Client | Location |
---|---|
Major North Sea Operator | UKCS |
Scope
A major North Sea Operator was required to complete a dump cooler modification scope with a 10” Cunifer seawater line during a quick turnaround shutdown scope for a Floating Storage and Offloading vessel. Pipe removal and replacement with the use of 10” 5.5mm FF Cunifer flange connections was necessary for replacement of this cooling water repair scope. Quickflange™ was the preferred choice as a cold-work application.
Solution
A Quickflange™ solution was delivered which had undergone leak testing, mechanical testing and burst testing to meet the required criteria for DNV Type Approval Certification. Due to time criticality and personnel limitations on board, two multi-skilled ICR technicians were mobilised to complete this scope on back-to-back day and night shifts. The highly competent technicians held the following certification: Clamshell Cutting, Advanced Quickflange™ Installations, Flange Joint Testing and MJI10 Bolting & Torquing. The technicians completed:
- Prepping the pipe and performing two straight cuts with clamshell cutting equipment
- Installation of 2 x 10” 5.5mm CuNi 90/10 16/20 Quickflange™ Connectors
- Flange strength testing of both connections utilising flange joint testers and ancillaries
- Bolting and torqueing of spools to tie-in the new pipework
During the first of the Quickflange™ installations, the pipe was found to be oval once the cut had been performed with the clamshell cutter. This scenario can occur where the pipe ‘springs’ once the cut has been made due to tension in the pipework. The technicians