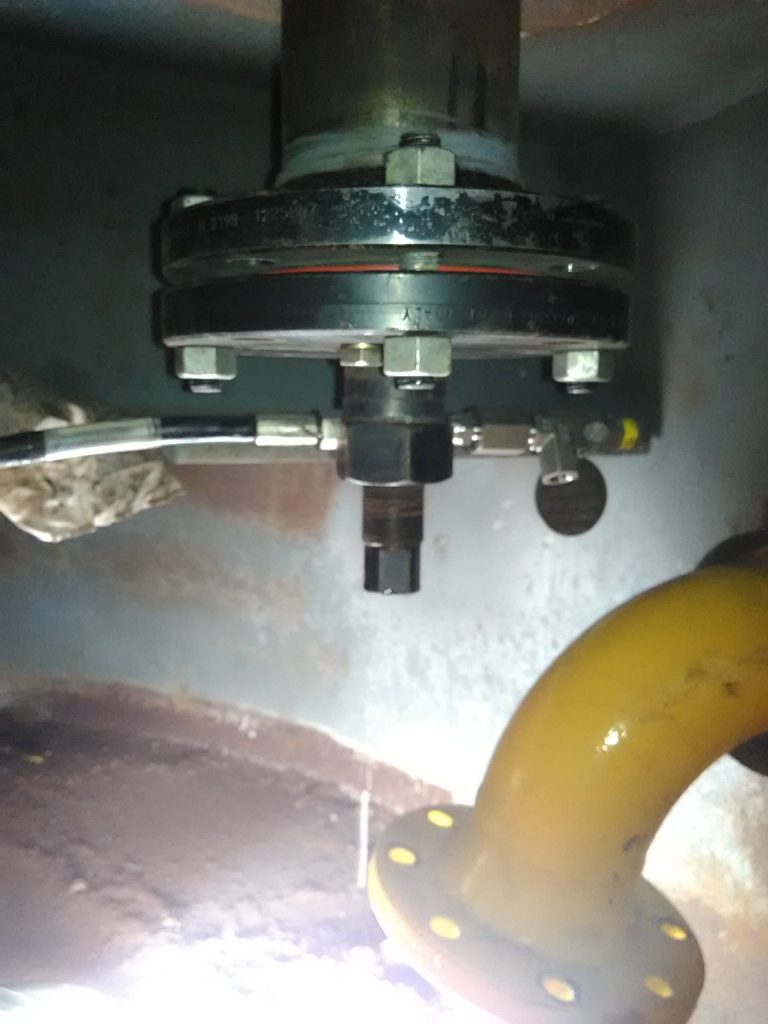
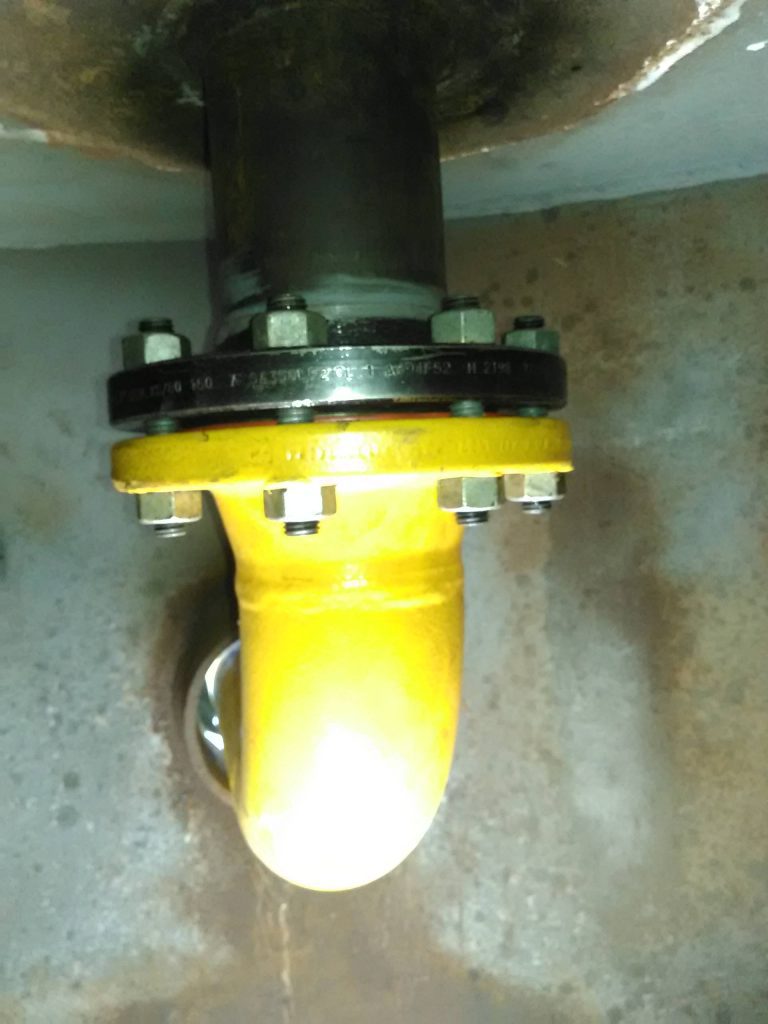
