Client: Talos Energy
Asset: Offshore platform
Location: Gulf of Mexico
Client challenge
A major operator in the Gulf of Mexico faced a critical issue with a carbon steel section of a methanol drip pan on their platform. The structure exhibited localized pitting, wall loss, and through-wall defects of varying sizes, necessitating immediate attention. The client approached ICR with the challenge of providing an engineered composite repair solution that would ensure a 10- year design life. The primary focus was on containing fluids, considering minor structural capacity and aiming for a cost-effective alternative to welded replacements.
What we did
To address the client’s challenge, we implemented a comprehensive solution utilizing two layers of Technowrap 2K™ glass fiber combined with Technowrap HA™ (High Ambient) resin. Localized plates were strategically placed over numerous through-wall defects, ensuring a holistic coverage of the entire drip pan. The design parameters included a 10-year lifespan, a fluid loading of 20 psf, and a maximum temperature of 120ºF. The composite repair was engineered to share the load with the existing steel structure, assuming an average remaining wall thickness of 0.125” (3.175mm).
Results
The implemented composite repair solution achieved significant results and benefits for our client:
Cost effectiveness: After multiple drip pan repairs with various operators, it was established that the composite repair method proved to be extremely cost-effective compared to the alternative of a welded replacement.
Efficiency in installation: The repair process was swift, reducing downtime and operational disruption. Its efficiency was further highlighted by the elimination of hot work requirements, significantly decreasing safety risks associated with traditional repair methods.
Minimal Personnel Onboard (POB) requirements: The repair was executed with a minimal crew, requiring only one Rope Access supervisor. This not only streamlined the installation process but also contributed to a reduction in overall project costs and logistical complexities.
In conclusion our engineered composite repair not only met the client’s requirements for a 10-year design life and fluid containment but also demonstrated notable advantages in terms of cost-effectiveness, efficiency, and safety. This case study underscores the effectiveness of composite repair solutions in extending the lifespan of critical infrastructure in challenging offshore environments.
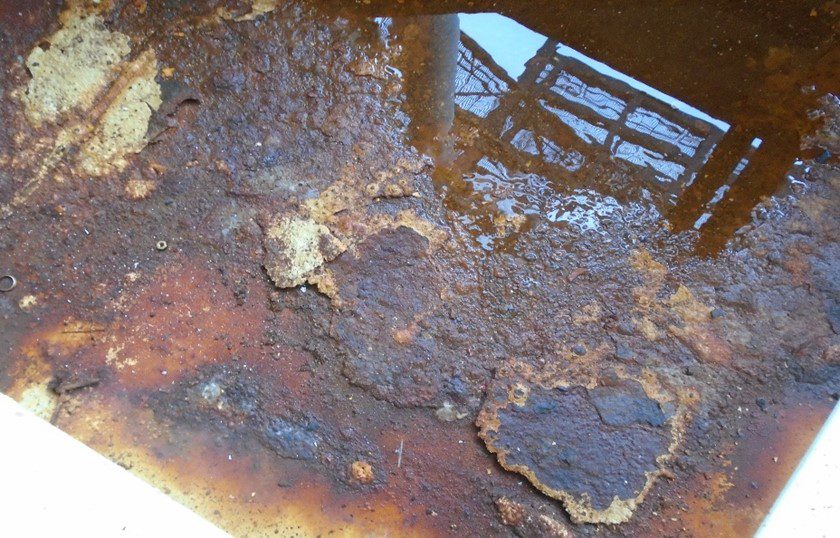
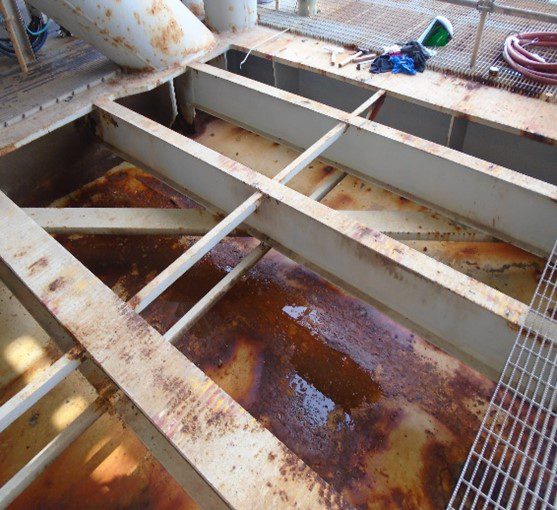
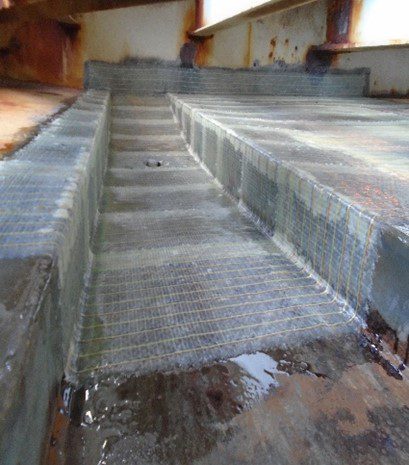
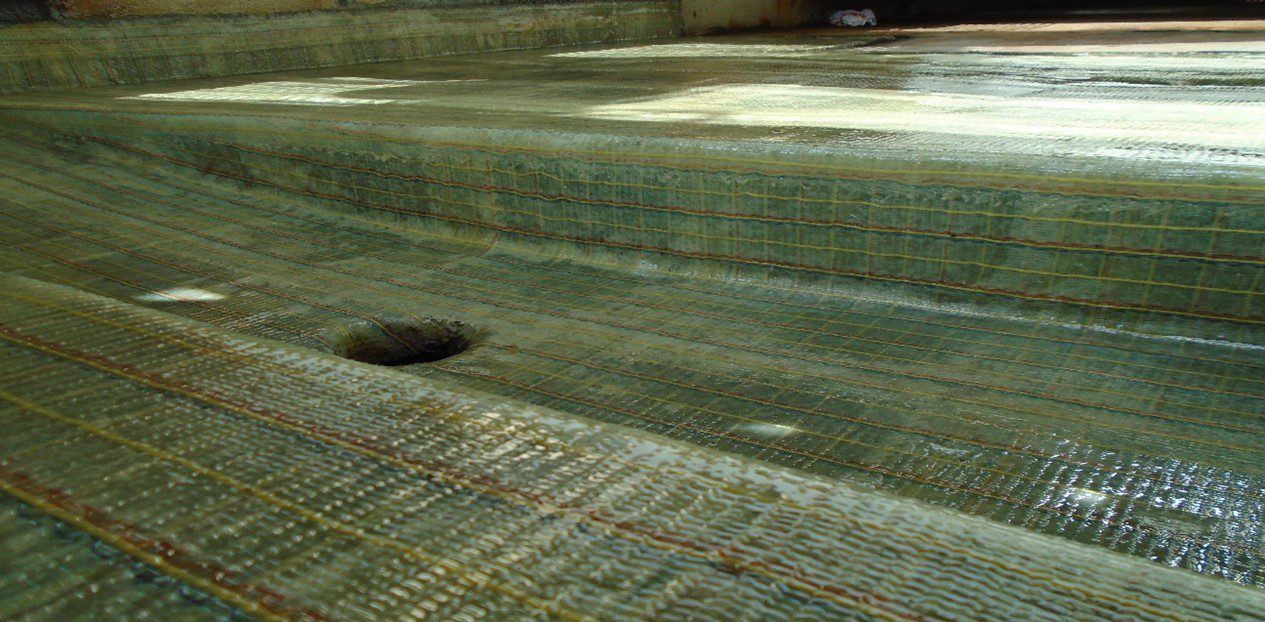