used tried and tested techniques to bring the pipe to within the required outer diameter tolerances allowing the Quickflange™ to be installed. The technicians also remained to assist the shutdown team with other modification work on the asset ensuring the full scope of work planned for the shutdown was completed on time and to the highest of standards.
Results & Benefits
- Work successfully completed over a 3-day period; technicians on 6 back-to-back shifts cut, installed and tested the Quickflanges™
- Long-term safety of system improved by permanent repair
- Safety, time, production and cost savings compared to conventional welding
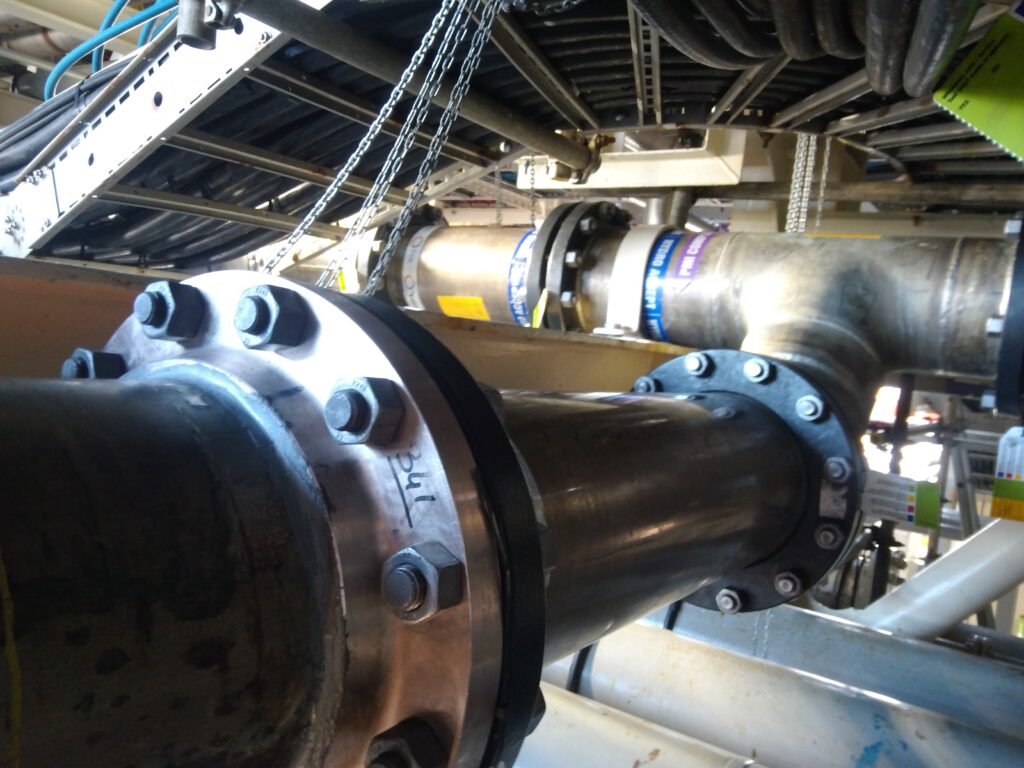
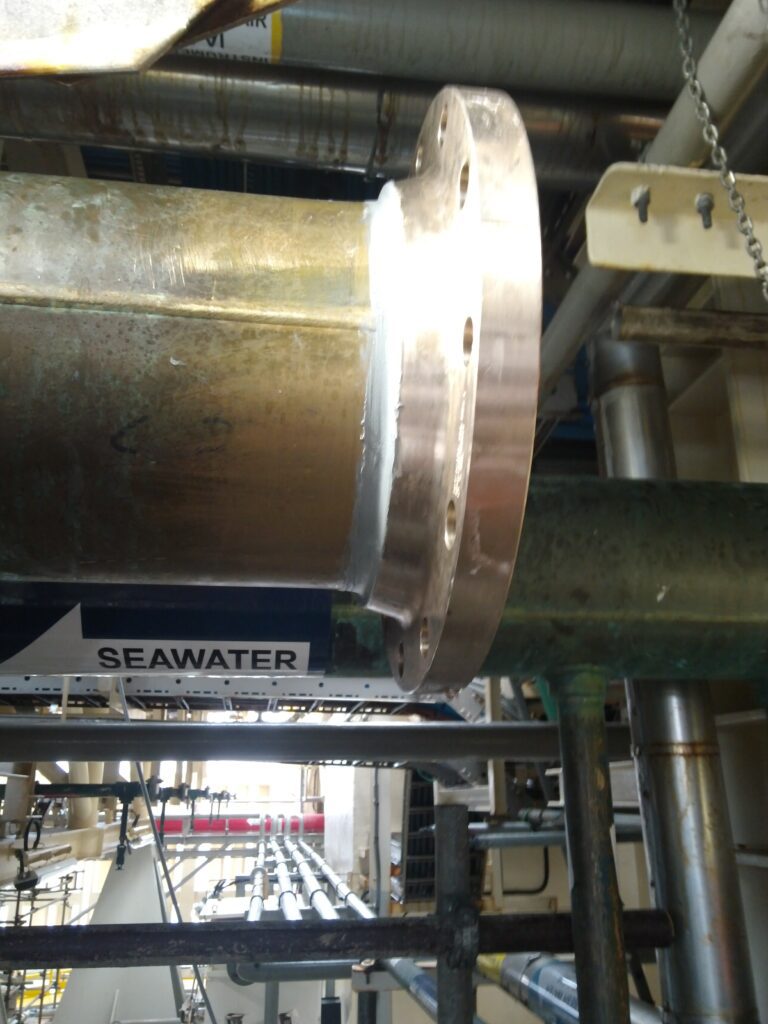
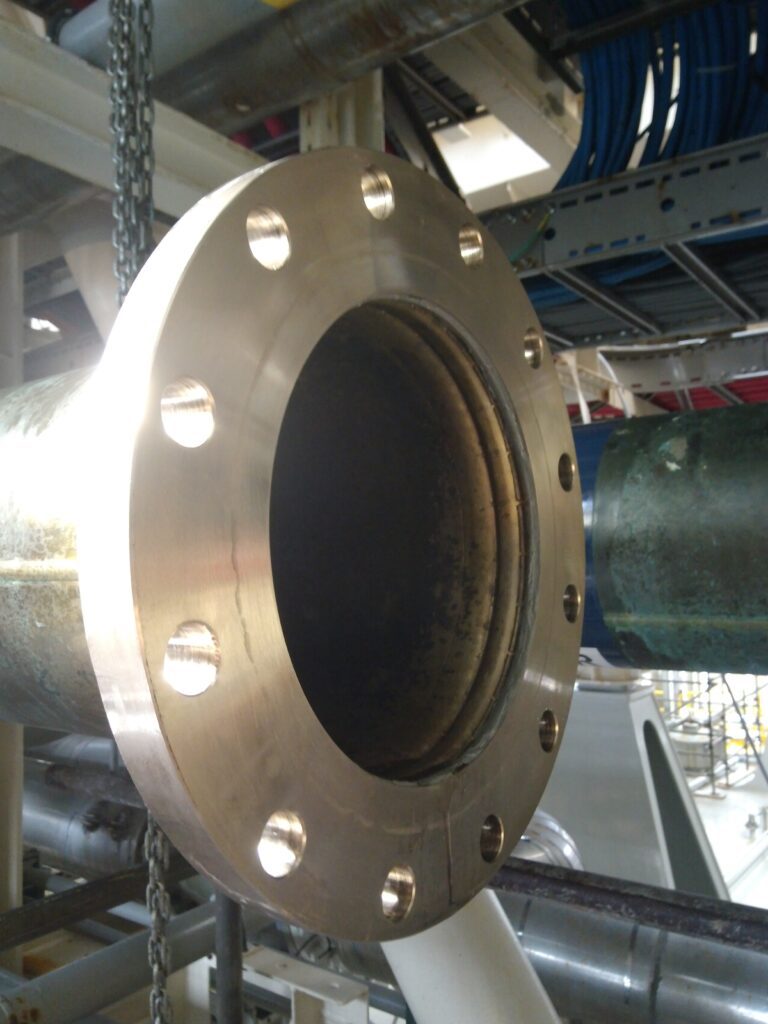
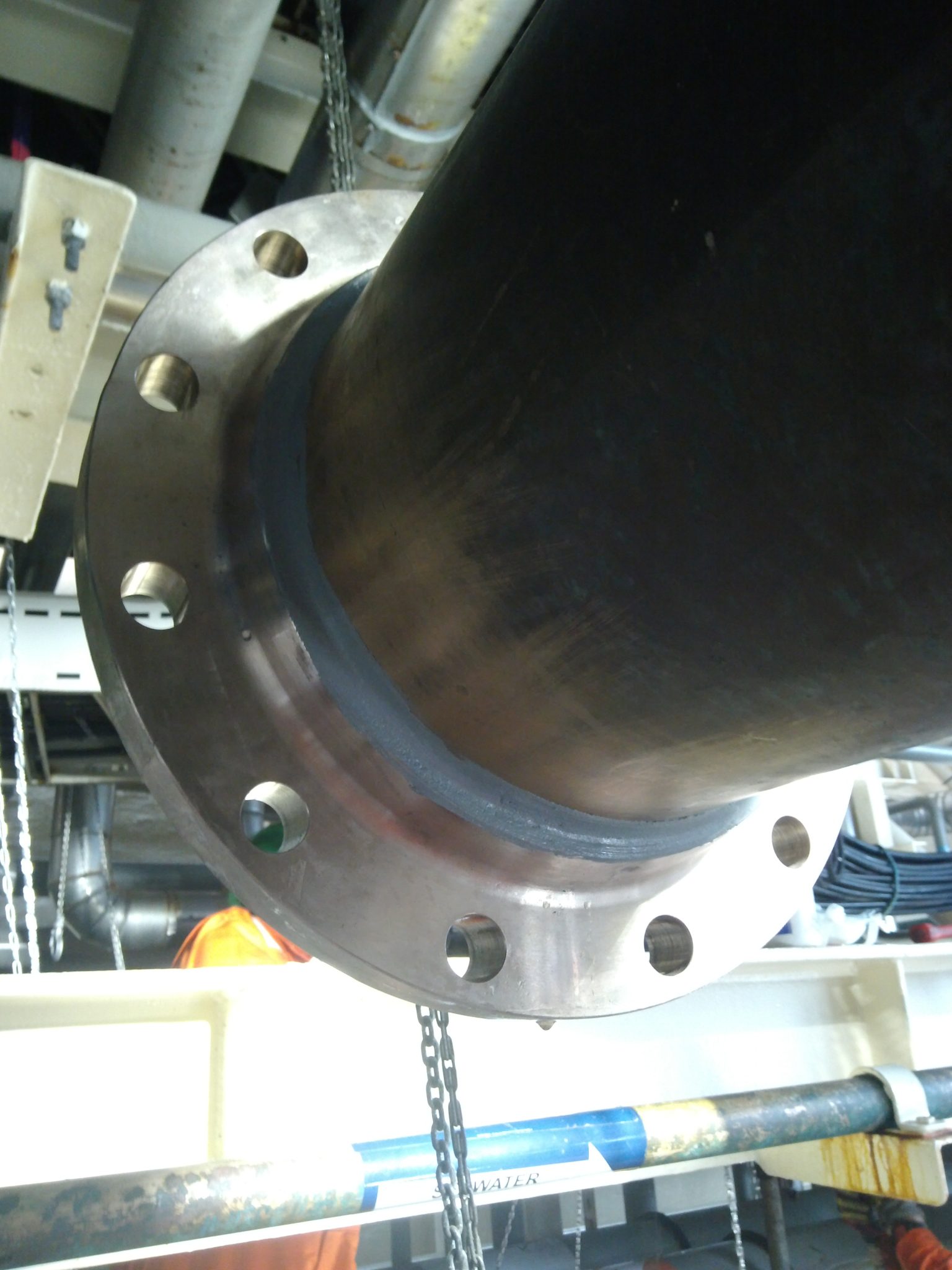