Date: October 2021
Client: Major North Sea operator
Location: UKCS
Client challenge
Our client, a major North Sea operator, required an Automatic Processing Unit (APU) to remotely adjust injection rates. The unit had to have the following specifications:
- A stainless steel 316 box frame for attaching to a H2S Scavenger rental unit.
- Single vs stroke speed (at 100 stroke length).
What we did
Our team provided an APU that enabled remote adjustment of chemical injection rates from a site control room. The APU received a 4-20mA signal from the control room, and based on this signal, adjusted the stroking speed of the pump proportionally. To control the pump’s stroking speed, the APU utilized a solenoid valve, which was installed locally to the pump in place of the normal Williams Controller. This solenoid valve effectively fulfilled the role of the Controller.
The APU unit offers several advantages, including:
- Remote adjustment of the pump flow rate allowing for quick and easy changeover, especially in a duty/standby setup.
- Remote starting and stopping of pumps enabling remote control of pump operations, enhancing convenience and flexibility.
- Reduction in chemical usage by remotely adjusting the chemical flow rates, the APU assists in reducing chemical consumption.
- Compatibility with site instrumentation as the APU can receive an analog signal from the site DCS or feedback from site or package instrumentation such as flowmeters. This facilitates precise adjustment of chemical injection rates.
- Proportional adjustment of stroke speed as the APU receives a 4-20mA signal and adjusts the pump’s stroke speed accordingly, ensuring accurate control.
The APU controls the stroke speed of the pump by opening and closing a solenoid valve installed locally to the pump, replacing the normal Williams Controller. The solenoid valve effectively performs the role of the Controller, enabling the increase or decrease of the pump’s stroke speed.
The table below provides an example that demonstrates the relationship between the analog signal sent to the APU and the resulting stroke speed or pump volume. It’s important to note that stroke speeds and volumes may vary depending on the specific pump models used.
Signal | Strokes per Minute | Litres per hour |
---|---|---|
4mA | 0 | 0 |
6mA | Pump A – 8.75 | 84 |
8mA | Pump A – 17.5 | 168 |
10mA | Pump A – 26.25 | 252 |
12mA | Pump A – 325 | 336 |
14mA | Pump A 35 & Pump B 8.75 | 420 |
16mA | Pump A 35 & Pump B 17.5 | 504 |
18mA | Pump A 35 & Pump B 26.25 | 588 |
20mA | Pump A – 35 & Pump B 35 | 672 |
Results
By successfully implementing the APU, our solution allowed our client to remotely adjust injection rates, control pump operations, and optimise chemical usage. The APU’s flexibility and compatibility with various instrumentation make it a valuable tool in enhancing operational efficiency and ensuring accurate control in critical processes.
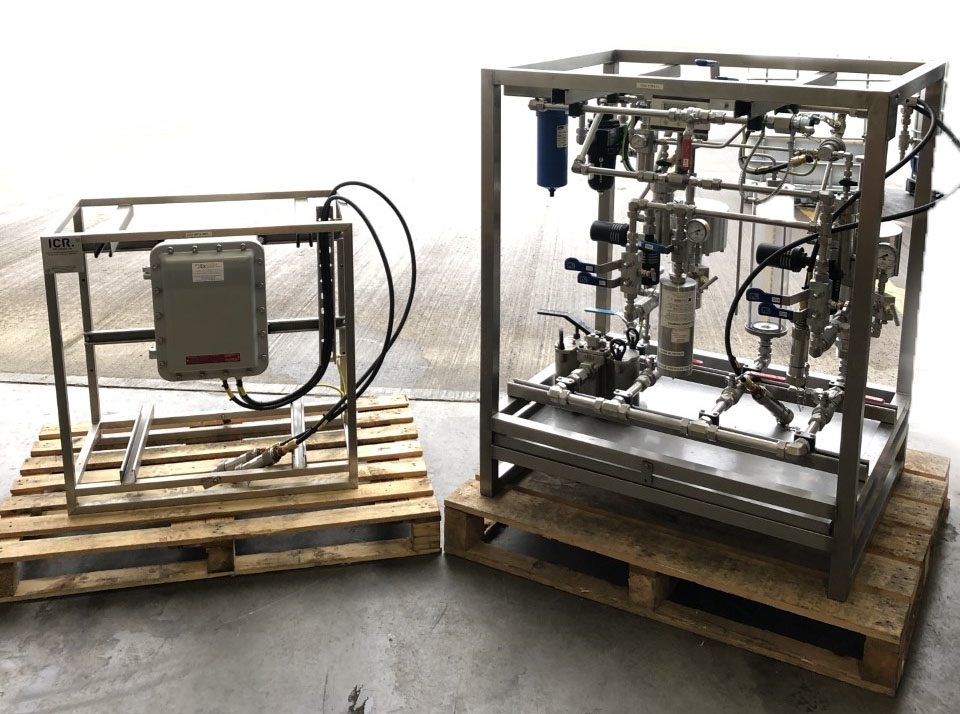