Challenges
- Remote location
- Extreme environment
- High-grade carbon steel
Benefits
- No hot work
- Minimal downtime
- Increased safety
Scope
The primary objective of this project involved the removal and replacement of a deteriorated section of API-5L Grade X42 line pipe, which had suffered significant corrosion over time. This required the installation of a prefabricated spool measuring 50 metres in length. The worksite’s remote desert location added unique logistical challenges, including limited accessibility, extreme environmental conditions, and the need for precise coordination to ensure seamless delivery and installation of the replacement spool. Despite these constraints, the project was designed to ensure minimal disruption to operations while adhering to strict industry standards and safety protocols.
Solution
Quickflange™ was selected as the preferred cold work repair solution. Trained personnel from our local partner were mobilised to the site to carry out the activations. After isolating the pipeline, a cold cut was performed on the corroded pipe section, and the pipe ends were prepared to accommodate the 6″ Sch40 Class 600 API-5L Grade X42 Quickflange™ connectors. Upon completion of the installations, each connector underwent hydrostatic testing in accordance with the client’s specifications.
Result
The successful installations were completed within a single shift. From pipe cutting to final activation, both installations were finished in a combined total of two hours. By employing a cold work method, the need for hot work was entirely eliminated, significantly reducing risks and ensuring strict compliance with safety protocols. This approach not only minimised downtime but also demonstrated the effectiveness of Quickflange™ in delivering fast, reliable pipeline repairs.
For more on our Quickflange™ technology, click here.
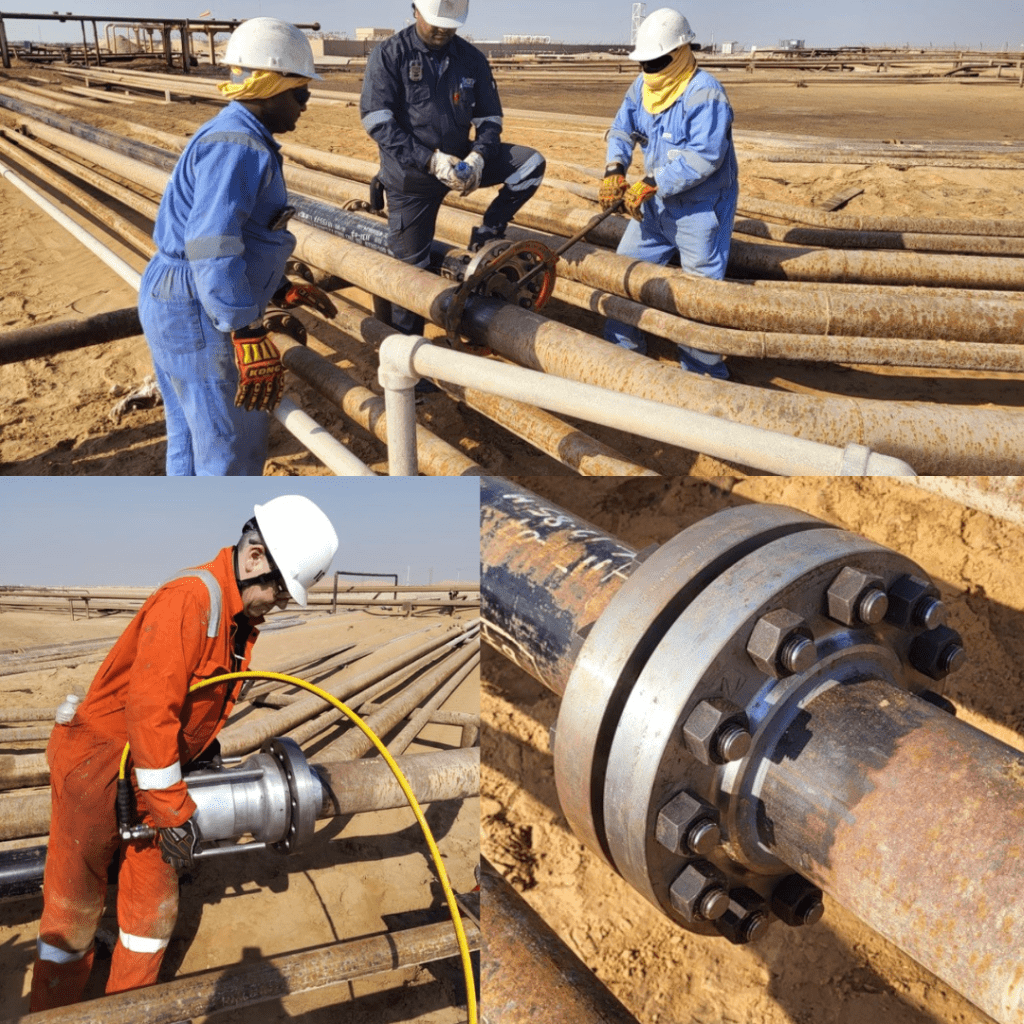