Challenges
- Multiple packages
Benefits
- Completed within timeframe and budget
- ICR supplied all bespoke equipment and personnel
Scope
A trusted supplier of tubular goods, surface and subsea equipment, our customer requested ICR’s experts to supply two permanent air-driven Williams chemical injection packages for its end user in the Middle East.
The project required ICR’s team to design and deliver a WI Biocide system, intended to kill bacteria and mitigate damage, as well as a Truescale system to prevent scale build-up.
Solution
At the beginning of the project, ICR conducted an optimisation study of the pumps supplied by a third party. Following a thorough assessment, ICR identified several improvements to the pump selection that would make the project more cost-effective. Reducing the variety of pumps used would also help streamline future maintenance and improve operational efficiency.
Thereafter, ICR designed and manufactured the topside packages as per the client’s specifications, while aligning these to industry standards. Both the Bioside and Truescale Injection packages included a Williams Milton Roy CLD400-316-TFE air-driven chemical injection pump with a duty / standby configuration, which was mounted in a robust 316-grade stainless steel box frame. The packages were complete with all necessary valves, instruments, and piping to ensure the system operates safely and efficiently.
All Williams pumps were designed and built in compliance with API1675 and have been assessed to be compliant with ATEX directive 2014/34/EU.
Result
ICR supplied all the required equipment to complete both the offline and online packages. The fully assembled, bespoke packages were completed by ICR’s experienced technicians as per the customer’s specifications and unique process parameters, and were delivered to the client’s site within budget and the required timeframe.
Both packages were a standardised size, ensuring a seamless installation in the client’s laydown area with only minor site infrastructure modification being required, leading to minimal disruption.
Furthermore, ICR quickly identified positive changes that could be made to the pump models. Standardising the pumps across both packages made the project more cost-effective and efficient, and minimised the amount of spare stock that needed to be held on site.
To discover more about ICR’s chemical injection solutions, and to see more case studies like this, please click here.
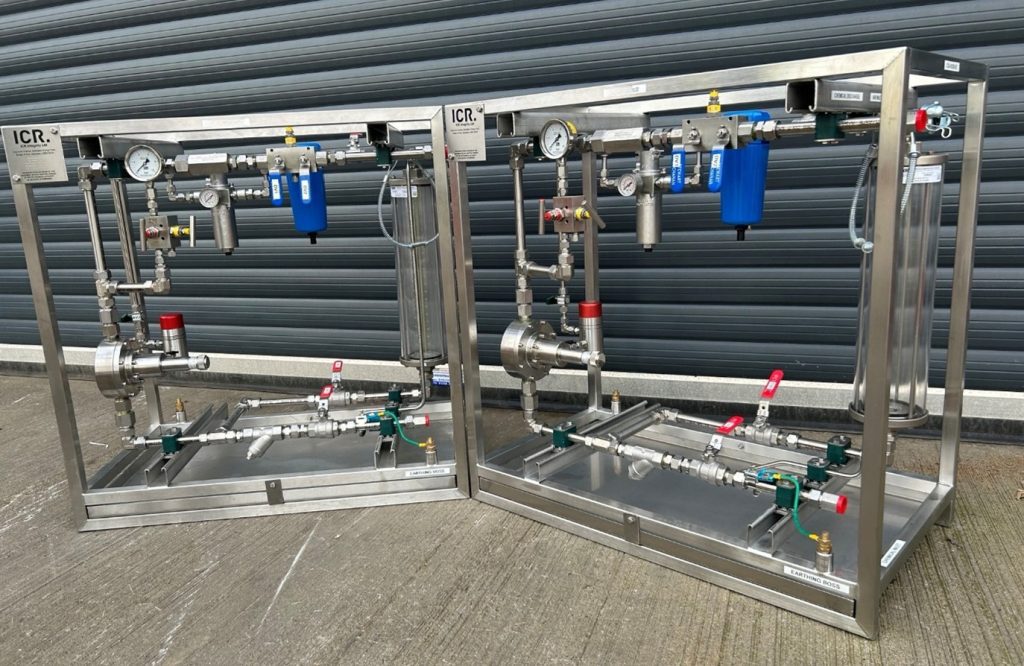