Client: Operator
Asset: Onshore terminal
Location: UK mainland
Result: INSONO™ inspection completed on production critical pipework. Results were fed back into WSE allowing continuous monitoring.
Client challenge
For many clients, ensuring the integrity of your repairs is an essential factor in establishing a baseline for future inspections and is integral to the Written Scheme of Examination (WSE)/ Risk Based Inspection (RBI) process. When an energy operator approached our team to conduct a comprehensive visual inspection and non-intrusive inspection (NII) on a repair, we utilised our extensive experience to accurately identify any potential anomalies that could jeopardise the suitability of the repair for service.
What we did
To address our client’s challenge, we conducted a meticulous close visual inspection covering 100% of the composite repair area, focusing on the external condition of the wrap. Following this, we used INSONO™, a proven non-intrusive technique that utilises soundwaves for a baseline NII examination. This comprehensive assessment evaluated the internal body of the composite wrap and substrate, recording any anomalies that might impact its integrity and life cycle. The established baseline serves as a reference point for future inspections/ examinations, aligning with the RBI and WSE.
Results
By using INSONO™ we effectively located, measured, recorded, and monitored anomalies associated with the wrap repair and substrate. By employing this technique, we provided the client with a robust solution for assessing composite repairs in areas with challenging accessibility or complex geometries, including bends, valves, multiple pipework connections, headers, pipe racks, vessels, and various structural locations. Our examination not only addressed the current concerns but also set the stage for ongoing monitoring and maintenance.
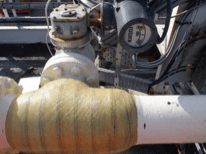