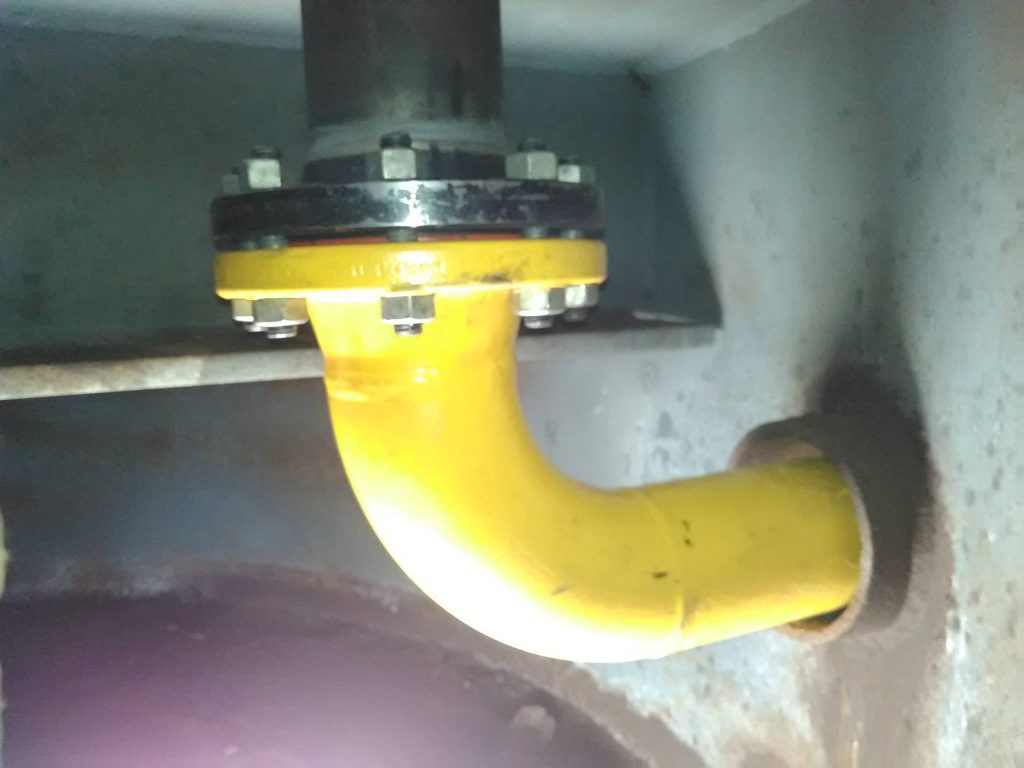
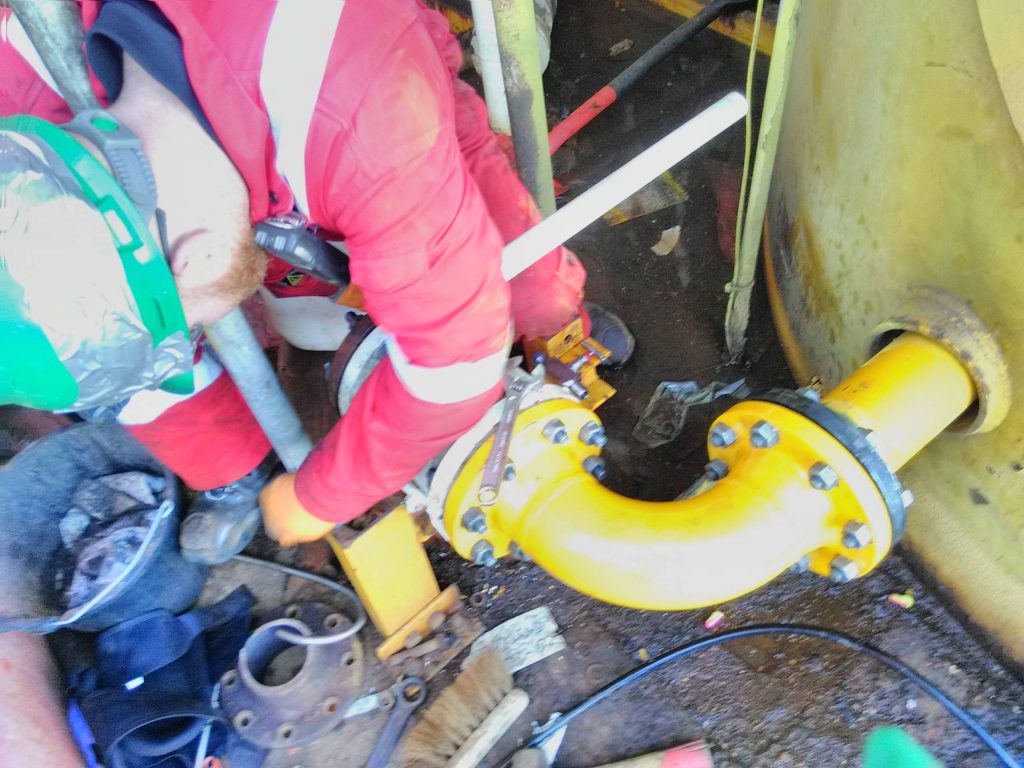